Подготовка и монтаж на детайли за заваряване
Точността на подготовката на частите за заваряване, тяхната чистота и качество на сглобяване оказват значително влияние върху носещата способност и икономичността на заварената конструкция. Недостатъчно внимателното изпълнение на операциите по доставка и монтаж води до рязко увеличаване на вероятността от дефекти в заварените съединения и в конструкцията като цяло. Анализът на дефектите, възникнали по време на заваряване, ясно показва, че значителна част от дефектите трябва да се отдаде на лошото качество на подготовката и монтажа. Коригирането на брака в готовия продукт не винаги води до пълно възстановяване на зададените свойства на заваръчното съединение и е трудоемка и технически трудна операция.
От това е очевидно, че е много по-рационално да се отстранят дефектите, възникнали по време на детайла и монтажа, преди заваръчната операция. Не трябва обаче да се налагат прекомерни и понякога трудни изисквания към точността на детайлите и тяхното сглобяване за заваряване, което значително увеличава разходите за производство на конструкцията. Методите за заваряване, използвани в практиката, позволяват да се получат висококачествени заварени съединения с някои допустими колебания в точността на детайла и монтажа. Възможно е, определено трябва да се използва.
За да се получи заготовка за сглобяване, е необходимо да се извършат редица операции. Предварително валцованият метал, от който ще бъде изработен детайлът, се подлага на изправяне и почистване, за да се елиминират замърсяванията и неравностите, образувани по време на валцуването, транспортирането и съхранението на метала. Редактирането на листовия материал се извършва в мелници за изправяне, оголване - в инсталация за бластиране или в специални вани за декапиране и пасивиране.
След това извършват маркиране или маркиране на части: маркиране - чрез прехвърляне на размерите на детайла от чертежа директно върху метала, щанцованеметал по линията на бъдещия разрез и маркиране на части; лепене - чрез прехвърляне върху метала на размерите, необходими за производството на детайла от шаблон, специално изработен от тънък метален лист, шперплат или картон. Контурите на шаблона се очертават с нож, след което се отстранява, нанасят се сърцевини по цялата линия на изрязване и детайлът се маркира. Рязането на заготовки се извършва на ножици, автоматични пламъчни машини или ръчни фрези. Напоследък започна да се използва рязане с компресирана дъга.
В някои случаи, за да се премахне втвърденият метал, образуван по ръбовете при рязане с ножица, за да се елиминират нередностите, характерни за ръчното рязане с газ, ръбовете се обработват на машини за рязане на ръбове. При необходимост се използва студено огъване на метал или огъване в нагрято състояние. Изборът на един или друг метод се определя от дебелината на метала и радиуса на кривината на грапавостта.
В зависимост от дебелината на заварявания метал и формата на среза, ръбовете се подготвят чрез подрязване с ножица, рендосване или газово рязане. Най-голямо приложение намира механизираното (машинно) кислородно рязане, което осигурява висока производителност и в повечето случаи достатъчна точност при подготовката на ръбовете. Не се изисква последваща механична обработка с висококачествен разрез за стомани от повечето класове. Необходимата точност на подготовката на ръба се определя от вида на шева, метода и начина на заваряване. Отклоненията от посочените размери могат да доведат до намаляване на качеството на шева или увеличаване на сложността на работата.
Преди сглобяването основният метал в местата на заваряване трябва да бъде почистен от ръжда, масло, влага, хлабав слой котлен камък и други замърсители, които могат да доведат до образуване на пори и други дефекти в шевовете. Особено внимание трябва да се обърне на почистването на металас механизирани методи за заваряване. На фиг. 5-17 показват местата, които трябва да бъдат почистени преди дъгова заварка за различни видове съединения. Особено внимателно трябва да се почистят краищата на съединяваните елементи.
Почистването се извършва преди сглобяването на модула механично (чрез пясъкоструене или бластиране, метални четки, абразив) или химически (ецване, пламъчно почистване). От металната повърхност трябва да се отстрани свободен слой ръжда и котлен камък, както и мръсотия и лед, дори ако замърсяването е извън зоната на заваряване. Това е необходимо, така че по време на транспортиране и накланяне на конструкцията замърсяването да не попадне в мястото на бъдещия шев. Почистването на сглобената единица в повечето случаи е неефективно, тъй като не се постига основната цел - почистване на ръбовете, които ще бъдат заварени, а понякога дори вредно поради факта, че продуктите
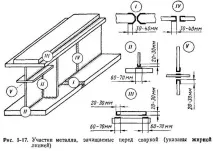
оголването, попадайки в пролуката (особено след заваряване на първия шев на тройника), се забавят там.
Има смисъл само да изгорите мястото на заваряване с газов пламък или да го продухате със сух сгъстен въздух непосредствено преди заваряване. В същото време влагата и мръсотията, които са попаднали в празнината след монтажа, се отстраняват. Тази операция постига целта си при изгаряне на метал с дебелина 10-12 мм от едната страна и 18-20 мм от двете страни. При електрошлаковото заваряване в повечето случаи не се изисква почистване на ръбовете.
Заваряването винаги се предшества от монтажа на конструкцията, т.е. монтажа и фиксирането на частите в позицията, предвидена от проекта. Сглобяването за заваряване е една от трудоемките и най-малко механизирани операции. Тя трябва да осигури възможност за висококачествено заваряване на конструкцията. За да направите това, е необходимо да поддържате определена празнина между частите, които трябва да се свържат, да инсталирате частите в проектното положение и да ги фиксирате заедно, така четака че взаимното разположение на частите да не се нарушава по време на заваряване и накланяне и, ако е необходимо, по време на транспортиране. Трябва да се осигури свободен достъп до мястото на заваряване. При електрошлаковото заваряване частите обикновено се сглобяват с междина, разширяваща се към края на заваръчния шев, което прави възможно компенсирането на свиването на заваръчния метал.
В по-голямата част от случаите относителното положение на частите преди електродъгово заваряване се фиксира с помощта на къси сегменти от шевове, наречени прихващания (фиг. 5-18, а). напречно сечение
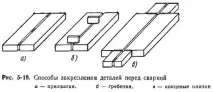
прихващанията не трябва да надвишават V3 на заваръчната секция. Максималното им сечение е не повече от 25-30 mm2, дължина 20-120 mm, разстояние между тях 300-800 mm. Прихващанията се правят с покрити електроди, в защитни газове или потопени. В някои случаи, особено при заваряване на твърди възли, прихващанията се заменят с непрекъсната заварка на малък участък (заваръчен шев), което значително повишава устойчивостта на заваръчния метал срещу кристализационни пукнатини и намалява вероятността от нарушаване на определеното относително положение на частите по време на заваряване поради напукване на заваръчните шевове.
Захващанията и плавният шев се препоръчват да се извършват от страната, противоположна на нанасянето на първия работен шев или слой. Бягащият шев, в допълнение към закрепващите части, служи за задържане на флюса и метала на заваръчната вана в пролуката. При заваряване на критични конструкции ръчно или в защитни газове в режими, които осигуряват малка дълбочина на проникване на основния метал, при нанасяне на работен шев трябва да се отстранят прихващанията и изтичащият шев чрез изчистване на корена на шева. При заваряване под флюс и в защитни газове в режими, които осигуряват достатъчно проникване на основния метал, тази операция не е необходима.
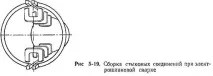
За закрепване на части преди заваряване и в процеса, специалнолентите с гребен се отстраняват при оформянето на шева (фиг. 5-18.6). Недостатъците на гребените са цената на метала за тяхното производство и необходимостта от заваряване и последващо почистване на остатъците от лепенки, разположени върху основния метал.
Скоби, клинове, затягащи ъгли и други механични устройства се използват широко за закрепване на части. В някои случаи при масовото производство се използват специални проводници, в които се извършва монтаж и заваряване.
В краищата на частта обикновено се монтират специални ленти, за да изведат началото и края на шева извън неговите граници (фиг. 5-18, c). Тези ленти служат и за закрепване на части. При заваряване със задължителна междина в горната част на междината се вкарват къси дистанционни елементи, които се свързват към листовете с помощта на щифтове. При електрошлаково заваряване се използват скоби за фиксиране на части (фиг. 5-19), монтирани на разстояние 500-1000 mm една от друга. Понякога се използват вложки, които се отстраняват, когато заваръчната машина се приближи. За да се изведе началото на шева от фугата по време на електрошлаковия процес, се използват извеждащи ленти, които имат същата дебелина като основния метал. Те също така служат като елемент, който държи частите заедно.