5.3. Рязане и почистване на отливки
След почистване от остатъците от формовъчен и сърцевинен пясък и следи от изгаряне върху отливките остават следи от подаването на захранващи устройства, нагоре, заливи, неравности, натрупвания и различни неравности. Всички неравности по повърхността на отливките се отстраняват чрез изрязване с длета, почистване с абразивни колела или дъгово рязане. Големите отливки се почистват след подрязване с осцилиращ шмиргел, движещ се по монорелсов път над почистващия конвейер или ролкова маса, върху която са разположени отливките. Отливките със сложна повърхност се почистват с абразивни колела, монтирани на универсални машини, наречени шмиргели, с едно или две абразивни колела. Скоростта на въртене на колелото може да се променя безстепенно в широк диапазон (1500–5000 об/мин), осигурявайки почистване на отливките в най-рационалните режими.
Широко разпространено приложение в масовото производство намериха автоматични линии за почистване на отливки, които имат формата на въртящо се тяло (шайби, дискове, барабани). За тези цели се използват многошпинделни инсталации с абразивни колела. Например, машина с осем шпиндела се използва за почистване на отливки на картера на двигателния блок, която обработва всички плоски повърхности (фиг. 5.7). Отливката по линията се премества от стъпков верижен конвейер 1 от една позиция в друга. Отливките се зареждат в линията с подемник и се разтоварват автоматично.
Всички хоризонтални равнини се почистват с тарелкови абразивни колела на шлифовъчни машини 2, наклонени странични повърхности - с кръгове на машини 3. Вертикалните крайни равнини се почистват с кръгове на машини 4, а вертикалните странични повърхности - с кръгове на машини 5.
Carter 6 се използва за преместване на картера в напречна посока, за да се почистят краищата.
Почистване на хоризонтални равнини, върху които първоначално е монтирана отливкатакартер, се произвежда от вертикални шпиндели след предварително преобръщане на отливката на 180 ° от наклонителя 7, задвижван от триещото устройство 8.
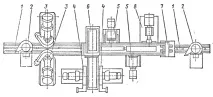
Фиг. 5.7. Автоматизирана инсталация за почистване на плоски повърхности на корпусни отливки
6. Мерки за предотвратяване и отстраняване на дефекти в отливките
6.1. Контрол на качеството в леярната
В нашата страна се създава хармонична система за управление на качеството на промишлените продукти, която се основава на организацията на контрола на качеството, навременното откриване на дефекти, техния анализ и предприемане на бързи мерки за отстраняване на причините на всички етапи на производството. При производство с масов поток забавянето при вземане на решение за отстраняване на открит дефект води до значителни материални загуби за предприятието.
Създадени са класификатори на дефекти за оперативно отчитане и вземане на мерки, обработка на информация за качеството. Компютрите се използват за обработка на информация за брака и като средство за получаване на препоръки за вземане на решения за отстраняване на дефекти.
Контролът на качеството се извършва на всички технологични етапи и във всички отдели на леярната: контрол на качеството на суровините (за подготовка на шихти, формовъчни и сърцевини); контрол на качеството и износване на цялото оборудване (модели, сърцевини, колби, проводници, сушилни плочи и др.);
контрол на качеството и износването на машини за формоване и сърцевини; контрол на качеството на течния метал (химичен състав, степен на дезоксидация, склонност към охлаждане, насищане с газ и др.); контрол на качеството на формите и сърцата; контрол на качеството на готовите отливки.
Отливките се контролират внимателно. Проверете техните геометрични и основни размери, необходими за по-нататъшна обработка,особено на автоматизирани линии. Отливките, работещи под налягане, се изпитват за хидротест по различни методи (отливката се пълни с течност под налягане или се потапя в течност и се нагнетява с въздух). В особено критични случаи отливките се подлагат на металографско и химическо изследване. Ако е необходимо да се изследват механичните свойства на метала, едновременно с отливките се отливат съответните проби или се изрязват от определени места за леене, предвидени в проекта.
За контрол на качеството на отливките се използват различни методи, от най-простите - визуални, шаблони, измервателни уреди и др. До най-модерните - магнитни, ултразвукови, рентгенови, с помощта на изотопи (гама дефектоскопия) и др. Тези методи, без да разрушават продукта, ви позволяват да определите местоположението и размера на дефекта.
Процесите на дефектоскопия в масовото производство са автоматизирани.