Защо е необходима автоматизация - Склад и оборудване
На фона на икономическия растеж в България през последните години все повече компании започват да се замислят за автоматизиране на своите производствени и складови процеси, а причината за това е непрекъснато нарастващият оборот, с който съществуващите схеми на предприятията, създадени преди няколко години и използващи предимно ръчен труд, не могат да се справят. Огромен поток от информация пада върху служителите, необходимо е да се запази много в паметта. В резултат на това броят на грешките се увеличава и работата изисква постоянно внимание.
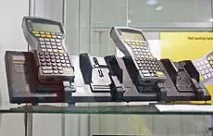
Процесът на автоматизиране на системите за управление на предприятието трябва преди всичко да помогне за намаляване на психологическото натоварване на човек, тъй като малцина са в състояние да поддържат повишено внимание към операциите през цялото време на работния ден. Следователно задачите, които изискват постоянна концентрация на внимание, обикновено се прехвърлят в компютърните технологии възможно най-много. Компютрите, работещи в рамките на набор от специфични схеми, вършат отлична работа с тях и човешка намеса или вземане на решение е необходима само в случаите, когато ситуацията стане необичайна или е необходим ръчен избор на една от стандартните схеми.
Пример е склад, в който се съхранява голям асортимент касети за принтери, опаковани в почти еднакви кутии, различаващи се само по артикулен номер от 4,6 знака и етикет срещу един от цветовете на опаковката. При ръчен избор служителят на склада трябва да вземе предвид всички тези параметри и правилно да избере правилното количество стоки. Излишно е да казвам, че до края на работната смяна преоценката беше фантастична. Терминалът лесно се справя с решението на такъв проблем, който чете баркода на продукта, сравнява го с кода на продукта в задачатаи или потвърждава правилността на избора, или дава сигнал за несъответствие. Човешка намеса е необходима само когато стоката не е налична в необходимото количество и се свежда само до посочване на реално изпратеното количество. След като наскоро прекарах около пет минути в търсене на необходимия патрон пред витрина, където стоките бяха ясно поставени по някаква схема, известна само на служителите в магазина, аз искрено съчувствах на собствениците на склада, които са принудени да вършат този вид работа всеки ден по осем часа.
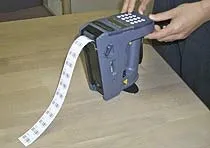
Почти всички подобни задачи могат да бъдат прехвърлени към софтуера, но за това е необходимо да се осигури бързо въвеждане на информация на "езика" на компютъра. Това може да се постигне само ако всеки продукт има някакъв вид идентификатор за автоматизирани системи. В момента най-разпространеният идентификатор е баркод, отпечатан върху етикети или директно върху опаковката на продукта. Печатът върху опаковката е по-евтин метод, но има редица ограничения. Например, не е възможно да се отпечата информация върху полиетиленово фолио, което обикновено се увива около палети. Също така е невъзможно да се прочете кодът на опаковката чрез този филм, следователно в момента най-достъпният начин за маркиране на палети е да се залепят хартиени етикети върху тях. Най-икономичните технологии за масово отпечатване на информация върху етикети в момента са методите за термичен и термотрансферен печат.
Изборът на устройство за отпечатване на такива етикети е доста прост, тъй като всички принтери са разделени на класове, всеки от които има препоръчително дневно натоварване. Имената на тези класове (десктоп, търговски, индустриален) често са подвеждащи и тогава купуваме по-скъпо оборудване, но сизлишни функции. Ако трябва да пуснете „настолен“ принтер в производство, трябва да положите известно усилие върху себе си, за да преодолеете условностите на терминологията. Тази ситуация е доста често срещана, особено ако има много точки за маркиране с ниско натоварване на печата на маркировка. Функционално, тоест по отношение на възможностите за печат, всички принтери са еднакви. Те се различават по способността на моторната част да издържа на определено ежедневно натоварване, както и допълнителни опции.
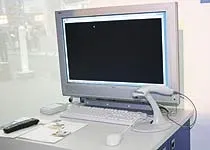
Настолните принтери са проектирани да отпечатват 70,90 m етикети на ден, търговските принтери - за 400 500 m на ден, лекопромишлените принтери - до 1,5 km, а индустриалните принтери са предназначени за денонощно производство.
Световните лидери в производството на термични и термотрансферни принтери са компании като Datamax, Intermec, Sato и Zebra. Цените за принтери от всеки клас са почти еднакви за тези компании, разликите са само в определени опции, които могат да бъдат полезни за решаване на конкретни проблеми. Струва си да се обърне внимание и на факта, че това, че търговският принтер има "индустриален метален корпус", не го прави индустриален принтер, тъй като това е само опция за корпуса, а моторната част остава в своя клас и може да издържи само определено ежедневно натоварване.
За входящо етикетиране в складове термотрансферните принтери са най-подходящ вариант. Ако стоките пристигнат в склада от производството, тогава е най-рационално да използвате автоматични апликатори за етикети с функция за печат. Такива устройства са лесни за поставяне на мястото на последния етап от производството и почти напълно премахват ръчния труд за залепване на етикети, намалявайкинамаляване на броя на грешките при етикетиране до минимум. Печатащият модул в апликаторите е индустриален термотрансферен принтер, управляван чрез информационната система на предприятието по същия начин като конвенционален принтер. Задача на персонала е единствено навременната подмяна на консумативите, необходимостта от допълване на които се сигнализира от апликатори със светлинна индикация директно на място или чрез компютърната мрежа на фирмата.
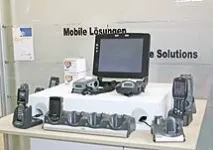
Правилното и точно етикетиране е доста важна част от всяка информационна система. Ако маркировката е нанесена неправилно при пристигане в склада, тогава грешката най-вероятно ще бъде открита само от клиента и това ще доведе до допълнителни разходи за връщане на стоките, повторна доставка и ще навреди на имиджа на компанията като надежден доставчик. При правилно входящо етикетиране на входящата стока с етикети чрез стационарни принтери се спестява частично ръчен труд, тъй като дори и приемането да се извършва с предварително отпечатани етикети, има възможност при голям брой различни стоки те да бъдат залепени върху друг продукт. Мобилните принтери ще помогнат за намаляване на броя на грешките в тази област. Използвайки ги, можете да отпечатате етикета директно до продукта, като по този начин увеличавате вероятността етикетът да бъде залепен върху продукта, за който е отпечатан. Времето, изразходвано за маркиране, също е намалено поради факта, че приемникът не трябва да се движи между инсталирания някъде принтер и стоките. Недостатъците на тези принтери включват ниска производителност, така че най-често те се използват за отпечатване само на вътрешноскладови маркировки, въпреки че такива маркировки са подходящи само за склад, не е възможно да се използват допълнително при клиент.
Веднага щом всичкипродуктите са маркирани, става възможно да се прехвърли задачата за разграничаване на стоки към програма, която осигурява четене на баркодове. Най-простите и следователно по-евтини устройства за четене са скенерите за баркод. Задачата на тези структурно прости устройства е само да сканират кода, да го декодират и да го прехвърлят на компютър. Основният недостатък на скенерите се крие в последната функция, тъй като те могат да бъдат премахнати от компютъра само с дължината на кабела. Освен това, ако човек се отдалечи от компютъра на дванадесет метра, той вече не може да проследи реакцията на софтуера към получените кодове. Например, ако продукт с такъв баркод не е в базата данни, на екрана се появява прозорец, който ви подканва да създадете карта за нов продукт, и съхраняващият склад, без да вижда това, продължава да сканира останалия продукт, като губи всички последващи данни.
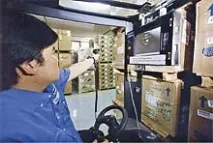
Въпреки това, ако проблемът с премахването на ограниченията за отдалечеността на четеца от компютъра може да бъде решен с помощта на радио скенери, тогава проблемът с липсата на обратна връзка между компютъра и скенера не може да бъде решен. Дори ако скенерът има дисплей, към него може да се предаде много малко информация и има много нестандартни ситуации по време на приемане. Попаднах на успешно работещо решение с използване на радиоскенери само в един склад, където двама души работеха по двойки с уоки-токита: един работник с радиоскенер получаваше входящите стоки, а вторият беше на компютъра и постоянно комуникираше чрез глас с първия служител, който действително видя стоките.
По-скъпите, но и по-функционални устройства - терминали - успешно се справят с такива задачи. Терминалът е мобилен компютър, оборудван със сканиращо устройство. На този мобилен компютър, служителсклад и взема решения за всички нестандартни ситуации. В зависимост от сложността на системата за складова отчетност, задачите могат да се прехвърлят към терминала чрез комуникационно устройство непосредствено до компютъра. Това е най-евтиното и лесно решение, но има редица ограничения, като основното е една складова операция на служител. Всъщност се получава следната ситуация: задачата за събиране на стоки в склада е дадена на един служител, който отива да ги събира в целия склад. Разбира се, тази задача може да бъде разделена поравно между двама, трима или повече служители, но резултатът от нея ще бъде известен само когато всички те, завършили обработката на своите части от задачата, прехвърлят резултатите на компютъра.
Използването на радиотерминали ще помогне за по-гъвкаво решаване на този проблем, когато служителят не трябва да ходи до компютър, за да получи задача (полупартида). Такава схема се показа добре в складове, разделени на зони, всяка от които има свой собствен пикап. Задачите са разделени на зони за съхранение на стоки, като на всеки служител се казва само тази част от тях, която се отнася пряко към неговата зона.
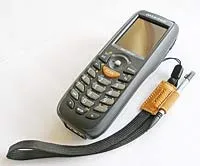
И двете схеми имат общ недостатък - резултатът от всяка складова операция става известен на складовата система едва след нейното приключване. Малките и средни складове най-често се задоволяват с този принцип на организация на работа, докато големите складове изискват по-модерно решение - WMS (Warehouse Management System). Терминалите, работещи с WMS, са в постоянен on-line контакт със системата, като системата сама решава разпределението на задачите между складовите служители в зависимост от ролята, която изпълняват в момента. Така например системата “вижда”, че до точка 1, от която трябва да се вземе стоката за изпращане до клиента,има товарач, който получава задачата да премести този товар до точка 2 - мястото на получаване на поръчката. Веднага след като товарачът отчете завършване на операцията, системата може да му даде като свободен и най-близо до необходимата точка задачата за вътрешно придвижване от комисионния склад до комисионната зона. По този начин всички складови задачи се разделят на операции, изпълнявани от най-„подходящите“ служители в момента, намалявайки броя на техните празни движения из склада почти наполовина.
Този режим на работа диктува определени изисквания към хардуера на терминалите, в частност към оборудването и организацията на радиомрежата. За разлика от полупакетната схема, когато терминалът, след като получи задачата, може да бъде извън радиокомуникационната зона и да се върне в нея само за предаване на резултата, в тази схема се изисква комуникация за терминала във всеки момент от време. Повечето производители на складови терминали ги разделят на три класа – малки, средни и високи. В почти всички класове има модели с функция за работа на радиоканал. Различават се по степен на защита, мощност на процесора и размер на дисплея. Един от най-важните параметри е устойчивостта на удар, тъй като условията на работа в склада и производството са много по-тежки, отколкото в търговската зала на магазина.

За малки и средни складове са подходящи терминали от малък и среден клас, за големи складове - терминали не по-ниски от средния клас. Колкото по-модерен е моделът на терминала, толкова по-надеждни компоненти се използват в производството му. Това се отразява на цената на устройството, но при интензивна употреба първоначалната инвестиция бързо се изплаща. Илюстрация е склад от клас А, където се използват едновременно малки и висок клас терминали. Отзадгодина на работа от същите служители, терминалите от малък клас се провалиха поради механични повреди два пъти по-често, въпреки факта, че имаше четири пъти по-малко от терминалите от висок клас. Освен това ремонтът на терминали от висок клас, парадоксално, беше по-евтин поради факта, че контактният им панел е разположен отделно от дисплея (100 евро), а на терминали от малък клас беше инсталиран сензорен монитор (тъчскрийн) за 400 евро.
Друг начин за въвеждане на информация в системата е инсталирането на автоматични скенери на мотокари, които независимо разчитат етикета от стоката в момента, в който мотокарът вземе палета. Този метод обаче включва повишени изисквания към мястото на маркиране върху палетите и към размерите на контейнерите със стоки в склада. Подходящ е за склад, който обработва само палети, излезли от производство, където те са маркирани с автоматични апликатори, т.е размерите на палетите са еднакви и мястото на маркиране е винаги едно и също.
Колкото по-точно са формулирани изискванията към системата, колкото по-подробно са описани процесите в предприятието, толкова по-оптимално ще бъде решението, предлагано на клиента. Цялото оборудване за автоматична идентификация е като набор от различни "тухли", като ги комбинирате правилно, можете да изградите комплекс, който напълно отговаря на нуждите на конкретен клиент, осигурявайки максимална гъвкавост на предлаганите решения.