Планиране и оптимизиране на запаси със SAP Advanced Safety Stock Planning и SAP SmartOps
Планиране и оптимизиране на запаси със SAP Advanced Safety Stock Planning и SAP SmartOps
Ключова концепция
РешениетоSAP SmartOps Enterprise Inventory Optimization (EIO) предоставя всеобхватен, обхващащ цялото предприятие процес за оптимизиране, управление и контролиране на нивата на попълване на готови стоки и суровини по цялата верига на доставки.
Поддържането на оптимално ниво на запаси във веригата за доставки може да реши съдбата на всяка производствена или логистична компания. Ниво под оптималното ще доведе до недостиг и последваща загуба на продажби, докато ниво, което е твърде високо, изяжда част от рентабилността на компанията. Преди това SAP предлагаше решение за планиране на запасите като част от своите основни решения SAP ERP Central Component (ECC) и Advanced Planning and Optimization (APO). SAP наскоро придоби SmartOps, което му позволява да предлага усъвършенствани възможности за планиране и оптимизиране на запасите в своята система за разширено планиране на запаси (ASSP).
ASSP ви позволява да изчислите размера на резервния запас за всички суровини, междинни продукти и готови продукти в съответните местоположения, като вземете предвид несигурността на търсенето и предлагането, нивото на обслужване и избрания тип ниво на обслужване.
Несигурността на търсенето е резултат от грешки в прогнозирането на нуждите на клиентите (т.е. подценяване или надценяване на нуждите на клиентите). Изчислението на запасите за безопасност взема предвид прогнозата от SAP Demand Planning и колебанията на търсенето въз основа на исторически прогнози и реализирано търсене. За да изчисли точността на своята прогноза, системата използва стойности от два показателя от времеви редове в района на планиране: планираното количество на търсенето и реализиранотоколичество на търсенето (т.е. действителни продажби). Мерките за времеви редове са APO мерки, които се съхраняват в InfoCube.
Несигурността на снабдяването възниква от неуспехи в производството (т.е. надценяване или подценяване на добивите) или колебания във времето за прибиране на реколтата (т.е. действително време за прибиране на реколтата над или под стандарта). Времето за доставка на продукт на дадено място е времето, необходимо за попълване на запасите от предишно местоположение на резервни запаси. Въз основа на две ключови цифри в областта на планиране, планираното време за доставка и реализираното време за доставка (т.е. действителното време за доставка), системата изчислява историческата стойност на ефективността, като взема предвид колебанията във времето за доставка.
Изчисляването на безопасния запас също зависи от изискванията за ниво на обслужване за артикула (т.е. колкото по-високо е нивото на обслужване, толкова повече запаси са необходими, за да се избегнат ситуации на недостиг). При изчисляване на осигурителния запас се взема предвид и избраният тип ниво на обслужване. Има две нива на обслужване, от които можете да избирате: алфа и бета. Алфа нивото на услугата се управлява от събития и се изчислява като броят на напълно доставените времеви прозорци, разделен на общия брой времеви прозорци. Бета нивото на услугата е ориентирано към количеството и се изчислява като изискването за навременна доставка, разделено на общото изискване. Нивото на услугата алфа е много по-строго дефинирано, тъй като частичното изпълнение на това ниво е неприемливо и се счита за неизпълнение на услугата. Следователно, ако е избрано ниво на обслужване алфа, това може да означава по-високи изисквания за предпазен запас.
- Пример за внедряване на APO ASSP
- Казус от практиката за внедряване на оптимизация на инвентара на предприятието (EIO) на SmartOps
- Преглед на ECC Dynamic Inventory Planning
- Прилики и разлики между приложенията за планиране на инвентара на SAP
Пример за внедряване на APO ASSP
Една от водещите компании за потребителски стоки с разнообразни бизнес интереси в секторите на тютюна, пакетираните храни и личната хигиена постоянно се сблъсква с недостиг във веригата си за доставки. В силно конкурентния пазар, на който работи тази компания, всеки недостиг ще доведе до загуба на продажби.
Компанията има огромна верига за доставки със 7 тютюневи фабрики и 12 подизпълнители за производство на пакетирани храни. От всички тези производствени места продуктите се доставят до четири големи склада (наречени основни възли), разделени в четири региона на страната. Тези огромни складове на свой ред разпределят материали до 35 склада, от които материалите се придвижват до 1200 дистрибутора.
Забележка. Терминът „възел-майка“ се използва в тази компания за означаване на много големи складове, които получават материали от фабриките и служат като разпределителни центрове. В случая има четири такива склада по райони на страната: север, юг, изток и запад.
Тази компания внедри APO ASSP, за да поддържа оптимално ниво на запаси от готови стоки на ниво дистрибутор (т.е. 1200 дистрибуторски центъра).
Трудности при внедряването на ASSP
По време на изпълнението компанията се натъкна на редица трудности. Въпреки че някои от тези трудности бяха свързани с внедряването на нови бизнес процеси, някои от тях бяха чисто технически. Разгледайте примери за такива технически трудности.
Техническа трудност: APO ASSP предполага, че количеството на склад винаги се отнася за предишната поръчка и може да бъде доставено по-късно (т.е. не възниква загуба на продажби). Този подход проработи в тютюневата индустрия, тъй като компанията работи почти изключително на този пазар. Дистрибуторите попълниха следващото количество за поръчка с допълнително недостигащо количество от последната поръчка (ако има такова). Това обаче не е напълно вярно за пакетираните храни и бързооборотните стоки, където всеки недостиг може да означава загуба на продажби за компанията, тъй като в този случай клиентът купува продукти на конкуренти. Поради тази причина компанията въведе ръчно управление. В противен случай тази опция се нарича лента за безопасност.
Техническа трудност: Друга трудност беше получаването на данни за несигурността на доставките. Стандартните срокове за изпълнение за всеки доставчик бяха поддържани в системата ECC. Действителното време за доставка обаче (т.е. разликата между датата, на която поръчката за покупка или графикът за доставка е изпратен на продавача и датата, на която стоките са получени от продавача) никога не е била записана в системата.
За някои артикули тези данни се поддържат в отделен файл на Excel от отделен купувач, който обработва конкретния артикул. Колебанията в предлагането бяха изчислени от данните в този Excel файл. За други елементи, за които не са налични данни, е направено разумно предположение (например колебания в предлагането от 40% до 50%). По време на внедряването компанията въведе система за записване на действителните данни за колебанията в доставките за бъдеща употреба. Данните за колебанията в предлагането често не са налични в много компании.
Техническа трудност: Основната работа по планиране на запасите за безопасност изискваше многовреме на изпълнение, тъй като включваше голям брой комбинации от местоположения на продукти (повече от 10 000 продукта и около 1500 местоположения). Компанията трябваше да направи много итерации с идентификатори за избор, за да намери оптималното време за изпълнение.
Концепцията за предпазна лента
Планирането на безопасен запас направи възможно получаването на най-добрите препоръки за повечето продукти, но една от трудностите за компанията беше, че за определени продукти безопасният запас се оказа твърде голям или недостатъчен. Тъй като компанията работи от много години, тези цифри понякога изглеждаха абсурдни за ръководството. това се случи поради редица причини: ниската точност на прогнозата за тези продукти и липсата на достатъчно количество исторически данни. Ето защо компанията първоначално въведе концепцията за предпазна лента.
Забележка: В този пример изборът на стойностите на обхвата беше извършен ръчно (например компания избра шест дни като горна граница на обхвата за тютюн с големи продавачи). За да се изчислят стойностите на безопасните запаси в компанията, беше използван стандартен макро-контролиран цикъл на безопасен запас на APO.
Категория | Бета ниво на услугата | Долна граница на предпазния запас (в дни) | По-висок диапазон на предпазен запас (в дни) |
Тютюн (продавачи на големи количества) | 99.9 | 2 | 6 |
Тютюн (продавачи в малък обем) | 99.9 | 6 | 10 |
Пакетирана храна | 95 | 2 | 6 |
Готови за консумация хранителни продукти | 95 | 6 | 10 |
Продукти за лична хигиена | 99 | 2 | 6 |
Нива на обслужване за различни продукти
Компанията също така е въвела процес за редовен преглед на тези стойности на обхвата и коригиране, ако е необходимо. Въвеждането на групата за безопасен запас беше иновативен подход, тъй като включваше смесица от наука с математически изчисления на оптималното ниво на безопасен запас и валидиране на тези данни според опита на планиращия, ако стойностите, генерирани от системата, се окажат нелогични поради неточни данни.
Стъпки за задаване на основни данни и конфигурация
Внедряването на APO ASSP за този проект изисква завършването на основните стъпки за настройка на данните и системната конфигурация. Повечето от данните бяха стандартни за APO и няколко персонализирани макроса бяха използвани за записване на правилата за лентите на запасите за безопасност. Нека започнем с настройка на основните данни.
Настройките на основните данни, поддържани в APO ASSP за този проект, са показани нафиг. 1. За достъп до този екран стартирайте основната транзакция на продукта /SAPAPO/MAT1 и изберете APO> Основни данни> Продукт> Размер на партида от менюто (APO> Основни данни> Продукт> Размер на партида). Посочен е метод на предпазен запас (метод поле $$tk) BT. BT означава бета ниво на услугата и метод на цикъл на поръчка за покупка. Както бе споменато по-горе, бета нивото на услугата предполага количествена ориентация. Използван е методът на цикъла на поръчката за покупка, тъй като попълването на запасите в дистрибуторските центрове от складовете на компанията се извършва на базата на цикъл на поръчка. В полето ниво на обслужване (%) сте запазили стойността на нивото на обслужване, необходимо за комбинацията от продукт и местоположение. В товаВ случай на пакетирана храна се определя ниво на обслужване от 95.0.
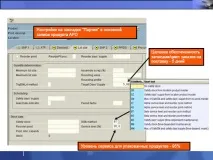
Основни данни след поддръжка в основния запис на продукта на APO за ASSP
Периодът на цикъла на поръчката се въвежда в полето „Доставка за целеви дни“ в раздела „Размер на партидата“ в главния запис на продукта. Цикълът на поръчката описва обичайния брой периоди между две изпълнения на планиране на поръчка. Тук стойността е 5,00 (т.е. продължителността на цикъла на поръчката е пет дни).