Схема на работа на безкомпресорен газлифт
При газлифт без компресор се използва енергията на газ под високо налягане, идващ от газови находища. Използването на газлифт без компресор е рационално при наличие на газови находища в близост до нефтени находища или при производство на газ под високо налягане в самите нефтени находища.
След като течността се издигне, газът има много по-ниско налягане, наситен е с течни пари, така че използването му е донякъде ограничено. В същото време безкомпресорната газова лифтова схема позволява издигането на течност от кладенци по най-простия метод без големи капиталови инвестиции и без сложни компресори и компресорни станции. Следователно този метод е намерил приложение в някои нефтени находища.
Нафиг. 4.16 показва блок-схемата на некомпресорния газлифт, използван в асоциацията Краснодарнефтегаз.
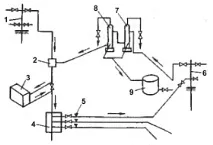
Газът от кладенци 1 под високо налягане (15,20 MPa) постъпва в пречиствателната станция (сушене 2), където преминава през хидроциклони сепаратори и кондензни колектори. След точката на пречистване газът навлиза в безпламъчния нагревател 3 за нагряване до 80,90 ° C и след това в газоразпределителната батерия 4. Газовото нагряване е ефективно средство за борба с образуването на хидрати по време на транспортиране и намаляване на газа. От батерията газът се насочва през регулиращите фитинги 5 към производствените нефтени кладенци 6. След повдигане на течността газът навлиза в газовите сепаратори на първия 7 и втория 8 етап, откъдето се изпраща към горивопроводите и към завода за газ и бензин. Течността от газовите сепаратори се изпраща в контейнер 9.
Сондажните платформи са предназначени за пробиване на производствени и дълбоки проучвателни кладенци по ротационен начин. Сондажната платформа е комплекс от пробивни машини,механизми и съоръжения, монтирани на сондажния пункт и осигуряващи с помощта на сондажен инструмент самостоятелно извършване на технологични операции. Съвременните сондажни платформи са разделени на следните компоненти:
- сондажно оборудване (ходов механизъм, помпи, лебедка, вирбел, ротор, задвижване, инсталация за гориво и масло, дизел-електрически станции, пневматична система);
- сондажни конструкции (платформа, фундаменти, сгъваеми рамково-панелни укрития);
- оборудване за механизиране на трудоемки работи (регулатор на подаването на битове, механизми за автоматизиране на операциите по изключване, пневматичен клинов захват за тръби, автоматична сондажна клеща, спомагателна лебедка, пневматичен разпръсквач, кранове за ремонтни работи, пулт за управление на сондажния процес, контролни станции);
- оборудване за приготвяне, пречистване и регенериране на миещия разтвор (приготвителен блок, вибрационни сита, сепаратори за пясък и глина, бустерни помпи, контейнери за химикали, вода и миещ разтвор);
- колектор (тръбопровод за впръскване в блоков дизайн, устройства за спиране на дросела, втулка за пробиване);
- устройства за нагревателни блокове на сондажната платформа (топлогенератори, отоплителни радиатори и комуникации за разпределяне на охлаждащата течност).
ИЗИСКВАНИЯ ЗА СТРАНА
Техническите изисквания са конструкцията на сондажната платформа да отговаря на последните постижения на науката и техниката, а параметрите й да отговарят на изискванията на съвременната сондажна техника по световни стандарти. Машините и оборудването, включени в сондажната платформа, трябва да имат висок коефициент на полезно действие (КПД), достатъчна здравина, надеждност и издръжливост.
Оперативни изискванияпредполага се, че по време на работа сондажната платформа ще се поддържа чрез поддръжка и ремонт. За тази цел е необходимо да се осигури висока ремонтопригодност на сондажната платформа, т.е. наличието на нейните агрегати за поддръжка и ремонт, възможност за наблюдение на техническото състояние и подмяна на износващите се части и компоненти.
Технологичните изисквания са свързани с разходите за материали и труд за производството на сондажни платформи. Те включват:
простотата на дизайна на машините, постигната чрез максимално опростяване на тяхната блокова схема;
простота на формите на частите, рационален избор на материал и метод за получаване на заготовки с цел спестяване на материал;
оптимална точност на производство и грапавост на повърхността, намаляване на размера на обработваните повърхности;
правилният избор на допуски и прилягания, осигуряващи взаимодействие на частите, взаимозаменяемост, съответствие с техния размер, за да се елиминира монтажната работа по време на монтажа;
максимално използване на стандартни и унифицирани компоненти и части;
намаляване на гамата от режещи и закрепващи инструменти, използвани при обработката и монтажа.
Подмяната на корони и част от частта се извършва в случаите, когато дизайнът предвижда сменяеми корони и когато (в зъбни блокове) поради износване на зъбите на една корона е непрактично да се отхвърли целият скъп блок.
Технологичният маршрут за подмяна на короната на подвижните зъбни колела (каретки) се състои от следните операции: износеното зъбно колело на блока се отрязва, седалката се обработва, прави се ново зъбно колело, след което се притиска към зъбния блок и допълнително се закрепва (заваряване, закрепване и др.). При натискане на короните,предварително нагряване в маслени бани за създаване на необходимата намеса (фиг. 24.2).
Ако конструкцията предвижда сменяеми корони в отделни зъбни блокове, тогава короните са занитени към главините; по-добре е да го извършите в студено състояние, докато съотношението на дължината на пръта на такъв нит към неговия диаметър трябва да бъде не повече от 1:4. Неспазването на това условие води до надлъжно огъване на вала на нита, което създава радиален натиск върху короната и може да причини нейната деформация. Механичната и топлинна обработка на напълно заварени зъбни венци и шлици на главината, както и шлици на валове, не се различават от производството на тези елементи в нови части. Технологията на изработване на детайли се изучава подробно в дисциплината "Технология на машиностроенето".
Колоната от пръти осигурява кинематичната връзка на силовото тяло с буталото на сондажната помпа. Колоната от пръти работи в много трудни условия, подложена е на действието на циклично променящо се натоварване: в горната част е пулсиращо, в долната част е редуващо се, потопено е в корозивна течност. Страничните му повърхности се износват поради кривината на кладенеца и абразивното износване.
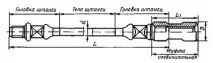
Проектиране на смукателни пръти и съединители
Необходимата издръжливост на кордажа се постига чрез подобряване на дизайна на кордажа, използване на добри технологии за производство на пръти, използване на здрави стомани и осигуряване на лесна работа.
Изчисляването на прътовия низ се свежда до определяне на големината и характера на промяната в натоварването върху тях, избор на формула за изчисление, съответстваща на условията на работа на прътите и определяне на допустимите напрежения, които определят надеждната работа на прътовия низ. изчисляването на колоната от пръти се извършва или по емпирични формули, или по специално съставени таблици, или пономограми. Смукателните пръти се произвеждат в диаметри: 12, 16, 19, 22, 25 мм. Средната дължина на пръчките е 8м. Конецът на пръчките се навива. Прътите и съединителите са изработени от St.40 за леки условия на работа, за трудни условия - от легирани стомани с последващо повърхностно закаляване.
Има тръбни пръти. Тяхното използване намалява потреблението на метал на оборудването в сондажа чрез елиминиране на тръбната колона, намалява пиковите натоварвания в точката на окачване чрез увеличаване на плаваемостта на колоната на пръта. Позволява някои технологични операции. Производството им обаче е по-сложно, а разходът и цената на метала са по-високи. SHSNU използва тръби с гладки и изкривени навън краища от якостни групи K, E, L, N, на тръби и съединители с резба a-600, конус 1:16.
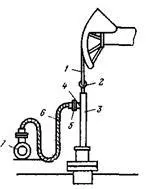
Диаграма за монтаж с тръбни пръти
1 - окачване на въже; 2 - точка на закрепване на пръта; 3 - тръбен прът;4 —страничен изход; 5 - фланцова връзка;6- гъвкав маркуч; 7 - колектор