Индукционни пещи за топене на цветни сплави
Повечето съвременни големи леярни за топене на цветни сплави са оборудвани с индукционни пещи с желязна сърцевина, които произвеждат сплави от тежки и леки цветни метали. Индукционните пещи имат значителни предимства пред всички други леярски пещи. Осигуряват високо качество и пълна хомогенност на сплавите, ниски загуби на метал, висока производителност, ниска консумация на енергия, висока чистота и култура на леярство. На фиг. 235 показва дизайна на домашна индукционна пещ тип ILO-0,75 (индукция, месинг, еднофазна с капацитет 0,75 тона, мощност 400 kva).
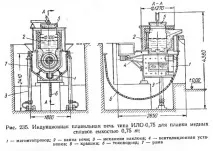
Пещите от този тип са широко разпространени в леярните за топене на мед, месинг, бронз, никел, купроникел и други цветни сплави. Индукционните пещи с желязна сърцевина, използвани за топене на алуминиеви сплави, се различават донякъде по своя дизайн. Факт е, че по време на топенето на алуминий алуминиевият оксид, образуван на повърхността на ваната, се отлага в каналите на пещта, което води до промяна в тяхното електрическо съпротивление и нарушаване на циркулацията на метала. За безплатно почистване на оксидни отлагания, каналите в пещите за топене на алуминий са направени прави с увеличено напречно сечение и оборудвани с отвори с тапи, които позволяват периодично отваряне и почистване на каналите. Поради намаляване на плътността на тока в каналите и увеличаване на дебелината на метала в шахтата, смесването на метала в пещта намалява, което отслабва отлагането на оксид в каналите. Индукционните пещи с желязна сърцевина, или така наречените канални пещи, могат да бъдат еднофазни и трифазни, с мощност от 400 до 2000ква, с вместимост от 0,75 до 15 тона за месинг, от 20 до 40 тона за цинк, от 0,5 до 6 тона за алуминий и мед. Броят на индукционните единици за пещи от този тип е 1-6. Пещите работят при напрежение 220-1000 V. Специфичният разход на енергия е, kWh/t: за месинг 200; за алуминий 450; за мед 240; за цинк 110. Времето на едно нагряване е от 0,5 до 3 часа.
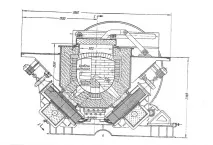
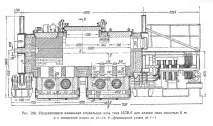
На фиг. 236 показва индукционна канална пещ с индустриална честота със стоманена сърцевина от типа ILK-6, използвана в съвременните медолеярни за производство на отливки от червена мед. Капацитетът на пещта за мед е 5-6 тона, общата мощност е 1600 kVA с активна мощност 1400 kW. Дневната производителност на пещта е 80-120 тона, броят на нагряванията на ден е 16-18. Пещта се състои от следните основни компоненти: заварен стоманен корпус с два носещи ръба за обръщане, облицован отвътре с огнеупорни тухли и пълнеж; четири подвижни монофазни индукционни блока; механизъм за завъртане на пещта; вентилатори за охлаждане на облицовката на каналната част на индукционни агрегати; три капака, единият от които (централният) е оборудван с повдигащ механизъм.
Индукционните модули са разположени в долната част на фурната в два реда. Всеки блок се състои от: корпус с огнеупорна обвивка, в която има правоъгълни топилни канали, магнитопровод с разглобяема ярма, вентилатор за охлаждане. При теч в някой от индукционните блокове не се извършва цялостен ремонт на цялата пещ, а се подменя само индукционния блок с нов, който е предварително подготвен отстрани.
Индукционните модули се захранват от понижаващ трансформатор при 450 V и 50 Hz. Токозахранването на пещта се осъществява от гъвкави кабели с водно охлаждане. Водно охлаждане се използва и за индуктори. Тялото на пещта се върти и в дветестрана с помощта на задвижващия механизъм. Сместа се зарежда през централния прозорец за зареждане с капака нагоре. Металът от пещта се източва през кран, разположен на крайната стена. Оста на кранния отвор съвпада с оста на въртене на пещта. Медта се топи под слой въглен или в атмосфера на защитен газ. Срокът на експлоатация на пещта ILK-6 е до 10 години. Пещта е добре комбинирана с индукционен миксер и машина за полунепрекъснато леене, което позволява получаването на медни блокове с тегло до 4 тона и дължина до 5 m.
В металургията на цинка за претопяване на катоди се използват индукционни пещи с желязна сърцевина с капацитет 20 и 40 тона от типа ITs-20 и ITs-40 (фиг. 237). Оборудвани са с шест индукционни нагревателя с хоризонтални нагревателни канали и вертикални магнитопроводи. Пещта ID-40 се захранва от два трифазни пещни трансформатора по 1000 kVA всеки с вторично напрежение 450-550 V. Пещта се състои от две камери: голяма камера за топене и малка разпределителна камера. Катодният цинк се зарежда в камерата за топене с помощта на ролкова маса през товарния вал, директно във ваната с разтопен метал. Разтопеният цинк се изхвърля от пещите през изхода на дозиращата камера в кофа или леярска машина. По време на топенето на катоден цинк се образуват дроси - смес от цинков оксид с метални частици, които периодично се отстраняват от повърхността на ваната през шлаков прозорец. Производителността на пещите за свински цинк е, t/ден: пещи ITs-20 до 110; пещи IC-40 до 300, консумация на енергия 110 - 120 kWh / t.
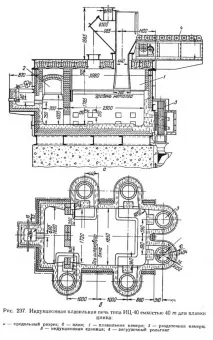
В допълнение към индукционните пещи с желязна сърцевина, индукционните пещи без желязна сърцевина се използват за топене на цветни и благородни метали и сплави.
На фиг. 238 показва индукционен вакуумен агрегат за топене и лееневакуумна мед с висока чистота, чиято основна част е тигелна високочестотна индукционна пещ с капацитет 500 kW с тигел с капацитет до 1 тон.
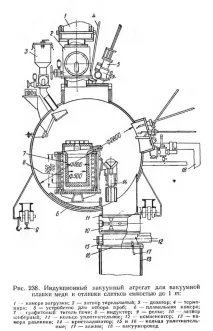
Камерата за зареждане е вертикален цилиндричен съд, прикрепен към горната част на камерата за топене чрез специална уплътнителна врата. Зареждащата камера има индуктор за предварително нагряване на контейнера със заряда, преди да се спусне в тигела на пещта.
Камерата за топене е хоризонтален цилиндричен съд, заварен от листова стомана. Вътре в камерата за топене има индукционна тигелна пещ с меден капацитет до 1 тон, чийто индуктор се захранва от високочестотен преобразувател с мощност 500 kW при напрежение 1500 V и честота 1000 Hz. Водоохлаждаема форма за леене на кръгли слитъци с диаметър 200–400 mm е монтирана на леярския нос на пещта. В долната част на камерата за топене, под формата, има камера за изливане, свързана с камерата за топене чрез специален затвор. В разливната камера има механизъм за повдигане и издърпване на блока от формата. Топилната камера на агрегата е непрекъснато под вакуум, а зареждането и разливането - периодично. Крайният вакуум на камерата за топене в студено състояние 5•10 -4 mm Hg. Изкуство.
За топене на мед с висока чистота се използва катодна мед от най-малко степен M0. Нарязаната мед се зарежда в цилиндрични стоманени контейнери с дъно, запечатано с медна тел. Контейнерите последователно влизат в зареждащата камера на блока, която се вакуумира не по-високо от 0,8 mm Hg. st, след това включете отоплението на контейнера с индукторв рамките на 15 мин. След нагряване на заряда и изравняване на налягането в камерата за топене и зареждане, горната врата се отваря и контейнерът със заряда се спуска в нагрятия тигел на пещта. Медната жица, която държи заряда, се разтопява и зарядът се излива от контейнера в тигела на пещта. Празният контейнер се изважда от уреда през шибъра и товарната камера, а на негово място влиза следващият контейнер със сместа. След като тигелът е поставен, целият метал се разтопява и дегазира под вакуум, получава се разлив. Преди изливане налягането в камерата за изливане трябва да бъде не повече от 0,1 mm Hg. Чл., след достигане на такъв вакуум, затворът се отваря, съобщавайки камерите за топене и изливане. С помощта на повдигащия механизъм се вкарва медно семе във формата, след което тигелът се накланя и формата се напълва с метал, а слитъкът се изтегля от нея чрез повдигащия механизъм.
След края на леенето слитъкът се спуска в леярската камера, която е отделена от камерата за топене с капак, след което готовият слитък се изважда от нея. Тигелът на индукционна пещ може да издържи около 100 нагрявания. Времето за едно загряване е 5 ч. Производителността на агрегата е 4,8 т/ден. Консумация на електроенергия: отопление, топене и рафиниране
1900 kWh/t, за вакуумни камери
340 kW/t. Разход на вода за охлаждане 200 m 3 /t. В момента се изграждат високочестотни индукционни пещи с мощност от 50 до 5000 kW с капацитет на тигела от 50 kg до 20 тона.