Технологични параметри на многослойни печатни платки и критерии за избора им
Александър Акулин
За инженер-конструктор, който започва да проследява следващия проект на многослойна печатна платка, ключовият въпрос е изборът на нейните технологични параметри. В случай, че можете да вземете предишни проекти в подобен дизайн като основа, няма специални проблеми - най-вероятно броят на слоевете и други параметри на печатната платка ще останат непроменени. Това ще позволи на отдела за покупки да се възползва от установените канали за поръчка на печатни платки, обръщайки се към доверени доставчици както за спешно производство на проби, така и за серийни поръчки.
Ако сложността на печатната платка се увеличи значително (броят на компонентите, схемите се увеличава, компонентите се появяват в по-сложни пакети, особено BGA с по-фина стъпка), има голяма вероятност тя да не се вмести в предварително разработените стандарти. Това означава, че успешното проследяване може да изисква:
- увеличаване на броя на слоевете;
- намаляване на ширината на проводника и пролуката;
- намаляване на размера на отворите;
- добавяне на "слепи" и скрити дупки;
- промяна на други параметри на PCB.
В такава ситуация и дизайнерът, и доставчикът, и дори ръководителят на компанията, очевидно не са сигурни, че проект с по-строги стандарти ще бъде изпълнен от предишните доставчици на печатни платки толкова надеждно, колкото и предишните поръчки. И има основателни причини.
Въпреки факта, че технологичните възможности както на българските, така и на чуждестранните доставчици на печатни платки нарастват всяка година, проектантът трябва да внимава да използва предлаганите от тях „гранични параметри“ в своите разработки. Факт е, че тези параметри могат да се прилагат само къмопределени условия, не всички от които могат да бъдат изпълнени в конкретен проект за печатна платка, с определен обем и спешност на поръчката.
Помислете, като типичен пример, таблица с параметри, предлагани от PCB технологията на своите клиенти (Таблица 1). В тази таблица основните параметри на оформлението и изборът на дизайн на платка са обобщени в три колони. Колоната с надпис „Опростена“ е най-евтината опция, с повечето опции за платки, избрани в тази колона, дизайнерът ще осигури най-големите спестявания на разходи както за проби, така и за производствени поръчки. До тях е показан стандартен набор от параметри - използването им не създава особени затруднения при производството. Най-дясната колона съдържа стойности, които по принцип са възможни за постигане, но са свързани с определени трудности и съответно ще доведат до увеличаване на цената и времето на поръчката. Компанията препоръчва на клиентите си да се придържат към параметрите, посочени в колона "Стандарт", когато е възможно, и да прибягват до "сложни" варианти само по изключение. Освен това не се препоръчва да се задават "сложни" параметри за потенциално серийни поръчки.

Какъв е проблемът тук? Има ли противоречие в това? Изглежда, че един инженер-конструктор не трябва да мисли за тънкостите, свързани с производството на печатни платки. Много клиенти мислят така: „Има таблица с допустими параметри, предоставена от производителя. Защо просто не го следвате и оставите на доставчика на печатни платки да изпълни тези изисквания с възможно най-доброто качество.“
Това е грешна позиция. Факт е, че при производството на печатни платки - изключително труден процес - много параметри са взаимосвързани. Неслучайно лозунгът„Дизайн за производство“. Проектантът на печатни платки трябва не само да се придържа сляпо към параметрите, дадени в референтните таблици на доставчиците, но и да има представа как ще бъде произведена печатната платка, през какви процеси и етапи преминава по време на производството и как те си влияят един на друг. Само в този случай можете:
- Оптимизирайте разходите за производство на печатни платки (като изберете най-евтината комбинация от параметри).
- Намалете времето за доставка на поръчката (поради избора на оптимална структура и материали).
- Увеличете надеждността на продукта (чрез подобряване на технологичността на платката).
Трябва да се съгласите, че всички страни са заинтересовани от изпълнението на тези точки. Нека да видим как трябва да "управлявате" параметрите на печатната платка и какви могат да бъдат причините за проблемите на производителите, когато задават неразумно твърди стойности за един или друг параметър.
Брой слоеве
Ако се планират серийни поръчки и е необходимо намаляване на разходите, препоръчително е да включите не повече от 6–8 слоя в проекта, в противен случай могат да възникнат проблеми с избора на доставчик в бъдеще. Защо? Факт е, че за завод от средно ниво (а именно в такива заводи цените могат да бъдат намалени при влизане в серийно производство), ограничението за максималния брой слоеве е по правило 6 или 8.
Причини за възможни проблеми:
- липса на оборудване за серийно сглобяване на повече от 8 слоя;
- неточност на подравняването на слоевете по време на пресоване (увеличава се с увеличаване на броя на слоевете);
- надлъжна и диагонална деформация на слоеве;
- неточност при центриране на пробиване;
- отклонение на свредлото в многослоен пакет;
- неточност на ецване и подрязване;
- проблеми с обшивката на отворите иPCB повърхност;
- необходимостта от повишено налягане при натискане на повече от 8 слоя.
Ширина и празнина на проводника
Често срещана практика сред разработчиците е да определят минимална ширина на проводника (напр. 0,1 mm) за целия проект. И всички проводници на платката са направени с тази ширина, въпреки че би било по-правилно да нарисувате 90% от следите с ширина 0,125 или дори 0,15 mm.
Фигурата показва стъпките в процеса на ецване на печатни проводници.
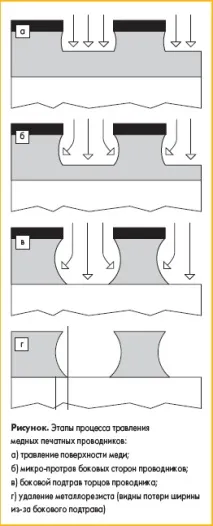
Загубите поради странично подрязване могат да достигнат до 50% от височината на проводника (дебелина на медта). Освен това, поради влиянието на различни фактори (нехомогенност на материала, дефекти във фотомаската, фоторезиста и др.), има голяма вероятност от поява на по-големи локални недоразбивания. Това е критично за проводници с ширина 0,1 mm и още по-важно за ширина 0,075 mm. Да кажем, че има някакъв шанс един от проводниците на таблото да е дефектен. Чрез промяна на ширината на проводника от 0,1 на 0,15 mm за 90% от проводниците, дизайнерът ще намали вероятността от производство на дефектна платка с фактор 10 (. ).
Таблици 3–5 позволяват да се прецени в кои случаи (за дадена дебелина на фолиото и за обща дебелина на медта) е допустимо да се използват проводници и междини с една или друга ширина. При използване на таблици трябва да се има предвид, че по време на метализирането на отворите върху външните слоеве на печатната платка се натрупва допълнителен слой мед с дебелина до 35 микрона. Таблица 2 изброява точки, изискващи специално внимание.