Методи за ремонт на части, MOT и TR на автомобил
Износените части на автомобилните механизми могат да бъдат ремонтирани по следните основни начини:
- обработка под ремонтния размер;
- натрупване на метал чрез заваряване, хромиране и покритие;
- монтаж на пръстени, втулки и маншони;
- пластична деформация (разпределение и кримпване).
Обработка на части за размер на ремонта
Начинът за възстановяване на частите до ремонтния размер е, че една от свързващите части се обработва машинно, за да се възстанови правилната геометрична форма. В този случай номиналният размер на частта неизбежно се променя (увеличава и намалява). В този случай свързващата част трябва да бъде заменена или преработена, за да се запази оригиналната хлабина или смущение. Например, износените цилиндри на двигателя се подлагат на пробиване и шлифоване до по-голям размер (увеличаване на диаметъра), след което за тези цилиндри се избират нови по-големи бутала. Размерът на новите бутала трябва да е достатъчен, за да се получи нормална хлабина между стената на цилиндъра и буталото. За да направите това, има предварително зададени ремонтни размери както за цилиндрите, така и за буталата.
Ремонт на части чрез метален удължител
Този метод се състои в това, че върху износената повърхност се нанася слой метал, след което повърхността се обработва, за да се получи желаният размер, и след това се подлага на термична обработка. Има няколко начина за нанасяне на метал върху износени повърхности.
Заваряване с кислородно-ацетиленов газ. Заваряването се състои в разтопяване на повърхността на детайла и съответния добавъчен материал с пламък на горелка. В този случай разтопеният метал на детайла се комбинира с пълнителя и слояметалът се натрупва на повърхността. Заваръчната ацетилен-кислородна инсталация се състои от цилиндър с кислород под налягане до 150 atm.
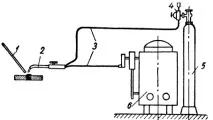
Ориз. Ацетилен-кислородна инсталация: 1 - пълнителен прът; 2 - заваръчна горелка; 3 - маркучи; 4 - редуктор; 5 - кислороден цилиндър; 6 - генератор на ацетилен.
На цилиндъра е монтиран редуктор за намаляване на налягането на кислорода на изхода до 2-3 atm и два манометъра - единият контролира налягането в цилиндъра, а другият на изхода.
За получаване на ацетилен има ацетиленов генератор, в който ацетиленът се получава чрез действието на вода върху калциев карбид.
Ацетиленът и кислородът се подават през маркучи към заваръчната горелка; тук те се запалват, което създава пламък с температура до 3000 °, който разтапя метала.
В допълнение към отлагането на метал с цел възстановяване на размера на детайла, заваряването се използва и за заваряване на различни пукнатини и счупвания в детайлите. Газовото заваряване обикновено се използва за части от чугун и части от цветни метали.
Частите от чугун със сложна конфигурация (цилиндров блок, цилиндрова глава) се нагряват бавно до 650-700 ° преди заваряване и след това бавно се охлаждат, за да се избегне изкривяване и напукване. По-малко сложните части се ремонтират чрез заваряване без нагряване.
Електрическото заваряване се използва по-често за наваряване на износени повърхности на стоманени детайли, както и за заваряване на пукнатини. При ремонта на автомобилни части се използва основно електродъгово заваряване по метода на инж. Славянов. При този метод заваряваната част се свързва към един от полюсите на DC или AC заваръчен генератор с напрежение 30-40 V и ток до 300 A. Другият полюс на заваръчния генератор е свързан към държача на електрода.
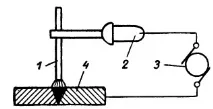
Ориз. Схема на инсталация за електродъгово заваряване: 1 - електрод; 2 - държач на електрод; 3 - заваръчен генератор; 4 - заварена част.
Когато електродът влезе в контакт с детайла и когато електродът впоследствие се отстрани с 2–3 mm, между детайла и електрода възниква електрическа дъга с температура 4000–5000°C, което води до стопяване на метала. Заваряването се извършва с метален електрод с подходящ състав. Съдържанието на въглерод в електрода трябва да бъде близко до това на заваряваната стомана. Електрическото заваряване, както и газовото заваряване, могат да се извършват с нагрети части и студено.
Процесът на заваряване и заваряване включва следните операции:
- почистване на местата за заваряване с метална четка (пукнатините се изрязват с напречен разрез, за да се получи скосяване на ръбовете под ъгъл 45 °);
- заваряване на метал с електрод;
- нормализиране или отгряване на детайла;
- металообработка и механична обработка на заварения слой;
- термична обработка на стомана (по спецификация);
- крайна обработка - шлайфане до номиналния размер.
Хромирането се използва като защитно и декоративно покритие за устойчивост на износване и за възстановяване на износени повърхности на части до номинални размери. Хромирането възстановява бутални щифтове, шарнири, лагерни шийки на разпределителния вал, тласкачи, стебла на клапани и други части. Хромният слой, нанесен върху повърхността, има висока твърдост и устойчивост на износване. Същността на хромирането се основава на законите на електролизата. Ако постоянен ток премине през електролит, съдържащ метален разтвор, тогава чистият метал ще се освободи от електролита и ще се отложи върху отрицателния електрод.
Електролитът по време на хромирането е воден разтвор на хромен анхидрид и химически чиста сярна киселина.киселини. Най-често се използват следните концентрации на разтвори:
- Хромен анхидрид: 150 г. Сярна киселина: 1,5 г. Вода: 1 л.
- Хромен анхидрид: 250 г. Сярна киселина: 2,5 г. Вода: 1 л.
Един от тези разтвори се излива в желязна вана с двойни стени. Пространството между стените се пълни с гореща вода за загряване на банята. Източникът на ток е 6-12-волтови генератори от 250 до 1000 a.
С подходящи токоизправители може да се използва и променлив ток.
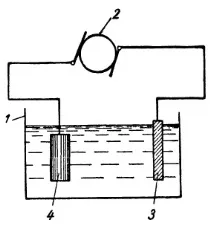
Ориз. Схема на свързване на части за хромиране: 1 — вана; 2 - генератор; 3 - оловна плоча; 4 - детайл.
По време на хромирането минусът на генератора е свързан към частта, суспендирана в разтвора за баня, а плюсът е свързан към неразтворима оловна плоча, също спусната в разтвора. Дебелината на слоя хром, нанесен върху износената повърхност на детайла, обикновено достига 0,5 mm. По-дебел слой хром е по-малко устойчив на износване.
Процесът на хромиране на износената повърхност на детайла включва следните операции:
- шлайфане и полиране на частта, за да й се придаде правилната геометрична форма;
- защита на неподлежащи на хромиране места чрез покриване с целулоид, разтворен в ацетон;
- укрепване на частта в специално устройство за окачване, което осигурява удобно поставяне на частта във ваната;
- обезмасляване на частта в алкален разтвор и измиване в гореща вода;
- потапяне на части в 5% разтвор на сярна киселина за 1-1,5 минути. за отстраняване на оксидни филми от тях;
- хромиране - спускане на частта във ваната и включване в текущата верига;
- измиване на частта в дестилирана вода за събиране на електролит от нея, след това измиване в течаща вода;
- отстраняване на частта от окачването;
- смилане на детайла до необходимия размер.
Метализацията се състои в нанасяне на слой от метал или сплав в разтопено и напръскано състояние върху износената повърхност на детайла. Разграничете газовата и електрическата метализация.
При електрическа метализация металът се разтопява от електрическа дъга, а при газова метализация - от кислородно-ацетиленов пламък.
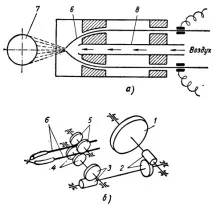
Ориз. електрометализатор; а - схема на метализация; b - схема на захранващото устройство: 1 - въздушна турбина; 2 и 3 - червячни зъбни колела; 4 - водещи ролки за подаване на тел; 5 - притискащи ролки; 6 - тел; 7 - детайл; 8 - канал за подаване на въздух.
Електрически метализатор е устройство, в което е поставен механизъм, който захранва телта; към разклонителната тръба на корпуса е свързан маркуч за подаване на сгъстен въздух от компресора към дюзата на електрическия метализатор. Освен това част от сгъстения въздух се подава през канала към работното колело на захранващото устройство. От работното колело въртенето се предава през две червячни двойки към ролки, които подават два проводника към дюзата.
На разстояние 10-12 mm от дюзата жиците се кръстосват и се разтопяват от електрическа дъга, която се образува от електрически ток, подаден към електрическия метализатор. Разтопеният метал се напръсква с въздушна струя и се нанася върху повърхността на детайла, който се монтира на машината и се върти (ако детайлът е цилиндричен).
Процесът на метализация включва следните операции:
- почистване и обезмасляване на детайла - обикновено се извършва с пясъкоструйка в специална пясъкоструйна машина;
- обработка на детайла, за да му се даде правилната геометрична форма;
- грапавост на повърхността - скъсана резба се нарязва на цилиндрична част (30-40 нишки на 1 инч);
- монтаж на частта върху машината, за да се върти със скорост 80-100 об / мин;
- монтаж на метализатор в опората на машината;
- отлагане на метал върху повърхността на детайла; в същото време опората с метализатора трябва да се движи по частта; дебелината на напръскания метален слой се довежда до номиналния размер на детайла плюс допустимото количество за последваща обработка; разстоянието от дюзата на метализатора до повърхността на детайла трябва да бъде 100-150 mm; при по-голямо или по-малко разстояние твърдостта на напръскания слой намалява;
- обработка на част до номинален размер.
Метализирането може да възстанови износени шийки на вала, легла на лагери, спирачни барабани и др.
Чрез метализиране е възможно също така да се затворят пукнатини (цилиндър блок, глава на блок), които първо трябва да бъдат изрязани с напречен разрез и обезмаслени.
Ремонт на части чрез монтиране на втулки, пръстени и маншони
Чрез монтиране на пръстени и втулки се възстановяват износени валове и оси. Процесът на възстановяване включва следните операции:
- завъртане на износената повърхност на детайла, като се вземе предвид възможността за натискане на втулка или пръстен със стени с дебелина най-малко 2-3 mm;
- производство на нова част (втулка, пръстен), чийто вътрешен диаметър трябва да осигурява пресово прилягане върху подготвена износена повърхност с намеса по 2-ри или 3-ти клас на точност;
- загряване на новата част до светлочервена топлина и притискане върху подготвеното място.
- обработка на повърхността до номиналния размер; Материалът за производство на втулки е стомана и чугун.
- термична обработка, ако е предвидено в техническите спецификации, и крайна механична обработка (шлайфане).
Притискащи втулкиви позволява да възстановите почти всяка износена дупка. Същността на този процес е следната:
- а) износеният отвор се пробива и след това се разширява до размер, който осигурява последващото натискане на втулката;
- 6) нова втулка е изработена от чугун, стомана или бронз и се притиска в подготвения отвор с намеса;
- в) пресованата втулка се разгръща до размера на свързващата част (щифт, щифт, вал, лагер), като се вземе предвид необходимата хлабина.
Възстановяване на части чрез пластична деформация
За възстановяване на частта има два метода на пластична деформация: разширяване и кримпване.
Чрез разпределяне се възстановяват части с форма на втулка и неработеща вътрешна повърхност (бутален щифт), сферични повърхности (кормилни щифтове), шлици, зъбни колела, клапани и др.. Същността на този метод се състои в пластичната деформация на метала под налягане.
Процесът на разширяване на стоманената част е както следва. Детайлът се нагрява до температура на коване 1000-1100°C, монтира се в подходяща матрица и с помощта на специален дорник детайлът се разпределя чрез удари или чрез преса. Тъй като диаметърът на дорника е по-голям от отвора, детайлът се разпределя по посока на износването, което води до увеличаване на външния му размер. След разширяване частта се подлага на предварителна обработка, след това, ако е необходимо, на термична обработка и накрая на окончателна обработка до номиналния размер.
Кримпването възстановява различни бронзови втулки (горната глава на мотовилката, щифт, пружинни щифтове и др.).
Същността на кримпването е следната. Вътре в ръкава, притиснат в частта, е монтиран кръгъл дорник с празнина, която осигуряванамаляване на вътрешния диаметър на втулката с желаната стойност. След това с помощта на гофрове от двете страни се прилага натиск върху краищата на втулката чрез преса. В този случай, поради пластичност, металът се деформира към пролуката, т.е. вътре и това намалява вътрешния диаметър на втулката. След кримпване втулката се разширява до необходимия размер.
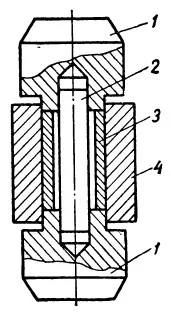
Ориз. Инструмент за кримпване на втулка: 1 — кримпване; 2 - кръгъл дорник; 3 - ръкав; 4 - детайл или матрица.
Ако е необходимо да се кримпва втулка, която не е притисната в детайла, тя се монтира в матрица с подходящ размер и се кримпва.