Феромолибден
Молибденът се използва широко в производството на неръждаеми, топлоустойчиви, киселинно устойчиви, инструментални и други стомани и сплави под формата на феромолибден (Таблица 17) и калциниран молибденов концентрат, съдържащ най-малко 50% Mo, и по-рядко под формата на метален молибден.
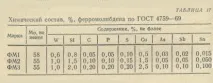
Суровини за производство на феромолибден
Съдържанието на молибден в земната кора е 3·10 -4%. Основният руден минерал (> 99% от производството) на молибден е молибденит - молибденов сулфид MoS2. Молибденовите минерали са разпръснати, а рудите, съдържащи 0,2% (понякога по-малко) молибден, подлежат на промишлена обработка.
Концентратите се получават в резултат на флотационно обогатяване или хидрометалургична обработка. Суров молибденов концентрат, съдържа
35% S. За отстраняване на сярата концентратът се подлага на окислително изпичане в пещи с много огнища. Тъй като MoO3 се характеризира с висока летливост, която се увеличава с повишаване на температурата, приетата гранична температура за изгаряне на концентрата е
680°C. Окислителната реакция протича с голямо отделяне на топлина, а външното нагряване, извършено в резултат на изгаряне на газ, е необходимо само в последния етап на печене, където концентрацията на сулфид вече е ниска. При 600°C MoO2 се образува съгласно реакцията MoS2(t) + MoO3(t) = 7MoO2(t) + 2 2>.
Калцинираният концентрат под формата на MoO2 съдържа 5–10% Mo. В същото време протича образуването на молибдати като CaMoO4, FeMoO4 и др. и окисляването на сулфидите на страничните метали. Образуваният в този случай SO2 при температури не по-високи от 600 ° C се окислява частично до SO3 и след това взаимодейства с метални оксиди, образувайки сулфатни соли, например Fe2 (SO4) 3, CuSO4 и др. Образуването на тези съединения е нежелателно, тъй като топенето ипелетизиране на концентрата, което влошава условията на работа на пещта и предизвиква увеличаване на съдържанието на калцинирания концентрат.
Условията за нормалното протичане на процеса на печене са равномерно натоварване и добро смесване на концентрата, достатъчно количество кислород и свободно отстраняване на серния диоксид от реакционната зона. Капацитетът на осемподова пещ с диаметър 6,8 m е 950 kg калциниран концентрат на час.
Калцинираният концентрат има приблизително следния състав: 80–90% MoO3; 3–8% FeO; 3–10% SiO2; 0,4-2% Cr2O3; 0,05–0,15% S и 0,02–0,15% P. След изпичане концентратът се смила до финост 2–0 mm. В случай на използване на концентрат за легиране на стомана, той се опакова в метален контейнер.
Като редуциращ агент се използва смес от феросилиций FS75, натрошен до фракция от 1 mm, и алуминиеви зърна с размер на зърното до 2 mm или феросиликоалуминий, съдържащ 10–14% Al и 76% Si + Al, под формата на зърна с размер до 1 mm.
Желязната руда трябва да съдържа не по-малко от 65% Fe под формата на Fe2O3 и не повече от 0,05% P и S. Рудата се изсушава и смила до размер на частиците не повече от 3 mm. Част от желязото се въвежда под формата на малки железни стружки, калцинирани за отстраняване на влага и масло. За втечняване на шлаката се използват флюси - вар и флуорипат.
Технология за производство на феромолибден
Молибденът е сребристобял метал със следните свойства: атомна маса 95,94, валентност 4 и 6, плътност 10,23 g/cm3, точка на топене 2622±10°C. Молибденът образува сплави с желязото във всякакви пропорции. В твърда форма молибденът образува FeMo и Fe7Mo6 съединения с желязото. Молибденовите оксиди имат ниска якост и могат лесно да се редуцират с въглерод, силиций и алуминий.
Възстановяване на молибден чрез въглеродреакциите 2/3(MoO3)+2Cst=2/3[Mo]+2 се провеждат лесно в електрическа пещ. Но този процес е свързан със значителни загуби на молибден и създава определени трудности при рафинирането на сплавта от въглерод, тъй като образуването на карбид M0C4 се извършва едновременно. Поради това в СССР се използва само металотермичният метод, като се използва силиций и частично алуминий като редуциращ агент. Процесът протича в съответствие със следните основни реакции:
По време на процеса на топене 99% от молибденовите оксиди се редуцират. Окисляването на силиций от оксиди на желязна руда е придружено от допълнително отделяне на топлина. Железните оксиди на рудата се редуцират с около 42% до желязо, останалата част се редуцира до FeO, който преминава в шлаката и допринася за нейното втечняване.
Концентратът на силициев диоксид и реакционните продукти на редукция на MoO3 и Fe2O3 със силиций образуват много вискозна шлака с високо съдържание на силициев диоксид. Намаляването на вискозитета на шлаката се постига чрез въвеждане в нея на FeO, флуор шпат и алуминиев оксид. Алуминиевият оксид се въвежда в шлаката чрез заместване на част от силиция с алуминий, което значително увеличава входящата топлина, води до повишаване на температурата на стопилката и намаляване на вискозитета на шлаката.
Изчисляването на заряда от условието за осигуряване на топлинния процес от 2030 kJ / kg (485 kcal / kg) дава приблизително следния състав на главата: 100 kg молибденов концентрат, 30 kg 75% феросилиций и 3,7–5 kg алуминиеви зърна или 38–39 kg феросиликоалуминий, 18 kg флуорошпат. 50 колоша се изразходват за един разгон.
Феромолибденът се топи в цилиндър (топилна шахта), облицован с шамотни тухли, поставен върху пясъчна основа с вдлъбнатина (гнездо) за приемане на течната сплав. Валът за топене има кранов отвор за източване на шлака. Отгоре шахтата е затворена с облицован свод с отвор за изпускане на газове. Зареден зарядуплътнен, което позволява да се увеличи извличането на молибден с 0,1%.
Топенето на феромолибден се извършва с горен предпазител, което намалява загубата на молибден. Обикновено топенето продължава 25-40 минути. Минимални загуби на молибден в шлаките се постигат при скорост на процеса 10–12 g/(cm 2 min). Оптималната температура на процеса е 1850-1950° C. Нормалният ход на технологичния процес се характеризира с обилно отделяне на газове от повърхността на горната част, шлаката образува нишки при освобождаване и вземане на проби и става стъкловидна при охлаждане; цветът му се променя от светлосин до тъмен.
След края на топенето следва 40-50-минутна експозиция за пълно утаяване на перлите от сплавта и след това шлаката се освобождава във формата или се гранулира. Шлаката има следния състав: 0,06–0,15 Mo; 62–68% SiO2; 7–11% FeO; 9-13% Al2O3; 6-8% CaO и 1-3% MgO.
Блокът от сплав се оставя в гнездото за 7-8 часа до пълно втвърдяване и след това за окончателно охлаждане се поставя в резервоар с вода за заключване. Тук сплавта се охлажда напълно в рамките на 4 часа. След това се раздробява на парчета с тегло до 5 кг, почиства се и се пакетира.
Най-важната задача на производството на феромолибден е да се осигури високо използване на молибден, което е 98,75% в местната промишленост. Това се постига чрез инсталиране на перфектна система за събиране на прах както от пещите, така и от шахтите за топене и чрез внимателно събиране и пълно изхвърляне на всички металосъдържащи отпадъци.
Извличането на молибден от отпадъци, съдържащи молибден, се извършва в електрическа пещ с капацитет 2,5 MVA, топене на блок с периодично отделяне на шлака. Получената сплав се претопява заедно със заряда по металотермичен метод. Богатите шлаки се отделят за извличане на молибденов концентрат, който се използва за претопяване. Отделнорециклирайте праха с извличането на съдържащите се в него олово и бисмут.
За да се получи 1 тон основата (60% месец) феромолибден, 1191 kg молибден концентрат (51% mO), 270 kg желязна руда, 230 kg стоманени чипсове, 362 kg 75% феросиликон, 57 kg алуминий, 265 вар, 30 kg флуорпапат са необходими при електролността, консумация на 800 kwh.