Суровини, свойства на порести агрегати, метод за производство на експандиран глинен чакъл,
За приготвяне на лек бетон се използват портланд цимент, бързо втвърдяващ портланд цимент и портланд шлаков цимент.
Като пълнители за лек бетон се използват естествени и изкуствени насипни порести материали с насипна плътност не повече от 1200 kg / m 3 с размер на зърното до 5 mm (пясък) и не повече от 1000 kg / m 3 с размер на зърното 5 ... 40 mm (натрошен камък, чакъл).
При класифицирането на порестите агрегати се разграничават порести естествени агрегати, вулканични и седиментни и изкуствени - специално произведени и твърди промишлени отпадъци. Групата агрегати с вулканичен произход включва трошен камък и пясък от пемза, вулканична шлака, туф и туфови лави. Агрегатите от седиментен произход включват порести варовици и варовити туфи, колба, триполи, диатомити. Като порести пълнители могат да служат различни промишлени отпадъци: горивни и металургични шлаки, летлива пепел и смеси от пепел и шлака, керамични болтове.
Специално произведените порести пълнители са експандирана глина и нейните разновидности (шунгизит, пепелен чакъл, глинеста пепелна експандирана глина и др.), аглопорит, шлакова пемза, гранулирана шлака, експандиран перлит и вермикулит. Те са специално получени под формата на чакъл, трошен камък и пясък в резултат на топлинна обработка на глина, пепел, шлака и други минерални суровини.
В резултат на отделянето на газообразни продукти, дължащи се на изгаряне на органични примеси и добавки, изпаряване или други процеси, по време на изпичане настъпва набъбване на минерални суровини. В същото време по време на процеса на изпичане значителна част от него преминава в стопилката, която трябва да има определен вискозитет, за да задържа газообразни продукти. Технологичният процес на получаване на изкуственипорести агрегати включва подготовката на суровините, тяхната топлинна обработка, раздробяване и сортиране.
Най-важните показатели за свойствата на порестите агрегати са обемна плътност, плътност и якост на зърната, състав на зърното, водопоглъщане, деформируемост, устойчивост на замръзване, устойчивост на гниене, топлопроводимост , Стойностите на някои основни свойства на обикновените порести агрегати са дадени в таблица. 1
Таблица 1 Основни свойства на порестите агрегати
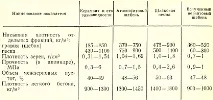
Най-широко използваният в лекия бетон е едрият порест добавъчен материал с фракция 10-20 mm, като е възможно да се използват и фракции 5-10 и 20-40 mm. Обемът на междузърнестите кухини намалява, когато факторът на формата на пълнителя се доближава до единица - съотношението на най-големия размер на зърното към най-малкия. За чакъла обемът на междузърнестите кухини е по-малък, отколкото за натрошен камък.
Водопоглъщането на инертния материал зависи както от стойността на общата порьозност, така и от структурата на парното пространство. Наличието на разтопена кора на повърхността на зърната значително намалява водопоглъщането. За експандиран глинен чакъл, който има такава кора, обемната водопоглъщаемост е почти два пъти по-ниска, отколкото за натрошен камък, който няма такава кора.
Якостта на порестите агрегати се определя чрез изстискване на зърната в цилиндъра със стоманена щанца до определена дълбочина. В същото време се намира стойността на напрежението, която се приема като показател за условна якост. Този показател обаче зависи от формата на зърната и празнината на сместа, поради което се използват специални коефициенти за преобразуване на условната якост на пълнителя в действителната якост на пълнителя, която характеризира неговата марка. За порести агрегати са установени 11 степени на якост: P25, P35, P50, P75, P100, P125, P150, P200, P250, P300 и P350.
МодулЕластичността на порестите пълнители е много по-ниска от тази на плътните. Това обуславя една от най-съществените характеристики на леките бетони – тяхната повишена деформируемост.
Експандираната глина е на първо място по отношение на производството на всички изкуствени порести агрегати. За производството му са най-подходящи нискотопими глинести скали, характеризиращи се със способността да набъбват по време на изпичане.
Химическият състав на тези скали е в следните граници: 50-55% - Si0 2, 15-25% - AI2O s, до 3% -CaO, до 4% - MgO, 6,5-10% - (Fe 2 0 s + + Fe O), 3,5-5% - (Na 2 O + K 2 O). Не трябва да съдържат повече от 30% песъчливи и прахообразни частици, както и карбонатни частици с размер над 0,2 mm, гипс и повече от 1-2% фини органични примеси. Като суровина за производството на експандирана глина се използва и пепел от топлоелектрически централи или смес от пепел и шлака.
Суровините от експандирана глина трябва да имат коефициент на набъбване (съотношението на обема на разширените към обема на суровите гранули) най-малко 2, температура на изпичане не по-висока от 1523 K, интервал на набъбване най-малко 50 K.
Има сух, пластичен и мокър метод за производство на експандирана глина. Сухият метод се използва при използване на каменоподобни глинести суровини (шисти, шунгити, кални камъни и др.), Мокрият метод се използва за добре напоени суровини, разредени до съдържание на влага в пулпа около 50%.
Най-широко използваният пластмасов метод (фиг. 1), при който гранули със съдържание на влага до 20% се образуват от насипни глинести суровини след предварителна обработка до състояние на пластична маса, последната след изсушаване или незабавно изпратена в ротационна пещ. За да се подобрят свойствата на експандираната глина, понякога в глинената маса се въвеждат железни и органични добавки. Гранулите се изпращат в ротационни пещи, където първо постепенно се нагряват до 470-880 K, а след това бързоповишаване на температурата до 1650 К. След изпичане експандираната глина се охлажда, фракционира и доставя в склада на готовите продукти.
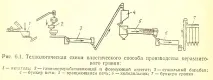
Аглопоритът се получава под формата на трошен камък чрез синтероване на нископластични глинести скали, които не набъбват по време на изпичане, или промишлени отпадъци от добив и обогатяване на въглища, горивна шлака и пепел от ТЕЦ. В шихтата за производството на аглопорит се въвежда горивна добавка, въглища. Съдържанието на гориво в заряда може да варира от 6 до 12%. При приготвянето на шихтата суровините се раздробяват, смесват, овлажняват и гранулират. Зърненият състав на заряда трябва да осигурява оптималната му газопропускливост.
Основната технологична операция при производството на аглопорит е синтероването на заряда върху решетката на непрекъсната (фиг. 6.2) или партидна машина за синтероване. Под решетката във вакуумната камера се създава вакуум, поради което през заряда се засмуква въздух. Поради изгарянето на въглища в заряда се развива температура до 1300 K и повече, което води до неговото синтероване под формата на пореста стъкловидна маса. Спечената аглопоритна торта се раздробява на трошен камък и пясък
Аглопоритният трошен камък се произвежда в размери от 5 до 40 mm в шест степени според насипната плътност: 400, 500, 600, 700, 800 и 900.
Силата на аглопоритния натрошен камък при същата плътност е много по-малка от тази на експандираната глина.
Изискванията за устойчивост на замръзване на аглопорит са подобни на тези за експандиран глинен чакъл. Средната стойност на коефициента на форма на аглопорит натрошен камък е 2-2,5, загубата на тегло на проба от аглопорит натрошен камък по време на калциниране е не повече от 3%. За аглопорита се поставя допълнително изискване за устойчивост на разлагане на силикат и желязо.
Аглопоритният чакъл се произвежда в четири степени по насипна плътност II -500, 600, 700 и 800 и седем степени по якост- ОТ P50 (крайна якост на натиск, в цилиндъра 1-1,29 MPa) до P250 (3 MPa или повече). Изчисленията показват, че замяната на 1 милион m 3 внесен естествен натрошен камък с аглопоритен чакъл от пепелта на местна топлоелектрическа централа, само чрез намаляване на транспортните разходи за транспортиране на разстояние от 500-1000 км, спестява около 2 милиона рубли.
Шлаковата пемза (термозит) е един от най-ефективните видове изкуствени порести агрегати. Получава се чрез порьозиране на шлакови стопилки в резултат на бързото им охлаждане с вода, въздух или пара.
Размерът на порите на шлаковата пемза, в зависимост от метода на производство, варира от 0,04 до 4,5 mm, порьозността е 52-78%, а водопоглъщането е 10-55%. Трошен камък се произвежда с насипна плътност 300-800 и класове на якост 25-150.
Разходите за труд за производството на 1 m 3 шлакова пемза са 5 пъти по-малко, отколкото за други порести агрегати, а производителността на труда е 4-5 пъти по-висока.
Разширен перлит. Перлитът е вулканична стъклена скала, съдържаща 65-75% аморфен силициев диоксид и около 1-2% свързана вода. При термична обработка в температурен диапазон 1250-1550K перлитът омеква и набъбва главно в резултат на интензивно отделяне на водни пари. Коефициентът на разширение на перлита достига 10-12. За термична подготовка на перлит се използват главно противотокови ротационни пещи с дължина 5–8 м и вътрешен диаметър 0,7–1,2 м. Преди изпичане суровините често се подлагат на предварителна топлинна обработка, за да се предотврати последващо напукване на скалата и да се получи разширен перлит с най-ниска плътност. В този случай при температура 250-4500C се отстранява свободната и слабо свързана вода.
Качеството на готовия продукт, естеството и степента на неговото набъбване се влияе от размера на зърната.
Оптимален размерзърната от изпечен перлит се считат за 5-15 mm.
Перлитният трошен камък се произвежда в 4 степени по обемно тегло: 300, 400, 500 и 600. Загубата му на тегло при 15-кратно замразяване и размразяване трябва да бъде не повече от 10%. С увеличаване на насипната плътност от 300 на 600, допустимата водопоглъщаемост за 1 час за натрошен перлит намалява от 75 на 30%.
Перлитният пясък е най-лекият от порестите пясъци. За лек бетон е подходящ перлитов пясък с минимална насипна плътност 200. Съдържанието на прахови фракции в него не трябва да надвишава 10%.