4.3.6. Производителността на екструзионната инсталация
Екструдирането е непрекъснат процес, състоящ се от поредица от последователни операции. Всяка операция, както е известно от теорията на непрекъснатите процеси, може да се превърне в "тясно място", което в общи линии може да определи работата на цялата инсталация. Следователно при разработването на процеса на екструдиране е необходимо, въз основа на моделите на процеса във всяка секция, да се изберат такива параметри на процеса, които биха били оптимални за всички секции с еднаква производителност.
Тъй като мощността на екструдера е взета като основа за определяне на мощността на инсталацията, се използва следната емпирична формула:
където Q е мощност, kg/h;
a е коефициентът на запълване на шнека с материала;
N е броят на оборотите на червея, rpm;
V е обемът на един оборот на винтовото нарязване в товарната зона;
γ е обемното тегло на натоварения материал.
Производителността на един и същ екструдер за различни материали не е еднаква. Ако вземем като единица производителността по време на обработката на PVC, тогава за други материали могат да бъдат зададени следните относителни стойности на производителност:
LDPE | HDPE | Винипласт | PS | ПП | PA |
0,8 | 0,6 | 0,5 | 0,45 | 0,4 | 0,35 |
На практика се търси подобряване на производителността, което може да се постигне по различни начини:
- увеличаване на скоростта на въртене на червея;
- увеличаване на дълбочината на режещия канал;
- увеличаване на ъгъла на наклон на рязане;
- намаляване на радиалния просвет между цилиндъра и червяка.
Производителността варира в зависимост от специфичните условия на работа на машината, вида на материалите, диаметъра на шнека и конструкцията на екструзионната глава.
Ако покажете зависимостипроизводителност на екструдера при натиск за различни обороти на червея, тогава получаваме серия от успоредни прави линии с отрицателен ъгъл на наклон (фиг. 4.10). Тези прави линии са характеристиките на червея.
Ориз. 4.10. Характеристики на червея при различни честоти на неговото въртене:
Увеличаването на дълбочината на шнековия канал в хомогенизиращата зона води до увеличаване на предния поток. Когато цилиндърът е отворен, производителността е висока, когато цилиндърът е затворен, когато има високо налягане, противотокът се увеличава и производителността рязко намалява.
Помислете как се променя производителността в зависимост от налягането и геометрията на червея (фиг. 4.13).
Ориз. 4.13. Зависимост на ефективността от
налягане и геометрия на червея:
1 - формираща глава с ниско съпротивление, 2 - глава с високо
съпротивление, 3 - шнек с фино рязане, 4 - шнек с дълбоко рязане
Установено е, че с малко съпротивление на главата, винт с дълбока резба осигурява най-добра производителност, с високо съпротивление на главата - винт с фина резба.
Известно е, че с увеличаване на дължината на дозиращата зона количеството на обратните потоци намалява както през шнековия канал, така и в пролуката между шнека и цилиндъра (фиг. 4.14).
Ориз. 4.14. Производителност спрямо дължина
шнекова дозираща зона:
1 - шнек с дълга дозираща зона,
2 - винт с къса дозираща зона
Чрез съответното удължаване на изходната зона на шнека е възможно да се компенсира, в определени граници, намаляването на производителността на екструдера, ако при средно противоналягане, т.е. когато използвате инструмент за формоване със средно съпротивление, използвайте винт с фино нарязване вместо винт с дълбоко нарязване.
Помислете как зависи ефективносттавърху геометрията на канала и дължината на дозиращата зона, като се вземе предвид налягането (фиг. 4.15).
Ориз. 4.15. Зависимост на ефективността от
геометрия на канала и дължина на дозиращата зона:
1 - винт с дълбоко рязане и къса екструзионна зона,
2 - шнек с фино рязане и къса екструзионна зона,
3 - винт с дълбоко рязане и дълга екструзионна зона
За високо съпротивление или натиск на мундщука, фино нарязаният винт с дълга зона на екструдиране осигурява най-доброто представяне.
Интерес представлява зависимостта на производителността от температурния режим (фиг. 4.16).
Стойността на производителността практически не се променя при едновременна промяна на температурата на стопилката в шнековия канал и главата, но е установено, че с повишаване на температурата на материала от 190 ºС до 240 ºС налягането на екструдиране намалява с почти 35%, т.е. разходите за енергия се намаляват с 1/3.
Ориз. 4.16. Зависимост на ефективността от
Най-важната цел на екструзионната машина е нагряването и термичната хомогенизация на стопилката. В екструзионните машини, особено тези с големи диаметри и дълги винтове, материалът може да се прегрее. диаметърът на червея значително влияе върху производителността и консумацията на енергия. Следователно по-пълна информация за процеса може да се получи, ако на характеристичната диаграма, освен температурните линии, се нанесат и линиите на хомогенност, границите на икономическата ефективност от използването на екструзионна машина при дадена производителност (фиг. 4.17).
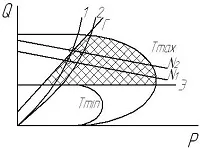
Ориз. 4.17. Обобщена характерна диаграма:
T min и Tmax - линии на минимални и максимални температури,
При промяна на параметрите на екструдиране, работната точка може да бъде изместена по такъв начин, че с и се получава новият режимнай-добър резултат по отношение на производителност, качество и други показатели.
Процесът на екструзия е в постоянно динамично равновесие: промяната в един параметър на процеса води до промяна в други. Следователно, за специфични продукти се изисква голямо умение от персонала по време на процеса, за да се идентифицират резервите и да се създаде най-продуктивният процес с висококачествени продукти.