Закаляване на работни повърхности на пътностроителна техника - ДМА
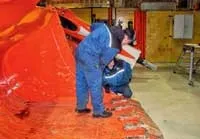
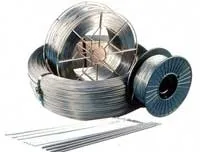
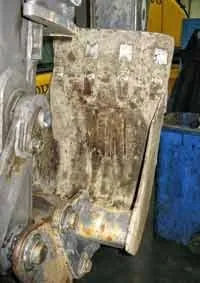
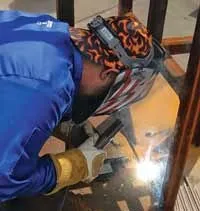
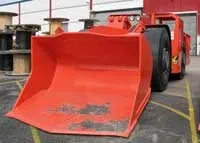
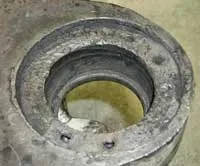
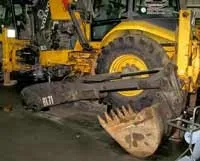
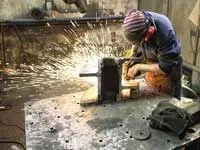
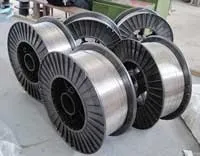
Повърхностното втвърдяване е бърз, лесен и ефективен начин да направите кофи, булдозерни ножове и друго оборудване по-издръжливи и издържани по-дълго, често за по-малко пари. Използва се закаляване на работни повърхности както на старо, така и на ново оборудване.
В процеса на втвърдяване металът за наваряване (твърд метал) се свързва с метала на детайла, за да му придаде определени качества на устойчивост на износване и/или да възстанови размерите след износване, по-точно тези наварки за наваряване правят основния метал устойчив на удар или абразия. Повърхностното втвърдяване може да върне износените части до почти ново състояние на цена от 25% до 75% по-ниска от цената за подмяна на износени части. Повърхностното закаляване може също така да увеличи живота на частите с до 300% спрямо частите без повърхностно закаляване, особено при ново оборудване.
Причини за износване на части
В зависимост от причините, причиняващи износване на работното оборудване, се избира сплавта за наваряване. В 55-60% от случаите износването се дължи на абразивни въздействия. Различават се следните основни видове абразивно износване: износване от малки абразивни частици; интензивно износване чрез смилане на метал с абразивни частици при наличие на натиск; комбинирано ударно-абразивно износване с режещо действие на плъзгащи се по метал твърди частици.
Типовете износване при удар и залепване (наричано също износване метал върху метал) също са често срещани.
Високотемпературните и корозивните видове износване са малко по-рядко срещани.
Най-лека формаабразивно износване - износване от малки частици - възниква, когато ерозията се развива бавно в метала под действието на малки минерални частици, плъзгащи се върху него. Поради липсата на ударни натоварвания, закаляването с крехки високовъглеродни карбиди, съдържащи карбид или хромов карбид, е най-добрата защита срещу този вид износване. Често в тези сплави се образува мрежа от малки пукнатини, облекчаващи вътрешните напрежения и предотвратяващи развитието на дълбоки пукнатини в основния метал.
Избор на метод на заваряване
Първо, трябва да определите точно какво е необходимо за втвърдяване на повърхностите: възстановяване на размерите, наваряване или комбинация от двата вида обработка. Технологията за завършване - последователно наслагване на слоеве чрез заваряване - връща износената част в първоначалните й размери. Наваряването е нанасянето на твърд слой, който предпазва повърхността от износване. Комбинацията от повторно боядисване и наваряване удължава живота на частта. Тази технология може да се използва многократно, връщайки частта в работно състояние.
Размерът, формата и ориентацията на частите, които се нуждаят от закаляване на работните повърхности, определя какъв тип заваряване ще се използва и какви изисквания ще бъдат поставени към квалификацията на заварчика. Най-често използваното за закаляване е ръчното заваряване с електрод (съкращение SMAW) или електродъгово заваряване с флюсова сърцевина (FCAW), но някои компании, които се занимават с нанасяне на големи обеми на части, предпочитат заваряване под флюс (SAW).
Всеки от изброените методи има определени предимства и недостатъци. Например оборудването за ръчно заваряване с електрод е много компактно и следователно идеално за работа извън цеха, на мястото на оборудването.Има много видове електроди, които се използват за различни заваръчни операции, заваръчни шевове във всяко пространствено положение, включително за наваряване на сравнително дебели плочи. MMA заваряването обаче има ниска икономичност, тъй като неизбежно остават остатъци от неизползван къс електрод, скоростите на отлагане са сравнително ниски (приблизително 0,5 до 3,0 kg/h) и може да се наложи да се отложат множество слоеве метал, за да се даде на детайла максимална устойчивост на износване. От друга страна, закаляването чрез заваряване с флюсова сърцевина осигурява по-висока скорост на отлагане (приблизително 2,0-11,0 kg/h) и е по-лесно за използване. Често се изисква само минимално обучение и лицето вече е способно да върши работата. Но за разлика от ръчното заваряване с електроди, заваряването с флюсова тел може да се извършва само върху плоски хоризонтални повърхности.
Закаляването и възстановяването, извършено на мястото на експлоатация на оборудването, особено ако е разположено в труднодостъпни райони, ви позволява да спестите от доставката на резервни части или транспортирането на части, първо за възстановяване до ремонтно съоръжение и след това обратно до мястото на работа.
Избор на основния метал на детайла
Трябва да се вземе предвид класът на основния метал. Най-често се закаляват въглеродни и нисколегирани стомани. Но трябва да се отбележи, че поради високото съдържание на въглерод и/или легиращи добавки, тези стомани могат да станат много крехки, когато са закалени и изискват предварителна или крайна термична обработка за облекчаване на вътрешните напрежения, за да се предотвратят пукнатини. Дебел неблагороден метал също може да се наложи да бъде термично обработен.
Аустенитни манганови стоманимогат да бъдат подложени на повърхностно втвърдяване и в резултат на заваряване да придобият повишена крехкост. Но за разлика от въглеродните и нисколегираните стомани, аустенитните манганови стомани не трябва да се подлагат на предварителна топлинна обработка, докато температурата на частта не падне под 10 °C. По време на закаляването температурата на основния метал трябва да остане под 260 °C, тъй като ако това ниво бъде надвишено за дълго време, крехкостта на стоманата ще се увеличи. В аустенитни манганови стомани с по-високо съдържание на въглерод и по-ниско съдържание на манган, тази реакция се ускорява и съотношението време/температура става прогресивно по-малко.
Преди да започнете наваряването, основният метал трябва да бъде закален, добре почистен от мръсотия, мазнини, ръжда и след това повърхността на детайла трябва да се измие. Може да се наложи да се отстранят остатъците от предварително заварения наварен метал чрез дъгово или плазмено изрязване, както и да се заварят пукнатините.