ПРОИЗВОДСТВО НА ПЛОСКО ЗАКАЛЕНО СТЪКЛО
Технологичният процес за производство на плоско закалено стъкло се състои от няколко етапа: подготовка на стъклото, нагряване до температурата на темпериране, рязко и равномерно охлаждане и контрол на качеството на получените продукти.
Подготовка на стъкло. За производството на плоско закалено стъкло от различни профили, използвани в автомобилния транспорт, от избрани листове стъкло, по определени шаблони, се изрязват формати, които отговарят по размери на рамите на автомобила. Закаленото стъкло трябва да е без ивици, шлиери, камъни, големи мехурчета и драскотини. Тези дефекти водят до напукване на стъклото по време на темперирането, тъй като на мястото на дефекта се образуват напрежения, които рязко се различават от напреженията в други части на стъклото.
Ръбовете на изрязаните формати се обработват на фасетни машини или шайби. Всички операции по механична обработка на стъкло (рязане, пробиване на отвори, обработка на ръбове) трябва да се извършват преди етапа на топлинна обработка, тъй като най-малкото увреждане на повърхностите или ръбовете на закаленото стъкло причинява неговото унищожаване. По изключение, малки повърхностни несъвършенства (деформация при затягане) в закалено стъкло могат да бъдат изравнени чрез леко завъртане на ръбовете на продукта, но не трябва да се използват груби абразиви и ударни натоварвания. Трябва да се помни, че след обработката величината на остатъчните напрежения в стъклото намалява пропорционално на квадрата на съотношението на дебелината на листа след смилане до първоначалната му дебелина, т.е. силата на закаленото стъкло намалява.
Нагряването е най-важната операция в производството на закалено стъкло и процесът на нагряване до температурата на закаляване трябва да протича при условия, които осигуряват равномерност.нагряване на повърхностите му. Температурата на закаляване зависи от химичния състав на стъклото и винаги е малко по-висока от температурата на встъкляване Td. Трябва да се помни, че температурата на темпериране на стъкла с еднакъв химичен състав също зависи от скоростта на охлаждане и може да се определи като температура, над която не се наблюдава повишаване на степента на темпериране при избрания режим на охлаждане. Закаляването на стъклата, нагряти до температура, която не достига оптималната стойност, води до намаляване на степента на втвърдяване и след това до спонтанно разрушаване на стъклото по време на охлаждане.
Установено е, че температурата и продължителността на нагряване на стъклото са взаимосвързани. Колкото по-висока е температурата на нагряване на стъклото, толкова по-кратко трябва да бъде, при равни други условия. Така например листовото стъкло с вертикално изтегляне във фабричната практика се темперира при температура 610-650 ° C. Продължителността на нагряване на стъкло с дебелина 6 mm в този случай е от 3 min 40 s до 5 min, или, както се практикува, на 1 mm дебелина на листа е в диапазона 36-50 s. По този начин изчисляването на времето за нагряване в зависимост от дебелината на стъклото се основава на факта, че за даден състав на стъклото, в определени граници, времето за нагряване в пещта е право пропорционално на неговата дебелина.
Висококачествено закалено стъкло може да се получи само ако продуктът, който се темперира, е равномерно нагрят. За тази цел е най-добре да се използват електросъпротивителни пещи, в които при нагряване на стъклото не се образуват продукти на горене и които лесно се поддават на автоматично регулиране на температурата.
При производството на плоско листово закалено или полузакалено стъкло, темпериранеинсталации от вертикален тип слот, състоящи се от непрекъсната електросъпротивителна пещ с мощност до 90 kW, захранвана от трифазна токова мрежа, и устройство за издухване (фиг. 17.1).
Нагревателните елементи на такава пещ са нихромови спирали с дебелина 3-4 mm. Нагревателите са разположени в огнеупорната облицовка на пещта от двете страни
Ориз. 17.1. Технологична схема за производство на плоско закалено стъкло
/ - товарна маса; 2 - машина за рязане на къдрави заготовки; 3 - машина за обработка на ръбове на стъкло; 4 - пералня и сушилня; 5 - стъклена заготовка; 6 - скоби; 7 - нагревателна електрическа пещ; 8 ■—въздушна решетка; 9 - устройство за контрол на закалено стъкло; 10 - транспортна количка
От стъклото, което се обработва, така че двете страни на листа да са изложени на еднаква равномерна топлина. Пещта има автоматичен контрол на включване и изключване и може да работи в два режима: нормален (70 kW) и форсиран (90 kW). Възможността за форсиране на режима на отопление позволява да се засили отоплението на пещта. Размерите на работното пространство на пещта (2000X800X300 mm) са предназначени за нагряване на лист с максимален размер (1300X700 mm).
След предварителна обработка и измиване, стъклото, предназначено за темпериране, се окачва вертикално над ръба с помощта на скоби в специални колички, които се изпращат в пещта за нагряване по релсите на окачването. Количките могат да се движат ръчно или механично.
Плоското листово стъкло се закалява при 650°C, докато пещта е в форсиран режим. Времето на престой на стъклото в пещта зависи от дебелината на листа (например за стъкло с дебелина 5,5 mm е 3 min 20 s). Увеличаването на дебелината на стъклото с 0,1 mm води до увеличаване навреме на престой с 4 s. Следователно, за лист с дебелина 6,5 мм, времето на задържане достига 4 минути.
Въвеждането на студено стъкло в пещта води до рязко понижаване на температурата му в началния момент. По време на задържането на стъклото температурата в пещта има време да се повиши до първоначалната стойност (650°C). При тази температура стъклото се изважда от пещта и се придвижва по надземни релси към решетката за издухване. Установено е, че стъклото може да се извади от пещта при по-ниска температура, но не по-ниска от 620 °C, за да се избегне разрушаването на стъклото в решетката за издухване.
Охлаждането на стъклото е вторият по важност процес в производството на закалено стъкло след интензивния
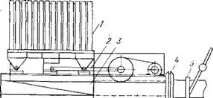
Ориз. 17.2. Секционна решетка за издухване за закаляване на плоско стъкло 1 — решетка за издухване; 2 - ексцентричен механизъм; 3—подвижен канал; 4 - диафрагма; 5 - прехвърлящ клапан
Степента на охлаждане на стъклото в крайна сметка определя степента на темпериране. Режимът на охлаждане е избран по такъв начин, че скоростта на охлаждане на стъклото, неговата дебелина и химичен състав определят степента на втвърдяване на продуктите.
Стъклото може да се охлажда с помощта на различни охлаждащи среди, които осигуряват бързо отвеждане на топлината - въздух, масла, органосилициеви течности, разтопени соли и метали. Най-широко разпространените методи за закаляване на стъклото с въздух, като най-разпространен е въздушно-струйният метод на закаляване. При този метод множество перпендикулярно насочени въздушни струи се подават симетрично под налягане към повърхността на втвърдения продукт. Методът на въздушно-струйно втвърдяване се извършва с помощта на решетки за издухване, които подават сгъстен въздух през голям брой отвори - дюзи с малък диаметър, подредени в шахматна дъска.
Решетката на вентилатора (фиг. 17.2) се състои от два реда кухи секции, в които, както беше отбелязано по-горе, се инжектира сгъстен въздух. Всеки участък има отвори с диаметър около 5 mm, разположени на стъпки от 50 mm. С помощта на ексцентричен механизъм обдухващата решетка извършва възвратно-постъпателни движения в хоризонтална посока на разстояние до 40 mm, което осигурява равномерно охлаждане на стъклото.
Налягането на въздуха в решетката за издухване зависи от необходимата степен на втвърдяване и дебелината на закалената част. При производството на автомобилно стъкло с дебелина 5,5–6,5 mm в решетката за издухване се поддържа налягане от около (53,2–59,85) 102 Pa. За подаване на въздух към надувната решетка се използват турбодувки с производителност 150 m3/min. Времето за преместване на стъкло от електрическата пещ до решетката за издухване трябва да бъде минимално и не повече от 3 минути.
В чуждестранната практика за производство на плоско закалено стъкло се използват решетки, които извършват въртеливо движение във вертикална равнина, като всяка струя въздух прави пълен кръг.
При опаковане готовото закалено стъкло се покрива по цялата повърхност с мека опаковъчна хартия, която не съдържа надраскващи примеси. След това пет-шест продукта се поставят в пакет, който се увива в същата хартия и се поставя в здрава дървена кутия. Пространството между продуктите и стените на кутията се запълва със сух опаковъчен материал (чипс, сено, слама). Опакованите продукти се съхраняват на закрито.
Контрол на качеството. Устойчивостта на удар на закалено стъкло се определя с помощта на метална топка. При дебелина на продукта над 5 mm, закаленото стъкло трябва да издържи, без да се счупи, удара на свободно падаща стоманена топка с тегло 800 g от височина 1200мм, а при дебелина до 5 мм - от височина 800 мм. При унищожаване продуктите трябва да се натрошат на парчета с размер не по-голям от 32 mm.
Степента на закалено стъкло се определя в зависимост от наличието на различни дефекти в него. Външни дефекти (мушици, мехури, ивици и др.) се откриват чрез проверка с невъоръжено око в пропускаща светлина, като продуктите се поставят на разстояние 0,6 m от окото на наблюдателя при нормални условия на дневна светлина. Размерите на дефектите се определят с конвенционален измервателен уред.
Дебелината на продуктите се проверява с микрометър в четири точки. Степента на деформация на стъклото, т.е. тяхната кривина, се проверява, както следва: такова стъкло се поставя върху проверена хоризонтална равнина и стрелката на отклонение се измерва със сонда.
Продуктът трябва да е безцветен. Допускат се леко зеленикави или леко синкави нюанси. Пропускането на светлина по отношение на 1 cm от дебелината на продукта трябва да бъде най-малко 84%.
Прогресивен метод за производство на плоско закалено стъкло, който елиминира недостатъците на вертикалния метод (наличието на такива специфични дефекти, които се появяват в точките на закрепване, като укрепване и кривина на стъклото), е закаляването на стъкло върху твърди опори (фиг. 17.3). При този метод за производство на закалено стъкло, предварително обработените листове се движат хоризонтално по протежение на ролков конвейер от азбестови шахти вътре в електрическа пещ, където се нагряват асиметрично по-интензивно отгоре, отколкото отдолу. При това нагряване стъклото се огъва с издутина нагоре, така че основната повърхност на листовете не докосва конвейерните ролки. В охладителното устройство стъклените листове отново придобиват плоска форма поради по-интензивното охлаждане отгоре.