Метод за производство на кумулативни заряди
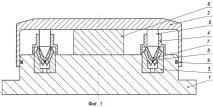
Собственици на патент RU 2389968:
Изобретението се отнася до производството на взривни устройства. Материалът на профилния заряд се вакуумира, материалът на профилния заряд се формира във вакуум и заедно с тялото, материалът на профилния заряд се вакуумира, матрицата се отваря и тялото с профилния заряд се отстранява, облицовката се вкарва във формирания профилиран заряд, поансон с повърхност, свързващата повърхност на облицовката се вкарва вътре в облицовката, възелът е покрит с еластична обвивка, потопен в хидростат, налягането в хидростат се увеличава и се извършва технологично задържане при повишено налягане и температура, налягането в хидростата се намалява до атмосферно, сглобката се отстранява от хидростата и се отстранява еластичната обвивка и поансон. Сформираният зареден материал се евакуира за най-малко 30 s, докато вакуумметърът покаже най-малко 650 mm Hg. Арт., Формовани под преса във вакуум и заедно с тялото формован заряден материал при специфично пресоване от 30 ... 3 до 5 минути. Подобрява качеството на зарядите. 1 з.п. f-ly, 2 ил.
Изобретението се отнася до взривните работи и може да се използва при производството на взривни устройства.
Известен метод за сглобяване на профилен заряд, включващ производството на профилен заряд чрез пресоване и след това свързването му към кутията чрез инсталиране на заряда в кутията (немска заявка № 3742290, публикация 22.06.89).
Този метод на сглобяване обаче има значителни недостатъци, свързани с факта, че когато зарядът е свързан към кутията, възниква празнина между заряда и кутията.празнина, която е практически невъзможна за премахване поради нейната малка площ и наличието на която води до изкривяване на фронта на детонационната вълна (т.е. отклонението му от осесиметричната форма), което води до намаляване на бронепробиваемостта. Освен това, когато зарядът е свързан към кутията, възниква проблемът с осесиметричната инсталация, което значително усложнява технологията на сглобяване.
Има известен метод за оборудване на кумулативна бойна глава, която се състои в отделно производство чрез натискане на самия оформен заряд, инсталиране на подплата и след това свързване на оформения заряд към тялото, като натискате в инструмент за пресата, докато прехвърляте притискащата сила към удара, стойността на която се избира от състоянието на необходимата плътност на оформената заряда (Bulgaria патент № 211438, публикува. 27.06.98).
Недостатъците на метода на сглобяване и пресовия инструмент за този метод на сглобяване са недостатъчното качество на профилния заряд, получен поради твърдото фиксиране на профилния заряд върху тавата на пресовия инструмент, което не позволява да се осигури необходимата плътност на височината на заряда (т.е. да се постигне минимална разлика в плътността), което от своя страна води до намаляване на характеристиките на проникване на бронята. В допълнение, има трудност при осигуряването на осесиметрична инсталация на кутията с такса, свързана с използването на допълнителни устройства. Друг недостатък е ниската технологичност.
Въпреки това, известният метод не позволява да се постигне минимална разлика в плътността (дисперсията) на зарядите и висока плътност на формираните заряди, което се отразява неблагоприятно на неговите свойства. Методът е много опасен и не е подходящ за масово зареждане на кумулятивни заряди в тънкостенни и нискоякостни корпуси.
Предлаганото изобретение решавазадачата за намаляване на дисперсията на плътността на формираните заряди, повишаване на нивото на безопасност, осигуряване на масово производство и възможност за оборудване на профилни заряди в тънкостенни и нискоякостни случаи.
Проблемът се решава чрез метод за производство на кумулативен заряд, включващ поставяне на материала на кумулативния заряд в гилзата, вакуумиране и формоване във вакуум на материала на кумулативен заряд заедно с гилзата под налягане, вакуумиране, отстраняване на гилзата с формирания кумулятен заряд, поставяне на облицовката в сформирания кумулятен заряд, поставяне на щанца с повърхност вътре в обшивката, съединителната повърхност на облицовката, покриване на получения комплект с ластик c обвивка, потапяне в хидростат и пресоване, докато пресоването се извършва в хидростат при специфично налягане на пресоване от 155 до 160 MPa при температура 65 ± 5 ° C, след което налягането в хидростата се намалява до атмосферно, възелът се отстранява от хидростата, еластичната обвивка се отстранява и щанцата се отстранява.
Сформираният заряден материал се евакуира за най-малко 30 s, докато вакуумният манометър покаже най-малко 650 mm Hg, профилираният заряден материал се формова под преса във вакуум и заедно с тялото профилираният заряден материал се формова под специфично налягане на пресоване от 30-90 MPa с време на задържане от 1-2 минути, преди пресоване в хидростат, възлите се държат при температура 65 ± 5 ° C за 20 до 30 минути, а пресоването в хидро състояние води от 3 до 5 минути.
В условията на широкомащабно производство производството на фасонен заряд чрез пресоване в пресов инструмент е възможно само чрез използване на многоместни устройства.
Както е известно, големината на плътността на заряда е право пропорционална на масата на пробата от взривно вещество и обратно пропорционална на обема на формирания заряд. Но масите иобемът на генерирания заряд имат известни разлики в стойностите си. Масата на фасонния заряд зависи от точността на претеглянето и допустимото отклонение на теглото на пробата, а количеството на заряда зависи от точността на изработване на формиращия профил на тялото и съставните елементи на пресовия инструмент. Когато се използва многоместно устройство за производство на фасонен заряд чрез пресоване върху пресово оборудване, силата на натискане се прилага твърдо от траверсата на пресата директно към всички поансони на пресовите инструменти. Поради факта, че масата на пробата и формиращите обеми на пресовите инструменти имат определени разлики в стойностите си, има неравномерно разпределение на общото налягане на пресоване между пресовите инструменти. Тоест зарядите, образувани от материала, изпитват различни специфични налягания на пресоване, което пряко определя градиента в стойностите на плътността.
Известните технически решения не осигуряват необходимата средна плътност на профилни заряди, имат повишена опасност и не са технологично напреднали, което не им позволява да се използват за масово зареждане на профилни заряди в кутии, включително тънкостенни и нискоякостни. Предложеното изобретение решава проблема с намаляването на дисперсията на плътността на формираните заряди, повишаването на нивото на безопасност и осигуряването на масово производство, а също така осигурява възможност за оборудване на профилни заряди в тънкостенни и нискоякостни кутии. Проблемът се решава по следния начин.
При производството на кумулятивни заряди тялото и материалът на кумулативния заряд се поставят в матрица тип касета, т.е. с голям брой малки форми на един плот и малки щанци, свързани към една подвижна притискаща плоча. Формата се затваря с капак с уплътнения и вакуум не епо-малко от 30 s, докато показанието на вакуумметъра стане поне 650 mm Hg. Фасонно шихтният материал се формова под преса във вакуум и заедно с тялото под специфично пресово налягане 30-90 МРа (300-900 kg/cm 2 ) с време на задържане 1-2 минути. Налягането се изравнява с атмосферното, формата се отваря и гилзите с кумулативни заряди се отстраняват.
След това облицовката се вкарва в образувания кумулативен заряд, щанцът с повърхност, съединителната повърхност на облицовката, се вкарва вътре в облицовката, модулът се покрива с еластична обвивка и се потапя в хидростат с работна течност (вода, дестилирана вода и т.н.), нагрята до 65±5°C. Поддържайте хидростата с възлите при температура 65±5°C за 20 до 30 минути. Налягането в хидростата се повишава до специфично налягане на пресоване от 155 до 160 MPa (1550 до 1600 kgf/cm 2 ) и хидростатът се поддържа под налягане в продължение на 3 до 5 минути. Налягането в хидростата се намалява до атмосферно налягане, модулът се отстранява от хидростата и еластичната обвивка и поансонът се отстраняват.
В резултат на това се получава кумулативен заряд със зададена крайна плътност и облицовка, оборудвана в тялото на продукта. При прилагането на този метод налягането при натискане от работната среда се прилага директно към всеки поансон за уплътняване на материала. В същото време налягането от работната среда също се прехвърля към външната обемна компресия на корпуса. Това не води до неравномерно разпределение на пресовото налягане между формираните заряди, осигурява стабилни равни стойности на средните плътности на всички профилирани заряди и дава възможност за оборудване на профилирани заряди в тънкостенни и нискоякостни кутии.
Пример за конкретна реализация
Формирани заряди се изработват в бойни елементи от типа ZKPO или ZKPM с материал за профилирани зарядина базата на HMX или RDX.
За производството се използва матрица съгласно фигура 1, на която 1 е основа, 2 е капак, 3 е вложка, 4 е водач, 5 е поансон, 6 е ограничител, 7 е фасонен заряден материал, 8 е тяло на фасонен заряд, 9 е уплътнение.
Натискане на такси, произведени, както следва. Капак 2 е прикрепен към горното бутало на пресата, в което е монтиран маркуч от вакуумната линия. Мухълът е фиксиран на долната таблица на пресата, центриран с капака 2. Вложките 3 са инсталирани във всеки отвор на основата 1. Уплътнение (уплътняващ пръстен) 9 е инсталирано в канала на основата 1. Всяка част от водата е инсталирана в центъра на основата 1. Тяло е инсталирана във всяка вложка. 5. Включете натискането и спуснете капака 2 върху основата 1 към маркировката, което определя уплътняването на притискащата кухина с помощта на уплътнителния пръстен 9. Вакуумирайте притискащата кухина за поне 30 секунди (в този случай четенето на вакуумния габарит трябва да бъде поне 650 mm Hg). Създайте специфично налягане на пресоване от 30-90 MPa. Изключете вакуумната линия. Издържайте под налягане за 1-2 минути (в този случай спадът на налягането трябва да бъде не повече от 0,3 MPa). Налягането се освобождава и се повдига горното бутало с капака 2. Поансоните 5 се отстраняват от водачите 4. Водачите 4 се отстраняват от корпусите 8. Корпусите 8 с образуваните в тях заряди 7 се изваждат от вложките 3.
Сглобете пресовия инструмент съгласно фигура 2, на която 7 е фасонен заряд, 8 е снабден с тяло, 10 е конус, 11 е облицовка, 12 е черупка.
С памучен тампон илимарля внимателно избършете всеки конус 10. Хидростат (не е показан) се нагрява с пара до температура 65±5°C. Качеството на прилягане на черупките 12 към оборудваната кутия 8 се проверява чрез допир. Поддържайте хидростата с възлите при температура 65±5°C за 20 до 30 минути. Налягането в хидростата се повишава до специфично налягане на пресоване от 155 до 160 MPa. Хидростатът се държи под налягане от 3 до 5 минути, налягането се намалява до атмосферно и хидростатът се разглобява. Сглобките се отстраняват от хидростата. Черупка 12 се отстранява от всяко оборудвано тяло 8, след това конус 10.
В резултат на това дисперсията на средната плътност на кумулативните заряди е намалена 5 пъти в сравнение с прототипа. Поради отсъствието на повишени температури по време на образуването на профилирани заряди и поради използването на хидростат с вода, нивото на безопасност на производството се повишава. Благодарение на използването на матрица с малки форми и щанци се осигурява масово производство.
Прилагането на предложения метод ще позволи да се реши проблемът с намаляването на дисперсията на плътността на профилните заряди, повишаването на нивото на безопасност и осигуряването на масово производство, а също така ще позволи оборудването на профилни заряди в тънкостенни и нискоякостни кутии.
1. Метод за производство на кумулятивни заряди, включващ поставяне на кумулативния заряд в кутията, вакуумиране и формоване на кумулативния заряд във вакуум заедно с кутията под налягане, вакуумиране, отстраняване на кутията с формирания кумулативен заряд, поставяне на облицовката във формирания кумулативен заряд, поставяне на удар с повърхност, съединителна повърхност вътре в обшивкатаоблицовка, покриване на получения възел с еластична обвивка, потапяне в хидростат и пресоване, докато пресоването се извършва в хидростат при специфично налягане на пресоване от 155 до 160 MPa при температура 65 ± 5 ° C, след което налягането в хидростата се намалява до атмосферно налягане, възелът се отстранява от хидростата, еластичната обвивка се отстранява и ударът се отстранява.
2. Метод съгласно претенция 1, характеризиращ се с това, че профилираният заряден материал се вакуумира за най-малко 30 s, докато вакуумметърът покаже най-малко 650 mm Hg, профилираният заряден материал се формова под преса във вакуум и заедно с тялото, профилираният заряден материал е под специфично налягане на пресоване от 30-90 MPa с време на задържане от 1-2 минути, преди пресоване в хидростата, възлите се поддържат при температура 65 ± 5 ° C за от 20 до 30 минути, а пресоването в хидростата се извършва от 3 до 5 минути.