Използването на полимерни материали при възстановяването на части, MOT и TR на автомобила
Главна информация
Полимерните материали се използват широко при ремонт на машини. Те имат широк спектър от положителни свойства:
- добри триещи и антифрикционни свойства
- достатъчна здравина
- устойчивост на масло, бензин и вода
- запазване на формата на частта
- способност да издържат на определено натоварване и температура
- лекота на възстановяване и производство на части и др.
Притежавайки ценни физични и механични свойства, полимерните материали могат да намалят трудоемкостта на ремонта и поддръжката на машини с 20-30% и да намалят консумацията на дефицитни материали (черни и цветни метали, материали за заваряване и настилка, спойка и др.) С 40-50%. Недостатъците на полимерните материали включват промяна в техните свойства в зависимост от експлоатационния живот (стареене), относително ниска твърдост, якост на умора и устойчивост на топлина.
Следните полимерни материали се препоръчват за използване при ремонт на машини: поликапроамид (капрон), полиетилен, полистирол, полиамид, фибростъкло, епоксидни смоли, синтетични лепила, уплътнители, анаеробни полимерни материали и др. Промишлеността произвежда специални комплекти за първа помощ и комплекти от полимерни материали за ремонт на машини.
Използването на полимерни материали не изисква сложно оборудване и висококвалифицирани работници. Възможно е в условията на специализирани ремонтни предприятия, в работилници на ферми, както и на полето.
Използването на епоксидни състави при възстановяването на части
Епоксидните смоли в тяхната чиста форма се използват много рядко. В ремонтната практика се използват епоксидни съединения, които са многокомпонентни системи. Най-важнитеПредимството на състава пред полимерите е тяхната повишена твърдост и якост, стабилност на размерите, повишена якост на удар, контролирано триене и други свойства. Въпреки това е невъзможно да се постигнат всички тези свойства в един състав.
В допълнение към епоксидната смола, в зависимост от предназначението, съставът може да включва пластификатори, пълнители, втвърдители, ускорители на втвърдяване, пигменти и други компоненти.
Пластификаторите намаляват чупливостта и устойчивостта на резки промени в температурата, но намаляват топлопроводимостта. Най-често използваният пластификатор е дибутил фталат.
Пълнителите се въвеждат за подобряване на физичните и механичните свойства, намаляване на вътрешните напрежения, произтичащи от разликата в коефициентите на линейно разширение на метала и полимера. Пълнителите се разделят на свързващи (фибростъкло, тъкани) и прахообразни (железен прах, алуминиев прах, цимент, талк, графит и др.).
Като втвърдител за епоксидни смоли по-често се използва полиетиленполиамин.
Епоксидните състави са универсален ремонтен материал. Използват се за запечатване на пукнатини, черупки, дупки, възстановяване на подвижни и неподвижни съединители, залепване на части. Съставът на състава зависи от необходимите свойства и условия на работа. За фиксиране на втулки, пръстени, винтове по време на възстановяване с помощта на ремонтни допълнителни части се използва състав без пълнители. За 100 части (тегловни) епоксидна смола ED-16 се вземат 10 части дибутилфталат и 12 части полиетилен полиамин. При запечатване на пукнатини, дупки, възстановяване на места за лагери, пълнители се въвеждат в състава.
Приготвянето на състава е както следва. Епоксидната смола в контейнер се нагрява до температура 70-80 ° C, отлива сенеобходимото количество в съда, добавете пластификатор и смесете двукомпонентния състав. След това, ако е необходимо, се добавя пълнител, предварително изсушен за 2-3 часа при температура 100-120 ° C и съставът се смесва добре. Втвърдителят се добавя преди употреба на състава.
Приготвеният състав трябва да се използва в рамките на 20-25 минути.
Запечатване на пукнатини и дупки
Епоксидните състави се използват за запечатване на пукнатини в части на тялото, които не преминават през отвори за втулки, седалки за лагери, резбови отвори с дължина не повече от 200 mm. След определяне на размерите на пукнатината, ръбовете й се пробиват със свредло с диаметър 3 mm, а пукнатината по цялата дължина се нарязва под ъгъл 60-70 °, на дълбочина 2-3 mm (с дебелина на стената над 5 mm). Ако дебелината на стената е по-малка от 2 мм, пукнатината не се изрязва. Повърхността на детайла се почиства до метален блясък на разстояние 40 mm от двете страни на пукнатината и се обезмаслява с ацетон. Приготвеният състав се нанася върху повърхността и се уплътнява със шпатула. За запечатване на малки пукнатини (до 20 мм) се използва състав без пълнител. При възстановяване на чугунени части с отвори и пукнатини по-дълги от 20 mm се използва следният състав. За 100 части (тегловни) смола ED-16 се вземат 15 части дибутилфталат, 120 части железен прах и 11 части полиетилен полиамин. За възстановяване на частите на тялото, изработени от алуминиеви сплави, вместо железен прах, като пълнител се използва алуминиев прах (25 части).
Пукнатина с дължина 20-150 mm върху частите на тялото или резервоарите е запечатана с епоксиден състав, подсилен с фибростъкло или технически калико. Първото платнено покритие трябва да покрива пукнатината с 20-25 mm от двете страни, а второто трябва да покрива първото с 10-15 mm. След нанасянена първия слой от епоксидния състав, първият слой се нанася и се навива с валяк. Тънък слой от състава се нанася върху повърхността на наслагването и се нанася втори слой, който също се навива с валяк. На второто наслагване отново нанесете слой от състава и оставете да се втвърди.
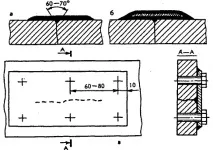
Ориз. Опции за запечатване на пукнатини: а - епоксиден състав; b - епоксидно съединение, подсилено с фибростъкло; c - епоксиден състав и метално покритие.
Пукнатини на частите на тялото с дължина над 150 мм се запечатват с облицовка от стоманена ламарина с дебелина 1,5-2,0 мм. Почистените повърхности на частта, облицовката и винтовете са покрити с епоксиден състав.
Съставът се втвърдява при температура 18-20 ° С "в продължение на 72 часа. Оставя се да се втвърдява при температура 20 ° С" в продължение на 12 часа и след това съгласно един от следните режими: при 40 ° С "- 48 часа; при 60 С" - 24 часа; при 80 С" - 52 часа; при 100 С "- 3 часа.
Дупките в частите на тялото, радиаторните резервоари, резервоарите за гориво са запечатани чрез припокриващи се лепенки с помощта на епоксидни състави. За малки дупки облицовката е от фибростъкло. Тънкостенните части се възстановяват чрез нанасяне на ламарина. Дупките в частите на тялото са запечатани чрез припокриване на метална облицовка върху винтовете. Стоманената подложка може да бъде фиксирана с епоксидно съединение, проникващо в допълнителните отвори за пробиване.
Ремонт на монтажни отвори
Епоксидните състави се използват при ремонта на неподвижни интерфейси на части като корпус - лагер, корпус - втулка, ако празнината в интерфейса не надвишава 0,1 mm. Преди нанасяне на състава, свързващите повърхности на отвора в корпуса, втулката (лагер) се почистват и обезмасляват. След изсъхване нанесетесъстав (без пълнител) върху подготвени повърхности със слой с дебелина не повече от 0,5 mm. След 10-15 минути втулката (лагерът) се притиска в отвора и се извършва втвърдяване съгласно един от горните режими.
Лепене на части със синтетични лепила
За лепене се използват лепила ВС-ЮТ и типове BF, 88N и др.. Лепилото ВС-ЮТ се използва за лепене на накладки към спирачни накладки и дискове на съединителя. Освен това може да се използва за залепване на метали, фибростъкло и други материали. Режим на втвърдяване: налягане на пресоване на залепените повърхности - 0,2-0,4 MPa, температура - 175-185 ° C, продължителност - 1,5-2,0 часа.
Лепила BF-2, BF-4, BF-6 се използват за лепене на метали, дърво и др.
Лепилото BF-6 дава по-еластични връзки, така че се използва за лепене на филц, филц, тъкани и други материали. Режим на залепване: налягане - 0,5-1,0 MPa, температура - 140-160 ° C, продължителност - 1,0-1,5 часа Лепилото BF-52T се използва за същите цели като лепилото VS-YUT.
За свързване на каучук и каучук с метал се използва лепило 88N.
Повърхностите за лепене се почистват от замърсявания и стари полимерни материали. Металните повърхности се почистват до метален блясък и се обезмасляват с ацетон или бензин. След изсъхване на частите върху залепваните повърхности се нанася слой лепило с дебелина 0,10-0,15 mm и се държи на стайна температура за 10-15 минути. След това се нанася втори слой лепило и частите се изсушават. Краят на сушенето се проверява "за лепкавост". Върху лепилния слой се нанася гумена пръчка, почистена с ацетон. Ако не залепва, повърхностите за лепене се поставят една върху друга и се притискат със специални приспособления. Детайлът, заедно с приспособленията, се поставя в специален шкаф за термична обработка (втвърдяванеадхезивен състав) и се инкубират за 40 min. За да се намалят остатъчните напрежения в залепващата връзка, частите се охлаждат заедно с корпуса до температура 80-100 ° C, а след това на въздух до температура 20-25 ° C за 2-3 часа и се отстраняват от приспособленията.
Чрез тази технология фрикционните накладки се залепват към спирачните накладки и дисковете.
Използването на еластомери при възстановяването на кацанията
Ремонтът на лагерните възли често се състои във възстановяване на първоначалната плътност. Нарушаването на прилягането допринася за смачкване на повърхностни неравности по време на пресоването и отстраняването на лагерите и поради въртенето на лагерния пръстен по време на работа на машината. За възстановяване на места за лагери в отвори и на валове, както и за втулки и зъбни колела с износване не повече от 0,06 mm се използват еластомери GEN-150 (B) или 6F.
Технологичният процес включва следните операции: подготовка на разтвора, почистване и обезмасляване на износени повърхности, нанасяне на разтвора върху подготвени повърхности, термична обработка и монтаж на възли. Разтворите се приготвят по следната рецепта: една част (тегл.) еластомер GEN-150(B) и 6,2 части ацетон; или 2 части еластомер 6F, 5 части ацетон и 5 части етил ацетат.
Еластомерният разтвор се нанася върху повърхността на детайла в аспиратор с четка. При нанасяне на разтвора не се допуска припокриване на слоеве. Дебелината на филма на един слой е 0,01 мм. Намазаната част се държи 20 минути, след което се поставя за термична обработка във фурна. Термичната обработка се провежда при температура 120 С за 30 минути. Всеки следващ слой до необходимата дебелина се нанася след термична обработка на предходния. Преди монтаж повърхността на частта, покрита с еластомер, се смазва с графитна грес, женската част се нагрява дотемператури 120-140°C.