Изчисляване на производството на азотна киселина
Описание на технологията за производство на азотна киселина под налягане. Блокова схема на производството на азотна киселина. Материалните потоци влизат и излизат от реакционния блок. Етапи на окисляване на амоняка, материален баланс на окисление на азотен оксид.
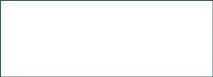
Изпратете добрата си работа в базата знания е лесно. Използвайте формата по-долу
Студенти, докторанти, млади учени, които използват базата от знания в обучението и работата си, ще ви бъдат много благодарни.
Хоствано на http://www.allbest.ru/
Азотната киселина е окислителна минерална киселина, чиито физични и химични свойства я правят един от най-ценните неорганични минерали. Азотната киселина се използва широко в промишлеността, като най-разпространени са производството на експлозиви, азотни торове и багрила.
Първоначално азотната киселина се произвежда с различни производствени методи; през 1914 г. в Донецк е разработен завод за азотна киселина, базиран на коксов газ амоняк, който през 1916 г. е пуснат в експлоатация. Сега получаването на азотна киселина от амоняк е основният метод за нейното производство. Процесът включва три основни етапа, първият е окисляването на амоняка за получаване на азотен оксид, вторият е окисляването на азотния оксид за получаване на азотен диоксид и тетроксид и накрая, адсорбцията на азотни оксиди във вода за получаване на азотна киселина [1].
4NH3 + 5O2 = 4NO + 6H2O - реакцията на окисление на амоняка е екзотермична, протича в областта на външната дифузия върху платинов катализатор под формата на решетки; температура
800 - 900 0С; концентрация на NH3 - 10%;
NO + O2 = NO2 - газофазова реакция, обратима, екзотермична;
2NO2 + H2O + O2 = 2HNO3 е хетерогенен ("газ - течност") химичен процес с допълнително окисление.
Описание на технологията за производство на азотна киселина под налягане 7.3 MPa [2]
При синтетично получаване на азотна киселина най-рационално е амонякът да се окислява при атмосферно налягане, а абсорбцията на азотни оксиди - при високо налягане. Тази целесъобразност е продиктувана от факта, че при окисляването на NH3 под налягане разходът на платина се увеличава значително, тъй като тя по-бързо губи своите каталитични свойства и се отнася в по-голяма степен от азотистите газове. Въпреки това, проектирането на рентабилни машини за компресиране на азотни газове причинява значителни трудности, в резултат на което при работа при налягане от около 6-8 MPa все още се счита за най-целесъобразно да се компресира сместа амоняк-въздух преди контакт с нея. Процесът на получаване на синтетична азотна киселина при налягания от 6-8 MPa е принципно същият като процеса на получаването й при атмосферно налягане. Отличителни черти на технологията и оборудването на първия от тези процеси са следните.
1. Амонячно-въздушната смес навлиза в контактния апарат при налягане 6-8 MPa и същото налягане се поддържа във втория и третия етап на производство, т.е. охлаждането на азотните газове и тяхната абсорбция се извършват при същото налягане. В резултат скоростта и степента на окисление на NO, както и скоростта на химичното взаимодействие на NO2 с водата, се увеличават значително. Следователно при инсталации, работещи при повишено налягане, обемът на оборудването е много по-малък, отколкото при инсталации с атмосферно налягане.
2. Поради факта, че образуването на азотна киселина от азотни оксиди става под налягане, нейните разтвори след напускане на системата за охлаждане и абсорбция съдържат значително количество разтворени азотни оксиди. Следователно, вЗа да се намали загубата на тези оксиди и следователно да се увеличи степента на превръщането им в HNO3, азотната киселина се подлага на продухване с въздух след абсорбционната колона. Когато това се случи, отстраняването на разтворените азотни оксиди от него и по този начин избелването му. Получените при това продухване азотни оксиди се връщат обратно в абсорбционната система. На диаграмата е показана опростена схема за производство на синтетична азотна киселина при налягане 6-8 MPa.
Въздухът след цялостно почистване във филтъра постъпва в турбокомпресора, в който поради енергията на компресията се загрява до 120-140°C. Оттук сгъстеният въздух се насочва към нагревателя. Нагрятият амоняк се изпраща в миксера. Амонячно-въздушната смес от смесителя се изпраща към контактния апарат. Когато NH3 се окислява, температурата на газа върху катализаторните мрежи достига 900-950°C. Поради това долната част на контактния апарат се охлажда с вода. За да се избегне замърсяването на амонячно-въздушната смес с корозионни продукти, всички тръбопроводи от филтъра до контактния апарат са изработени от хром-никелова стомана, а горната част на този апарат е от никел. При излизане от контактния апарат азотистите газове навлизат в котела-утилизатор, оттук в нагревателя на отработените газове и след това във водния охладител-кондензатор. В първия от тези апарати газовете се охлаждат до 380-400°C, във втория - до 180-200°C и в хладилника - до 35-40°C. В котела-утилизатор топлината на азотните газове се използва за получаване на водна пара, а в подгревателя се използва за нагряване на компресираните отработени газове, напускащи абсорбционната колона. След това 15-20% от енергията на компресия на тези газове се използва в разширителната турбина на турбокомпресора. Поради кондензацията на водни пари в хладилника се образува 30% азотна киселина. В газовия сепаратор тази киселина се отделяот неабсорбирани азотни газове, преминава през специален филтър за улавяне на платината и се изпраща в абсорбционната колона и след това в колоната за продухване. В първата от тези колони концентрацията на азотна киселина се повишава до максимум (58-60% HNO3) при тези условия поради абсорбцията на азотни газове, идващи тук от газовия сепаратор. Към същата колона се подава вода и допълнителен сгъстен въздух. Във втората колона киселината се освобождава от разтворените в нея азотни оксиди чрез нагряване с мъртва пара и продухване със сгъстен въздух. От колоната за продухване избелената азотна киселина влиза в склада за готов продукт; концентрацията му е 58-60% HN03. Тарелкови абсорбционни и продухващи колони. Киселината в тях се стича по плочите към газовете: в първата колона - азотен, във втората - сгъстен въздух.
Отработените газове от двете колони влизат в скрубера, който се напоява с концентрирана сярна киселина. В това устройство остатъците от азотни оксиди, съдържащи се в отработените газове, се абсорбират от сярна киселина, която под формата на нитроза се използва при производството на сярна киселина по метода на кулата. Степента на превръщане на NO в азотна киселина в инсталации, работещи при налягане 6-8 MPa, достига 97-98%.
Структурна схема на производство на азотна киселина:
Технологични единици на опростена схема: