Особености на използването на благородни феросплави за микролегиране на стомана по време на извън пещта
Кисиленко В.В., Дюдкин Д.А. Украинската асоциация на стоманодобивниците UDC 669.046.558.28
Терминът благородни феросплави (в английската литература noble alloys) обикновено означава ферованадий, феромолибден и ферониобий. Нивото на потребление на ванадий, ниобий и молибден в промишлеността е един от най-важните показатели за техническия прогрес на всяка държава. Добавките на тези елементи имат положителен ефект върху качеството на широка гама от стомани и сплави.
Въвеждането на тези елементи в стоманата позволява да се образува структурно състояние, което подобрява набор от потребителски свойства (смилане на аустенитни зърна, карбонитридно втвърдяване на стомана, неутрализиране на вредното въздействие на азота, разтворен във ферит, и предотвратяване на процесите на стареене на стоманата, увеличаване на вискозитета на метала в комбинация с повишена якост, повишаване на устойчивостта на корозия и др.). Тези елементи се използват за производство на високоякостни нисковъглеродни нисколегирани стомани, предназначени за производство на конструкции в мостостроенето, автомобилостроенето, тръби с голям диаметър за северни газопроводи и за тръбопроводи, работещи в агресивни среди при високи температури, специални конструкционни стомани, корабостроителни стомани, високоякостни релсови стомани и др. Използването на стомани, легирани с тези елементи, намалява теглото на продуктите с 30-50% и увеличава експлоатационния им живот с един и половина до два пъти.
В металургичната промишленост се използват благородни феросплави за легиране на стомана с тези елементи - ферованадий, ферониобий и феромолибден.
особеностИзползването на благородни феросплави от тези класове при легиране на стомана е тяхната висока точка на топене (за FeV80 - повече от 1650 o C, за FeMo60-70 - повече от 1800 o C, за FeNb60-65 - около 1587-1600 o C), следователно, тези материали в течен метал са предимно разтворени.
Когато се използват тези материали за регулиране на съдържанието на V, Nb и Mo в еднократна форма по време на обработка извън пещта, парчета феросплави преминават през слоя шлака в металната стопилка, след което се придвижват по-нататък и едновременно с това се разтварят, пренос на маса (усредняване) на разтворената добавка в обема на ваната на кофата. В същото време върху повърхността на детайла се образува шлакова обвивка в резултат на преминаването му през слоя шлака върху повърхността на стопилката в стоманоразливния коф, а пространствената траектория на движение на детайла под влияние на хидродинамиката на стопилката (включително поради дънно продухване с диспергиран аргон), в зависимост от размера на парчетата, може да приеме различни форми - вкл. движение към горната част на кофата [2, 3].
Проведените изследвания показват значителен ефект върху продължителността на разтваряне (топене) на бучките добавки на гранулометричния състав на последните. По този начин продължителността на разтваряне (топене) се увеличава с коефициент 10–20 с увеличаване на размера на парчетата от 5 до 50 mm (в диаметър), независимо от вида на добавката (включително за тежки феросплави) и консумацията на диспергиран аргон в изследваните граници. Непрактично е (поради значително увеличаване на продължителността на разтваряне или топене) всички разглеждани феросплави да се използват на парчета с фракция над 50 mm. Също така е икономически и технологично нецелесъобразно тези феросплави да се използват на парчета от фракции от 0–5 mm (което може да допринесе за отстраняването им в шлака или заплитане на отделнипарчета в шлаката при преминаване през слоя шлака по време на добавянето).
Трябва също да се отбележи, че гранулометричният състав на еднократната добавка влияе върху продължителността на нейното осредняване - увеличаването на фракцията на парчета от 5 до 50 mm (в диаметър) удължава този период на асимилация с 1,5–3,0 пъти.
В допълнение, асимилацията се влияе и от масовата скорост на навлизане на водещия елемент във ваната с кофа - при известен излишък в зоната на локално взаимодействие елементът просто няма да има време да се разтвори и да бъде пренесен в шлаката чрез възходящи метални потоци.
Всичко това създава някои трудности при легиране на стомана с посочените феросплави в бучна форма.
Както показва практиката на много металургични предприятия, при легиране на стомана нивото на асимилация на водещите елементи от бучки благородни феросплави е доста високо (ванадий - 80-85%, ниобий - 85-90, молибден - 90-95%), но поради горните причини е нестабилно. Например, в едно от предприятията средната асимилация на молибден по групи марки стомана е 83,3–100% (в технологичните инструкции асимилацията на молибден се приема за 97%). В същото време в 24% от случаите асимилацията е под 90%, а в 52% - под 95%. Липсата на стабилни показатели за асимилация води до увеличен разход на скъп материал и съответно увеличени разходи за легиране на стомана.
Средната степен на асимилация на ванадий при използване на бучки в различни предприятия е 80–88% (минимумът е 65–75%). Когато стоманата е легирана с бучки ферованадий, разпространението на стойностите на съдържанието на V в готовата стомана (за различни степени на стомана) е 0,010–0,020% абс. (30–70 % отн.), е необходима допълнителна корекция на съдържанието на V в стоманата за отделни нагрявания.
Както вече беше отбелязано, нестабилна асимилацияна тези елементи от бучки феросплави най-често се свързва с точността на дозиране на бучките материали, скоростта на разтваряне или топене на парчета с различни размери в стопилката, заплитане на отделни парчета в шлаката (например с допълнителна настройка на блока кофа-пещ) и др. В условията на страните от ОНД много важен фактор за нестабилното усвояване на тези материали е и използването на скъпи феросплави не по предназначение.
За да се повиши стабилността на процеса на микролегиране и да се елиминират горните фактори, позволява прецизна обработка на стопилката - използването на тел с флюсова сърцевина, напълнена с посочените феросплави.
Въвеждането на технологията за въвеждане на тези феросплави с флюсова сърцевина позволява да се стабилизира асимилацията на елементите на високо ниво (97–100%), което се потвърждава от резултатите от тестването на тази технология в някои предприятия. Въпреки сравнително малката разлика в асимилацията в сравнение с добавката на бучки материали, въвеждането на ферованадий и феромолибден под формата на флюсова тел е икономически осъществимо, което се обяснява с високата цена на тези материали (цената на телта, като правило, е значително по-ниска от цената на бучките) и високия коефициент на запълване на телта с прах (повече от 72 тегл.% за FeV80, 77–80 тегл. % за FeNb60–65 и 79–83 тегл. % за FeMo60–70). При използване на тел се осигурява стабилност на дозировката на феросплави, става възможно да се гарантира определеното съдържание на тези елементи в стоманата на долната граница на регулаторните изисквания (0,002–0,003% по-малко в сравнение с еднократния материал), което води до намаляване на потреблението на феросплави (намаляване на разходните норми на материалите), елиминиране на утаяването по отношение на съдържанието на елементи и, съответно,намаляване на технологичните и експлоатационни разходи за допълнителна настройка и като цяло цената на производството на стомана, докато операциите по претегляне на материала са изключени, а операцията по въвеждане на феросплави в метала е механизирана [4–7].
Освен това се изключва възможността за използване на скъпи феросплави за други цели.
Тук трябва да се отбележи, че за да се получат горните показатели при извънпещна обработка на стомана с флюсови телове, трябва да бъдат изпълнени редица условия:
При спазване на условията за използване икономическата ефективност от използването на прецизна обработка с флюсови телове с посочените феросплави в различни предприятия е 0,5–1,5 долара. US/t стомана.
Трябва да се отбележи, че за висококачествено запълване на жицата с тези материали трябва да се извърши специална подготовка на праха. Така че, за феросплави със същия химичен състав (и съответно специфично тегло), обемната плътност на праха, в зависимост от размера и формата на частиците, може да варира с 20–30%, докато коефициентът на уплътняване по време на валцуване, който показва възможността за уплътняване на прахове от различни материали на определена линия за производство на тел с флюсова сърцевина, за такива материали (фракционен състав от 0–2 mm) също ще варира значително - от 2–3 пъти. Например за тел с диаметър 13 mm номиналното пълнене на телта от различни производители варира в следните граници: FeV80 - 400-460 g/m, FeNb60-65 - 600-680 g/m, FeMo60-70 - 620-750 g/m.
На сегашния етап на развитие много металургични предприятия отчитат всички предимства от използването на флюсова тел и затова например в България има доста високо ниво на потребление на флюсова тел, напълнена с благородни метали.феросплави - през 2010 г. количеството на използвания ферониобий под формата на флюсова тел възлиза на 64,8% от общото количество ферониобий, количеството на тел, напълнено с ферованадий (по отношение на 100% съдържание на ванадий), възлиза на 41,3% от общото количество използван ферованадий, тел с феромолибден - 31,1%.
Спорова тел с благородни феросплави през 2010 г. е произведена от 10 предприятия в България, като 92,1% от телта с ферониобий и 79,1% от телта с феромолибден са произведени от три предприятия - ОАО Северстал-Метиз (Череповец), ОАО ММК-Метиз (Магнитогорск) и ЗАО Фергосплавск (Челябинск) (Челябин). ск) (Челябинск) (Челябинск) (Челябинск) . 42,5% от телта, напълнена с ферованадий, е произведена в ZJSC Vanadium-Tula (Тула) (Таблици 1, 2).
Таблица 1- Потребление на флюсова тел с напълване с благородни феросплави в България през 2010 г., тона (при 100% съдържание на основния елемент)
Забележки.1. Всички предприятия в България произвеждаха тел предимно с диаметър 14-15 mm. 2. Българските производители през 2010 г. са изнесли 128,02 т тел с ферованадий, 25,13 т тел с ферониобий и 21,46 т тел с феромолибден (при 100% съдържание на основния елемент).
Таблица 2- Потребление на ферованадий на парчета и под формата на флюсова тел (FC) в металургичните предприятия в България през 2010 г., тонове (при 100% съдържание на V)
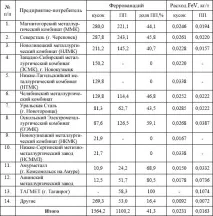
В Украйна през 2010 г. основното количество благородни феросплави (FeV80 и FeNb60-65) под формата на тел е използвано в железодобивния комбинат Азовстал - до 100 тона на месец (при 100% съдържание на основния елемент). Основният производител на тел с пълнеж от благородни феросплави в Украйна през 2010 г. е PE"Daryal", през 2011 г. телта с ферониобий започна да се произвежда в KhMF MK им. Илич, а тел с ферованадий и феромолибден беше доставена в Украйна от Plus Trade AG, швейцарска компания с украински корени.
Много металургични предприятия в България разбират, че в настоящите икономически условия използването на флюсова тел (не само с пълнеж от нискотонажни феросплави, но и с калций-съдържащи, въглерод-съдържащи и други пълнители) при извънпещна металообработка създава възможности за решаване на проблемите за осигуряване на необходимото качество на метала, разширяване на гамата и конкурентоспособността на произвежданите продукти без значителни капиталови разходи.
Според прогнозите производството на стомана през следващите години ще се увеличи с 15-16%, цената на благородните феросплави също ще се увеличи с около 15-20%, в т.ч. под формата на тел.
По този начин използването на благородни феросплави под формата на тел с флюсова сърцевина позволява значително да се повиши ефективността на използването на въведените елементи, да се намалят разходите за обработка извън пещта, като същевременно се гарантира определеното качество на готовия метал.