Изчисляване на условията на рязане по време на струговане с помощта на справочна литература
Целта на работата: Да се проучи методът за настройка на режима на рязане според таблиците на стандартите. Запознайте се и придобийте умения за работа с нормативната уредба.
Струговането е широко използван метод за обработка на въртящи се тела чрез рязане.
Използва се за премахване на външните, вътрешните и крайните повърхностни слоеве на детайлите (цилиндрични, конусни и фасонни). Помислете за следните видове завъртане:
1) грубо струговане ("пилинг") - отстраняване на дефектни слоеве на детайла, рязане, отрязване и подрязване на краищата на детайла. Повърхностната "кора" и основната (>70%) част от резерва за обработка са отрязани, което прави възможно получаването на грапавост от 50. 12.5 Ra;
2) полуфинално струговане - премахване на 20,25% от надбавката и ви позволява да получите грапавост от 6,3. 3.2 Ra и точност 10. 11 клас. Заготовката получава форма, близка до детайла.
3) фино струговане - осигурява грапавост 3,2. 1.6 Ra и точност на 7-9-та квалификация. Детайлът получава окончателната си форма и размери;
4) фино струговане - позволява при рязане на много тънки чипове да се получи на повърхностите на частта грапавост от 0,40..0,20 Ra и точност от 5-7 степени.
Определянето на условията на рязане се състои в избора на най-изгодната комбинация от дълбочина на рязане, подаване и скорост на рязане за дадените условия на обработка, осигуряваща най-малко трудоемкост и цена на операцията.
Условията на рязане се задават в следния ред:
1. Определяне на дълбочината на рязане t mm и броя на проходите i. При грубо струговане е препоръчително да се отстрани цялата надбавка с едно минаване (в някои случаи, когато има ограничение на мощността на машината, може да е изгодно да се премахне надбавката на няколко минавания). Целесъобразността на това трябва да се определи чрез сравнително изчисляване на продължителността на оперативното време. дивизиядопуски за няколко прохода също са направени за полуфинално и крайно струговане, както и за машинна обработка
фрези с допълнителен режещ ръб (j1=0).
2. Избор на подаване S mm/rev. Подаването се избира в зависимост от площта на напречното сечение на държача на ножа, диаметъра на обработка и дълбочината на рязане. Избраното захранване се проверява за допустимост по мощността на електродвигателя, здравината на държача на ножа, здравината на твърдосплавните пластини и определената чистота
3. Определяне на стандартната скорост на рязане Vm/min. И съответстващата му честота на въртене n, min -1. Според стойността на скоростта се избира необходимата скорост на шпиндела, която се коригира според паспорта на машината.
4. Силите и мощностите на рязане се определят според избраните стойности на t, S и V.
5. Проверка на възможността за изпълнение на избрания режим на рязане на дадена машина според нейните експлоатационни данни. Ако намереният режим не може да се изпълни на дадена машина и избраното подаване удовлетворява, е необходимо да се намали скоростта на рязане. Намаляването на скоростта V се извършва чрез въвеждане на корекционен коефициент за промяна на скоростта Kv, в зависимост от съотношението на мощността на шпиндела, разрешена от машината, към мощността съгласно стандартите.
6. Корекция на избрания режим за машината в съответствие с нейните паспортни данни.
Пример за решение на проблем
Изчислете режима на рязане при предварително завъртане на част от типа вал
Изходни данни: вид и размер на детайла - валцована стомана, стомана 45; sv=550
MPa; D=80 mm; d=68 mm; l=275 mm; условия за извършване на операцията - празно
се монтира в самоцентриращ се патронник с предварително натоварен център на опашката.
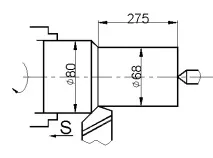
Изпълнение на скица за обработка.
2. Избор на режещ инструмент.
За въртене на стоманен вал 45приемаме стругова фреза права дясна с пластина от твърда сплав Т5К10 [2] или [3] j=45°; j1=10°; c=4 mm (дебелина на плочата); ВхН=25х25 (държач секция); Ip=1,5 N (надвес
3. Назначаване на режими на рязане.
Изчисляването на условията на рязане се извършва в традиционната последователност с
използвайки данните от [7].
3.1 Дълбочина на рязане. При грубо обработване изрязваме надбавката наведнъж
мм
3.2 Задаваме терен. За държач на фреза със сечение 25x25 mm, диаметър на обработка до 100 mm и дълбочина на рязане до 8 mm се препоръчва подаването S = 0,5. 0,7 мм/об.;
и за ножа j1> 0° се допуска подаване S = 0,7 mm/об. За стомана с якост на опън sv = 550 MPa (55 kg / mm 2) корекция
коефициент Kms=1.07. Следователно допустимото подаване от мощността на електродвигателя (от условията за осигуряване на работа за твърда сплав със скорост минимум 50 m/min) S=0,7×1,07=0,75 mm/об. За фреза с държач със сечение 25x25 mm и дълбочина на рязане t=6 mm намираме подаването S=3 mm/об. Умножавайки това захранване с корекционния коефициент Kms \u003d 1,07, съответстващ на стомана с якост на опън sv \u003d 550 MPa (55 kg / mm 2), и Kms \u003d 0,58, съответстващ на обхвата
нож l=1,5 H, намираме допустимото подаване от силата на държача на ножа:
За фреза с основен ъгъл в план j=45°, дебелина на плочата от твърда сплав c=4 mm и дълбочина на рязане t=6 mm намираме подаването S=1,11 mm/об.
Като се вземе предвид корекционният коефициент за стомана (sv = 550 MPa), Kms = 1,07, е разрешено да се достави плоча от твърда сплав според якостта
От сравнението на подаванията S=0,7 mm/rev, S=1,86 mm/rev и S=1,19 mm/rev, виждаме, че скоростта на подаване ограничава мощността на електродвигателя. Подаване, разрешено от мощността на двигателя, не ограничава максималното подаване S=0,7 mm/об. Такъв терене наличен на машината (според паспортните данни), следователно ще го приемем за извършване на технологичния преход на обработка Æ68.
3.3. Скорост на рязане и скорост на шпиндела.
За дълбочина на рязане t=6 mm на прав фреза с водещ ъгъл j=45° за S=0,7 mm/об.
съответства на V=100 m/min, Pz=6630 H, Ne=10,7 kW. Определяме корекционните коефициенти за променените условия на фрезата. В този пример е необходимо само да се вземе предвид корекционният коефициент в зависимост от якостта на опън на обработвания материал sv. За sv=550
MPa намираме Kmv = 1,18, , .
Следователно, за дадените условия на обработка стандартните стойности на V, Pz и Ne са: V=100×1.18=118 m/min; Pz=6630×0,92=6100 N; Ne=10,7×1,09=11,6 kW.
Намереният режим не може да бъде приложен на дадена машина, тъй като ефективната мощност, необходима за рязане Ne = 11,6 kW, е по-висока от мощността на шпиндела, допустимата номинална мощност на електродвигателя (7,5
kW според паспорта на машината). Скоростта на рязане трябва да се намали. Коефициентът на изменение на скоростта на рязане зависи от съотношението на мощността на шпиндела, разрешена от машината, към мощността по стандартите.
В този пример това съотношение ще бъде 7,5/11,6=0,6. За това съотношение коефициентът на промяна на скоростта на рязане: Kv \u003d 0,55 m / min. Скорост на рязане, зададена според мощността на машината, V=188×0,55=65 m/min
Скорост на шпиндела
об/мин
Според паспорта на машината избираме n \u003d 250 rpm. След това действителната скорост на рязане
м/мин.
Накрая за преход на обработка Æ80: дълбочина на рязане t=6 mm, подаване
S=0,7 mm/об, n=250 rpm, Vf=62,8 m/min.
4. Редовно време
мин. където L е пътят на фрезата
тук l1 е стойността на подаването на ножа (за този пример).За дълбочина на рязане t=6 mm и основен ъгъл в план j=45° намираме l1=6 mm; l е дължината на обработваната повърхност.