Метод за пробиване на дълбок отвор в детайла
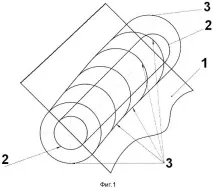
Собственици на патент RU 2421302:
Методът включва пробиване с помощта на балансьор, при което преди началото на процеса на пробиване допълнително се определя неравномерността на твърдостта на материала по сеченията на детайла по геометричната ос на пробиване, за което преди пробиването по цялата дължина на детайла на еднакво разстояние един от друг се измерва твърдостта на материала на детайла в четири диаметрално разположени точки на сечението. След това, въз основа на получените стойности на твърдостта на материала на детайла, се разработва модел за разпределение на механичните свойства на детайла. След това, в съответствие с този модел, се задава монтаж на балансира във всяка от секциите и съответно се поставя върху частите в зоната, където се намира свредлото, след което се извършва пробиване на подходяща дълбочина. В бъдеще, преди всяко следващо пробиване, правилността на монтажа на балансира за дадена секция се проверява и коригира чрез измерване на действително получената дебелина на стената на детайла по пръстеновидната повърхност с намиране на нейните максимални и минимални стойности. ЕФЕКТ: елиминиране на отместването на свредлото спрямо геометричната ос на отвора. 3 ил., 3 табл.
Изобретението се отнася до областта на машиностроенето, а именно до обработката на метали чрез рязане, по-специално до методи за пробиване на дълбок отвор в част по геометричната му ос, докато отворите се считат за дълбоки, ако l/d0> 5, където l е дължината на отвора, а d0 е диаметърът на отвора.
Известен метод за пробиване на дълбоки дупки с малък диаметър, включващ изпълнение на пилотен входен отвор с конвенционална бормашина, последвано от пробиване с едностранна лопатка (вижте например Троицки Н.Д. "Дълбоко пробиване", 1971 г., стр. 142, 143). Въпреки това, ако в детайла на детайла,който трябва да бъде обработен, по протежение на напречното му сечение има неравномерни механични свойства на материала (виж, например, N.F. Utkin et al. Обработка на дълбоки дупки, 1988, стр. 31-33), тогава върху свредлото, което извършва процеса на пробиване, действат неравномерни сили. Например, силата от едната страна на свредлото не е равна на силата върху него от другата, което причинява изместване на оста на пробиване. Следователно, за да върнете свредлото към геометричната ос на пробиване, е необходимо да балансирате тези сили. Известни са мерки за предотвратяване на изтеглянето на надлъжната ос на дупките, особено когато l/d0 е значително по-голямо от 5 (виж, например, Н. Ф. Уткин и др. "Обработка на дълбоки дупки", 1988 г., стр. 3, 31-33, 140-143, 175-177). Предложеното техническо решение е разширение на арсенала от инструменти, които предоставят решение на този проблем.
Техническият резултат от настоящото изобретение се състои в допълване на процеса на пробиване на даден дълбок отвор чрез определяне на причината за въздействието на силите върху свредлото, принуждавайки го да се движи от геометричната ос на пробиване и след това балансиране на тези действащи сили чрез инсталиране на балансьор.
Посоченият технически резултат се постига чрез факта, че процесът на пробиване се извършва с помощта на балансьор, докато преди началото на процеса на пробиване се изследва допълнително неравномерността на механичните свойства на материала по сеченията на детайла по геометричната ос на пробиване, за което преди пробиване по цялата дължина на детайла на същото разстояние един от друг се измерва твърдостта на материала на детайла в четири диаметрално разположени точки на сечението, след което, съгласно получените стойности на твърдостта на материала на детайла се разработва модел за разпределение на механичните свойства на детайла, след което в съответствие с този модел се задавамонтирането на балансира във всяка от секциите и съответно се поставя върху частите в зоната на свредлото, след което се извършва пробиване до подходящата дълбочина и след това, преди всяко следващо пробиване, правилността на монтажа на балансира за тази секция се проверява и коригира чрез измерване на действително получената дебелина на стената на детайла по протежение на пръстеновидната повърхност с намиране на нейните максимални и минимални стойности.
Твърдостта на материала на детайла може да се измери по известни методи, например с помощта на динамичен тестер за твърдост марка 54-359M (вижте например статията на Павлов A.G. и др. „Устройства за безразрушителен контрол, разработени и произведени от SUE „ЦНИИМатериалов“, 2001 г., № 1, стр. 66-67). Имайки стойностите на твърдостта на материала в определен участък в съответствие с предложения метод, допълнително е необходимо да се разработи модел за разпределение на механичните свойства на детайла, което може да се направи с помощта на дискретна, или линейна, или параболична, или някаква друга интерполация, например по метода на най-малките квадрати (виж, например, Glagolev A.A. et al. "Курс по висша математика", 1971, стр. 418-42 0). Последващата настройка на закона за поставяне на балансира, за да се балансират силите, действащи върху свредлото, може да се извърши с помощта на закона за движение на центъра на масата (вижте например Gernet M.M. "Курс по теоретична механика", 1970 г., стр. 290-295, стр. 334-335, стр. 337-339 и др.).
Дължината на разстоянията между точките на измерване на твърдостта на материала се определя от размерите и параметрите на балансира, колкото е по-широк, толкова по-дълъг ще бъде.
Поради наличието на горните основни отличителни характеристики е възможно да се пробие дълбок отвор, като същевременно се минимизира отклонението на свредлото от геометричната ос.
НаФигура 1 показва повърхностното разпределение на стойностите на твърдостта по протежение на оста на пробиване; фигура 2 - равнината на разпределение на максималните и минималните стойности на твърдостта; на фиг. 3 схематично показва процеса на пробиване с различни позиции на балансира в съответствие с разпределението на максималните и минималните стойности на твърдост.
Таблица 1 показва примери за стойности при определяне на твърдостта на материала, таблица 2 - примери за стойности на твърдостта на материалите в една от равнините, таблица 3 - примери за стойности за параметрите на настройка на балансиращата лента.
Разпределението на максималните и минималните стойности на твърдостта, което е показано под формата на равнина (вижте фигура 2), може да има тази форма само в определен конкретен пример, в общия случай може да приеме формата на всяка повърхност, например спирална.
В съответствие с заявения метод, фигури 1, 2, 3 показват, че 1 е равнината на срязване на повърхността на стойностите на твърдостта за най-малките и най-големите стойности, 2 е детайлът, който трябва да се пробие, 3 е повърхността (линията на равнината на срязване) на стойностите на твърдостта, 4 е свредлото и неговото положение, 5 е балансиращата лента и нейното положение.
Ще разгледаме прилагането на предложения метод на етапи, като използваме конкретен пример. Така например, при пробиване на прът, изработен от стомана 12X13-Sh с размер ⌀ 63 × 6000 mm с бормашина 022 mm, в началото на работа се откриват точки с максимални и минимални стойности на твърдост. За да направите това, приблизително в средата на дължината на заготовката 2, перпендикулярна на нейната генераторна, пръстеновидната повърхност се почиства, както се изисква от техниката за измерване на твърдостта, и твърдостта се измерва върху нея на разстояние една от друга, равно на приблизително една десета от обиколката. От получените стойности се избират точки с максимална и минимална твърдост, а след товапрез тях се прекарват линии 3 по образуващите на пръта-заготовка 2. Същите линии 3 се прекарват през точки, разположени в средата на дъгите на окръжност между предварително начертаните линии 3. Това се прави така, че ако положението на максималната и минималната твърдост се промени, това да може да се открие навреме. На разстояние 300 mm една от друга, започвайки от края на детайла 2, се изчертават кръгови линии. В пресечните точки на двете семейства на тези линии повърхността се почиства, както се изисква от техниката за измерване на твърдостта, след което се извършват самите измервания. Да предположим, че техните стойности са представени в таблица 1. От повърхността на разпределение на твърдостта, получена в дискретна форма, в този случай се избира равнината на разпределение на максималните и минималните стойности на твърдост, чиито стойности са представени в таблица 2. Въз основа на данните в таблица 2 се задават параметрите за настройка на балансира 5, например, както са представени в таблица 3.
След извършване на горната работа, процесът на пробиване започва с помощта на свредлото 4. Когато се достигне първият участък, процесът се спира и дебелината на получената стена се измерва на тръбната заготовка 2 по пръстеновидната повърхност с установяване на нейните максимални и минимални стойности. След това се сравняват получените и необходимите резултати, въз основа на които се регулират настройките на позицията на балансира 5. След това пробиването продължава до достигане на втората маркировка с извършените по-горе действия. Тази процедура се извършва до завършване на процеса на пробиване.