Изпит по заваряване - страница 2
Тези флюсове се използват за почистване на повърхността на запоения метал, както и за намаляване на повърхностното напрежение и подобряване на разпространението и омокряемостта на течната спойка.
Флюсът (с изключение на реактивното спояване с флюс) не трябва да взаимодейства химически с припоя. Точката на топене на флюса трябва да е под точката на топене на спойката. Потокът в разтопено и газообразно състояние трябва да допринесе за намокрянето на повърхността на основния метал с разтопен припой. Флюсовете могат да бъдат твърди, пастообразни, течни и газообразни.
Потоците се класифицират въз основа на:
Температурен диапазон на запояване при ниска температура (t4500C); Естеството на разтворителя на воден и неводен;
Естеството на активатора за колофон, халид, флуороборат, анилин, киселина и др.;
По агрегатно състояние на твърди, течни и пастообразни По химически
Най-често срещаните флюсове за запояване са боракс (Na2B4O7) и борна киселина (H3BO3), цинков хлорид (ZnCl2), калиев флуорид (KF) и други соли на алкални метали.
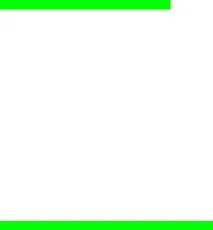
17. Предимства и недостатъци на спойките
Предимства на спойките: възможност за свързване на части не само от хомогенни, но и от различни материали, например стомана с цветни сплави; метали с графит, ферит, порцелан и др.; повишена технологичност, тъй като е възможно да се извърши запояване в скрити или недостъпни места на конструкцията, да се произвеждат сложни възли наведнъж, да се запоява не по контура, а едновременно по цялата повърхност на връзката; като изберете подходящите припои, можете да изберете температурата на запояване, така че при нагряване за запояване предварително топлинно обработените материали да запазят механичните си свойства в продукта (в готовиявръзка) или че нагряването за запояване едновременно осигурява термична обработка на частите на връзката; възможност за запояване на връзката.
Недостатъци: относително ниска якост на срязване на запоената връзка и много ниска якост на отлепване; висока трудоемкост на производството на продукти чрез високотемпературни методи за запояване.
Трябва да се отбележи, че якостта на запоения шев е по-висока (понякога значително) от якостта на спойката поради разтварянето на материала на частите в слоя спойка и поради факта, че слоят спойка е в ограничено напрегнато състояние между частите, които трябва да бъдат съединени.
Чрез запояване се свързват части с различни форми: листове, тръбни пръти и др. Напоследък се използват запоени структури с пчелна пита; в обшивката на самолетите листовете от алуминиеви сплави с ниска якост се заменят със запоени, високоякостни и твърди панели от тънки стоманени листове с пчелна пита или гофриран междинен пълнител.
Запоените съединения за предпочитане са припокрити; зоната на припокриване (областта на запояване) трябва да бъде зададена така, че якостта на запоената връзка да е равна на якостта на цялата част.
18. Техника за изработване на перли при ръчно дъгово заваряване
При преместване на електрода в права линия по протежение на шева без осцилационни движения се заварява тясна (резбова) ролка. При нанасяне на ролката електродът трябва да се държи наклонено, под определен ъгъл спрямо вертикалната линия, така че капките метал, движещи се при разтопяване на края на електрода по посока на оста му, да попаднат в разтопения метал на ваната. Електродът трябва да бъде наклонен към посоката на заваряване. В този случай дълбочината на проникване на основния метал е по-голяма. Ъгълът на наклон a на покрития електрод спрямо вертикалата трябва да бъде 15-20°.
Чрез промяна на наклона на електрода заварчикът може да регулира дълбочинатаразтопяване на метала, допринасят за по-доброто формиране на заваръчния ръб и влияят на скоростта на охлаждане на ваната.
При заваряване на основата на шева, заваряване на тънки листове, заваряване на хоризонтални и таванни шевове (независимо от броя на слоевете) се прилага тесен ръб. Колкото по-бавно заварчикът движи електрода по шева, толкова по-широка е перлата. В тесен, но висок зърно, обемът на отложения метал е малък, такъв зърно се втвърдява по-бързо и неосвободените газове, разтворени в метала, могат да причинят порьозност на заваръчния шев. Поради това по-често се използват разширени ролки, които също са по-малко склонни към образуване на кристализационни пукнатини. Когато ги изпълнява, заварчикът информира електрода за колебателни движения през шева, а краят на електрода трябва да направи три движения (фиг. 65, а): транслационно I по оста на електрода отгоре надолу, транслационно 2 по линията на шева и осцилаторно 3 през шева, перпендикулярно на неговата ос. Осцилаторните движения на електрода допринасят за нагряването на ръбовете и забавят охлаждането на заваръчната вана.
Схеми на движение на края на електрода по време на наваряване на разширени перли са показани на фиг. 65б. В точки 1, 2 и 3 скоростта на движение на електрода намалява, което допринася за нагряването на ръбовете.
Най-добро качество имат ролките с ширина, равна на 2,5-3 диаметъра на електрода. В този случай всички кратери от разтопен метал 1, 2, 3 се сливат в един басейн и се осигурява най-доброто сливане на основния и отложения метал.
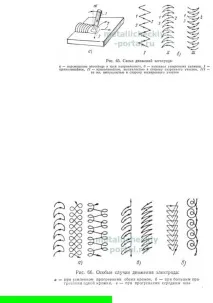
Ако ширината на перлите е твърде голяма, металът в точка 1 ще се втвърди до момента, в който дъгата се върне в точка 3, и на това място може да се образува липса на сливане. В допълнение, производителността на заваряването намалява. На фиг. 66, а показва движенията на края на електрода, необходими за нагряване на двата ръба, на фиг. 66, b - за отопление само на един ръб(например при заваряване на листове с различна дебелина). За да се загрее средата на шева, електродът се премества съгласно схемата, дадена на фиг. 66, c. При заваряване на шев, заварчикът може да бъде отстрани на шева и да движи електрода отляво надясно или да бъде разположен по оста на шева и да води електрода „към“ или „далеч от вас“.
След края на напластяването на зърното, кратерът, останал в края му, трябва да бъде внимателно заварен, така че на това място да не се появи пукнатина.
При заваряване с покрити електроди е необходимо да се осигури пълна и равномерна защита на течния метал чрез слой разтопена шлака. Шлаката трябва да се намира зад дъгата, да не се смесва с разтопения метал и да не тече пред дъгата, т.е. да не пада върху повърхността на неразтопения метал. Металът се поддържа в течно състояние за достатъчно време, така че частиците на шлаката да изплуват на повърхността на ваната и шлаката има време да деоксидира метала.
19. Класификация на контактното заваряване
Класификация на съпротивително заваряване:
Според технологията на изработване на заварено съединение (точково, релефно, шев, челно)
По броя на връзките, произведени едновременно (една или повече връзки)
По вид ток (заваряване с импулсен или променлив ток)
Точковото заваряване се извършва чрез плътно притискане на детайлите един към друг и свързването им в една или повече точки.
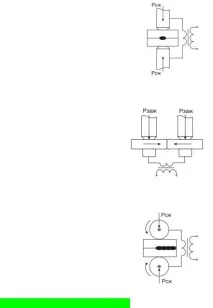
Челно заваряване - съпротивително заваряване, предназначено за свързване на части по цялата повърхност на техния контакт
Шевното заваряване е аналог на точковото заваряване, само в този случай точките на заваряване следват една друга, образувайки един шев.
20. Недостатъци на лепените съединения
Лепенето е технологичен процес за получаване на неразглобяеми съединения.
Лепилните съединения имат следните предимства: позволяватдостатъчно надеждно и здраво за свързване на разнородни материали (пластмаси с метали) с различна дебелина, разнородни метали без образуване на крехки интерметални фази, неизбежно при други методи (заваряване, запояване, използване на нитове и болтове), премахване на необходимостта от пробиване на отвори, изработване на болтове и нитове; процесът на свързване става по-прост и по-евтин, теглото на конструкцията е намалено, ставите имат гладка повърхност, добра плътност и висока циклична якост.
Основният недостатък на повечето лепила е тяхната ниска топлоустойчивост. Разработени са редица лепила на базата на органични, органоелементарни и неорганични полимери, които могат да работят при температури над 1000°C, но повечето от тях не осигуряват достатъчно еластичен адхезивен филм, което все още ограничава тяхното приложение.
Освен това недостатъкът на лепилните съединения е и тяхната относително ниска якост с неравномерно разделяне и необходимостта в много случаи да се произвежда нагряване по време на залепване, необходимостта от използване на сложно оборудване и високо прецизно оборудване, намаляване на якостта на фугите в резултат на стареене на лепилото,
токсичност на някои видове лепила.
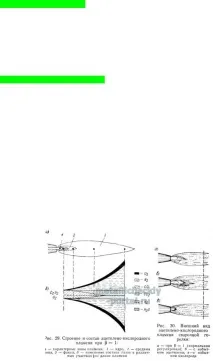
21. Неконсумируеми електроди
Неконсумируемите електроди са един от видовете неметални електроди за заваряване. Използва се главно за заваряване в защитен газ и плазмено заваряване и рязане. Неконсумируемите електроди са волфрамова тел - пръчки. Волфрамът е огнеупорен метал, температурата му на топене достига 4500 °C, така че консумацията му по време на заваряване е незначителна. Използването на волфрамови електроди позволява да се извършва заваряване с аргонова дъга на различни високолегирани стомани и цветни метали без пълнител или с добавъчен материал,като същевременно осигурява добра защита на зоната на заваряване с инертен газ.
22. Състав и свойства на газов пламък
Структурата и съставът на заваръчния пламък
За пламъчна обработка на метали като горими газове се използват главно различни въглеводороди и само в някои случаи водород.
Структурата на пламъка по време на изгаряне на въглеводороди в кислород или във въздух се характеризира с наличието на три зони:
Формата, типът и относителните размери на тези зони зависят от съотношението на кислород (V към) и горим газ (V g) в сместа, т.е. регулиране на пламъка, характеризиращо се с коефициента B
Процесът на горене протича на няколко етапа.
Първият етап - подготовката на горивото за изгаряне - се характеризира с разграждането на въглеводорода в крайната му форма на въглерод и водород.
Реакцията се ускорява в присъствието на кислород, смесен с въглеводород. Реакциите на гниене протичат вътре в ядрото на пламъка.
Вторият етап на горене се характеризира с образуването на CO и H 2 .
По време на горенето елементарните частици въглерод се нажежават и тяхното сияние показва границата на ядрото на пламъка. Ако има достатъчно кислород в горимата смес, вече няма свободно въглеродно ядро отвъд тази граница.
В пламък с излишък на кислород (B> 1,3), във втората зона, в допълнение към CO, H 2 и H, има значителни количества CO 2 и H 2 0 и по-голямо количество свободен кислород. Тази зона на пламъка е по-гореща (има по-висока температура, отколкото при B = 1-1.1) поради
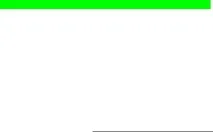
допълнителен топлинен ефект на изгаряне на CO в CO 2 и H 2 в H 2 0 и има по-висока окислителна способност по отношение на нагрятия и разтопен метал.В зависимост от съотношението между кислород и ацетилен се получават три основни вида
заваръчен пламък: нормален, окислителен икарбуризиране. Нормален пламък (фиг. 36.6) теоретично се получава, когато един обем ацетилен влезе в горелката за един обем кислород. Към горелката се подава почти повече кислород
- от 1,1 до 1,3 от обема на ацетилена. Нормалният пламък се характеризира с липсата на свободен кислород и въглерод в неговата редукционна зона. Към горелката се подава малко повече кислород поради ниското му замърсяване и консумацията за изгаряне на водород. При нормален пламък и трите зони са ясно изразени.
Ядрото има рязко изразена форма (близка до формата на цилиндър), плавно заоблена в края, с ярко светеща обвивка. Черупката се състои от нажежени въглеродни частици, които горят във външния слой на черупката. Размерът на ядрото зависи от състава на горивната смес, нейния дебит и скоростта на изтичане. Диаметърът на канала на мундщука на горелката определя диаметъра на ядрото на пламъка, а скоростта на изтичане на газовата смес определя дължината му.
Площта на напречното сечение на канала на мундщука на горелката е право пропорционална на дебелината на заварения метал. Заваръчният пламък не трябва да бъде твърде "мек" или "твърд". Мекият пламък е склонен към откат и пукане, твърдият пламък е в състояние да издуха разтопения метал от заваръчната вана. С увеличаване на налягането на кислорода скоростта на изтичане на горимата смес се увеличава и сърцевината на заваръчния пламък се удължава, с намаляване на скоростта на изтичане ядрото се скъсява. С увеличаване на броя на мундщука, размерът на сърцевината се увеличава. Температурата в сърцевината достига 1000°C.
23. Покрития на електроди, състав и предназначение на компонентите
Дължината на електрода може да варира от 250 до 450, диаметър от 1,6 до 6 mm. Електродът се прави 1) потапяне (разтворът се разрежда и потапя няколко пъти, изважда се, изсушава се и се потапя няколко пъти) 2) измазване Използва се потапянерядко, защото се нанася неравномерно. Изисквания към електрода: 1. осигуряване на стабилна дъга и добро оформяне на шева. 2. нагласям се. Химичният състав на заваръчния метал.3. Спокоен и равномерен разтопен електрод и покритие с минимални загуби. 4. Лесно отделяне на шлаката и достатъчна здравина на покритието. 5. запазване на физ. И хим. Свойства по време на деф. време. 6. Минимален данък. в производството на електроди и работа с тях. Състав на покритието: шлаково спояване
предпазва разтопения метал от излагане на кислород и частично го рафинира. Шлакообразуващите компоненти намаляват скоростта на охлаждане на метала и допринасят за отделянето на неметални включвания от него. Компонентите, образуващи шлака, могат да включват: титанов концентрат, манганова руда, фелдшпат, калий (ваширен мрамор, кварцов пясък). Газообразуващи компоненти: състоят се от дървесно брашно, памучна прежда, целулоза, нишесте, брашно. Дезоксидиращи съставки: необходими за отстраняване на кислорода от стопения метал, те включват елементи, които имат по-голям разтвор на кислород от желязото (например лед, силиций, титан, алуминий). Дезоксидиращите компоненти са необходими в състава на покритието за издаване на метал. Спец. шев Свойствата са: устойчивост на топлина, устойчивост на износване, устойчивост на корозия с повишени метални свойства. Легиращите елементи са манган, хром, титан, ванадий, молибден, никел, волфрам. Въвеждат се и стабилизиращи компоненти (за стабилна дъга), това са тези елементи, които имат нисък йонизационен потенциал (калий, натрий, калций). Свързващи лепилни компоненти: за заваряване заедно в покритието и покритието върху електрода. Като тях се използват калиево или натриево течно стъкло, докстрин, желатин.