Технология на производство на пенобетонни блокове смес от пенобетон, формоване, сушене (Видео)
Технологията на производство на пенобетонни блокове включва няколко основни етапа:
- подготовка на смес от пенобетон;
- формоване;
- сушене;
- оголване, рязане, термична обработка.
Всеки от тези етапи може да има свои собствени характеристики в зависимост от избраната технология и оборудване в конкретно предприятие. Помислете за всички нюанси на всеки етап от производството и тяхното въздействие върху качеството на крайния продукт.
Производство на смес от пенобетон
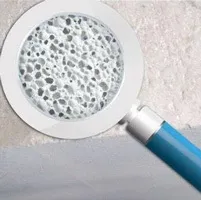
- Класическият метод с използване на генератор на пяна по своята същност може да се опише по следния начин: сместа от пяна се приготвя отделно в генератора на пяна и след това се въвежда в готовата бетонова смес, смесва се и се изпраща към формите чрез тръбопроводи с помощта на помпи.
- Баротехнология - при този метод всички компоненти на сместа от пенобетон (цимент, пясък, концентрат от смес от пяна, вода) се подават в запечатан смесител. Компресорът изпомпва въздух, създавайки налягане вътре в миксера и започва процесът на смесване, по време на който разтворът се насища с въздух. След това готовата смес се подава под налягане в шприцформи, където набъбва в резултат на спад на налягането.
И двата метода включват възможността за използване на различни добавки и пластификатори. Първият метод изисква по-скъпо технологично оборудване, а вторият се счита за по-обещаващ, тъй като има възможност за използване на изкуствени добавки за разпенване исамият процес е по-бърз. Въпреки това, качеството на пенобетона, приготвен по първия метод, е все още по-високо и това се отразява в цената.
Формовка от пеноблок
За получаване на блокове от пяна с желаната форма и размер се използват две основни технологии: изливане във форми с необходимия размер или изрязване от твърд монолит.
Технология за формоване на блокове от инжекционна пяна
Технологията на леене е близка до класическия метод за производство на такива строителни материали, когато готовата смес се излива в подходяща форма, изсушава се, след това се отстранява и се довежда до готовност (сушене, изпичане, смилане).
При производството на пеноблоковесе използват метални касетъчни форми с подвижни страни и прегради между секциите. При производството на касети за леене на блокове от пяна се запазва основният параметър на размерите - височината на формата е 600 mm.
Несъмнените предимства на този метод включват факта, че след отстраняване на продукцията има готов продукт, който изисква само сушене и опаковане. На практика обаче могат да се срещнат много трудности. На първо място, формата трябва да бъде изработена от качествен материал, включително прегради. Качествените форми могат да бъдат направени от скъпа дебела стоманена ламарина. Използването на матрица с тънки прегради може да доведе до нарушаване на геометрията, когато преградата може да бъде изместена или деформирана по време на изливането на пенобетон под налягане.
За да бъде изваждането безболезнено,формата изисква смазване. Технологията включва използването на специална смазка, която е доста скъпа, тъй като производителите понякога използват добив на петрол. Получателят на такива продукти рискува да получи остатъци от грес върху блока от пяна, което допълнително ще повлияе на качествотонастройка на материала по време на полагане и довършване. Трябва да се отбележи, че нискокачественото машинно масло може да има пагубен ефект дори върху висококачествен бетон.
В допълнение,технологията изисква определено време на задържане, узряване на сместа от пенобетон, след което тя може да бъде извадена от формата без риск от повреда. При ограничен брой касети в предприятието има изкушение да се ускори този процес, което може да повлияе на качеството на продукта, неговата здравина; съществува риск от получаване на блокове с повредени ъгли и повърхности.
Друг недостатък от гледна точка на потребителя е образуването на така наречената "сол " върху горния слой на напълнената касета. Всъщност не е възможно да се избегне "розовото" с никакъв метод на отливане и втвърдяване с отворено горно ниво. Достатъчно е да си припомним обичайната касета за замразяване на лед в домашен фризер. Същото се случва, например, със стоманобетонни подови плочи, където всички страни са гладки и равни, с изключение на една горна част.
От гледна точка на производителя, недостатъкът на метода на шприцване може да се счита за ограниченото производство по отношение на размера на блоковете от пяна. Броят на опциите зависи от набора налични касети. Можете да изчислите необходимостта от форми с един или друг размер, като проучите потребителския пазар, но също така може да е нерентабилно да поддържате скъпи форми за производство на малки партиди.
Рязане на блокове. Този метод се извършва на два етапа:
- изливане на масата от пенобетон в голяма форма, изсушаване и изваждане от формата;
- нарязване на монолитна бетонна плоча на блокове с желания размер.
За рязане е необходима специална инсталация, като съединителни елементи могат да се използват специални струни или лентови и верижни триони.Този метод има редица предимства, като напрза производителя и за потребителя. Ето основните от тях:
- Възможността за преконфигуриране на инсталацията за рязане дава възможност за производство на блокове с произволни размери по желание на клиента.
- Висока геометрична точност, включително форма и размер на блока. Това позволява на потребителя да ускори процеса на полагане и последващо довършване. В допълнение, геометрично правилните блокове могат да бъдат положени чрез закрепване със специално лепило. Това не изисква дебел слой, необходим за изравняване на грапавостта, шевът е тънък и не изисква допълнително фугиране.
- Липсата на смазване върху повърхностите на блоковете осигурява нормална адхезия, адхезия на повърхността на блока с материала, използван за довършителни работи (замазка, гипс и др.)
- Рязането с трион гарантира равни странични ръбове и липса на стърготини, когато блокът се извади от матрицата. Също така, в процеса на рязане на монолита, „розовото“ се отрязва.
Недостатъците на тази технология включват необходимостта от точно експониране на процеса на узряване на пенобетонната маса във формата. Когато използвате устройство за низ за рязане, е необходимо да се уверите, че масата не изсъхва, вече поддържа формата си добре, но все още не е придобила желаната сила.
При рязане с лентови плочи е необходимо, напротив, масата да придобие достатъчна якост, тъй като при този метод блоковете са наклонени върху масата за рязане и в противен случай са възможни стружки на ръбовете или деформация.
Сушене на блокове от пяна и втвърдяване
За леене под налягане на блокове от пяна са възможни две опции за сушене:
- естествено сушене, по време на което пенобетонната маса престоява във формите за 10 часа, за да придобие здравина, след коетоследва деформиране;
- термична обработка в камерата за пара: в този случай само за няколко часа масата от пенобетон може да придобие до 75% от проектната якост.
Този последен метод е най-широко използван не само при производството на блокове от пяна, но и за формоване на стоманобетонни продукти.
За технологияизползваща рязане на монолитни плочи,използва се само естествен метод на сушене. Времето на процеса на сушене е от 4 до 14 часа и зависи от технологията на рязане, използването на режещите елементи, както и от използваните добавки, които влияят на процеса на втвърдяване.
Заключение
В заключение казваме, че въпреки че областтана използване на блокове от пяна в строителството има някои ограничения, например при многоетажно строителство, тенденцията да се използват в нискомасово и индивидуално строителство допринася за разширяването на производството и подобряването на качеството на този строителен материал. Въпреки това, както можете да видите, използването на различни технологии води до различен продукт. Когато се свържете с фирма за производство и продажба на блокове от пяна, трябва да се запознаете с използваната технология. Така че, с класическия метод на производство с помощта на генератор на пяна, за производството на маса от пяна се използват само биологични добавки, а крайният продукт е наистина екологичен строителен материал. Познавайки начина на формиране на блоковете, може да се прецени колко трудоемко ще бъде полагането и последващото довършване.