Сондиране - Статии
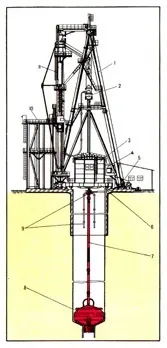
Сондирането в съвременния смисъл е предложено от Хонигман (Холандия) през 1894 г. - при нормални (за изграждане на шахти с малък диаметър) условия. В сондажните платформи се използват ротационни и планетарни задвижващи механизми (задвижвания, съответно на повърхността и в дъното на отвора). От 60-те години. в СССР се използват инсталации с планетарно-турбинни тела за рязане на скали (виж реактивно-турбинно сондиране); около 550 минни шахти и кладенци с голям диаметър (от 1 до 6,5 m) с обща дължина около 150 хиляди m (края на 70-те години) са пробити в СССР.
Технологичните процеси на проникване на сондажи включват разрушаване на скалната маса, отстраняване на скалата от лицето и закрепване на шахтата. По време на сондирането шахтата се пълни с вода или сондажна течност, която създава хидростатично налягане върху стените на изработката и по този начин изпълнява функциите на временна облицовка. В този случай течността в циркулационната система през сондажните тръби и пръстена на сондажния отвор също се използва за хидротранспортиране на разрушената скала (пулпа) на повърхността. При схема с директна циркулация течността се подава по тръбите от кални помпи и суспензиятасе издига нагоре по багажника; в обратния случай течността се движи по протежение на сондажа, а пулпата се издига през тръбите с помощта на въздушен лифт. На повърхността пулпата се почиства от скала в утаителни резервоари или в сито-хидроциклони. За укрепване на насипни и водопоглъщащи скали се използват тиксотропни глинести разтвори като сондажна течност, чиято твърда фаза запълва порите, държи скалните частици заедно и образува глинена торта - мембрана по стените на ствола. Сондиране в стабилни формации с малък приток на вода е възможно без сондажна течност. В същото време скалните частици се отстраняват чрез пневматичен транспорт - през сондажни тръби с въздушно налягане в пръстена или чрез изсмукване на пневматичната смес от тръбите.
За да се ограничи мощността и товароносимостта на сондажните платформи и въртящият момент, предаван от сондажните тръби, при пробиване на шахти с голям диаметър (в СССР до 8,75 m грубо) се извършва фазово пробиване - разширяване на работата до необходимия диаметър в няколко прохода до пълна дълбочина. Подпората се издига основно след завършване на проникването на шахтата на пълна дълбочина. В същото време сондажната течност остава в изработката, а опората се монтира на повърхността и се спуска в отвора.
Със схемата на секционен монтаж на облицовката (най-често срещана в СССР), нейните отделни секции (предимно стоманени черупки, заварени от къси връзки) се спускат последователно и се съединяват във вала отдолу нагоре. При монтиране на опората на вода се прави херметично дъно в долната връзка; следващите връзки са херметически изградени на повърхността към предишните (главно чрез електрическо заваряване); полученото "стъкло" постепенно се потапя в сондажната течност под действието на собственото си тегло чрез добавяне на баластна течност (вода) вътре в нея. Креп,изграден на повърхността, е по-прав във височината на сондажа и е запечатан, но изисква повишено качество на заваръчните работи и спазване на праволинейността на сондажа по време на сондиране.
След издигането на металната облицовка до пълна дълбочина, фиксираното пространство се запушва и течността се отстранява от сондажа. Производителността на сондиране с RTB платформи (диаметър 3,2 m) в скали със средна якост (f = 5-6) е около 1,3 m 3 / h, консумацията на енергия е около 3000 MJ / m 3, проникването на комплект фрези е около 3 м. задвижването на комплект фрези е около 5,7 m; максималният диаметър на пробиване с платформата UZTM-8.75 (фиг.) е 8,75 m (на дълбочина 800 m), с платформата Z-40 от Wirt (Германия) - 8 m (на дълбочина 1000 m). Обхватът на проникването на сондажите се увеличава.