НП АРПЕТ
UDC 678.01:53; 677,494; 678.674
Керницки В.И., Жир Н.А.
Статията анализира различни варианти за подготовка и преработка на отпадъци от полиетилен терефталат (PET), които позволяват (в зависимост от тяхното качество) да се прилагат най-ефективните технологии за получаване на високотечни материали и продукти на тяхна основа.
През 2016 г. производството на PET за бутилки в света ще достигне 21,5 милиона тона (броят на бутилките е около 550 милиарда броя) [1-2]; производство на полиестер: щапелни влакна 16 милиона тона, нишки 34 милиона тона [3-4]. При цялото съвършенство на съвременните технологии се генерира голямо количество PET отпадъци с различни свойства и степен на замърсяване. Събирането на PET бутилки в света надхвърли 10 милиона тона.Текстилните отпадъци от PET влакна и конци, според най-консервативните оценки, са около 2,5 милиона тона.Класификацията на PET отпадъците и някои процеси за тяхната рационална обработка бяха описани по-рано [4-7]. Като се има предвид постоянното нарастване на абсолютното количество отпадъци от PET, подобряването на съществуващите и появата на нови технологии за преработка, затягането на изискванията за пестене на енергия и органични суровини, както и екологичните проблеми, въпросите за тяхната оптимална преработка изискват най-съвременни решения.
За България тази тема стана още по-актуална с въвеждането на новия Федерален закон № 458-ФЗ, според който производителите и вносителите са длъжни от 2016 г. самостоятелно да осигурят обезвреждането на отпадъчни продукти и техните опаковки или да плащат екологична такса в бюджета на България [8]. За PET контейнери стандартът за екологична такса е 3691 рубли/т. Законът има за цел да ускори въвеждането на разделно събиране на отпадъци, което ще увеличи обема на събираните PET съдове с поне 30-40%. Потреблението на PET опаковки в България е 533 през 2015 гхил. тона, а събираемостта на отпадъците й е 115 хил. т. През следващите 4 години събираемостта ще надхвърли 250 хил. тона PET бутилки годишно. Съществуващите (предимно примитивни) предприятия, които преработват PET отпадъците в груби щапелни влакна и нетъкани материали, не са оптималното решение за използването на тази ценна полимерна суровина.
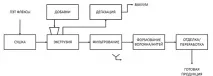
Ориз. 1 Получаване на PET влакна и нишки от отпадъци от бутилки
Схематична диаграма на такива процеси е показана на фиг.1. Има някои характеристики и разлики за влакна и нишки. По този начин, при производството на влакна, някои компании не използват сушене на люспи, тъй като използват многошнекови екструдери, които осигуряват висока междинна повърхност и ефективно обезгазяване, минимизирайки хидролизата на стопилката. При производството на конци е необходимо сушене. Появиха се технологии, които позволяват при производството на щапелни влакна, освен флексове (IV 0,75-0,84), да се влагат до 20% агломерирани влакнести отпадъци (IV 0,6 -0,64). Такава „смес“ (80% flexes + 20% агломерат) с помощта на агломерат, приготвен по технологията на Herbold (Германия), беше (като част от развитието на проекта за полиестерен комплекс Иваново) успешно обработен на щапелна единица от Truetschzler (Германия) във влакно 7 дение с показатели, практически същите като тези за влакна от първични PET гранули. Леко влошаване на индекса на цвета на влакното може да бъде компенсирано чрез въвеждане на оптични избелители, а за нишки - чрез въвеждане на концентрат на полимерно багрило (основна партида). Екструзията (за предпочитане многошнекови или двушнекови екструдери) със зона за дегазиране и последваща филтрация (обикновено двустепенна до 20μ) осигуряват отстраняването на летливи и твърди замърсители и максимална хомогенизация на стопилката. При въвеждане на агломерирани влакнести отпадъциедна от най-важните задачи е дестилацията под вакуум (до 0,001 mbar) на съдържащия се в тях предачен препарат, наличието на който в стопилката прави невъзможно изпридането на влакна. Като добавки могат да се въведат: мастер бач, TiO2, забавители на горенето. Като последното все повече се използват полифосфонати, които не се отделят от полимерната матрица, не са токсични и осигуряват време за изгасване на пламъка в някои полиестерни тъкани под 1 s. [9]. Филтрирането на PET стопилката от чужди примеси позволява да се изолират всички твърди включвания и да се осигури висока (за такъв специфичен полимер) продължителност на работа на спанбонд комплекти. Доста често за тази цел се използва каскада от два филтъра (40 μ и 20 μ) с обратно промиване на филтърните повърхности със стопилката. Системата за обезгазяване трябва да осигурява непрекъсната работа и безопасно отстраняване на уловените летливи компоненти от процеса. Основните параметри, които влияят върху ефективността на обработката на отпадъците съгласно горната схема и стабилността на свойствата (и преди всичко на вискозитета) на полимерната стопилка, подадена за формоване, са: температура, дълбочина на вакуум и подаване на входни люспи, контролирани от вградения вискозиметър на стопилката. Един от лидерите в създаването на такива инсталации с пълен комплект е компанията Gneuβ (Германия). Цялостни инсталацииVarioFil® R+за получаване на полиестерни POY прежди от флекс, разработени от BBEngineering и Oerlicon Barmag (Германия) са с капацитет до 11 т./ден. и правят възможно получаването на нишки с достатъчно високи физични и механични свойства. Нишките се формоват при класически скорости на навиване (2500-3400m/min) чрез страничен удар за 4 позиции на предене (10 нишки на позиция). Независими изследвания във VNIISV (Tver) POYнишките и текстурираните (DTY) нишки, получени от тях от заводаVarioFil® R+показаха, че техните свойства се различават малко от подобни нишки, направени от първичен полимер. Например, нишка DTY от 16,9 tex има натоварване на скъсване от 0,72 kgf, специфично натоварване на скъсване от 42 g/tex, удължение при скъсване от 14,6%, с ниски коефициенти на вариация на тези показатели.
Таблица 1. Препоръчителни характеристики на люспи за производство на хранителни бутилки, нишки и влакна.