FT - Equipment_dlya_lk
Гранулатори (или преси)-механизми, чрез които се извършва гранулирането чрез претриване на масите през сито.
Гранулаторът (фиг. 9.1) съдържа работна камера (1), в която през захранваща фуния се подава влажният материал за гранулиране. Винтовете (3) са монтирани в камерата на два успоредни вала (2), снабдени с надлъжни пръти (4) и гребни колела (5), монтирани в противоположните краища на валовете. Шнековете се движат и избърсват материала през перфорирана плоча, която образува дъното на работната камера.
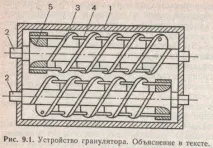
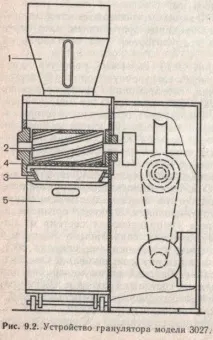
Гранулатор модел 3027 (фиг. 9.2), произведен в търговската мрежа от MNPO Minmedbiospetstekhoborudovaniye, има два работни тела и се използва за мокро и сухо гранулиране. Работното тяло на механизма за мокро гранулиране се състои от цилиндър, оборудван с три спирални лопатки с еволвентен профил (ъгъл на спиралата 80°), разположени под ъгъл спрямо оста на цилиндъра. Те елиминират слепването. Работното тяло на механизма за сухо гранулиране се състои от винт и шест търкащи се пръта, което ви позволява да премествате гранулирания материал в аксиална посока.
Инсталацията работи по следния начин: в бункера (1) се зарежда мокра маса или брикети, които, попадайки в работната зона, се прокарват през твърдо монтирана гранулираща мрежа (4) с помощта на работните органи (2) на механизма, въртящи се в противоположни посоки. В същото време е важно разстоянието между работното тяло на механизма и гранулиращата мрежа да бъде оптимално и да бъде в диапазона от 1,1-1,5 mm. Установено е, че колкото по-голяма е тази празнина, толкова повече прахообразни фракции ще има в гранулометричния състав на получения гранулат и толкова по-бавно той ще запълва матрицата, т.е.д. производителността на машината за ротационна преса и точността на масата на таблетката ще намалеят. Пюрираният гранулат пада надолу през направляващия бункер (3) в подвижен контейнер (5), който по време на работа се затваря с корпуса на гранулатора.
В зависимост от необходимия размер на гранулите се монтира една от взаимозаменяемите мрежи със съответния диаметър на отвора от 1 до 4 mm (интервалът на промяна на размера на диаметъра на отвора е 0,5 mm). Ако е необходимо да се осигури непрекъснатост на процеса, тази инсталация се използва с елеватори за зареждане на бункера и извозване на готовия гранулат до мястото на консумация.
Загранулиране на таблетни смеси в суспензионно леглошироко се използват агрегати от партиден тип, които включват сушилни гранулатори от типа SG-30 и SG-60, разработени от Ленинградската НПО Прогрес.
Принципът на действие на устройството SG-30 (503) и устройството му са показани на фиг. 9.7. Корпусът на апарата (11) е изграден от три изцяло заварени секции. Резервоарът за продукта (3) има формата на пресечен конус, разширява се нагоре и след това преминава в корпуса на пулверизатора (4), който е свързан с корпуса на ръкавния филтър (5).
Резервоарът с изходните компоненти на количката (1) се навива в апарата, повдига се от пневматичния цилиндър (2) и се запечатва със спрей-черупката. Въздушният поток се засмуква от вентилатор (8), задвижван от електродвигател (7), почиства се във въздушни филтри (12), загрява се до предварително определена температура в калорична единица (16) и преминава отдолу нагоре през въздухоразпределителна безканална решетка, монтирана в долната част на резервоара за храна. В този случай продуктът влиза в суспендирано състояние - той се смесва. След това в кипящия слой на първоначалните компоненти от резервоара (14) от дозиращата помпа (13)гранулиращата течност се подава през дюзата и таблетната смес се гранулира. Сгъстеният въздух, подаван към пневматичната дюза чрез специална система (15), се използва не само за пръскане на гранулиращата течност, но и за дистанционно управление на дюзата. По време на гранулирането, ръкавните филтри се разбъркват автоматично. Разклащащото устройство (6) е електропневматично свързано с устройството, което изключва щорите (10). Когато ръкавните филтри се разклатят, амортисьорът затваря флуидизиращия въздух към вентилатора, като по този начин спира флуидизацията на продукта и премахва въздушното натоварване от ръкавните филтри. Чрез разклащане филтрите се почистват от продукта под формата на прах, който след това се гранулира. В изходната част на вентилатора има шибър (9) с механизъм за ръчно управление. Той е предназначен да контролира флуидизиращия въздушен поток. След определен период от време спрей системата се изключва и започва сушенето на гранулата. Устройството работи в автоматичен режим. Релето за време осигурява последователността и необходимата продължителност на операциите, както и синхронната с него цикличност и продължителност на процеса на разклащане на ръкавните филтри и работата на клапата. В края на целия цикъл на гранулиране, вентилаторът автоматично се изключва и подаването на пара към калоричния модул спира. Резервоарът за храна се спуска. Количката заедно с резервоара се разточва, от сушилнята гранулатът се подава към таблетиране. Използването на инсталации тип SG осигурява редица предимства: съкращаване на производствения цикъл, в повечето случаи той продължава 25-45 минути (вместо 11-30 часа); намаляване на броя на използваното оборудване (от 5 на 2 вида) и съответно намаляване на производствените площи с почти 50%;намаляване на сложността на процеса, тъй като се елиминират редица ръчни производствени операции. Трябва също така да се отбележи, че във флуидизирания слой гранулатът е по-хомогенен по фракционен състав от този, получен чрез метода на щанцоване. По-голямата част от гранулите (60-80%) е с размер от 0,25 до 1,5 mm. Този гранулометричен състав допринася за по-равномерна работа на таблетните преси. Спецификата на всяко лекарствено вещество обаче е такава, че според веднъж разработената технология за гранулиране с помощта на SG единица не е възможно да се гранулира друго вещество в този режим. Необходимо е отново да се разработят режимите, да се определи количеството, качеството, скоростта на подаване на гранулиращата течност и др.
Оборудване за сухо гранулиране
Най-обещаващи са комбинираните инсталации, които комбинират процесите на уплътняване, смилане и отделяне на получените гранули. Диаграма на такава инсталация е показана на фиг. 9.9. Сместа от прахове за гранулиране се зарежда от захранващото устройство (11) през тръбопровода (9) в смесителя (8), където се смесва и се подава от шнека (7) към ролковата преса (6). Преминавайки през ролките, необходимото разстояние между които се задава от контролното устройство (5), масата се пресова под налягане и след това предварително се смила в ударна мелница (4). Натрошеният материал постъпва в самия гранулатор (3) и преминава през неговата мрежа (10). Готовите гранули се разделят по големина на вибрационно сито (2). Гранули с необходимия размер се събират в контейнер (1) за по-нататъшно таблетиране, а останалите - твърде големи гранули и прахова фракция - се връщат в миксера през тръбопровода.
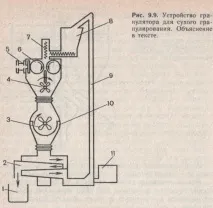
Фирма F
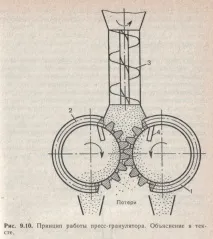
Същността на метода се състои в това, че гранулите, получени чрез пресоване през сито в гранулатор, се подлагат на валцуване до сферична форма в специален апарат - мармеризатор (мармеризатор) (фиг. 9.11 и фиг. 9.12), който представлява неподвижен вертикален, отворен отгоре цилиндър с гладки стени. Вътре в цилиндъра в основата се върти гофрирана плоча със скорост 400-1600 rpm, чиято повърхност е покрита с вдлъбнатини от 2-4 mm. В мармеризатора постъпва цилиндричен гранулат с форма на фиде, получен чрез прекарване на пластмасовата маса през радиално или крайно сито. При него цилиндрите се раздробяват на парчета с дължина, равна на диаметъра на гранулата, и се валцуват до сферична форма под действието на центробежни и триещи сили. Времето за разработка на гранулите е средно 2 минути, производителността е до 20 000 kg/h.
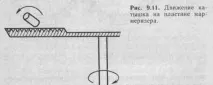
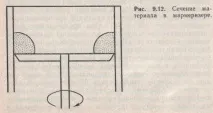
Сушене на гранулата.В домашни условияВ химическата и фармацевтичната промишленост се използват сушилни от този тип, разработени от LNPO Progress и предназначени за сушене на таблетни гранули, които не съдържат органични разтворители.
Заводът в Пенза "Dezhimoborudovaniye" произвежда сушилни SP-30, SP-60, SP-100, където цифрите показват номиналното натоварване на изходния материал в килограми.
C
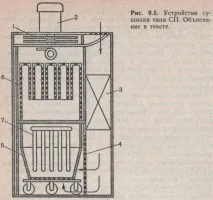