Производство на синтетични чугуни

Фигура 2.11- Зависимостта на специфичната производителност и специфичното потребление на кокс в доменните пещи от съдържанието на силиций в чугуна (числа близо до кривите - обеми на доменни пещи, m 3 )
В момента е натрупан голям положителен опит в производството на синтетичен чугун в редица металургични заводи в Украйна и България. В същото време добавянето на феросилиций към чугуна се извършва в поток от чугун върху улея на доменна пещ или директно в чугунен коф. Въпреки това, висока степен на асимилация на феросилиций (85-90%) се постига само при най-благоприятните условия за разтваряне на феросилиций. И така, при производството на синтетичен чугун в завода за желязо и стомана Магнитогорск, феросилиций FS75, предварително загрят в контейнери с коксов газ (размер на парчето 50-80 mm), се зарежда в нажежен черпак. В редица металургични заводи течен феросилиций се подава в кофата преди изливане на желязо. Организационните и технологичните недостатъци на такива технологии по принцип са доста очевидни, което всъщност се потвърждава от факта, че те не са получили сериозно разпространение.
Високи темпове на усвояване на твърд феросилиций са постигнати от NPO Tulachermet. В същото време феросилиций от електрическа пещ FS45 и FS75 се въвеждат в строго стандартизирани дози в потока от чугун на улея на доменната пещ по време на изпускане. Най-добрите условия за асимилация на феросилиций (85-95%) съответстват на определен размер на парчетата (около 30 mm) и температурата на чугуна на изхода (около 1550 ° C). Проведените изследвания показват значителна разнородност на чугуна по отношение на съдържанието на силиций в него, което за оптимални условия на обработка е поне 0,2-0,3%.
Анализирайки разгледаните резултати, трябва да се отбележи, чепроблемът за най-пълното разтваряне на феросилиция в чугуна се определя от два основни аспекта: наличието на положителен топлинен баланс по отношение на осигуряването на процеса на топене на въведения феросилиций; осигуряване на условия за бързо разтваряне на феросилиций поради интензификация на процесите на пренос на маса и топлина (принудително смесване).
Фигура 2.12 показва изчислената диаграма на промяната на температурата на чугуна по време на разтварянето на феросилиций директно в кофата, изградена въз основа на топлинния баланс.
При изчислението беше прието, че феросилицийът се зарежда в кофата след източване на чугуна и неговото разтваряне става след напълване на кофата при условия на интензивно смесване. Предполага се, че поради енталпията на облицовката на кофата (топлина от предишната стопилка), феросилиций се нагрява до температура от 500 ° C преди изливане, а преди принудително смесване чугунът и феросилиций се държат в кофата за 80-90 минути (загубата на топлина от кофата по време на задържане е 0,5 ° C / min, а по време на смесване - 1,0 ° C / min).
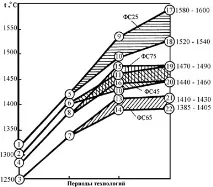
Фигура 2.12- Диаграма на изменението на температурата на чугуна в кофата: 1-4 - температура на топене на феросилиций; 5-8 - температура в черпака след изваждане от доменната пещ; 9-16 - температура по време на нагряване и топене на феросилиций; 17-22 - необходимата температура на изхода от доменната пещ; точки 9,11,13,15,17,19,21 съответстват на увеличение на съдържанието на силиций в чугуна с 1%; точки 10,12,14, 16,18,20,22 съответстват на увеличение на съдържанието на силиций в чугуна с 2,5%.
Необходимата температура на желязото на изхода от доменната пещ се определя като сумата от топлинните загуби на желязото по време на нагряване и топене с феросилиций (като се отчита топлинният ефект), изход от доменната пещ, транспортиране и обработка, добавени къмтемпература на топене на феросилиций от даден клас.
Както се вижда от диаграмата, най-благоприятните условия за топене на феросилиций се създават при използване на FS65, тъй като консумацията на топлина за неговото топене се определя главно от топлинните загуби на чугун по време на задържане в кофата, а температурата му на топене е най-ниската.
Въпреки факта, че динамиката на промяна на температурата на чугуна по време на топенето на феросилиций FS65 и FS75 е почти еднаква, топенето на последния изисква висока температура на чугуна на изхода поради разликата в температурите на топене. Използването на феросилиций FS25, очевидно, може да бъде само от ограничен характер и преди всичко за лека корекция на съдържанието на силиций в чугуна. Сравнявайки получените данни за необходимата температура на желязото на изхода от доменната пещ с данните на NPO Tulachermet, трябва да се отбележи, че изчислените данни се оказаха малко по-ниски. Това, според нас, показва, че смесването на чугун с феросилиций не е достатъчно ефективно в технологията Тулачермет. Следователно, по-пълно усвояване на феросилиция може да се постигне чрез увеличаване на времето на престой на феросилиция в чугуна (по-пълно използване на енталпията на чугуна), предварително нагряване на феросилиций и принудителното му смесване с чугун по време на обработка с кофа (увеличаване на плътността на топлинния поток, намаляване на дебелината на граничния слой, както и отделяне на ненапълно разтворени частици на феросилиций поради излагане на принудителни конвективни потоци). Типичен пример за такава технология, която съчетава всички тези принципи, е технологията за производство на синтетичен чугун чрез пулсиращо смесване на метала вкофа, която включва следните основни стъпки:
- зареждане на феросилиций в горещ коф след източване на желязо от него на мястото на леярските машини;
- транспортиране на кофата до доменни пещи, по време на което феросилиций се загрява предварително поради енталпията на облицовката на кофата (1,5-2,0 h);
- пълнене на кофата с чугун, при което поради положението на феросилиция на дъното на кофата се получава неговото „замръзване“;
- транспортиране на кофата с чугун до блока за обработка извън пещта (0,8-1,2 часа), по време на което се извършва последващо нагряване на феросилиций до точката на топене;
- разтваряне на феросилиций в чугун в процеса на пулсиращо смесване (14-15 минути) чрез измиване на "замразения" феросилиций с пулсираща наводнена струя чугун.
Технологията и промишлената инсталация са тествани в условията на Донецкия металургичен завод (фиг. 2.13).
Проучванията показват, че степента на асимилация при пулсиращо смесване може да бъде 90-95% дори за ненатрошен феросилиций. Съществуващите, макар и доста незначителни, загуби на феросилиций очевидно са свързани с факта, че при взаимодействието на феросилиция с пулсиращи струи чугун, част от парчетата изплуват на повърхността и попадат в шлаката, където тяхното топене е значително затруднено. Освен това е установено, че когато чугунът се източва на машина за изливане, известно количество чугун (обикновено не повече от 2 тона) почти винаги остава в кофата, което не се взема предвид при определяне на степента на усвояване на феросилиций.
Степента на усвояване на феросилиция зависи от температурата на чугуна в кофата и за чугуна с недостатъчно висока температура тя значително намалява (фиг. 2.14), тъй като неговото топенеспира, когато температурата на желязото падне под точката на топене на феросилиция. Установено е, че неразтопеният феросилиций остава "замръзнал" до дъното на кофата и се разтваря при последващо изливане, което може да доведе до производството на некачествен чугун.
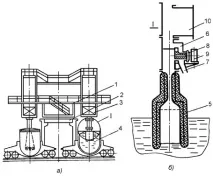
Фигура 2.13- Пилотна инсталация за пулсиращо смесване на желязо: 1-работна количка с валове; 2-естакада; 3-карета; 4-чугунен черпак с метал; 5-линейна потопяема колона; 6.7-тръба за отвеждане и подаване на газ; 8-разпределителен вентил; 9-клапанно задвижване; 10 приемник
От гледна точка на намаляване на разходите за получаване на синтетичен чугун, използването на феросилиций без допълнително раздробяване е от значителен интерес (обикновено феросилиций се доставя на парчета с максимален линеен размер 300-350 mm). Степента на асимилация на феросилиция обаче намалява с поне 20-25% поради изкачването на големи парчета в шлаката. Увеличаване на степента на асимилация (до 93-94%) в този случай може да се постигне чрез намаляване на дълбочината на потапяне на пулсиращата колона с 1,5-3,5 пъти в последните 0,25-0,50 от периода на обработка, което стимулира смесването на горните слоеве чугун с плаващи парчета феросилиций.
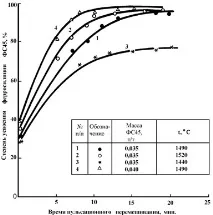
Фигура 2.14- Степени на усвояване на натрошен феросилиций FS45 за различни температури на чугун и продължителност на пулсационна обработка
В комбинация с разглежданата технология за производство на синтетичен чугун е изследвана възможността за десулфурирането му със слитък магнезий в кофа. От гледна точка на осигуряване на минимална продължителност на лечението, най-предпочитано е последователното разтваряне на феросилиций и след това третиране с магнезий. В този случай продължителността на пулсиращото смесване може да бъдеда се намали до 7-10 минути, тъй като по-късно чугунът се смесва интензивно по време на десулфуризацията. В същото време ефективността на използването на магнезий за десулфуризация на синтетичен чугун е поне не по-ниска от тази на конвенционалната доменна пещ. Това очевидно се дължи на факта, че температурата на синтетичния чугун е малко по-ниска по време на обработката. Характерна особеност на метода за производство на синтетичен чугун чрез пулсиращо смесване е постигането на висока химична еднородност не само в макро, но и в микро обеми. Проучванията, проведени с помощта на рентгенов микроанализатор MS-46 "Cameca", показаха, че концентрационните профили на разпределение на силиция в синтетичния чугун и чугуна от доменни пещи са почти еднакви.
Обобщавайки прегледаните проучвания, може да се твърди, че в цеховете за доменни пещи на металургичните заводи има достатъчно възможности за фина настройка на чугуна до нивото на висококачествено леярско желязо, което представлява значителен интерес за потребителите - леярни на машиностроителни заводи. Разбира се, ако е необходимо да се получат висококачествени отливки, леярните ще се интересуват от закупуването на оригиналния висококачествен чугун.
Що се отнася до обработката на чугун извън пещта директно в леярни, според нас основната му област на приложение може да бъде до голяма степен ограничена до регулиране на химическия състав на чугуна до регулиран състав, както и неговата модификация и микролегиране за висококачествени продукти за критични цели. В този случай много по-малки количества лигатури ще бъдат въведени в чугуна, което в крайна сметка не изисква значителни топлинни вложения за тяхното топене или асимилация. Методи за въвежданемодификатори и основни сплави в метала също могат да бъдат различни: натрошени материали, инжектиране на прахове, прахообразна тел и др. Изглежда най-целесъобразно и ефективно да се въведат сплави и други материали едновременно с интензивно смесване на стопилката.
При избора на оптимални методи за обработка на чугун и методи за въвеждане на добавки, механизмът и кинетиката на разтварянето на феросплав (или друг материал) в течен чугун са от голямо значение. В зависимост от съотношението на температурата на топене на входящия материал TP се разграничават температурата на кристализация на чугуна TK и температурата на чугуна в PT кофата, стопима (TP PT). Такова условно разделение на въведените в метала материали позволява да се сравни кинетиката на тяхното разтваряне в чугун (фиг. 2.15). По този начин процесът на разтваряне на нискотопима феросплав протича на три етапа. По време на първия етап феросплавта се нагрява до точката на топене и върху повърхността му "замръзва" твърда кора от чугун.
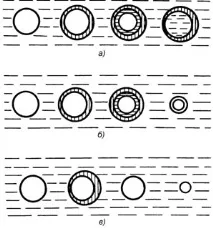
Фигура 2.15- Схематично представяне на кинетиката на топене на нискотопима (a, b) и огнеупорна (c) феросплав в чугун
На втория етап феросплавта започва да се топи под „замръзналата“ кора и в зависимост от специфичните условия (големината на топлинния поток и топлофизичните свойства на феросплава), периодът завършва или с пълното разтваряне на феросплава, или с пълното разтопяване на твърдата обвивка и потапянето на неразтопената част от парчето феросплав в стопилката. По време на третия етап завършва или разтварянето на твърдата обвивка, или разтварянето на входящия материал. Образуването на течна фаза на феросплав под твърда обвивка може в крайна сметка да причини появата на пукнатини в нея (обемът на течната феросплав е по-голям от този на твърдата) и изтичане на течна феросплав, коетоинтензифицира процеса на неговото разтваряне поради локално прегряване на стопилката. Напукването на обвивката на "замръзналата" стомана, например, във връзка с разтварянето на феросилиций увеличава скоростта на неговото разтваряне с 1,5-1,6 пъти. Процесът на разтваряне на огнеупорна феросплав в метал също може условно да бъде разделен на три етапа: на първия етап металът „замръзва“ върху парче феросплав, на втория етап феросплавта се нагрява до температурата на топене и кората се топи, а на третия етап феросплавта се топи и се разтваря в метала.
В съответствие с разглежданата класификация повечето индустриални марки феросплави, за разлика от стоманата, са огнеупорни на чугуна. Съответно е необходимо да се коригират методите за въвеждане на феросплави в стопилката. На първо място, можем да говорим за създаване на условия за дълъг престой на частиците на въведения материал в стопилката при условия на принудително смесване. Допълнителни възможности за подобряване на разтворимостта на модификатори и феросплави в течно желязо могат да бъдат създадени чрез придаване на въведените частици на специална геометрична форма, например под формата на плочи.