Аустенитни високолегирани стомани
Аустенитни високолегирани стомани
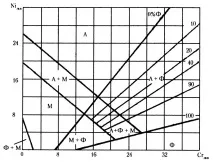
Ориз. 1. Структурна диаграма на Шефлер
Изчисляването на съдържанието на елементи в заваръчния метал съгласно тези формули се извършва, като се вземат предвид пропорциите на основния и допълнителния метал.
Има няколко характеристики на заваряемостта на стоманите от този клас, които трябва да се вземат предвид при разработването на технологията.
1. Рискът от възникване в заваръчния метал и 3TV на така наречената междукристална корозия (ICC). Механизмът на това явление, което се случва в определена температурно-времева област, е изчерпването на хрома в граничните области на металните зърна поради дифузията му към границите на зърната и образуването на хромни карбиди там.
Причината за това може да бъде неблагоприятният режим на заваряване (фиг. 2) (ниски скорости на охлаждане), когато има достатъчно време за дифузия на хромни атоми от приграничните области на зърното към неговите граници и образуване на карбиди там, което води до появата на метални зони, обеднени на хром. Именно те са подложени на корозионно унищожаване, когато продуктът работи в агресивна среда.
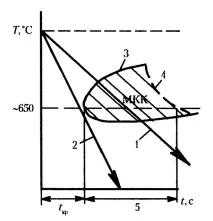
Ориз. 2. Схематично представяне на зоната на възникване на междукристална корозия на аустенитна стомана по време на нейното нагряване:
1 - скорост на охлаждане, допринасяща за утаяването на карбиди; 2 - скорост на охлаждане, която не води до утаяване на карбиди; 3 - началото на появата на тенденцията на метала към ICC; 4 - край на процеса на образуване на карбиди; 5 - първоначална тенденция към ICC (tim)
Прилагането на някои от тези препоръки по технологичен начин се състои в разработването на такива технологии, които позволяват да се получи стойността на скоростта на охлаждане, която пада за дадена марка стомана в инкубационния период за образуване на хромни карбиди (виж фиг. 2, крива 2).
2. Наличие на изразена едродендритна колонна структуразаваръчен метал, което повишава чувствителността му към горещо напукване. За да се намали тази опасност, се препоръчва да се използват всички методи, водещи до усъвършенстване на структурата: модифициране на метала с титан и ниобий, използването на физични методи (въвеждане на вибрации, ултразвук, електромагнитно смесване), както и въвеждането на феритизиращи елементи в шева, което води до образуването на острови от δ-ферит в шева. Също така трябва да се избягват условия на заваряване, водещи до тесни и дълбоки пробиви. Актуално, особено при дълбоки аустенитни заварки, е да се намали съдържанието на примеси като фосфор и сяра, които образуват евтектика с ниска топимост.
3. Дифузионни процеси (особено за топлоустойчиви стомани), протичащи в заварени съединения при високи работни температури. По този начин термичното стареене в температурния диапазон от 350 500°C причинява появата на "475-градусова чупливост".
При температури 500-650°C се наблюдава утаяване на карбиди и образуване на σ-фаза и се наблюдава утаяване на интерметални съединения. Всички тези процеси на топлинно стареене водят до крехкост на метала при ниски температури и намаляване на якостта при високи температури. Ефективна мярка за предотвратяване на вредните ефекти от топлинното стареене е да се намали съдържанието на въглерод както в основния метал, така и в метала на заваръчния шев.
Технологията на заваряване на стомани от този клас трябва да бъде изградена, като се вземат предвид както тези характеристики, така и техните термофизични свойства. Последните се характеризират с ниски стойности на топлопроводимост и високи стойности на коефициента на линейно разширение. Това предполага (при други равни условия в сравнение с перлитни стомани) увеличаване на дълбочината на проникване. За да се намалят деформациите, най-добрите методи и режими на заваряване ще бъдат тези, които се характеризират смаксимална концентрация на топлинна енергия.
Технологичните начини за борба с образуването на пукнатини включват търсене на структурни форми на заварени съединения и режими на заваряване, които намаляват скоростта на нарастване на деформациите в процеса на охлаждане на съединението. Важна е формата на проникване, която не трябва да е дълбока при малка ширина (опасност от появата на горещи пукнатини по равнината на разцепване на кристалитите в заваръчната вана по време на втвърдяването).
За заваряване на този клас стомани са приложими почти всички методи за заваряване чрез стопяване.
При ръчно заваряване с електрод с консумативно покритие основната трудност е стабилното осигуряване на необходимия химичен състав на заваръчния шев, в зависимост от неговото пространствено положение, за различни видове заварени съединения, като се вземат предвид промените в количеството на отложен метал и дълбочината на проникване на основния. Това се постига главно чрез регулиране на състава на покритието (според съдържанието на необходимото количество ферит в шева).
Тип покритие - основен (например калциев флуорид), постоянен ток с обратна полярност. Шевовете се препоръчват да се извършват при ниски токове с минимален диаметър на електрода (за да се избегнат горещи пукнатини). При заваряване на най-често срещаните устойчиви на корозия стомани марки 08Kh18N10, 08Kh18N10T, 12Kh18N10T, 08Kh18N12T и др., Препоръчва се използването на електроди от типа E-04Kh20N9, E-07Kh20N9, E-08Kh19N10G2B клас TsL-11, и т.н.
При заваряване на критични конструкции трябва да се вземат мерки за предотвратяване на падането на капки разтопен метал върху повърхността на основния метал, за да се избегнат микротермични удари, които могат да причинят корозионно напукване в тези зони по време на работа.
Автоматизираното заваряване под флюс се използва широко за структурно производствоот елементи в дебелини 4.0. 60,0 мм. В същото време процесът осигурява висока стабилност на химичния състав на шева по дължината с едновременна добра защита на шева и неговото формиране. Токът е постоянен, полярността - в зависимост от марката на използваните потоци. Токовите режими са малки (в сравнение с перлитни стомани). Легирането на шева се извършва чрез поток или чрез тел. Неокисляващи или слабо окисляващи потоци (ниско съдържание на силициев флуорид или силно основно съдържание на флуор). Широко използвани са марките АН-26, 48-ОФ-10 и АНФ-14. В зависимост от класа на заваряваната стомана се избира системата от флюсова тел (например за стомана 20Kh23N8, тел Sv-13Kh25N18, поток ANF-5).
При заваряване в защитни газове се използват както активни газове (CO2), така и инертни газове (аргон, хелий) или техни смеси. Тук (особено при използване на смеси) става възможно да се контролира широко формата на проникване, да се увеличи стабилността на изгарянето на дъгата и да се намали загубата на легиращи елементи. При заваряване в инертни газове е възможно да се използват както неконсумируеми (волфрамови), така и консумативни електроди. Първият се използва за заваряване на метал с малка дебелина или за осигуряване на висококачествено проникване на корена на заваръчния шев. Използва се волфрамов електрод в комбинация с аргон от най-висок или първи клас за фуги с дебелина до 12,0 mm (което не изключва използването на метода за заваряване на големи дебелини).
Заваряването се извършва на постоянен ток с права полярност във всички пространствени позиции с непрекъсната или импулсна дъга. Последният метод, с отлично формиране на заваръчния шев при малки дебелини, позволява да се намалят деформациите и ширината на ЗТВ, да се получи дезориентирана структура на първичната кристализация на заваръчния шев, като по този начин се намалява рискът от горещи пукнатини. При заваряване с консумативен електрод съставът може да се регулираотложен метал чрез промяна на състава на защитната атмосфера.
Заваряването с консумативен електрод се извършва както в инертни, така и в активни газове или техни смеси. В зависимост от плътността на тока и диаметъра на електродната тел, преносът на метала в дъгата може да бъде капков и струен (последният изглежда по-предпочитан - при него пръскането е практически елиминирано).
Преносът на струята, освен с критичния ток, е свързан със състава на газовата атмосфера. По този начин добавянето на 3,5% кислород намалява големината на критичния ток и (поради окисляване) намалява порьозността, причинена от водорода. Последното се постига със смес от 85,80% Ag +15. 20% CO2. Тази смес е по-евтина от чистия аргон, но съществува риск от изгаряне на легиращи елементи от отложения метал. Същият процес съпътства заваряването в чист CO2, както и известна карбуризация на отложения метал.
Силата на тока при заваряване с волфрамов електрод се избира в зависимост от неговия диаметър, а при заваряване с консумативен електрод - в зависимост от диаметъра на електродната тел и дебелината на заваряваните елементи. Така че, за дебелина от 4,0 mm, челното заваряване без режещи ръбове се извършва в един проход de = 1,0. 1,6 мм; Iw=160. 280А; консумация на аргон φ \u003d 6.8 l / min и заваряване с дебелина 8.0 mm с V-образен жлеб - в два прохода с тел de \u003d 1.6. 2,0 mm при сила на тока Isv \u003d 240. 340 A, при скорост на потока φ \u003d 12. 15 л/мин.