Автоматично регулиране на групата макари на мастиления модул
Валери Щоляков Проф. MGUP
Мастилителните модули са част от секцията за офсетов печат и са разположени близо до печатащата форма, тъй като мастилото се нанася върху плочата чрез контакт. Те трябва да осигурят стабилно и равномерно нанасяне на необходимото количество боя върху формата с възможност за безстепенно регулиране на подаването му и бързо излизане в режим на работа. В зависимост от консистенцията на боите, машините за мастило се разделят на устройства за вискозни и течни бои. Пресите за висок печат и плоския офсетов печат традиционно използват вискозни мастила.
Принципът на работа на машините за мастило за вискозни мастила се основава на отделянето от общата маса мастило, поставено в кутията за мастило, част от мастилото, което след това се разточва, намалявайки дебелината до необходимата стойност, след което се навива върху печатната форма. Процесът на приготвяне на равномерен мастилен слой се извършва последователно от три групи мастилен апарат:
• група за подаване на боя или за подаване на боя, предназначена за отстраняване на мастилото от кутията за мастило и подаването му към групата за валцуване;
• валцоваща група, която осигурява създаването на равномерен непрекъснат слой боя за пренасянето му към валцоващите валяци;
• ролкова група, предназначена за нанасяне на тънък равномерен слой мастило върху печатащите елементи на формата.
По време на стационарния процес на печат, в резултат на действието на мастилоподаващата и ролковата групи, се образува стабилен поток от мастило, който, движейки се към формата, се изтънява поради добавянето и разделянето на слоеве мастило във всяка контактна зона на мастилените ролки. Валцоващата група на мастилената единица извършва довършителната операция по нанасяне на тънък,равномерен слой мастило върху печатащите елементи на формата.
Ролковите ролки нямат принудително задвижване. Те еластично взаимодействат с печатната форма и ролковите цилиндри, въртящи се поради силите на триещо сцепление с тях. Процесът на нанасяне на боя върху формата е придружен от два насрещни потока боя, единият от които е работен, който осигурява ролките на боята върху формата, а другият е обратният, който се образува след контакта на ролките с формата. В момента на контакт на всяка назъбена ролка с печатащите елементи на формата, върху повърхността им остават непотърсени участъци с мастило, които остават в ролковата група. Това е така нареченият обратен релеф на мастилото, който се образува поради наличието на празнини върху формата, които не приемат мастило и които, за да се поддържа стабилната работа на мастиления апарат, трябва да бъдат унищожени в групата за валцуване. Като се има предвид индивидуалността на всяка печатна форма, естеството на обратния релеф на мастилото също е индивидуално, което не позволява да се създаде идеална мастилена машина за всички случаи.
За да оптимизират процеса на нанасяне на мастило върху формата, водещите световни производители на печатно оборудване са разработили специални програми за изчисляване на мастилените единици на офсетните печатни машини. С помощта на тези програми се определят най-кратките пътища на мастилото до формата, вариантите за конструиране на мастилена машина, нейните основни конструктивни параметри, както и нейната производителност. Оптималният път на потока на мастилото осигурява максимално подаване на мастило към първите две ролки, което е до 90% от основния обем. Останалите ролки прехвърлят останалите 10% от мастилото върху плочата, докато изравняват предварително нанесения мастилен слой.
Като правило, в мастилената единица на листови офсетови пресиброят на назъбващите ролки е четири, а при валцоващите машини - две или три. Диаметрите на назъбващите ролки и разстоянията между тях са избрани така, че печатащите елементи на формата, ако е възможно, да се срещат с различни секции на ролките. За да направите това, разстоянието между двойка назъбени ролки не трябва да бъде кратно на диаметъра на тези ролки. Подобна подредба допринася за нанасянето на равномерен слой мастило с по-малка вероятност от шаблониране, което може да се прояви в налагането на използвани преди това печатни или празни елементи от чертежа на формата върху отпечатъка. Причината за шаблонизирането е наличието на неунищожен обратен мастилен релеф, който може да допринесе за появата на вторичен, т. нар. паразитен мастилен релеф върху формата или нейните фрагменти.
Качеството на печат зависи от равномерността на нанасяне на мастилото върху печатната форма, която се определя от точността на монтажа на ролките спрямо формата и ролковите цилиндри. За да направите това, ролките са фиксирани в специални ключалки, които ви позволяват точно да регулирате силата на тяхното притискане към формата и цилиндрите на ролката. Нарушаването на правилната инсталация на ролките води до промени в равномерността на слоя мастило, когато се нанася върху формата. Всяка ролка от търкалящата група е разположена между две задвижващи цилиндрични повърхности (валцови и пластинчати цилиндри). Назъбените ролки се въртят около фиксираната си ос поради силите на триене, които трябва да се вземат предвид при регулиране на тяхната позиция и сила на притискане към формата и цилиндъра на ролката. Има определен ред, в който се настройват назъбените ролки, като назъбената ролка първо се подравнява с печатния цилиндър и след това с повърхността на плочата. В момента се използват различни конструкции на инсталационни механизми.ролки (ключалки), които, независимо от схемата на тяхната конструкция, се характеризират с общи характеристики:
• по време на подготовката на машината за печат или при автоматично спиране на процеса на печат, формиращите ролки трябва да бъдат отделени от цилиндъра на формите, така че печатната форма да не се пренасища с мастило. За да направите това, назъбените ролки са еластично притиснати към формата с пружина или пневматика;
• всяка ролка, заедно с лагерите, притиснати върху шийките й, е фиксирана в специални ключалки, които ви позволяват да регулирате позицията й спрямо ролковия цилиндър и форма, както и бързо да ги отстранявате и инсталирате в мастилената машина.
На фиг. Фигура 1 показва опция за монтаж на ролки от валцоващата група, където всяка ролка 1 е фиксирана от двете страни с ключалки, фиксирани в закачалки 2, монтирани спрямо стените на машината в ексцентрични втулки 3 и 7. Благодарение на действието на компресионните пружини 4, ролката е еластично притисната към формата 5 и валцовия цилиндър 6. Когато втулките 3 се въртят, пресоването силата на ролката спрямо търкалящия цилиндър 6 се променя и с помощта на ексцентрика. При вътрешните втулки 7, опиращи се върху повърхността на лостовете 8, налягането се регулира спрямо ролковия цилиндър. Когато ролките се освободят, лостовете 8 автоматично или ръчно се завъртат и, компресирайки пружината, изваждат всички ролки от матрицата (на диаграмата позицията на ролката 1 по време на оставката е показана с пунктирана линия). Ексцентричните втулки се завъртат от принтера ръчно чрез червячни, винтови или лостови механизми, управлението на които е поставено на стените на машината за лесна поддръжка.
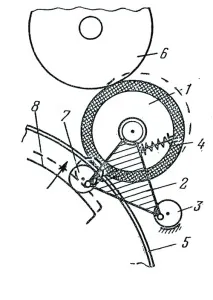
Ориз. 1. Схема на механизма за монтиране и регулиране на набраздяващата ролка
Регулирането на назъбените ролки изисква спазването на определени изисквания при монтажа им. Изкривяване или силен натискролките към печатащия барабан може да причинят ивици, засенчване или неравномерен печат. Резултатите от такова нарушение не само ще повлияят на качеството на печата, но и ще причинят преждевременно износване на печатната форма и самите ролки. В същото време силното притискане на ролките към формата може да доведе до изстискване на слой овлажняващ разтвор от повърхността й и частично смилане на повърхността на матрицата, което ще наруши нейната микрогеометрия. Във всеки случай прекомерното силово взаимодействие в контактните зони на еластичната назъбена ролка ще доведе до активно износване на нейната повърхност.
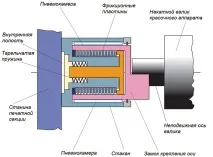
Ориз. 2. Структурата на механизма за автоматично регулиране на позицията на набраздяващата ролка
Трябва да се има предвид, че ролките, хлабаво поставени спрямо печатната форма, причиняват неотпечатване на изображението с мастило върху отпечатания материал и могат да причинят ивици, които се появяват върху отпечатъците под формата на напречни ивици с нарушение на оптичната плътност. В допълнение, причината за ивиците доста често е износването на опорните елементи на назъбените ролки или частичното им разрушаване, в резултат на което в момента, в който навлязат в работната зона на цилиндъра на плочата, те започват да „скачат“ поради удар на ръба, което води до нарушаване на качеството на печат.
Операцията по регулиране на назъбените ролки се извършва ръчно и като правило изисква много време. Въпреки това, благодарение на дизайна, разработен от концерна KBA, регулирането на назъбените ролки в мастиления блок на ролната печатна машина може да бъде автоматизирано, което ще позволи дистанционно регулиране и контрол на налягането в контактните зони, както и извършване на тяхното оттегляне. За тази цел всяка назъбена ролка е монтирана в ключалки, които са поставени вътре в чашите, фиксирани на стената на машината. На фиг. Показан е 2 монтажназъбена ролка от страната на задвижването. Назъбените ролки традиционно се изработват под формата на кухи цилиндри, покрити с еластичен материал и свободно монтирани върху иглени лагери спрямо неподвижна ос, фиксирана в ключалките. Четири камери от мембранен тип (пневматични камери) са разположени симетрично между тялото на ключалката и вътрешната повърхност на чашата, всяка от които е свързана с въздушна мрежа и е предназначена да контролира позицията на набраздяващите ролки спрямо валцоващите и оформящи цилиндри. Позицията на назъбената ролка се контролира чрез подаване на въздух към вътрешната кухина на чашата, за да се облекчи натоварването от пружините Belleville, което позволява да се намали сцеплението на фрикционните плочи в опорните чаши за по-нататъшно движение на ключалката на набраздената ролка. След това налягането в пневматичните камери се променя, в резултат на което набраздяващата ролка има възможност да се движи в една или друга посока поради изместването на оста си спрямо неподвижните чаши.
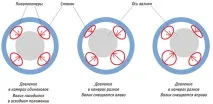
Ориз. 3. Регулиране на позицията на набраздяващата ролка при промяна на налягането в пневматичните камери
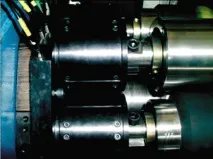
Ориз. 4. Външен вид на механизмите за закрепване на назъбени ролки
На фиг. 3 показва варианти за позициониране на набраздяващата ролка в зависимост от разликата в налягането в пневматичните камери. Наличието на пневматика позволява да се осигури, при определена разлика в налягането в пневматичните камери, точна, без изкривяване, инсталация на назъбените ролки спрямо цилиндрите на плочата и ролката. След регулиране на позицията на назъбената ролка, налягането вътре в чашата и пневматичните камери се отстранява, в резултат на което конусната пружина фиксира ключалките на назъбената ролка в нова позиция. Външният вид на механизмите за закрепване на две назъбени ролки от страната на задвижването на машината е показан на фиг. 4.
Настройка и управление на пенсиониранетонарязването на ролките се извършва от пневматични системи за автоматизация в автоматичен режим в съответствие с разработения алгоритъм. Новият оригинален дизайн на инсталацията на назъбените ролки позволява на принтера дистанционно, от контролния панел, бързо да извършва прецизно позициониране на всяка назъбена ролка, както и да регулира и контролира силата на нейното силово взаимодействие с формата и цилиндъра на ролката. Операцията по регулиране е значително улеснена и ускорява подготовката на мастилените модули на ролната печатна машина за работа, като позволява за няколко минути едновременно да се регулира и контролира позиционирането на назъбените ролки, чийто брой в съвременните машини за вестници достига няколко десетки.