Физични и механични свойства
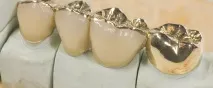
Физични и механични свойства на метали и метални сплави
Металите имат различни цветови нюанси на почти целия спектър, но като правило за неблагородните метали е сиво, синкаво, синкаво с различна степен на тежест и различни комбинации. Благородните метали се характеризират с жълто-оранжева гама и белезникаво-сребрист оттенък; тези вещества имат доста висока плътност (виж Таблица 20). Така плътността на златосъдържащите сплави е 14-18 g / cm3, плътността на кобалтово-хромовите сплави (виж таблици 39-40) е 8,4 g / cm3, плътността на никело-хромовите сплави (виж таблица 37) е 8,2 g / cm3. Както вече споменахме, те са топло- и електропроводими и съответно се разширяват и свиват при нагряване и охлаждане.
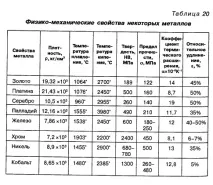
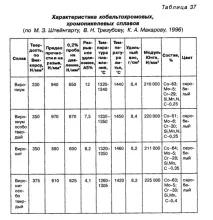
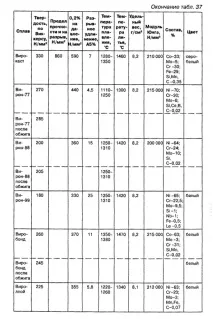
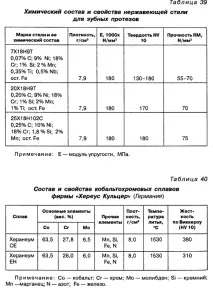
Точката на топене на металите (виж таблица 20) варира в широки граници. В тази връзка се изолират топими метали с точка на топене, по-ниска от тази на чистия калай (232 ° C), както и огнеупорни метали, чиято точка на топене е по-висока от тази на желязото (1535 ° C). Между тези полюси са средните температури на топене, характерни за повечето метали и сплави. Точката на топене и точката на втвърдяване на чистите метали винаги е постоянна и докато една фаза изчезне - топенето на твърдата част при нагряване или втвърдяването на течната част при охлаждане - температурата остава непроменена.Пластичната деформация води до промяна на физичните свойства на метала, а именно: - увеличаване на електрическото съпротивление; - намаляване на плътността; — промяна в магнитните свойства.
Всички вътрешни промени, които възникват по време на пластичната деформация, причиняват втвърдяванеметал. Характеристиките на якост (якост на опън, граница на провлачване, твърдост) се увеличават, докато пластичните характеристики намаляват.
Закаляването на метала под действието на пластична деформация се нарича работно закаляване.
Твърдо обработените (закалени) метали са по-податливи на увреждане от корозия по време на работа. За да се премахне напълно втвърдяването, металите се подлагат на рекристализиращо отгряване.
Рекристализацията е процес на възникване и растеж на нови недеформирани кристални зърна на поликристал за сметка на други зърна.
Рекристализацията се използва на практика, за да се даде на материала най-голяма пластичност. Освен това, той протича особено интензивно в пластично деформирани материали при по-високи температури. Температурата на рекристализация е от голямо практическо значение. За да се възстановят структурата и свойствата на закаления (напрегнат) метал (например при щамповане на короната под налягане след набиване на втулката върху модела мелот), той трябва да се нагрее над температурата на рекристализация.
Наборът от свойства, характеризиращи устойчивостта на метал и сплав към действието на външни механични сили (натоварвания), приложени към него, обикновено се нарича механични свойства.
Силите могат да бъдат приложени като товар:
- статичен (плавно нарастващ);
- динамични (нарастващи рязко и с висока скорост);
- повторно променлива (многократно прилагана, променяща се по големина и посока).
Съответно механичните изпитвания се разделят на:
- статични (опън, компресия, огъване, усукване, твърдост);
— динамични (ударно огъване);
- умора (при многократно променливо натоварване);
- висока температура(например за дълготрайна сила).
По правило всички тестове се провеждат при определени условия върху проби с дадена форма и размер, т.е. съгласно международни и национални стандарти, което гарантира сравнимостта на получените резултати и тяхната правилна интерпретация.
Когато се разтяга или компресира, пробата има способността да устои на еластични деформации, което определя твърдостта на материала - модула на еластичност E. Размерът на модула на еластичност E в системата SI е Pascal (Pa, N / m2) или Megapascal (MPa, N / mm 2). Границата на еластичност е посочена както следва - ?0,05. Таблици 22 и 23 показват теоретичната и действителната якост на някои материали.
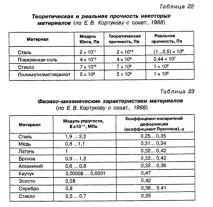
Металите се характеризират с висока якост (виж таблици 20, 21). В същото време някои от тях могат да бъдат пластмасови или еластични (пружинирани), докато други, напротив, са крехки. Крайната якост на златните сплави е по-ниска от якостта на лятите кобалтово-хромови сплави (виж таблица 41). Високата якост затруднява завършването на конструкцията на протезата, но е устойчива на повреди по време на нейната работа (предимно абразия).
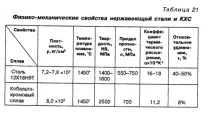
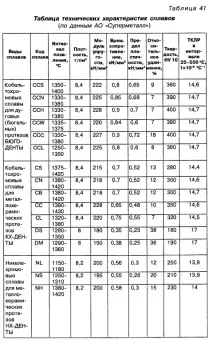
От всички механични тестове най-често се определя твърдостта, тъй като методът е лесен за използване.
Основните методи за определяне на твърдостта са методи за въвеждане на стандартни накрайници, изработени от твърди недеформируеми материали, в повърхността на изпитвания метал под действието на статични натоварвания:
- Метод на Бринел (вдлъбнатина на стоманена топка с определен диаметър);
- Метод на Рокуел (вдлъбнатина на диамантен конус или топка от закалена стомана с диаметър 1,58 mm);
- Метод на Викерс (вдлъбнатина на тетраедрична диамантена пирамида с квадратна основа).
Твърдост по Рокуел обозначават HRA, HRB, HRC (в зависимост от приложената скала A, B или C).
Твърдостта по Викерс (HV) има същата единица като числата за твърдост по Бринел, т.е. MPa или kgf/mm 2 . Числата на твърдост по Викерс и Бринел за материали с твърдост до HV 400-450 всъщност съвпадат (виж таблица 41). Твърдостта като характеристика на сплавта е тясно свързана с другите й параметри. Така например, с увеличаване на твърдостта на златните сплави, границата на провлачване и якостта на опън също се увеличават, а с увеличаване на твърдостта и якостта, удължението намалява. Микротвърдостта на метална сплав (фиг. 10) може да се промени по време на леене чрез излагане на електромагнитно поле с различни честоти, което прави възможно получаването на сплав с желаните свойства [Бобров А.П., 2001].
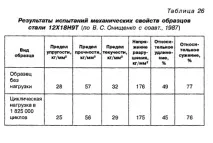
В резултат на цикличните напрежения металът се "уморява", силата му намалява (виж таблица 26) и настъпва разрушаване на пробата (протеза). Това явление се нарича умора, а устойчивостта на умора се нарича издръжливост. Разрушаването от умора винаги възниква внезапно поради натрупването на необратими промени в метала, които водят до появата на микроскопични пукнатини - пукнатини от умора, които се появяват в повърхностните зони на пробата. В този случай, колкото повече драскотини, дупки и други дефекти, които причиняват концентрация на напрежение върху повърхността, толкова по-бързо се образуват пукнатини от умора.