Древна металургия - Студиопедия
Всъщност металургичното производство, т.е. процесът на извличане (извличане) на метали от руди произхожда от епохата на "неолитната революция" (10-6 хиляди години пр. н. е.), когато технологията за термична обработка на продуктите е усвоена от човечеството. Първите такива продукти бяха керамични, а първият термичен блок беше огън без принудителна тяга, осигуряващ температурно ниво от 600–700 °C. От този момент започва постепенно повишаване на температурния потенциал на цивилизацията, т.е. температурно ниво на термична обработка на продуктите и извличане на метали от руди.
Температурите, необходими за извличане на определени метали от руди и термомеханична обработка на основни материали и метали от древността, както и основните термични устройства (пещи), които осигуряват тези температури, са представени в таблица 2.
Таблица 2 - Температурно ниво на производство на основните материали от древността
и основни термични устройства
материал | Температурно ниво на производство, °C | Тип единица | Температурно ниво, °С |
бронз | 650-1100 | Пожар без принудителна тяга | 600-700 |
Керамика | 700-1200 | Gorn - пещ с принудително взривяване; предназначен за изпичане на керамика и тигелно топене на метали | 700-950 |
Олово и калай | 800-900 | "Вълча яма" - първият специален агрегат за добив на метали от руди | 900-1200 |
Мед | 750-1200 | Cheeseforge | Преди 1350 г |
Желязо | 1150-1450 | Пещ Домница и Телуел за топене на стъкло | Над 1350 |
Стъклена чаша | 1350-1700 |
Когато човек се научи да получаважелязо от руди, процесът на получаването му се състоеше в използването на сурови пещи и беше непродуктивен. Те започнаха да подобряват този процес - въведоха обогатяването на желязото с въглерод и последващото му втвърдяване. Така се правеше стоманата. И до 1-во хилядолетие пр.н.е. желязото е станало най-често срещаното сред материалите, използвани от човека (Европа, Азия) (Фигура 18).
Методите за производство на желязо (стомана) от руди в тигли, поставени в специални пещи (подобни на древните пещи, използвани за производството на керамични изделия), и в ями, които в Западна Европа получиха името "вълк", станаха първите в историята. И двата метода са металургични техники, наследени от по-рано овладяното производство на мед и бронз, със значителни подобрения, свързани с естествените различия в металните руди и тяхното поведение по време на топене. Топенето в тигел е обществен занаятчийски метод на производство, „домашна“ технология. С развитието на технологията за получаване на метали във "вълчите ями" металургията се превърна в първата истинска индустрия (Фигура 19). Въпреки това, до началото на новата ера, архаичната „вълча яма“ беше почти навсякъде заменена от много по-напреднала металургична единица - мина за сурови метали, докато тигелният процес на топене на желязо от руди беше доразвит (предимно в азиатските страни), тъй като направи възможно, макар и в малки количества, да се получи стомана с най-високо, дори по съвременни стандарти, качество.
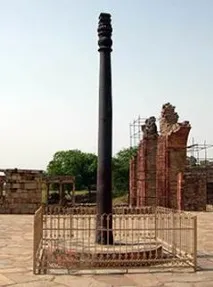
Фигура 18 - Желязна колона в Делхи (IV-V век от н.е.)
Разликите между металургичните единици, в които се обработва желязна руда от техните предшественици, са както следва:
1) за редуцирането на желязото от оксиди е необходимо значително по-голямо количество въглен, отколкото за топенето на медруди, където играе ролята само на източник на топлина;
2) дизайнът на огнището и технологията на топене трябва да са осигурили значително по-високо температурно ниво на процеса, тъй като отделянето на желязото и отпадъчната скала е възможно само след прехвърляне на един от материалите в разтопено състояние, в конкретен случай, след образуването на шлака.
Минималната температура за образуване на шлакова стопилка, чийто основен компонент е минералът фаялит (Fe2SiO4), е около 1200 °C. При производството на мед и бронз температурата в пещта е не повече от 1000 °C. Следователно, за да се повиши температурното ниво на процеса, беше необходимо да се използват по-мощни вентилатори или да се създадат условия за интензивен естествен въздушен поток. В древни времена те се опитват да намалят точката на топене на шлаката, като добавят специални флюсови добавки към заряда, например в Месопотамия и Мала Азия за тези цели още през 2-ро хилядолетие пр.н.е. използвана е смес от костна пепел и доломит. Този метод обаче може да даде осезаем ефект само в някои случаи и само при топене в тигел.
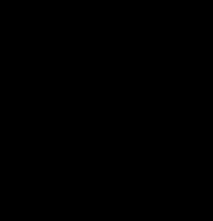
Фигура 19 - Яма "Вълк".
Тигелният метод за производство на ковък чугун, а по-късно и стомана, е широко разпространен още в древния свят. Склонността на европейската металургия към топенето на сурово желязо се проявява едва през последните векове на тази епоха. В Азия тигелното топене съществува като основна металургична технология до края на 19 век.
За топене в тигел се използват цилиндрични тигли с височина до 1,2 m и вътрешен диаметър до 12 cm (Фигура 20). Дебелината на стените варира от 2 до 4 см. Тигелите са направени от специална смес от пясък и топлоустойчива глина. Тигелите са правени по "шаблон" - платзарибяване. Те издържат на температури до 1650 ºС. Отгоре тигелите бяха затворени с полусферични капаци с отвори в централната част за отделяне на газове по време на топене.
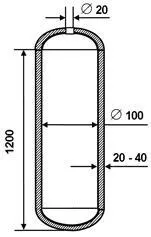
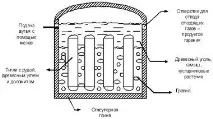
Фигура 20 - Дизайнът на тигела (а) и разположението на огнището за топене на тигела (б)
Съставът на заряда включва: желязна руда, дървени въглища и потоци, от които най-често се използва доломит. Всички шихтови материали бяха предварително натрошени до размера на лешник и старателно смесени. Сместа се зарежда в предварително изгорени тигли, които след това се поставят в огнище и частично се покриват с чакъл за стабилност.
Окончателният стоманен състав се образува в долната част на тигела в резултат на просмукване на метални капки през слой от предварително образувана и по-лека шлака.
След приключване на процеса тигелът остава в огнището до пълното му охлаждане. Охладеният метален блок се отстранява чрез счупване на тигела. Масата му рядко надвишава 2-3 кг, но това количество е напълно достатъчно за производството на острие или части от броня.
Тайната на високото качество на тигелната стомана беше дълготрайният контакт, първо на блума, а по-късно на разтопения метал, с желязната шлака. В същото време най-вредните от гледна точка на качеството на метала примеси преминават от метала в шлаката: фосфор и сяра.
Ковачницата (Фигура 21) стана първата металургична единица, специално проектирана за производство на желязо от руди. Дизайнът му е следствие от желанието на древните металурзи да увеличат интензитета на въздуха, влизащ в устройството, което е необходимо за повишаване на температурата на процеса.
Височината на ковачницата за сирене беше не повече от 1,5 м и лесно се поддържаше на ръка (Фигура 22).
Ковачница за сирене на около две трети от височината беше пълна с дървовъглища и едва след това се зареждаше. Върху горната част на огнището отново се поставят въглища, така че да се образува малка конусовидна възвишение. Дървените въглища се запалваха през канал за изхвърляне на шлака, който беше пълен с малки дърва за огрев и храсти. Подаването на взрив към огнището доведе до разпалване на въглища, чийто въглерод при липса на кислород изгаря до въглероден окис (CO). Така в пещта се създава редуцираща среда, която допринася за редуцирането на желязото от оксиди.
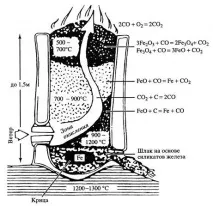
Фигура 21 - Общо разположение на ковачница за сирене
и диаграма на процеса
Температурата на нагряване на материалите в огнищата не надвишава 1300 ºС, което е недостатъчно за разтопяване на полученото при процеса нисковъглеродно желязо. Следователно продуктът на процеса беше "вик". Kritsa беше порест (подобен на гъба) материал - спечен желязо с неравномерен химичен състав с шлака.
Нагретите до пастообразно състояние пластмасови частици желязо, слепвайки се и споявайки се върху платиката на огнището, образували крица (от старославянската дума „крич” – ковач).
Порестата шлака, импрегнирана с желязна шлака, се изцежда, за да се отстрани под специални дървени преси в близост до огнището.
В резултат на процеса, който продължи около денонощие, се образуваха един или няколко поточета. В първите етапи на усвояване на технологията теглото на цъфтежа рядко надвишава 1-2 кг. По-късно обаче се научиха как да произвеждат криц с тегло 25-40 кг, а в най-продуктивните каталонски ковачници - до 120-150 кг.
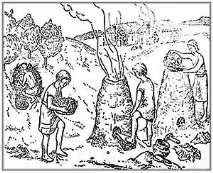
Фигура 22 - Работата на ковачниците за сирене
Шлаката постоянно изтичаше от пещта през специален канал в долната й част. Крайната шлака, изтичаща от пещта с сурово огнище, съдържа до 50–55% FeO, 10–15% Fe2O3(Fe2O3 се отнася до магнетит FeO-Fe2O3, преминаващ в шлака).
Съставът на крайната шлака от една от якутските сурови пещи е както следва, %: FeO - 48,5; Fe2O3 - 14,82; SiO2 - 23.01; A12O3 - 2,67; MnO - 3,48; CaO - 2,84; P2O5 - 0,87.
За сравнение, шлаката на съвременна доменна пещ съдържа 0,5–1,0% FeO, а от всеки 1000 kg заряд само 3–5 kg желязо преминава в шлака и 997–995 kg желязо в чугун. В ковачницата с грубо огнище не повече от 600–700 kg желязо преминават в металния цъфтеж от всеки 1000 kg Fe-заряд. Останалата част от масата на желязото (300–400 kg) не е възстановена и е изгубена безвъзвратно с изтичащата от огнището шлака.
Основността (CaO/SiO2) на шлаката от пещи с сурово огнище не надвишава 0,1–0,3; следователно десулфурирането на метала (FeS + CaO = CaS + FeO) почти не се извършва и сярата на заряда се превръща в крекинг. От чисти серни руди се получава висококачествен метал. Флаш нисковъглеродното желязо беше лесно изковано, но не позволи да се получат отлети продукти.
Необходимостта да се извлече цветът от ковачницата изискваше периодични спирания на ковачницата. Наложи се да се разбие предната стена на ковачницата, да се извади крицата и отново да се възстанови зидарията на ковачницата. Прекъснатостта и периодичността на суровото топене беше един от основните му недостатъци, което доведе до ниската производителност на пещите.
Пукнатината, извлечена от огнището с помощта на лостове или специални клещи, съдържаше голям брой включвания от шлака и неизгорели въглища. Поради това е обработен с дървени чукове, за да се отстранят гореспоменатите примеси. Едва след това започнаха термомеханична обработка на метала.
Ковачниците за сирене се отличават с голямо разнообразие от дизайни (Фигура 23).
в - преходна форма от "вълчата яма" към ниската ковачница; d - сурово издухано огнище от планински райониРумъния
Фигура 23 - Проекти на ковачници за сирене
Най-важните недостатъци на процеса на производство на сирене включват: ниска температура на зоната на изгаряне на въглища и степента на използване на газовата енергия, високо ниво на загуби на желязо със шлака и периодичност на процеса. По-нататъшното развитие на технологията за топене на желязна руда последва пътя на подобряване на дизайна на пещи с сурово огнище и отстраняване на недостатъците.
След предварителната обработка некованото сурово желязо беше доставено в ковачницата. Тук основният технологичен метод беше горещото коване. Ковашкото коване може да се извърши само с метал в пластично състояние, така че желязото се нагрява в ковачница. Скалата се отстранява със специални флюсове, които се поръсват върху местата на заваряване.
Не намерихте това, което търсихте? Използвайте търсачката:
Деактивирайте adBlock! и обновете страницата (F5)наистина е необходимо