Мартенов процес на скрап руда с използване на твърди окислители
Пълненето се стреми да се извърши за възможно най-кратко време (10 - 15 минути), което обикновено се постига чрез комбиниране на тази операция с освобождаване на стопилката.
Зареждане със твърд заряд. По време на зареждането в пещта се зареждат варовик, желязна руда и метален скрап, необходими за топенето.
По време на процеса на пълнене трябва да се спазват следните правила. На първо място, в пещта трябва да се заредят материали с най-ниска топлопроводимост. От твърдите шихтови материали металният скрап има най-висока топлопроводимост, а варовикът - най-ниска. Варовикът обаче не се зарежда директно върху дъното на пещта, за да се избегне възможно заваряване.
Като се има предвид това, рационалната последователност на зареждане на твърди зарядни материали може да бъде следната. Огнището на пещта е покрито с тънък слой желязна руда или лек метален скрап. Той е зареден с цялото количество варовик, необходимо за топене. След това се зарежда останалото количество желязна руда, леко тегло и след това тежък метален скрап. Неметалните материали се натрупват на слоеве с прекъсвания, за да се нагреят.
Използват се и по-сложни методи за пълнене, при които твърдите зареждащи материали са разположени на дъното на пещта не в еднакви слоеве, а в отделни „лещи“.
Парадично нагряване. Средната температура на металния скрап до края на периода на загряване трябва да бъде 1300 - 1400 ° C.
По време на нагряването на заряда оперативният персонал извършва операциите по добавяне на фалшиви прагове, монтиране на улуци за източване на чугун в пещта, подмяна на шлакови чаши и др.На площадката е монтирана купа за шлака, не се поръсва.
Източването на течния чугунв пещта се извършва в най-кратки срокове.
Топене. По време на периода на топене във ваната на пещта протичат следните процеси:
- разтваряне на метален скрап в течна високовъглеродна стопилка;
- разлагане на варовик;
- разтваряне на железни оксиди и отпадъци от твърди окислители в шлаката;
- окисляване на примеси от метални заряди с кислород от твърди окислители и газовата фаза на пещта с прехода на оксиди към шлака, чието образуване започва по време на изливането на чугун.
Информация за промяната в химичния състав на метала и шлаката по време на периода на топене е представена на фигура 16.1.
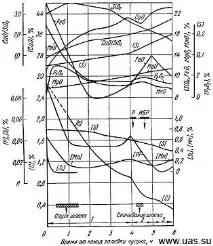
При тежкотоварни пещи 50-60% от общото количество шлака от периода на топене (6-8% от теглото на метала) се изтегля 15-20 минути след изливането на чугуна. От гледна точка на добива на добра стомана, спускането на шлаката е нежелана операция, тъй като добивът на течна стомана се намалява с 1–2%. Но въпреки загубата на желязо, спускането на първичната шлака допринася за увеличаване на производителността на пещта и качеството на метала, тъй като в този случай: топлообменът между факела и метала се подобрява; степента на дефосфоризация и десулфуризация на метала се увеличава; варовик и вар се спестяват, тъй като изхвърлената шлака съдържа 2 пъти по-малко калциев оксид и 1,5 пъти повече силициев диоксид от крайната шлака.
Краят на периода на топене се определя визуално чрез спиране на изтичането на метал в пещта, което показва липсата на твърди материали във ваната. Съдържанието на въглерод в метала в края на периода на топене трябва да бъде по-високо от концентрацията му в края на обработката с 0,3 - 0,5%.
Краят на периода на топене се счита за такова температурно състояние на банята,когато е възможно да се произвеждат добавки от желязна руда в количество най-малко 1% от теглото на метала, т.е. когато прегряването на метала над точката на топене е 50 - 70 ° C. В този случай, в зависимост от съдържанието на въглерод след топенето, температурата на метала, измерена от потапящата термодвойка, е 1520 - 1560 ° C.
В края на периода на топене се вземат проби от метал и шлака за химичен анализ, в зависимост от резултатите от които се определят мерките, които трябва да се предприемат при завършване на стопилката.
Рафиниране на топлината. В началото на периода на довършване металът съдържа излишни количества въглерод, фосфор и сяра. Температурата на метала е с 60 - 100 o C по-ниска от необходимата преди освобождаването на стопилката. Следователно, в довършителния период се решават задачите за отстраняване на излишното количество примеси и загряване на банята.
Ако концентрацията на сяра и фосфор чрез топене е по-висока от необходимата в готовата стомана, периодът на полиране се извършва с подновяване на шлаката от пещта. За да направите това, когато след добавянето на желязна руда и нейното усвояване нивото на метала и шлаката в пещта се повиши, шлаката се изтегля частично през прага на средния прозорец за пълнене в купата за шлака, монтирана под работната платформа. След това, за да се внесе нова шлака в пещта, вар и боксит се добавят заедно с желязна руда.
Основната задачана периода на чисто кипенее загряването на метала до температура, която осигурява нормалното изпълнение на операциите по нарязване и леене.
Предварително деоксидиране и легиране. Предварителното разкисляване и легиране на метал в пещ не са задължителни операции в процеса на топене на стомана по метода скрап-руда.
При топенето на въглеродна стомана може да се извърши предварително деоксидиране, за да се получи точното съдържание на въглерод в метала, както се изисква.преди освобождаването на стопилката. При топенето на легирана стомана предварителното дезоксидиране позволява да се намали окисляването на метала и да се намали загубата на легиращи елементи в резултат на отпадъците.
По време на предварителното дезоксидиране феросилиций се въвежда във ваната, за да се получи остатъчно съдържание на силиций в метала
0,1%, след което ваната спира да кипи. За предварително дезоксидиране е желателно да се използват лоши класове феросилиций, които с висока плътност преминават през слоя шлака към метала. Отпадъците от силиций по време на предварителното дезоксидиране обикновено са 40 - 60%.
Добавянето на легиращи материали към пещта обикновено започва 15-20 минути след предварителното дезоксидиране на банята. Масата на единична добавка от феросплави не трябва да надвишава 1 - 1,5% от масата на метала. Следващото добавяне на феросплави се извършва не по-рано от 20 минути по-късно. Това време е необходимо за разтварянето на феросплавите, осредняването на химическия състав и възстановяването на температурата на ваната.
Освобождаване. По време на разточването в стоманения коф обикновено се въвеждат дезоксиданти и легиращи добавки.
След освобождаването на метала от пещта, шлаката от пещта излиза през изхода за стомана, който, ако не се вземат мерки за отделяне на окислителната шлака от метала, първо влиза в кофата за разливане на стомана, а от нея в купата за шлака, монтирана до кофата.