Концепцията за точност на обработката
Огромна роля за осигуряване на необходимото качество на продукта принадлежи на точността на обработката на частите и тяхното сглобяване в готови продукти.
Точността на обработката се разбира като степента на съответствие на произведения детайл с дадените размери, форма и относително разположение на неговите повърхности, тяхната грапавост, както и механични и физични свойства. Точността на обработката се определя от общата резултатна грешка, причинена от комбинираните действия на всички фактори, които възникват в процеса на получаване на детайла.
Различни производствени фактори могат да причинят систематични (постоянни и променливи) и случайни грешки.Постояннасистематична грешка е например грешката на всички отвори, обработени от райбер, който има отклонение в размера от определения.
Къмпроменливисистематичните грешки включват, например, непрекъснато променящи се размери на дълъг вал, когато се обработва с нож поради износване на последния.
Случайниса такива грешки, които имат различни стойности в обхвата на дадена задача, чийто момент на възникване и точната стойност не могат да бъдат определени предварително (при дадено ниво на развитие на науката). Поради действието на различни производствени фактори е невъзможно да се получат части с абсолютно точни размери при обработка. Действителният размер на детайла, разкрит чрез директното му измерване след обработка, винаги ще се различава от номиналния размер, посочен в чертежа.
Номиналният размер е основният проектен размер, спрямо който се определят допустимите гранични размери; тя е отправна точка за отклонения.
Правете разлика между най-големия и най-малкия граничен размер. Има и горно отклонение като алгебрикаразликата между най-големия граничен и номиналния размер. Долно отклонение - алгебричната разлика между най-малката граница и номиналните размери.
Толерансът е разликата между най-големия и най-малкия граничен размер или абсолютната стойност на алгебричната разлика между горното и долното отклонение. Допустимо поле - поле, ограничено от горни и долни отклонения. На фиг. 17.1 показва пример за настройка на максималните размери и отклонения на вала.
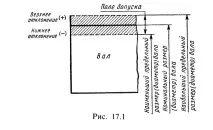
Прието е всички външни (покрити) повърхности да се наричат вал, а вътрешните (покриващи) повърхности - дупка. Характерът на връзката на частите (отвор и вал), определен от големината на пролуките и произтичащите от това смущения, се нарича годност. Когато размерът на вала е по-малък от размера на отвора, има хлабина. Ако размерът на вала преди сглобяването надвишава размера на отвора, намесата е подходяща. Има и преходни сглобки, при които могат да се получат както хлабина, така и намеса, тъй като полетата на толеранс на отвора и вала се припокриват частично или напълно.
За детайлите на всякакви връзки е установен принципът на взаимозаменяемост.
Взаимозаменяемостта е свойството на независимо произведени части, възли да се сглобяват без монтаж и да изпълняват служебното си предназначение, без да нарушават техническите изисквания за продукта. Има размерна и технологична и функционална взаимозаменяемост.
Размерна и технологична взаимозаменяемост —осигуряване на изискванията за сглобяване (сглобяване и взаимна подмяна на части със същото име).
Функционалната взаимозаменяемосте осигуряване на работоспособността на продукта, запазване на неговата производителност през даден експлоатационен живот (например пружини).
Изискванията за монтаж се изпълняват чрез прецизностгеометрични параметри - размери, форма, относителна позиция на съединителните повърхности. Функционалните изисквания се осигуряват от точността на геометричните и физико-химичните параметри, които влияят върху работата на продукта.
Частите са взаимозаменяеми, ако номиналните стойности на техните параметри и допустимите отклонения на тези параметри (допуски) съвпадат.
Взаимозаменяемостта е от голямо техническо и икономическо значение, позволява организирането на широкомащабно и масово производство на части, които се подават директно към монтажа. Освен това, по време на работа на продукта в случай на счупване или износване на детайла, можете да го замените с друг, взаимозаменяем.
Действащите в СССР стандарти на Съвета за икономическа взаимопомощ (ST SEV 144-75 и ST SEV 145-75) създават единна система от допуски и фитинги за гладки връзки. Тази система установи 19 квалификации (01, 0, 1, 2, . 17), всяка от които установява набор от допустими отклонения, съответстващи на еднаква степен на точност за всички номинални размери.
Същите стандарти установяват различни кацания. Кацанията се избират според две системи - системата на отворите и системата на вала. В системата с отвори естеството на свързването на частите, определено от големината на пролуките или смущенията, произтичащи от него, се извършва поради размерите на вала, неговите максимални отклонения. В тази система отворът се счита за основен (обозначен с буквата H), чието долно отклонение е нула, а горното, независимо от естеството на прилягането, е постоянно за определено качество. В системата на вала основният вал (обозначен с букватаI)има горно отклонение равно на нула, а долният остава постоянен (в определено качество) независимо от напасването.
Обозначението за кацане включва номиналноторазмера, общ за отвора и вала, и след това символа за техните полета на толеранс, например:
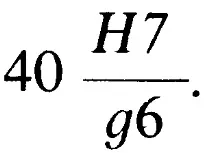
Това кацане е направено по системата на отворите, в която основният отворНе направен според 7-ми клас, а кацането -gпоради вала от 6-ти клас. В системата на вала за номинален размер 40 може да има такова напасване 40Р7 - h6.За избор на напасване според стандарта са предоставени 27 опции за полета на толеранс на вала: a, b, c, . и т.н. доzc(в системата на отворите) и същия брой за полетата на толеранс на отворите:A, B, C, .и t.за доZC(в системата на вала).
Графично представяне на кацанията в системите за отвори и валове е показано на фиг. 17.2.
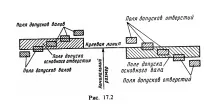
Системата с отвори е най-често срещаната. По-икономичен е, тъй като граничните размери на отвор с всякакъв номинален диаметър и качество остават постоянни, независимо от прилягането, което не изисква използването на различни режещи инструменти (свредла, райбери и др.).
В допълнение към допустимите отклонения и прилягания за гладки съединения са разработени различни стандарти, които са валидни и за други видове съединения. Например, има редица стандарти за допуски за резбови съединения (GOST 9000-81, GOST 16093-81 и др.), широко използвани стандарти за допустими отклонения на цилиндрични зъбни колела (GOST 9178-81, GOST 1643-81) и др.