Характеристики на получаване на полиолефинови пени чрез екструзионни методи
ПЕНЕНИ ПЛАСТМАСИ
Характеристики на получаване на полиолефинови пени чрез екструзионни методи
Но ниският вискозитет на стопилката на полиолефините, особено на полиетилена с ниска плътност (LDPE), не е единствената причина, която предотвратява производството на лека пяна. Известно е [1], че необходимото условие за постигане на стабилна клетъчна структура и нейното последващо фиксиране в твърда структура от пяна е по-скоро не вискозитетът на първоначалния състав, а скоростта на увеличаване на вискозитета, с увеличаване на което се увеличава здравината на стените и ръбовете на клетките. За дунапрени на основата на линейни високи полимери това условие се постига чрез физическо действие – охлаждане на пяната. Достатъчно бързото охлаждане на всеки газонапълнен материал, включително полимерна пяна, обаче е трудно поради ниската му топлопроводимост. В резултат на това вискозитетът на течната фаза намалява твърде бавно и пяната се разпада. Този нежелан "термофизичен" ефект, който може да причини коалесценция на всяка полимерна пяна, е още по-утежнен в случай на разпенени полиолефини поради тяхната висока степен на кристалност, тъй като тяхната скорост на охлаждане намалява значително, когато се достигне температурата, при която се отделя топлината на кристализация (за LDPE това се случва при 95 - 100 0C), което също предотвратява бързото увеличаване на вискозитета на системата.
За да се преодолеят тези трудности при производството на леки полиолефинови пени, се използват следните две техники:
1) въвеждането на нискокипящи течности (физични газови генератори) в състава, които, изпарявайки и разпенвайки полимерната стопилка, отнемат голямо количество топлина и по този начиндопълнително охлаждане на полимерната фаза (от тази гледна точка, въпреки екологичните проблеми, фреоните, които имат много висока топлина на изпарение, остават най-добрите добавки досега);
2) омрежване на полиолефини чрез химически (поради химични реакции с въвеждането на омрежващи агенти, които за PE обикновено са пероксиди, като дикумил пероксид) и физически (третиране с бета или гама лъчение) методи и по този начин фиксиране на тяхната разпенена структура.
Въз основа на това съществуват методи за производство на пенопластмаси с помощта на химически или физически разпенващи агенти (с други думи, разпенващи агенти или разпенващи агенти). Ако се използват химически разпенващи агенти (CGE), тогава методите за формоване чрез екструзия могат да бъдат разделени на директна екструзия и екструзия, последвана от разпенване. В първия случай гранулите на състава влизат в екструдера, където се нагряват до температурата на разлагане на разпенващия агент, след което разтопеният състав се изстисква през главата на екструдера и, охлаждайки, се пени в момента на излизане от главата. Трябва да се отбележи обаче, че този метод практически не се използва, тъй като без използването на омрежващ агент се получава сравнително тежка пенопласт - с видима плътност най-малко 350 kg / m
Отличителна черта на екструдирането с последващо разпенване е, че стопилката от ПМ или изобщо не се разпенва, или само частично се разпенва, когато напуска екструдера, а окончателното разпенване се случва едновременно с процеса на омрежване, когато заготовките се нагряват до температурата на омекване на полимера. Такова разширение на технологичнияВ същото време процесът осигурява някои предимства: дизайнът на главата на екструдера е опростен и производството на пяна с ниска видима плътност е улеснено. Основната трудност при изпълнението на този процес е равномерното разпенване на детайла във всичките три измерения по време на вторичното му нагряване.
Съставите, съдържащи химически омрежващи агенти, се преработват в продукти, пълни с газ, като се използва само двустепенна технология. При радиационното омрежване се използват както директни, така и двуетапни технологии. Ако се използват физически разпенващи агенти, тогава е възможно само директно (едноетапно) екструдиране (фиг. 1).
Таблица. Основните показатели за физичните и механичните свойства на екструдирани полиетиленови пени, получени с помощта на физически (едноетапен метод) и химични (двуетапен метод) разпенващи агенти
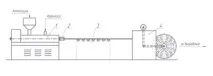
Ориз. Фиг. 1. Схема на екструзионна линия за производство на профили от пенополиетилен с използване на нискокипяща течност като разпенващ агент: 1 - екструдер с устройство за въвеждане на разпенващ агент в стопилката; 2 - екструзионна глава; 3 - ролкова маса; 4 - дръпнете намотката
В стопилката обикновено се въвежда нискокипяща течностполиолефини в дегазиращата зона на шнека. Съставът, който представлява полимерни гранули, прахообразни с талк, който служи като нуклеиращ агент, се разтопява в цевта на екструдера 1 и се насища с пенообразувател. В матрицата 2 се формира екструдируем профил, който се пени при напускане на матрицата за екструдиране и се охлажда поради изпарението на течността. На ролковата маса 3 профилът за получаване влиза в изтеглящото устройство за навиване. След това пяната се изпраща за стареене, по време на което, поради дифузията на нискокипяща течност, тя се заменя с въздух. Свойствата на полиетиленовите пени, получени с помощта на физични и химични разпенващи агенти, са показани в таблицата.
Понастоящем омрежените полимерни пени представляват нарастващ интерес за потребителите. В допълнение към ниската плътност, те имат по-високи (в сравнение с неомрежени полимери от пяна) физични и механични свойства, стабилност на размерите и (което напоследък стана особено важно) повишена устойчивост на топлина. Използваното за тези цели радиационно омрежване обаче има няколко съществени недостатъка. От гледна точка на потребителите, това са преди всичко малката дебелина на стената на екструдирания профил (по-малко от 1,5 mm) и ограничената форма на секцията на екструдата (понастоящем по този метод се произвеждат само листови омрежени пенополимери). Освен това има проблеми, причинени от строгите изисквания за безопасност при използването на радиация. Ето защо понастоящем двуетапният метод за производство на разпенени профили с помощта на химически разпенващи агенти и (или) химически омрежващи агенти е намерил най-широко приложение.
Например, за производството на пенополиетилен, използвайки двуетапна технология, състав, състоящ се отLDPE, разпенващ агент (porofor марка ChKhZ-21), омрежващ агент (дикумил пероксид) и активиращ комплекс, състоящ се от цинков оксид, цинков стеарат и стеаринова киселина. За да се получат висококачествени пени, съставът трябва да бъде възможно най-хомогенен. Трудността при създаването на хомогенни многокомпонентни състави на базата на полиолефини (по-специално полипропилен) се определя от факта, че тези полимери имат лоша съвместимост с повечето твърди и течни вещества, използвани като компоненти на състава. Съществуват редица методи за приготвяне на състави за разпенване на полиолефини, всеки от които не е лишен от недостатъци [2]: • разпрашаване на полимерни гранули с фино диспергиран прах от разпенващ агент с добавяне на минерално или трансформаторно масло за по-добра адхезия на полимера и разпенващия агент; • смесване в миксер от затворен тип на полимерни гранули, разпенващ агент и филмообразуващ разтвор (15% разтвор на нискомолекулен полиетилен). След отстраняване на разтворителя, например CCl4, най-тънкият филм се образува върху повърхността на полимерните гранули; • смесване на прахообразни частици от полимера на порообразуващия агент и други компоненти и след това гранулиране на получената смес; • валцуване на полимера, разпенващия агент и други компоненти при повишена температура, последвано от раздробяване или гранулиране на състава; • въвеждане на разпенващ агент и други компоненти в полиетилен във вискозно състояние, последвано от гранулиране на състава.
Последният метод, въпреки високата специфична консумация на енергия, е най-разпространеният, главно поради неговата технологичност. Концентратите на разпенващия агент и други необходими компоненти под формата на гранули се въвеждат в състава чрез смесване с полиолефинови гранули. ПриВ този случай е желателно концентратът и полиолефиновите гранули да имат еднаква плътност и размер, което би предотвратило разслояването на състава. Съставът под формата на гранули се зарежда в бункера на екструдера 1 на листовия блок (фиг. 2). Зоната за зареждане на цилиндъра за материал и винта трябва да се охлади с вода. Цилиндърът на екструдера има различни температури в зони. Например при LDPE температурата на зона I е 110 0С, зона II - 120 0С, зона III - 125 0С. Температурата на плоската шлицева глава 2 е зададена на (135) 0С, а температурата на крайните зони на нагревателите е (140) 0С.
В цевта на екструдера масата се разтопява и хомогенизира. Освен това хомогенната стопилка се пресова през главата с плоски прорези 2 и под формата на лист постъпва в калибриращите ролки 3 с температура 80 - 90 0С. Формованият лист влиза в ролковата маса 4, където се извършва въздушното охлаждане на листа, а след това в устройството 5 за подрязване на ръбове с ширина 50 mm. След това листът влиза в устройствата за навиване 6. Отрязаните ръбове на листа се използват като отпадъци за връщане. При получаване на листов полуфабрикат не се допуска преждевременното му разпенване (разлагане на разпенващия агент). След излагане в продължение на 48 часа, полуготовите листове се нагряват в специална баня (фиг. 3) до температура 200 - 220 0C за омрежване и разпенване. Като топлопреносна течност се използват силиконови течности, парафин, восък, но най-често разтопени соли, като нитритно-нитратна смес.
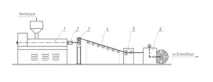
Ориз. Фиг. 2. Схема на екструзионна линия за производство на листови полуготови продукти от полиетиленова пяна с използване на химически разпенващ агент и химически омрежващ агент: 1 - екструдер; 2 - екструзионна глава; 3 - калибриращи ролки; 4 - ролкова маса; 5 - устройство за подрязване на ръбове; 6 - издърпваненавивач
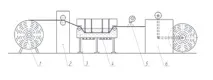
Ориз. 3. Схема на линията за разпенване на листови полуфабрикати: 1 - ролка листови полуфабрикати; 2 - спирачни ролки; 3 - баня; 4 - нагревателни елементи; 5 – вентилатор; 6 - дръпнете намотката
На базата на полиолефини се изработват еластични, полутвърди и твърди дунапрени в широк диапазон от стойности на видима плътност - от 40 до 850 kg/m3, които се характеризират с висока амортизационна способност, ниска водопоглъщаемост, отлични електроизолационни свойства, висока химическа устойчивост и липса на корозионна способност. Омрежените полиолефинови пени също са леки, имат еднаква структура с фина мрежа, висока топлоустойчивост, устойчивост на атмосферни влияния и UV устойчивост.
Литература 1. Берлин А.А., Шутов Ф.А. Химия и технология на газонапълнени високополимери. – М.: Наука, 1980. – 504 с. 2. Ларионов А.И., Матюхина Г.Н., Чернова К.Л. Пенополиетилен, неговите свойства и приложение. - Л.: LDNTP, 1973. - 48 с. 3. Панов Ю.Т. Научни основи за създаване на пенопласти от второ поколение. - Владимир: Владимирски държавен университет, 2003. - 176 с.
Ю.Т. Панов
Според материалите на списание "Полимерни материали"