Кой и как строи железопътни цистерни
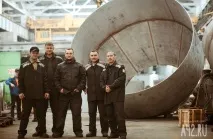
Цистерната е предназначена за превоз на течности: масло, химикали, втечнен газ, вода. Прекомерното налягане вътре в котела може или да отсъства - например, ако се транспортира масло, или да достигне двадесет атмосфери, ако резервоарът е предназначен за втечнен газ. За да издържат на такова натоварване, стените му трябва да са много здрави.
от работилниците на Кузбаската вагоностроителна компания
KVSK заема 22 хектара, площта на промишлените помещения е 30,5 хиляди квадратни метра. Тук се строят гондоли, цистерни, железопътни платформи, оборудване за химическата и въгледобивната промишленост. Сондажни пръти за въглищни миньори, чието производство е наскоро усвоено, са в голямо търсене. Преди това Кузбас трябваше да купува пръчки в САЩ.
Владимир Юргенсон е стругар от пета категория, работи в KVSK от 36 години. Цялото семейство работи в завода: синът работи като стругар, съпругата му работи като складов.
„Сега младите момчета не са свикнали да работят. Всеки иска всичко наведнъж. Колкото ученици имах, останаха двама. Един от тях е синът ми Едуард. Стругарската професия постепенно изчезва. Не защото автоматизацията идва да го замени, не. Имаме няколко такива машини, но къде без човек? Правим големи детайли, сериозни. Те не само трябва да бъдат инсталирани в машината, но и да бъдат управлявани. Като цяло знаем как да работим, ценим труда. Нека и те ни оценят”, казва Владимир.
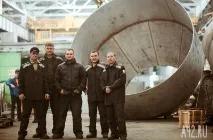
Бригадата на Александър Карманов (вляво). Котелни и заваръчни работи - това е тяхната част
Раждането на резервоар започва на машина за термично рязане. Електрически ток създава електрическа дъга между електрода и металния лист, която превръща газовата струя в плазма с температура 30 000 градуса. Тя избухвадюзи със скорост 150 метра в секунда и е в състояние да реже 10 сантиметра стомана. За производството на резервоари се използва метал с дебелина до три сантиметра - това е достатъчно, за да издържи на налягането на втечнения газ.
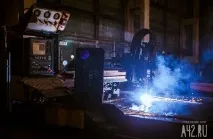
Всички подготвителни работи и монтаж на малки елементи се извършват в цеха за малки агрегати. Тук работи стругар Сергей Малютин, един от най-старите работници на завода. Опит 45 години. Преди три години можеше да се пенсионира, но остана.
„Не искам да си стоя вкъщи. Тъй като обичам работата си, растението израсна пред очите ми. Какво се промени оттогава? Продуктите са станали по-сложни. Бих искал и оборудването да се смени. Не веднага, разбира се, но постепенно“, казва Сергей Малютин.
Заваряването като изкуство
Заготовката на дъното на резервоара е стоманен диск с диаметър около три метра. Придаването му на изпъкнала форма се извършва в магазина за разточване. Преса за щамповане от 500 тона може да направи това за четири часа. Работниците трябва само да заредят детайла, машината ще свърши останалото. Разбира се, под наблюдението на оператора.
Всички неравности след щамповането се отстраняват с фланцова машина. В продължение на около час тя търкаля дъното на резервоара между масивни стоманени ролки, а работниците проверяват резултата с шаблон.
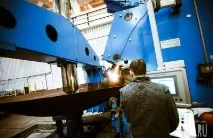
Валцуваната заготовка се изпраща в пещта и остава там за един час при температура от 630 градуса. Нагряването облекчава умората на метала и предотвратява пукнатини“, обясни бригадирът на обекта Иля Манахов.
Още два часа се отделят на нагряване и охлаждане, след което неравните ръбове се изрязват и дъното се подготвя за заваряване с черупката.
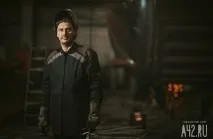
Заварчикът Евгений Прагун: „Заваряването е работа с метал,това е изкуство. И аз го харесвам. Въпреки че имам висше образование, продължавамработа като заварчик
За да построите вагон, трябва да заварявате огромен брой части. Колко дълго ще издържи продуктът зависи от уменията на заварчиците. Във фабриката има специалист, който винаги прави перфектни заварки. Името му е FANUC. Това е робот.
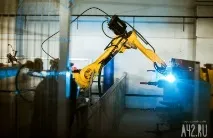
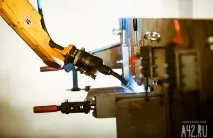
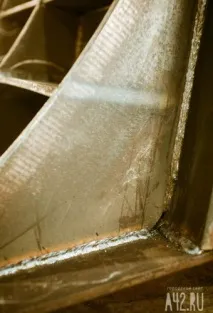
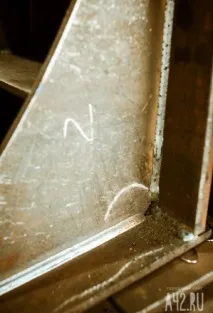
Отляво е дело на човек, отдясно - робот
За да сте сигурни, че резервоарът не изтича, заваръчните шевове се „показват“ в рентгенова камера, изследват се с ултразвук и се тестват чрез изпомпване на вода под високо налягане. И едва тогава работниците пристъпват към окончателното довършване и боядисване.
Художникът Галина Мизина е ударник на труда, наградена е с благодарствени писма от губернатора и ръководството на завода, нейният портрет е на почетния списък.
„Харесвам работата. Притеснявам се за резултата, за плана. Веднага приготвям всичко необходимо, за да не се разсейвам, и работя. Средно за два часа се справям с един вагон. Трябва да можем да правим всичко: да рисуваме и да прилагаме надписи. В крайна сметка от нас зависи как ще изглежда колата“, казва Галина.
Пожарният резервоар е предварително изолиран, така че водата да не замръзва, обвит с листове тънка стомана и едва след това боядисан. И тези контейнери, които се оказват заровени в земята, се залепват с Uniflex - хидроизолационен материал. Нямат нужда от боя.
Автоцистерна се изгражда за един ден, платформа - от един и половина до два. За един месец заводът може да произведе 180 вагона: 90 цистерни и същия брой платформи.