Дифузно хромиране
Хромирането е процесът на насищане на повърхностния слой на стоманата с хром, за да се повиши устойчивостта на корозия и топлината, а в случай на хромиране на високовъглеродни стомани, за да се повиши твърдостта и устойчивостта на износване.
При хромиране в прахообразни смеси частите се нагряват в стоманени кутии в смес, състояща се от 50% хром (ферохром), 49% алуминиев оксид (каолин) и 1% амониев хлорид. Използва се и смес, състояща се от 60% хром (ферохром), 35% алуминиев оксид (каолин) и 5% солна киселина. Натрошеният хром (ферохром) първо се обработва със солна киселина и след това се смесва с алуминиев оксид (каолин). Температура на хромиране 1000-1050°C, експозиция 6-12 часа, дебелината на получения слой е 0,08-0,15 mm върху части от нисковъглеродна стомана и 0,01-0,03 mm върху части от високовъглеродна стомана.
По време на хромиране в смес от хром (ферохром) с амониев хлорид протичат следните реакции:
Когато повърхността на нагрята част влезе в контакт с газообразен
хромният хлорид реагира
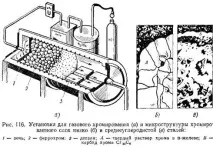
Полученият атомен хром дифундира в повърхността на детайла.
Газовото хромиране се извършва по следния начин: Смес от водород и хлороводород или газообразен хлороводород (хлор) преминава през ретортата, където се поставят ферохром (хром) и части (фиг. 116). В първия случай водородът преминава през концентрирана солна киселина и изместеният хлороводород, заедно с водорода, влиза в реторта, загрята до 950-1000 ° C. Когато ферохромът (хром) е изложен на хлороводород, се образува изпаряващ се хромен хлорид:
който дифундира в повърхността на детайла. След излагане в продължение на 5-6 часа се получава слой с дебелина 0,08-0,10 mm.
или 20-25% прах
ферохром. След излагане на 10-15 минути, слой с дебелина0,01-0,03 mm; недостатъкът на този метод е намаляването на активността на банята поради натрупването на реакционни продукти.
Повърхностната твърдост на детайлите, изработени от хромирана нисковъглеродна стомана, е ниска - HV 180-280, а частите, изработени от високовъглеродна стомана, достигат NU 1350 и надвишават твърдостта не само на карбуризирана и закалена стомана, но и на азотирана. Хромираният слой върху детайли от средно и високо въглеродни стомани има висока устойчивост на износване. Хромираният слой върху части от нисковъглеродна стомана има добра пластичност; частите могат да бъдат огънати, разместени, сплеснати и т.н. Хромираният слой върху детайлите от високовъглеродна стомана има повишена крехкост, особено при остри ръбове, което е основният му недостатък.
Антикорозионните свойства в много среди (разтвори на сол, морска вода, сяра и въглероден диоксид и др.) Имат хромирани слоеве, получени върху части, изработени от всяка стомана, но стоманата с карбиден слой е по-устойчива, която се съпротивлява добре на действието на 20% солна киселина и 30-50% азотна киселина. Топлоустойчивостта на хромираната стомана е ограничена до температура от 800 ° C. Различни части са подложени на хромиране: компресорни клапани, втулки на помпата, матрици за студена глава и др.