Изработка на фибростъклен фюзелаж на авиомодел
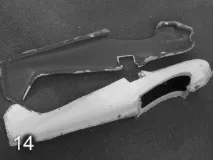
Изработка на фибростъклен фюзелаж на авиомодел.
Композитни материали в моделирането. Автор: В. Ходеев
Списание "Modelist" (№ 4, 2009 г., № 1 2010 г.) вече публикува материали за преглед на композитни материали, технологията за производство на негативни форми и в този материал ще разгледаме процеса на производство на детайл в калъп.
Има няколко начина за залепване на композитни продукти. Мисля, че много хора са запознати със „страшната“ технология с вакуумна торба и помпа. Такъв трудоемък метод е необходим при използване на сандвич ламиниране, където има слоеве от фибростъкло, балса или пяна. Ще разгледаме обичайния метод "без вакуум" за ламиниране от фибростъкло, в нашия случай фюзелажа на самолета. Тази работа се състои от няколко етапа: обработка на формата със сепаратор, нанасяне на повърхностен слой, ламиниране, включително сглобяване на формата и залепване на шева, отстраняване на готовия продукт.
Обработка на формуляра с разделител
Преди да започнете работа по ламиниране, е необходимо да подготвите формуляр.
Композитна форма за залепване на фюзелажа |
Същността на този препарат е да се третира с разделителен слой, който ще предотврати залепването на продукта върху формата.
![]() |
Нанасяне на гелкоата върху матрицата с пистолет |
Като основен разделителен материал се използва специален мехлем (восък). По правило този материал се основава на пчелен восък. Мехлемът се нанася с мек памучен (!) парцал върху повърхността на формата и фланеца, оставя се да изсъхне за 10-15 минути и се полира с лек сух натиск.плат (памук) салфетка. Както вече беше описано в предишната тема, производителят (например R&G) препоръчва нанасяне на 4-5 слоя мехлем с прекъсване за изсъхване (втвърдяване) на всеки слой за 4-6 часа. Този брой слоеве създава плътна лъскава защитна обвивка върху повърхността на формата. Невъзможно е да бързате на този етап от работата, ако не се придържате към тази технология, можете да разрушите формата и много скъпи материали. Също така не си струва да експериментирате със замяната на сепаратора с други продукти, като мастика за паркет, сапун и т.н. Необходимо е да се купуват само модерни, специално проектирани компоненти за тази цел. При производството на големи или сложни (с много издатини) детайли, както и при първото формоване на продукт в нова форма, се препоръчва използването на друг много ефективен разделител, това е течен PVA разделител. Нанася се върху повърхността с мека четка или фин спрей. Изсъхвайки (приблизително 20-30 минути), разтяга се и създава най-тънкия гланцов филм. PVA освобождаващият агент се нанася само върху повърхността на формата, предварително обработена с освобождаващ мехлем. След отстраняване на залепената част от формата върху нея остава PVA сепараторът, който лесно се отмива с вода. При подготовката на матрицата за залепване на втория продукт е необходимо да се нанесат още 2-3 слоя разделителна паста със съхнене. При последваща работа един слой ще бъде достатъчен. Според препоръките на производителите, по-нататъшната работа може да започне не по-рано от 4 часа след обработката на матрицата с освобождаваща паста.
Повърхностен слой
И така, формулярът се обработва от разделител. Следващият етап от работата е нанасянето на слой гелкоат, грубо казано, боядисване на формата. Gelcoat е родовото име за полиестерен материал.приложен към съзнанието за идеалната повърхност на композитен продукт.
Този слой създава идеална повърхност върху готовия продукт и предотвратява образуването на микропори, които задължително се появяват поради въздушни мехурчета в смесената смола. Изсъхналият слой на гелкоата е здраво свързан с епоксида при ламиниране. Ако залепите части без този слой, тогава при боядисването му веднага ще се появят порите и ще ви създадат редица проблеми. Е, външният вид на самия продукт ще бъде перфектен, бял и в много случаи изобщо не изисква боядисване! Гелкоутът също така предпазва епоксида от ултравиолетова светлина и създава декоративен и издръжлив слой върху външната повърхност на композитния продукт. Преди употреба към него се добавя течен втвърдител. За нанасяне със спрей може леко да се разреди с ацетон. Качеството на нанесената повърхност не играе никаква роля, тъй като тя ще бъде вътрешният компонент на композитния слой, а "лицето" на детайла ще бъде гладка повърхност, която ще бъде отпечатана във формата. Важно е да бъде равномерен, достатъчно дебел ("мазнен") слой. Трябва да се има предвид, че този материал има много остра летлива миризма, което означава, че работата с него трябва да се извършва в добре проветриви помещения и в респиратор.
Поставяне на част
След като слоят гелкоат е напълно изсъхнал (при температура 25 градуса, около 5-8 часа), можете да започнете ламинирането на продукта. Тук говорим за процеса на залепване на композитни части от фибростъкло и специална "патентована" епоксидна смола. За разлика от "съветската епоксидна смола", тези смоли имат приблизително течна консистенциякато слънчогледово масло и още по-разреден втвърдител. На външен вид тази смола е безцветна, прозрачна и без мирис. Втвърдителят е предимно син на цвят със силна миризма на амоняк. Например, при разреждане на най-често срещаната марка епоксидна смола Larit L-285 от Lange & Ritter, към нея се добавят 40% втвърдител, тоест за 100 грама тегловна смола, 40 грама втвърдител. Смола с такава доста течна консистенция се нанася върху тъканта с четка и лесно я импрегнира.
Всички работи с епоксидни и полиестерни материали трябва да се извършват със защитни ръкавици и в проветриво нежилищно помещение. В началото на работата разредената смола се смесва с памучен (микроцелулозен) пълнител до плътност на заквасена сметана и всички релефни места на формата се намазват с тази маса с тънък слой
![]() |
![]() |
Всички релефни места на формата се намазват със смола с пълнител |
Дълбоките места и ръбовете се запълват с по-дебела маса. Ако формата е голяма, ще бъде удобно да извършите тази работа, например, като използвате хартиена торбичка, навита около молив, като я използвате като спринцовка
След това можете да поставите фибростъклото. Първо трябва да се нареже на лесни за използване части, по-добре е да направите това според монтирани хартиени шаблони. Платът се разстила във форма и се глади с четка, потопена в смола.
![]() |
![]() |
Необходимо е да се гарантира, че под тъканта няма да останат въздушни мехурчета и да се нанасят смоли не повече, отколкото слоят тъкан може да абсорбира. |
Необходимо е да се гарантира, че под тъканта няма да останат въздушни мехурчета и да се нанасят смоли не повече, отколкото този слой тъкан може да абсорбира. Когато първият слой се постави във формата, точнопоставете втория по същия начин. Такава работа е лесна, фибростъклото не залепва за четката и прилепва добре към повърхността на матрицата. В зависимост от дизайна на продукта е възможно да се подсилят някои от ръбовете със сноп от въглеродни влакна, който трябва да се постави между слоевете плат. Какво и каква дебелина на фибростъкло да се използва за производството на части трябва да се определи практически. Що се отнася до структурата, най-добре е да работите с кепър, например, с тегло 163 g/m2. Фюзелажът на модела Me-109, върху който илюстрираме този материал, използва 2 слоя 163 g/m2 стъклен кепър. В областта на носа и централната част корпусът беше подсилен с въглеродна тъкан с тегло 160 g / m2, която беше поставена между слоевете от фибростъкло.
![]() |
Всички слоеве плат са подредени във форма |
Ако върху матрицата има сложни ъглови места, те трябва да бъдат формовани с малки парчета по-тънък фибростъкло, преди да се постави първият основен слой. След като цялата тъкан е положена в двете половини на матрицата, е необходимо да се отреже тъканта, стърчаща извън матрицата по периметъра на фланеца.
![]() |
Изпъкналият плат се подрязва с извити ножици "наравно" с фланеца |
По-добре е да направите това със специални извити медицински ножици. Но първо, на този етап, трябва да решите как ще бъдат залепени половинките на фюзелажа в сглобената форма. Тук има няколко варианта.
Съединяване на половинките на формата
В този случай нашата форма има голям отвор в носа и точките за закрепване на крилото, през които можете да получите достъп до обработката на ставата. Първи вариант: цялата тъкан се изрязва наравно с фланеца,формата се затваря, усуква се с болтове, а по линията на фугата отвътре се поставя фибростъкло.
![]() |
Свързаните половини на формата са усукани с болтове |
За удобство при залепване на тъканта в дълбочината на фюзелажа можете да фиксирате четката върху дълга релса или тръба. Един от колегите ми дори инсталира ярък светодиод на такава тръба, за да работи с корпуса на планера, така че качеството на шева да се вижда по-добре. Вторият вариант: върху първата половина на формата тъканта се изрязва само от дясната страна, а остава отляво. Във втората половина, напротив, те се изрязват само от лявата страна и се оставят отдясно. Така подготвените половинки на формата трябва да се затворят правилно с отместване, така че стърчащият плат да се застъпва от страната, където е изрязан.
След това, в свързана форма, линията на фугата се глади с четка. Тази опция създава най-трайното свързване на частите на продукта. Ако затворена част е направена без отвор или с труден достъп до шева, можете да използвате следната технология за свързване на частта във формата. По целия периметър на ръба на формата стърчащият плат се изрязва с извити ножици „наравно“ с фланеца. Изоставащата тъкан се изглажда до формата с четка, потопена в смола. След това по целия периметър на ръба (ръба на прехода на формата към фланеца) се нанася непрекъснато плъзгане (шев) с височина прибл. 3-5 mm от гъста маса от смола и пълнител (удобно е да използвате същата хартиена „шприц“). Това се прави на всяка половина на калъпа, след което се затваря и завинтва. В същото време и двата плъзгача смола ще се слеят, частично ще се изтласкат в частта и ще създадат силен „заваръчен“ шев. В някои случаи, в зависимост от дизайна на формата, може да се приложи комбинация от всички горепосочени опции. И така, детайлът е залепен,формата е усукана
![]() |
Фюзелажът е изваден от формата |
и го оставете да изсъхне. След работа можете да измиете четките първо с метанол, след това със сапун и вода, така че те все още да са подходящи за по-нататъшна работа. Не по-рано от 24 часа можете да започнете да отваряте формата и да отстранявате корпуса. Всички болтове се развиват, след което нож и малки букови клинове се вкарват внимателно, с малко усилие, в линията на кръстовището на половинките на формата. По този начин, по целия периметър, бавно вкарвайки и задълбочавайки нови клинове, можете да отворите половината форма. Ако разделителят е приложен според технологията, тогава половината от формата се отваря без много усилия.
Можете също така да премахнете частта от втората половина, като леко завъртите матрицата в различни посоки. Върху готовия фюзелаж тънката част от шева се отстранява с ножица и след това внимателно се изрязва с остър нож.