14.2. Прикрепване на кристали към калъфа
Сглобяването на полупроводникови устройства и интегрални схеми е най-трудоемкият и отговорен технологичен етап от цялостния цикъл на тяхното производство. Процесът на сглобяване включва три основни технологични операции: закрепване на кристал към основата на корпуса; свързване на тоководещи изводи към активни и пасивни елементи на полупроводниковия кристал към вътрешните елементи на корпуса; запечатване на кристала от външната среда.
Запояване, заваряване и залепване са основните методи за извършване на монтажни операции: монтаж на чипове и платки, свързване на проводници, запечатване на пакети.
14.2.1. Прикрепване на кристала към основата на кутията
Запояването е процесът на свързване на две различни части, без да се разтопяват, като се използва трети компонент, наречен спойка. Разтопеният припой намокря повърхностите на съединяваните детайли, запълвайки цялата междина между тях, след което в намокрените места протичат процесите на междуатомно взаимодействие между припоя и всеки от двата намокрени от него материала. След охлаждане спойката става твърда и се образува здрава спойка.
Има нискотемпературно запояване (до 450 °C) и високотемпературно запояване (над 450 °C). Меките или нискотемпературни припои включват сплави от калай с олово 40% Sn + 6O% Pb; 61% Sn + 38,2% Pb + 0,8% Sb), калай с бисмут и др., Както и евтектични сплави Au + Si (94 и 6%) (T топене = 370 ° C) и Au + Ge (88 и 12%) (T топене = 356 °C). Твърдите или високотемпературни спояващи сплави включват сплави на сребърна основа 45% Ag + 30% Cu + 25% Zn; 72% Ag + 28% Cu) и др.
Припоите за запояване се използват под формата на таблетки, подложки за покритие върху частите, които трябва да се съединят, или локални зони.
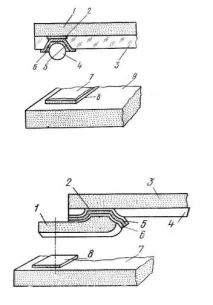
Интензификацията на запояването се осигурява от потоци, редуциращи среди,натиск върху частите за запояване, колебания на индустриалната честота, струя горещ газ.
Режим на запояване: максимална температура, скорост на нагряване, време на задържане при максимална температура, натиск върху частите за съединяване, скорост на охлаждане на частите.
Свързването на части се извършва от край до край, припокриване, както и комбинирани начини.
Предимствата на запояването са простотата на процеса, липсата на топене и относително ниско нагряване на частите, които трябва да се съединят, възможността за свързване на части със сложна конфигурация.
Процесът на запояване беше допълнително разработен по време на сглобяването на интегрални схеми, използвайки технологията "flip-chip". Тази технология включва предварително създаване на "топкови изводи" или "контактни издатини" (фиг. 14.4) от мед, покрити с припой или калай. Кристалът се обръща и равнинната му страна през туберкулите влиза в контакт с повърхността на основата на кутията.
1 кристал; 2 контактна площадка; 3 стъкло; 4 медна топка; 5 медна подложка; 6 спойка (висока температура); 7 спойка (ниска температура); 8 олово от AgPb сплав; 9 субстрат.
1 златен лъч; 2 силицидни плочи; 3 кристала; 4 силициев нитрид; 5платина; 6 титан; 7 субстрат; 8 златна подложка
Ориз. 14 . 4 Схема на свързване (сглобяване) на кристала и подложката чрез запояване
a - с изводи на лъча, b - със сачмени изводи
Метод на директен контакт. С работната повърхност нагоре структурите на MI ще бъдат свързани към основите на кутиите.
Основни изисквания към монтажните операции: осигуряване на висока механична якост на фугите, добро отвеждане на топлината от конструкцията и в някои случаи добра електропроводимост. Температурите и силите на натиск по време на монтажа не трябва да бъдат твърде високи, за да не се скъсат предварително получените връзки,да не влошава параметрите на конструкциите, да не нарушава механичната им цялост. В същото време те трябва да са достатъчни за здрава връзка. Долната температурна граница е ограничена от необходимостта след монтажа още два пъти (при свързване на проводниците на електродите и запечатване) да се излагат конструкциите на топлина, която трябва последователно да намалява от операция на операция. При избора на метод на монтаж е необходимо също така да се вземат предвид условията на работа на IM.
Лепене . Залепващите фуги не изискват сложно оборудване, лесни са за изпълнение, но не винаги осигуряват добро качество на контакта. Това обяснява използването им главно за микросхеми с ниска мощност, работещи в нетежки условия на работа. Към адхезивния състав се налагат следните изисквания: висока адхезия към материала на тялото, възможно най-близката стойност на TCR за лепилото и материала на тялото, висока устойчивост на влага, нисък вискозитет на лепилото, осигуряващ лепило с дебелина 0,1-0,2 mm, умерена температура на втвърдяване (не повече от 70 ... 80 ° C). Разграничете
непроводими и проводими лепила. Проводимите лепила са състави на базата на епоксидни, органосилициеви и полиестерни смоли с добавяне на сребърни или никелови прахове. Най-добрите уплътнителни свойства се основават на съединения.
Силата на лепилната връзка зависи от качеството на подготовката на залепваните повърхности, дебелината на лепилото, правилния избор на режим и качеството на лепилото.
Недостатъци на лепилните съединения: ниска топлопроводимост, невъзможност за замяна на дефектни конструкции, прегряване при свързване на електродни проводници, възможно изпускане на газове в запечатан корпус.
Стъклените връзки осигуряват добро съгласие за TCLE, отличават се с ниска цена. Основни недостатъцифуги със стъкло: няма електрически контакт, лошо разсейване на топлината, висока температура на омекване на стъклото от около 500°C. Стъклофугите се използват основно при монтаж на стъклокерамични, поликорни и керамични плоскости.
Технологията за монтиране на стъкло включва нанасяне на суспензия от стъклен прах или стъклена паста върху почистена повърхност, компресиране на частите, които трябва да бъдат съединени в касета, изсушаване и претопяване в пещ в контролирана атмосфера.
Запояването с метални припои осигурява висока топло- и електрическа проводимост на ставите, механична якост, добра
споразумение за TKLR. Меките спойки позволяват, ако е необходимо, демонтиране на кристали. В същото време относително ниските температури на топене, най-вече не повече от 280 ... 300 ° C, ограничават използването на меки спойки, необходимостта от нагряване при последващи монтажни операции.
14.2.2. Свързващи щифтове
В зависимост от използваните средства се разграничават жични и безжични инсталации. За монтаж на проводници се използват проводници от сплави Au, Al, Al + Si, Al + Mg.
Заваряването е процесът на получаване на цялостна връзка на части без участието на спойка в резултат на тяхното сближаване на разстояние от атомно въздействие. В процеса на заваряване са възможни следните състояния на материалите на повърхностите на съединяваните части: пластична деформация, топене и пластична деформация, топене и последваща кристализация.
Заваряването може да се извърши с или без нагряване, със или без сила на натиск.
Най-често се използват следните методи за заваряване: термокомпресионно, с индиректно импулсно нагряване, ултразвуково, двуелектродно, лазерно точково и шевно, студено, електроконтактно,
Термокомпресионното заваряване позволява свързване на електрически проводнициняколко десетки микрометра дебели до омични контакти
кристали с диаметър най-малко 20 50 микрона, а електрическият изход може да бъде свързан директно към повърхността на полупроводника без междинно метално покритие: върху кристала се нанася тънка Au или Al жица и се притиска с нагрята пръчка (фиг. 14.5).
Ориз. 14.5 Схема на термокомпресионно заваряване с нагряване на инструмента:
1 - работна маса, 2 - субстрат с тънък филм, 3 - инструмент с нагревател, 4 - проводник
Повърхността на полупроводников кристал, покрит със слой Au или Al, се обезмаслява. Златната тел се отгрява при 300-600°C за 5-20 минути, в зависимост от начина на съединяване на частите. Алуминиевата тел се ецва в наситен разтвор на натриев хидроксид при 80°C за 1-2 минути, промива се с дестилирана вода и се суши.
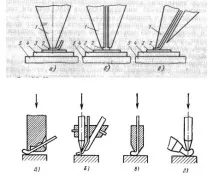
Термокомпресионното заваряване има много разновидности, които могат да бъдат класифицирани според метода на нагряване, метода на закрепване, формата на инструмента.
Според метода на нагряване термокомпресионното заваряване се отличава с отделно нагряване на иглата, кристала или щанца, както и с едновременно нагряване на два от тези елементи. Според метода на свързване заваряването може да бъде челно и припокриващо се. Според формата на инструмента се разграничават „птичи клюн“, „клин“, „капиляр“ и „игла“ (фиг. 14.6).
Микрофугата се образува чрез едновременно излагане на частите на температура и налягане. Налягането се предава на материалите, които ще се съединяват чрез заваръчния инструмент и трябва да гарантира, след нагряване, деформацията на проводника, който ще се свързва, е не по-малко от 25%, но не повече от 75%. С повишаването на температурата е по-вероятно да има химическа връзка между материалите, които ще се съединяват.
Пластичните деформации водят до ефективно разрушаванеповърхностни оксидни филми, които са основната пречка за химичното взаимодействие.
Ориз. 14.6 Инструмент за термично компресиране:
а - клин; b - капилярна; клюн"; 1 - инструмент; 2. - свързан проводник; 3 - контактна площадка; 4 -
субстрат; 5 - маса на заваръчната инсталация
"птичи клюн"; b "клин"; в "капиляра"; g "игла"
Основните параметри на режима на термокомпресионно заваряване са специфично налягане, температура на нагряване и време на заваряване.
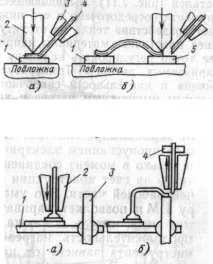
Термичното компресиране с клин за припокриване се използва, когато има ниски изисквания за точността на позицията на заваръчното петно върху контактната зона и за производителността на процеса (фиг. 14.7); термична компресия на дупето
Ориз. 14.7 Термична компресия на клинова обиколка:
a - свързване на проводника към кристала; b - връзка с контактната площадка и прекъсване на проводника;
1 - кристал; 2 - клин; 3 - капилярна; 4 - проводник; 5-контактна подложка
Ориз. 14.8 Термична компресия на задната топка:
а - заваряване на златна тел с алуминиева контактна площадка; б - заваряване на втория край на телта с траверса на изхода на тялото и счупване на телта;
1 - основата на тялото на IM; 2 – капилярна; 3 - траверса; 4 затягащо устройство
Термична компресия чрез зашиване (фиг. 14.9) - двете съединения се припокриват, за да се получи отпечатък на инструмент с усилвател върху телта на мястото на заваряване.
Заваряването с термична компресия има следните предимства:
1. частите се свързват без разтопяване на заваряваните материали;
2. специфичното налягане, приложено върху кристала, не води до механично увреждане на полупроводниковия материал;
3. връзките се получават без замърсяване, тъй като не се използват спойки и потоци.
ДА СЕНедостатъците включват ограничен брой двойки заварени материали, високи изисквания към качеството на повърхностите, които трябва да бъдат съединени, и относително ниска производителност на визуално подравняване.
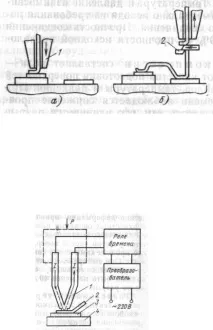
Ориз. 14.9 Термична компресия чрез зашиване:
а - заваряване на проводника с контактната площадка на кристала; b - заваряване на втория край на проводника с контактната площадка;
1 – капилярна; 2- ножица
Електроконтактното заваряване се състои в нагряване на свързаните елементи в локалните области на приложение на електрода.
При заваряване под налягане с индиректно импулсно нагряване (SKIP)
нагряването на работната зона се осъществява чрез токов импулс, преминаващ директно през инструмента (фиг. 14.10).
Ориз. 14.10 Схема на микрозаваряване с индиректно импулсно нагряване:
1 - инструмент за заваряване; 2 - свързан проводник; 3 - контактна площадка; 4 - субстрат
Възможно е да се заваряват по-малко пластмасови материали, като Au, Al, Cu, Ni (до 100 микрона в диаметър) с филми от много материали, както и по-прецизно да се контролира количеството и продължителността на нагряване на заваряваните части. За да смекчите топлинния шок върху контактната подложка с филм, препоръчително е едновременно да загреете продукта (т.е. работния плот).
Основните параметри на процеса на електроконтактно заваряване са стойността на заваръчния ток, скоростта на нарастване на тока, времето на излагане на тока на елементите, които трябва да бъдат свързани, и силата на притискане на електродите към частите, които трябва да бъдат свързани.
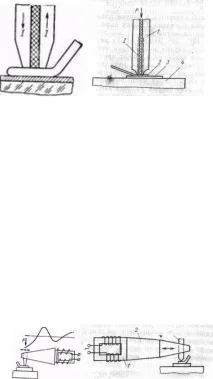
Използват се два метода за електроконтактно заваряване: с едностранно разположение на два електрода и с едностранно разположение на един двоен електрод (фиг. 14.11).
Ориз. 14.11 Микрозаваряване с двоен електрод:
1 - инструмент за заваряване; 2 - свързан проводник; 3 - контактна площадка; 4 -субстрат
При преминаване на електрически ток основната част от джауловата топлина се отделя в зоната на максимално съпротивление в точката на контакт на заваряваните части.
Основните предимства на метода: малка площ и кратка продължителност на термично излагане, висока производителност.
Недостатъци: Възможни са изтичане на ток и термичен удар.
Ултразвуковото заваряване има следните предимства: липса на нагряване на съединяваните елементи, кратко време за заваряване, възможност за заваряване на различни и трудни за заваряване материали (и дори диелектрици). Липсата на отопление ви позволява да получавате връзки, без да разтопявате частите за заваряване. Краткото време за заваряване позволява да се увеличи производителността на процеса на сглобяване.
Повърхностите, които трябва да бъдат съединени, се подлагат на силни сили на срязване, като се използва нормално налягане и надлъжни вибрации на инструмента с честотата на ултразвук (фиг. 14.12) (предаването на вибрации в контакт между повърхностите, които трябва да бъдат заварени, се дължи на силите на триене), в резултат на което микрограпавините се отрязват, оксидните филми се разрушават и се избутват обратно в пролуките между микроиздатините. За повишаване на производителността и качеството на процеса те се комбинират с импулсно индиректно нагряване на инструмента.
Ориз. 14.12 Ултразвуково микрозаваряване:
1 - магнитостриктор; 2 - 3 - инструмент за заваряване