Методи за получаване на различни екструдирани продукти
Екструзията може да произвежда голямо разнообразие от продукти. По-долу е дадено описание на характеристиките на процесите за получаване на типични екструдирани продукти.
Екструдиране на пръти и плочи
На пръв поглед може да изглежда, че процесът на екструдиране на пръти от висококачествен полиамид не представлява никакви затруднения. Въпреки това, когато се усвои този процес, беше открита тенденция към образуване на кухини в средната част на екструдата, особено в дебелите участъци. Тези празнини се образуват от свиването на невтвърдената сърцевина на екструдата, заобиколена от вече втвърдена твърда обвивка. Този ефект се дължи на рязък преход от твърдо към разтопено състояние и обратно,
Ориз. 4.8. Инсталация за производство на монолитни пръти от полиамиди.
Както и голямо обемно свиване на полимера по време на втвърдяване. При обработката на повечето други термопласти, кухините могат да бъдат избегнати чрез бавно и контролирано охлаждане на екструдата. Начин за преодоляване на тези трудности при обработката на полиамиди е открит от Stott [9]. В предложения метод, по време на образуването на пръчка върху разтопената сърцевина на екструдата, се създава свръхналягане от страната на стената на формиращата глава, което допринася за частичното уплътняване на материала. Тъй като разтопеният екструдат беше под постоянно налягане, не се образуваха кухини. Количеството обратно налягане по време на удебеляването на закалената обвивка се контролира от скоростта на охлаждане и когато се достигне стабилна работа на оборудването, се установяват равновесни условия. Инсталацията за получаване на монолитни пръти по описания метод е показана на фиг. 4.8 [6].
NV Onderzockinstitut Research [10] получи патент за метод за уплътняване на тънка закалена обвивка под действието наналягане на топене. При този метод, базиран на същия принцип, е обърнато внимание на постепенното охлаждане на екструдата, докато влиза в матрицата.
Когато се използват описаните по-горе методи за получаване на екструдирани продукти без кухини, поради разликата в скоростите на охлаждане в напречното сечение на екструдата, възникват значителни вътрешни напрежения. За продукти, чийто диаметър на напречното сечение надвишава 25 mm, обикновено се използва топлинна обработка -
Продуктът се загрява в масло, последвано от бавно охлаждане. Описаните методи на формоване се използват в промишлеността за производство на пръти с диаметър до 200 mm.
Основната характеристика на екструзионните инсталации, предназначени за производство на тръби, е наличието на глава с пръстеновидна формовъчна част и устройства за точно калибриране на външния и вътрешния диаметър на детайла. Има два основни дизайна на формиращи глави: матрица с директен поток (или аксиална), в която се извършва формоването и калибрирането на екструдата, и матрица под ъгъл, с помощта на която потокът на материала променя посоката на потока с 90 °. След като екструдатът напусне формиращата глава, той се калибрира до зададените размери, след което тръбата влиза в приемното устройство. Двата дизайна на главата, обозначени с *, са показани на фиг. 4.9 [6].
Правите глави са по-благоприятни за получаване на тръби с постоянна дебелина на стената. Техният недостатък обаче е невъзможността да се контролира температурата на дорника или торпедото поради трудностите, свързани с подаването на топлина през държача на дорника. Дизайнът с ъглова глава осигурява лесен достъп до мундщука и елиминира необходимостта от дорник. Загряването и охлаждането на дорника е много лесно. Освен това, в директни главипрекъсването на потока от стопилка от напречния елемент на дорника води до образуване на слаби места под формата на линии за запояване. Линиите на шевовете може да не се виждат, но те съществуват и нарушават структурата на полимера.
В главите и на двата дизайна не трябва да има резки промени в напречните сечения. По правило напречното сечение на каналите в главите постепенно намалява към държача на дорника.
Размерите на напречното сечение на екструдата и изхода на матрицата рядко съвпадат. Крайната форма и размерите на тръбата се определят от размерите не
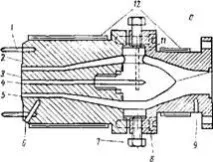
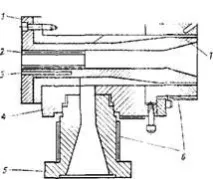
Ориз. 4.9. Конструкции на матрици за екструдиране на тръби:
A - директен поток: 1 - дюзи за калибриране на външния диаметър; 2—мундщук; 3 - дорник; 4 - въздушен канал; 5 - декориращ канал; 6, 9 - ръкави за термодвойки; 7 - центриращи винтове; c - тяло. 10 - торпедо; аз - дор
държач; 12—отопление; b - ъглова: 1 - дорник; 2—нагряване на дорник; 3, “—втулки за термодвойки; 4— тяло; 5 - адаптер; 6, 11 - отопление; 7—мундщук; 9 - дюзи за калибриране на външния диаметър; 10 - центриращи винтове.
Само глави, но и калибриращи дюзи, в които под действието на вакуум (за предпочитане) или сгъстен въздух екструдатът придобива необходимите контури на тръбата. Сгъстен въздух обикновено се използва за постигане на необходимите размери на тръби с малък диаметър. В този случай въздухът се нагнетява през торпедото в екструдираната тръба, предотвратявайки нейната деформация и в същото време осигурява определените размери и дебелина на стената. Вакуумът на външната повърхност на тръбата се създава, когато тя излезе от формиращата глава и влезе в калибриращата дюза. В последния случай се осигурява малка междина между оформящата глава и оразмеряващата дюза, в която се получава известно разтягане на тръбата.
В ходЗа да се калибрират тръбите до определени размери, е необходимо разсейване на топлината, за да се предотвратят последващи промени в размерите. За целта се извършва водно охлаждане в калибровъчното устройство.
За производството на тръби с повишена точност на размерите и във всички случаи на формоване, когато между формиращата глава и оразмеряващата дюза остава въздушна междина, се използват полиамиди с висок вискозитет.
Покриване на проводници и полагане на кабелна изолация
Полиамидите могат да се използват като основен слой при покриване на проводници. Но най-често полиамидно покритие се нанася върху проводник, вече изолиран с друг полимер, като PVC, като вторична изолация, която има повишена абразивна и химическа устойчивост.
Полиамиди с нисък вискозитет се използват за покритие на проводници. В същото време се поддържат много високи температури по време на процеса на екструдиране. Процесът на нанасяне на покритие постига висока
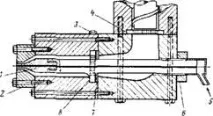
Rns. 4.10. Проектиране на ъглова глава с вакуумна линия за полагане на изолация на проводници:
/ - торпедо; 2 - формираща глава; 3 - vitae, каутеризиращ червей; 4, 8 - опъваща решетка; 5 - вакуумна линия; 6 - фиксираща гайка; 7 - пакет филтърни мрежи.
Степента на изтегляне на екструдата се дължи на високата скорост на екструдиране. Дебелината на изолационния слой се регулира чрез промяна на скоростта на червея.
За полагане на изолация се използват ъглови глави, чийто дизайн е показан на фиг. 4.10 [7]. За постигане на определена дебелина на изолационния слой е необходима междина между дорника и върха на торпедото.
Инсталацията за нанасяне на изолация върху проводници включва, в допълнение към екструдера, охлаждащо устройство, приемно устройство от барабанен тип и устройство за навиване, последователноконструкция, подобна на подобни устройства, използвани при производството на кабелна изолация от полиетилен или PVC. Често се предвижда въвеждането на средства за контрол и измерване в линията за определяне на диаметъра на изолирания кабел.
Екструзионното формоване на филми от полиамиди може да се извърши както чрез ръкав (екструзия, последвана от раздуване), така и чрез плосък метод. За получаване на тръбен филм се използват полиамиди с висок вискозитет (техният вискозитет трябва да бъде приблизително 10-12 пъти по-висок от вискозитета на полиамидите, използвани за нанасяне на кабелна изолация). Температурата във формиращата глава трябва да бъде 5°C над точката на топене на полиамида.
Обикновено производството на тръбен филм включва пълнене на екструдираната втулка със сгъстен въздух през централен отвор в торпедото и равномерно охлаждане на напълнената с въздух втулка от външната страна. Размерите на фолиото - неговата дебелина и ширина - се регулират от налягането на въздуха от вътрешната страна на ръкава и скоростта на навиване на приемното устройство. След охлаждане на надутия ръкав, полученият филм се сгъва в плоска двойна лента, опъва се между изтеглящите ролки и се навива на макари.
Производството на филм по метода с плосък прорез се извършва чрез екструдиране на стопилката през широк прорез на формиращата глава, последвано от охлаждане на екструдата върху повърхността на въртящ се барабан или водна баня. За получаване на тънък филм се използват полиамиди със среден вискозитет. Температурата на формовъчната глава се поддържа на 15-20 °C над точката на топене на обработения полиамид. Поради по-бързото охлаждане, степента на кристалност на филма, произведен чрез процеса на плосък прорез, обикновено е по-ниска от степента на кристалност на тръбния филм, направен от същияполимер.
Напречното сечение на монофила има формата на кръг с много малък диаметър, като диаметърът в края на монофила е 0,1 mm и в началото 1,8 mm.
Инсталацията за производство на монофил се състои от екструдер, устройство за кондициониране на отработените газове и устройство за навиване под формата на бобини. Производството на монофиламент е много подобно на процеса на предене на стопилка на полиамидно влакно. Моновлакнестият екструдер включва зъбна помпа (вместо шнек), пясъчен филтърен пакет с голям брой отвори, разположен преди формиращата глава. След напускане на формиращата глава влакното се екструдира във водна баня с температура на водата приблизително 40 °C. След това влакното преминава през два реда издърпващи ролки (наречени въртящи се колела), които се въртят с различни скорости. Тук нишката се нагрява и изтегля, за да се намали диаметърът и да се увеличи здравината. След изтегляне може да настъпи допълнителна промяна в размерите на монофиламента. За да се елиминира това, конецът преминава през нагрята камера за кондициониране и след това се навива върху бобини. За производството на моновлакна се използват най-ниско вискозните полиамиди.