Разработване на технологичния процес на монтаж и заваряване
Заваряването като прогресивен технологичен процес за получаване на неразглобяеми съединения на части, което позволява да се създават конструкции с високи експлоатационни характеристики. Характеристики на развитието на процеса на сглобяване и неговата обосновка.
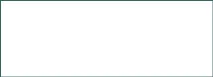
Изпратете добрата си работа в базата знания е лесно. Използвайте формата по-долу
Студенти, докторанти, млади учени, които използват базата от знания в обучението и работата си, ще ви бъдат много благодарни.
Хоствано на http://www.allbest.ru/
Заваряването е прогресивен технологичен процес за получаване на неразглобяеми съединения на части, което прави възможно създаването на конструкции с високи експлоатационни характеристики. Предимствата на заваръчните съединения допринасят за широкото им използване в конструкции за различни цели. Използването на заваряване спестява материали и време при производството на конструкции. Това открива големи възможности за механизация и автоматизация, производителност и подобрява условията на труд на работниците. С развитието на научно-техническия прогрес се разширява възможността за заваряване на части от различни дебелини на материалите и във връзка с това наборът от използвани видове и методи за заваряване. В момента се заваряват детайли с дебелина от няколко милиметра до десетки сантиметри и дори метри.
Наред с конструкционните въглеродни и нисколегирани стомани все повече се налага заваряването на специални стомани, леки сплави и сплави на основата на метан, молибден, цирконий и други метали, както и разнородни метали. От прогресивността на прилаганите заваръчни процеси и качеството и надеждността на готовите конструкции, и ефективността на производството като цяло. Една от най-развиващите се области в заваръчното производство е широкото използване на механизирани иавтоматично дъгово заваряване. Тези проблеми се решават чрез механизация и автоматизация, както на самите процеси на заваряване, така и чрез комплексна механизация и автоматизация, обхващаща всички видове работи, свързани с производството на заварени конструкции и създаването на странични и автоматични производствени линии. В този случай голямо значение се отдава на създаването на специално заваръчно оборудване и средства за оборудване на технологични процеси. В условията на непрекъснато усложняване на конструкциите, постоянно увеличаване на обема на заваръчните работи, правилното провеждане на технологичната подготовка на производството играе важна роля, което до голяма степен определя неговата трудоемкост и време за разработка, икономически показатели и използване на средства за механизация и автоматизация. Най-големият ефект от технологичната подготовка се постига с цялостно решаване на проблемите - технологичното развитие на самите конструкции и развитието на технологичните процеси и тяхното оборудване на всички етапи на производството.
1.1 Предназначение, условия на работа и описание на устройството, дизайн на продукта
Сепараторът има формата на цилиндър с разширение в горната част. Горещият въздух, който също е флуидизиращ агент, се подава в слоя през затворена разпределителна решетка.
Веществото за окисляване се подава през дюзи директно в слоя. Топлината на реакцията се отнема от U-образни хоризонтални топлообменни елементи, разположени в слоя. Хладилният агент е вряща вода.
В горната част на устройството вертикално са монтирани патронни филтърни елементи от стъклопакет, които почистват контактните газове от праха на сепаратора.
От описанието на дизайна може да се види, че апаратът с кипящ слой е много по-прост от апарата с неподвижен слой катализатор за подобен процес, но добивът и качеството на продукта сав стационарен слой е по-висок, отколкото в флуидизиран.
1.2 Спецификации за материали, монтаж и заваряване, GOSTs
Спецификацията е технически документ, който се разработва по искане на клиента или по решение на разработчика на продукта.
Спецификациите са неразделна част от комплект проектна или техническа документация за продуктите и при липса на документация те трябва да съдържат пълен набор от изисквания към продуктите, тяхното производство, контрол и приемане. Изискванията на установените технически условия не трябва да противоречат на задължителните изисквания на GOST.
Въглеродна стомана с обикновено качество се доставя в съответствие с GOST 380-94 и се използва при производството на черупки, дъна, фланци, люкове, разклонителни тръби и други части на апарати, работещи в температурен диапазон от - 20 до + 425 и налягане до 5 MPa.
Механични свойства на стоманата:
Клас стомана VSt3sp5
Химични свойства на стомана VSt3sp5
VSt3sp5GOST 380-94
Въглерод - 0,14 - 0,22;
Манган - 0,40 - 0,65;
Силиций - 0,12 - 0,80;
Сяра не повече от 0,050;
Фосфор не повече от 0,040;
2. Технологична част
2.1 Схема на монтаж и заваряване
2.2 Разработване на процеса на монтаж и монтаж и неговата обосновка
2.2.1 функции за сглобяване и заваряване
След подготовката частите на заварените конструкции се изпращат за монтаж. Монтажът е процес на последователно свързване на части един към друг по начина, предписан от технологичния процес и чертежите за последователно заваряване.
Основната цел на процеса на сглобяване е да се определи най-изгодната последователност на сглобяване на отделни части, която да гарантира изпълнението на технологичните изисквания за производство.на този продукт с минимална работна сила, време, спомагателни материали. Преди монтаж монтажникът визуално проверява съответствието на частите с изискванията на чертежа и технологичния процес. Свързващите се повърхности и съседните зони на сглобените части с ширина най-малко 20 mm трябва да бъдат добре почистени от ръжда, масло, мръсотия, котлен камък и влага, за да се избегне появата на пори и други дефекти в заваръчния метал.
При сглобяване на заварени конструкции се осигурява такова взаимно разположение на сглобяваните части на сглобката, в която те трябва да бъдат разположени в готовата сглобка. Редът на сглобяване, установен от технолога-заварчик, е посочен в технологичните схеми. Пропуските по време на монтажа трябва стриктно да отговарят на чертежа. Повдигането на ръба на един от елементите на челната връзка над другия, ако не е предвидено и не е специално посочено в чертежа, е разрешено по цялата дължина на шева не повече от 0,2 от дебелината на елемента и 0,15 от дебелината на елемента. Местните излишни ръбове се определят от най-малката дебелина на заварените части. Излишъкът на ръбовете се контролира преди заваряването.
При сглобяване на заварени конструкции частите се свързват помежду си с прихващания, които се поставят на местата на бъдещите заварки. Захващанията се извършват покрити, в защитните са потопени. Площта на напречното сечение на хълмовете не трябва да надвишава 2/3 от площта на напречното сечение на бъдещия шев и да бъде не повече от 25 - 30 mm 2. Дължината на всяка халс трябва да бъде равна на 4 - 5 дебелини на свързване на частите, но не по-малко от 30 mm и не повече от 100 mm. Колкото по-малка е дебелината на заварените части, толкова по-малко е разстоянието между халките. В решетъчните конструкции всеки елемент се захваща от двете страни с шевове с дължина 30–40 mm, с крак не повече от 5 mm.
2.2.2 Избор на вид ток и полярност
Влияние на вида на тока и полярността върху формата на шевапоради различното количество топлина, отделена на катода и анода. При заваряване под флюс на анода се отделя по-малко топлина, а при постоянен ток с права полярност дълбочината на проникване е приблизително 40-50% по-малка, отколкото при заваряване с обратна полярност и 15-20% по-малко, отколкото при заваряване с променлив ток. В тази връзка при заваряване с директна полярност коефициентът на отлагане и височината на изпъкналостта на заваръчния шев са по-големи, отколкото при заваряване с обратна полярност.
2.2.3 Избор на метод на заваряване
Ръчно дъгово заваряване - топлината, необходима за топене на основния метал и електродния прът, се образува в резултат на изгаряне на електрическа дъга с висока температура до 4000 - 6000 ° C. Разтопеният основен и електроден метал се смесват в заваръчната вана и се втвърдяват бързо с напредването на дъгата, образувайки заваръчен шев. Електродното покритие, нанесено върху металния прът на електрода, се състои от различни компоненти, които при стопяване създават защита от шлака и газ на заваръчната вана от вредното въздействие на кислорода и азота във въздуха.
Автоматично заваряване под флюс - в този случай електрическата дъга гори под слой гранулиран флюс, който предпазва разтопения метал от въздух и, ако е необходимо, го легира. Електродната тел се подава в дъгата автоматично с помощта на заваръчна глава, оборудвана с електродвигател. Потокът попада в зоната на заваряване под действието на собствената си маса. В същото време цялата инсталация се движи по протежение на заваръчния шев. С този метод на заваряване се осигурява висока производителност и добро качество на шева.
2.2.4 Избор на марка електроди, заваръчна тел, флюс
Студено изтеглена твърда стоманена заваръчна тел се произвежда в съответствие с GOST 2246-70, който предвижда 77 класаразличен химичен състав.