АВТОМАТИЗИРАН КОНТРОЛ НА ЕКСТРУЗИОННАТА ИНСТАЛАЦИЯ, Издстатия RSCI, Международен
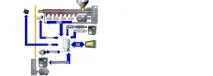
Гридин С.М.
Студент, катедра Вътрешноелектрическо оборудване и автоматизация,
Моногаров С.И.
FSBEI HPE "Кубански държавен технологичен университет"
Армавирски институт по механика и технологии
АВТОМАТИЗИРАН КОНТРОЛ НА ЕКСТРУЗИОННИЯ МОДУЛ
Резюме
Статията разглежда въвеждането на автоматизирана система за управление на екструдера за подобряване на качеството на продуктите, опростяване на процесите на управление на екструдера, привличане на предприемачи и осигуряване на икономическото развитие на предприятието на тази основа.
Ключови думи: автоматизация, екструдер, индустрия.
Ключови думи: автоматизация, екструдер, индустрия.
В екструзионната индустрия има нарастваща тенденция за комбиниране на различни контролни устройства под управлението на едно общо устройство, което упражнява пълен контрол и управление на всички механизми на екструзионната линия. Трябва да се отбележи, че множество етапи на управление на екструдера могат да бъдат реализирани в йерархична връзка. Най-често срещаните устройства, които комбинират контрол на температурата в различни области. Най-често задачата на такива системи е да поддържат зададените параметри на стопилката, като контролират нагряването на първите две или три зони, които са най-близо до зоната, в която се топи полимерът. Промяната на температурата в такива зони се извършва автоматично от системата за каскадно управление. По този начин обаче е възможно да се извърши регулиране при доста ниска скорост, тъй като реакцията на зоните на работния обем към промените в температурните параметри е много бавна. Също така честоима системи за контрол на налягането, които разчитат на плавна промяна на скоростта на шнека, за да поддържат постоянно налягане на полимерната стопилка.
Най-новите видове екструдери често са оборудвани с микропроцесорна система, която позволява едновременен контрол и управление на температурата и налягането на стопилката, както и дебелината и ширината на екструдата и други параметри на екструдирането. Някои системи за контрол могат да бъдат комбинирани в обща система за управление на производството. Например, те позволяват освен управлението на екструдера, да се контролират системите, които подготвят материала за зареждане в екструдера, паралелният екструдер по време на коекструзия, задвижването и температурата на зъбната помпа, системата за контрол на здравината и изрязването на ръбовете на екструдата и много други параметри.
При анализ на литературата /1,4,6/ става ясно, че на практика не се постига истински пълен контрол на процеса на екструдиране. За да може системата да се нарече система за истински пълен контрол, тя трябва да упражнява контрол по следния начин: контролираният процес трябва да се разглежда като система от много променливи, чиято връзка е напълно известна и взета предвид в системата за управление. Въпреки това, повечето микропроцесорни контролни системи, които контролират параметрите на екструдираната полимерна стопилка, са по-скоро като набор от несвързани обратни връзки, всяка от които контролира само един параметър. По този начин такова устройство е проста комбинация от няколко регулатора в един пакет, без да се променя същността им. Такива регулатори могат да осигурят по-ниска цена, но не подобряват адекватността на управляваната верига.
Най-важните параметри на процеса на екструдиране са налягането и температурата. Те са най-точнипокажете колко добре функционира екструдерът. Сензорите за налягане и температура са тези, които първи реагират на промените по време на процеса.
Контролът на налягането на стопилката е важен поради две основни причини: контрол и мониторинг на процеса и от гледна точка на безопасността. Налягането в екструзионната глава определя характеристиките на екструдата. Именно това налягане е необходимо за преодоляване на съпротивлението, създадено от матрицата спрямо потока. Ако входното налягане не е постоянно във времето, тогава геометричните размери на екструдата също ще бъдат нестабилни. По този начин, чрез наблюдение на промяната в налягането, можем точно да определим дали процесът на екструдиране е стабилен или не.
Необходимостта от контрол на налягането също е продиктувана от съображения за промишлена безопасност, за да се предотвратят инциденти с експлозия при възникване на свръхналягане. С развитието на прекомерно налягане цевта на екструдера или матрицата може да се спука. И двете явления са много опасни и в никакъв случай не трябва да се допускат. Всички екструдери трябва да бъдат снабдени с устройства за защита срещу свръхналягане, като например свиващ се диск или срязващ щифт на задържащата скоба на матрицата. Но дори и с такива устройства, екструдерът трябва да бъде оборудван с поне един сензор за налягане, което ще направи по-вероятно да се избегне критична ситуация, особено в случай на неизправност на устройствата за защита от свръхналягане. Налягането може да се повиши много бързо без никакви симптоми и да причини катастрофални последици.
Добро решение е да използвате автоматичен превключвател на екструдера, когато се достигне критично ниво на налягане. При измерване на налягането е необходимо да се знае средното му ниво, но също така е важно и вВ някои случаи е необходимо да се записват колебанията на налягането във времето, тъй като обикновено промяната в размера на екструдата ясно корелира с промяната в налягането. Обикновено спадовете на налягането имат период по-малък от секунда, така че трябва да се използват достатъчно бързи сензори.Налягането в инсталацията за екструдиране се счита за около 390-400 бара.
В тази машина за екструдиране използваме сензор за свръхналягане DMK331PBDSensors, неговото свръхналягане е 0…400 bar, максималната температура е около 150 0C, което съответства на нашия проект.
Контролът на температурата се извършва в различни части на екструдера: по цялата дължина на цевта, в стопилката на полимера. Изборът на метод за измерване на температурата зависи от мястото и целта на измерването. За контрол на температурата се използват температурни сензори - термодвойки, обикновено се използват TXA или TPL. Зоните се поддържат при температура от приблизително 145-150 0 C. Те са свързани към устройства за автоматичен контрол на температурата, в този случай към Delta PLC.
Налягането и температурата са най-важните параметри на процеса на екструдиране, но някои други параметри не могат да бъдат пренебрегнати:
1. Скорост на шнека;
2. Дебелина на екструдата;
3. Качество на повърхността на екструдата.
За измерване на скоростта на винта се предлага да се използва сензор на Хол. Прикрепяме постоянен магнит към шайбата на двигателя, поставяме сензора на Хол срещу магнита, свързваме изхода на сензора на Хол към входа на Delta PLC. Полученият сигнал в сензора при влизане в магнитното поле на постоянен магнит се чете и променливите се записват в регистрите на контролера. След това от записания фрагмент изберете интервал от една секунда и пребройте броя на импулсите, след което умножаваме по 60 и получаваме числотообороти на двигателя в минута. Ние правим всички изчисления с помощта на програмата в контролера. Използва се промишлен сензор на Хол от серията A5S.
Сигналът на сензора може да се изчисли с помощта на програмата на контролера, поради пълното завъртане на шайбата на двигателя, можете да изчислите ъгловата скорост и да покажете графиката на панела HMISamkoon.
За измерване на дебелината на екструдата се използва оптичен сензор LS-5.
За измерване на дебелината на екструдата, сензорът има следната функция: има мъртва зона пред 10 mm фотодетектор, върху която не измерва. Сензорът измерва 20 мм. Тоест, регулира се токовият сигнал от 4-20 mA, в зависимост от позицията на проводника с екструдата. Този сигнал преминава през контролера, т.е. генерира се променлива, която се показва на HMI панела. Колкото по-малък е mm, толкова по-бавно работи захранващото устройство, толкова повече екструдатът се нанася върху проводника. В противен случай, обратното.
За оптичния сензор се използва специална програма за илюстриране на графиката на дебелината на проводника.
За да измерите необходимото качество на повърхността на екструдата, ще трябва да закупите няколко оптични сензора LS-5. И ги подредете последователно отгоре и отдолу (фиг. 1).
Фиг.1 - Качество на повърхността на екструдата
За измерване на дължината на проводника се използва инкрементален енкодер. За броя на импулсите можете да изчислите кадрите на жицата. Първо се изчислява колко разстояние ще бъде един пълен оборот на енкодера, тоест какво ще бъде равно на 1 импулс. След това всичко се изчислява и тези променливи се въвеждат в Delta PLC, след което се показват на екрана на HMISamkoon. В нашия случай се използва енкодер ES3-01CN6941.
Автоматизацията на екструдера е следната: в автоматичния контрол на физическите величини като налягане, температура,скорост на винта. Необходима е удобна индикация за тези стойности и удобна промяна на параметрите на панела HMISamkoon. Блоковата схема е показана на фиг. 2.
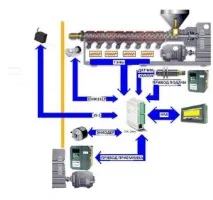
Фиг.2 - Структурна схема на управление на екструдера
В допълнение към контрола на температурата (нагряване/охлаждане) на отделните зони и показване на температурата на топене с всички контролни функции (забрана на пускане, контрол на винта, диапазон на толеранс, свръхтемпература (напр. изключване на охлаждане), се наблюдават съответните нагревателни токове. Налягането на стопилката също се измерва и следи. Осигурено е автоматично калибриране на сензора за налягане на стопилката DMK. Измервателните устройства за други параметри на периферното оборудване могат да бъдат свързани към системата чрез съществуващи връзки По този начин всички "класически" сигнали могат да бъдат оценени или коригирани на екструдера.
В представеното тук решение цялата автоматизация се извършва чрез компактен цветен дисплей и PLC, монтиран на DIN шина. Разпределение на I/O системи за цифрови и аналогови процесни сигнали и оборудване. Софтуерът на системата за управление на машината, потока на процеса и управлението вече е готов за работа и се нуждае само от проста конфигурация на дисплея според действителната ситуация (брой зони, задвижвания и т.н.). В нашия случай ние използваме програмата SamDraw 3.0 за програмиране на панела HMISamkoon. След това на екрана ще бъдат показани само необходимите работни параметри. Тоест програмираме в SamDraw броя на физическите променливи, които ще бъдат зададени при управление на екструдера. Следователно свързваме този панел с Delta PLC, тоест с тези променливи, които се записват в регистрите на този PLC и променяме всякапъти конфигурацията на физическите величини, от които се нуждаем. След това PLC събира данни от сензорите, които му дават друг алгоритъм на поведение, и следователно стойността се появява на HMI панела. След това PLC управлява честотните преобразуватели на захранващото задвижване и задвижването на приемника.
Екструзионната машина използва два честотни преобразувателя, 1-фазен и 3-фазен. 3-фазен честотен преобразувател е инсталиран на главното захранващо задвижване, 1-фазен честотен преобразувател е инсталиран на приемното задвижване.
Честотният преобразувател на захранващото устройство се използва за регулиране и поддържане на налягането в екструдера. Честотният преобразувател, инсталиран на задвижването на приемника, се използва за контрол на дебелината на екструдата; там се използва отрицателна обратна връзка.
Цената на елементите, използвани в производството, е 66866 рубли.
Резултатите, получени в работата, бяха използвани за модернизиране на екструзионната инсталация в предприятието IP Lerman MS, Армавир.
РЕФЕРЕНЦИИ
- Vent D.P., Magergut V.Z. „Изследване и разработване на адаптивни алгоритми за управление на екструдер, базирани на микрокомпютър“. Новомосковск, 1989. 40 с.
- Николайчук Н.О. "Съвременна автоматизация" - М.: SOLON-Press, 2003. 256 с.
- Rauwendaal "Основи на екструдирането" - Професия, 2006, 280 с.
- Стрепихеев А.А., Деревицкая В.А. "Основи на химията на високомолекулните съединения" - М .: Химия, 1976. 440 с.
- Тагер А.А. "Физикохимия на полимерите" - М .: Химия, 1978. 544 с.
- Шелепов В.М., Гуменчук Л.М., Мусин Н.М. "Автоматизация на контрола на налягането на стопилката по време на обработката на полимерни състави чрез екструзия" // Пластмасови маси. № 4, 1993. стр. 58-59.