Клапанно устройство
По дизайн вентилите са успоредни и клиновидни, с прибиращ се и фиксиран шпиндел. Шибърите осигуряват малко хидравлично съпротивление на потока на средата. Вода, пара или газ могат да се подават във вентила от всяка страна.
Паралелният шибър е изработен от чугун, като тръбопроводът е свързан с помощта на фланци с болтове. Има корпус с капак и свободно монтирани на шпиндела дискове. Между дисковете е монтиран дистанционен клин. При завъртане на маховика по посока на часовниковата стрелка шпинделът се спуска заедно с дисковете, клинът, опрян в тялото, раздалечава дисковете, които се притискат към бронзовите пръстени в тялото и затварят прохода към средата. За да затворите плътно клапана, дисковете и пръстените в тялото се търкат. Когато ръчното колело се завърти обратно на часовниковата стрелка, шпинделът с дискове се издига, клинът се спуска, дисковете и клапаните се отварят.
Успоредните шибъри се произвеждат с диаметър 50, 80, 100, 125, 150, 200, 300, 400 mm.
Клинови стоманени шибъри се използват за вода и пара с работно налягане до . изработват се без редуктор с , с редуктор и ел. задвижване .
В клиновидни шибъри проходният отвор е блокиран от клинов кръгъл диск. Дискът се поставя между ъгловите О-пръстени на тялото. Когато ръчното колело се завърти, шпинделът движи диска с помощта на гайка, отваряйки или затваряйки прохода.
При клапаните с повдигащо се стебло, повдигащото се стебло се върти с ръчното колело. Краят на шпиндела и дисковете са с резба. Когато маховикът се върти, шпинделът също се върти, резбовите дискове се издигат или падат, отваряйки или затваряйки прохода.
Шпинделът е уплътнен в точките на преминаване през капака на корпуса и в двата случая чрез уплътнение на салника.
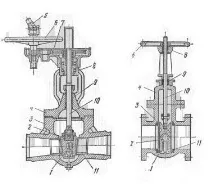
Уловителите за конденз са предназначени за събиране и последващо отстраняване откондензен газопровод, както и за отстраняване на вода, попаднала в него по време на строителство, промиване и др. Кондензните колектори се монтират в най-ниските точки на газопровода. Течността от газопровода навлиза в колектора на кондензат чрез гравитация. Кондензатният уловител се състои от колектор, монтиран под газопровода, свързан с него чрез дренаж за кондензат, тръба за продухване със спирателни вентили и устройство за автоматично отстраняване на течността. Както и линия за изравняване на налягането. Кондензните колектори се изработват от тръби и фабрично изработени части. Диаметърът и дебелината на стената на кондензните колектори се определят чрез изчисление. Кондензните колектори се покриват с антикорозионна изолация, съответстваща на изолацията на тръбопровода в този участък, и се подлагат на предварителен хидравличен тест за налягане, равно на едно и половина работно налягане в газопровода. Колекторите на кондензат периодично се освобождават от кондензат в мобилни резервоари, а също така е възможно да се изпомпва кондензат до най-близкия нефтопровод. На газоразпределителните тръбопроводи се монтират кондензни колектори за отстраняване на изпадащия в тях конденз. Има колектори за конденз с ниско, средно и високо налягане.
5.5 Свързване на тръби и фитинги на газопроводи.
Според метода на свързване към тръбопровода газовите фитинги се разделят на фланцови, съединителни, щифтови и фитинги с краища за заваряване.
Фланцовите връзки са най-често срещаните връзки. Обикновено се използват плоски заварени фланци. Според условното налягане те се делят на 6;10;16; и 25 и челно заварени фланци с перваза тип А и с кухина тип В. За уплътняване на фланцовата връзка се използват уплътнителни материали, изборът на които зависи от налягането в газопроводите.
За налягания до 16 се използва паронит от марката PMB с дебелина от0,2-6 мм. При ниско налягане се използва уплътнителен картон клас B. Уплътнението трябва да бъде смажено с графитен прах преди монтажа.
При монтаж и демонтаж на фланцовата връзка се спазва следната процедура. Демонтажът се извършва след пълно спиране и прочистване на газопровода. Демонтажът започва от долната точка встрани от вас, като разхлабвате резбовата връзка "кръст-кръст" с 3 резби.
Сглобяването започва след центроване и изправяне по същия начин като разглобяването. При правилно сглобен фланец болтът или шпилката трябва да стърчат от гайката с поне 3-4 нишки, не трябва да има изкривявания, уплътнението не трябва да има изпъкнали части.
Щифтова връзка е връзка със съединителна гайка, резбова връзка. Резбовата връзка трябва да бъде запечатана, за това се използват уплътнителни материали, като FUM лента, лен, импрегниран с цинково бяло.
5.6 Ремонт и поддръжка на газова арматура.
. Текущият ремонт на спирателната арматура включва следните работи: - почистване на арматурата от мръсотия; - боядисване (при необходимост); - ускоряване на винта на клапана и неговото смазване; - проверка и пълнене на епиплон; - проверка на изправността и ремонт на задвижващото устройство на ключалките; - проверка на херметичността на всички заварени, резбови и фланцови съединения със сапунена емулсия или уред; - смяна на износени и повредени болтове и гарнитури. Тест за течове. Годността на арматурата за работа се потвърждава чрез хидравличен тест за якост и плътност на метала и за херметичност на ставите. Армировката се подлага на хидравлично изпитване в процеса на производство на детайли преди и след тяхната обработка, както и в готов вид. Такива тестове се извършват по време на ремонта на арматурата, както и преди монтажа на тръбопровода (в заводите за доставка за монтажорганизации).
Частите на армировката се изпитват за якост и плътност при изпитвателно налягане, когато въздухът е напълно отстранен от кухината на армировката. Фитингите обикновено се тестват при 20. °C със запушени проходни отвори. Излятите части се почукват с оловен или меден чук с тегло 0,8. 1 кг.
Не се подлагат на хидравлично изпитване армировка с незаварени пукнатини и черупки, прорези и люспи по крайните равнини на уплътнението, заваръчни фаски на краищата на тръбите и отвори за опорни пръстени, както и с прорези и скъсвания на резба на болтовете.
Тестът за херметичност определя степента на прилягане на уплътнителните повърхности (херметичност) на тарелката и леглото на клапана
Контролни въпроси: 1. Класификация на газовата арматура? 2. Изисквания към газовата арматура? Характеристики на ремонта на газови арматури? 4. Какво включва текущият ремонт на арматура? 5. Устройство с клинов клапан? 7. Ред за опаковане за опаковане на жлеза?
Глава 6. Ремонт на газорегулаторни пунктове и инсталации.
6.1 Предназначение и схема на газорегулаторни пунктове и инсталации.
Газови контролни точки (инсталации) е комплекс от технологично оборудване и устройства, предназначени да понижат налягането на входния газ до предварително определено ниво и да го поддържат постоянно на изхода.
В зависимост от местоположението на оборудването, контролните пунктове за газ се разделят на няколко типа: - блок за регулиране на газ (GRU) - оборудването е монтирано на рамка и се намира в помещението, в което се намира газовата инсталация, или в помещението, свързано с него чрез отворен отвор; - шкафова газорегулаторна станция (ГРПШ) - оборудването се поставя в шкаф от огнеупорни материали; - блокова газова контролна станция (GRPB) -оборудването е инсталирано в една или повече сгради от контейнерен тип.
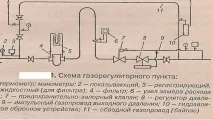
В зависимост от налягането на газа на входа на хидравличното разбиване (GRU) има средно (повече от 0,05 до 3 kgf / cm 2) и високо (повече от 3 до 12 kgf / cm 2) налягане. В съответствие с назначението в GRP (GRU) се поставя следното оборудване:
1) Регулатор на налягането, който автоматично понижава налягането на газа и го поддържа в контролирана точка на дадено ниво (наричан по-нататък регулатор);
2) Предпазен спирателен вентил (ПЗК), който автоматично спира подаването на газ при повишаване или спадане на налягането му над определените граници. Монтира се пред регулатора по посока на газта;
3) Предпазно предпазно устройство (PSU), което изхвърля излишния газ от газопровода зад регулатора в атмосферата, така че налягането на газа в контролираната точка да не надвишава определеното. Свързват се към изходящия газопровод, при наличие на разходомер - зад него. В хидравличните разпределителни станции в шкафа е разрешено преместването на PSU извън шкафа4
4) Филтър за пречистване на газове от механични примеси. Монтира се пред ПЗК. Филтърът не може да бъде инсталиран в GRU, разположен на разстояние не повече от 1000 m от газоразпределителния блок или централизираната точка за пречистване на газ на предприятието;
5) Обходен газопровод (байпас) с последователно разположени спирателни (първи в газовия поток) и спирателни и контролни устройства за подаване на газ през него за периода на ревизия и ремонт, както и аварийното състояние на оборудването на редукционната линия. Диаметърът на байпаса трябва да бъде поне толкова голям, колкото диаметъра на гнездото на регулатора4
6) Измервателни уреди: налягане на газа пред регулатора и зад него - показващи и самоотчитащи се манометри; диференциално налягане през филтъра - диференциален манометър; термометри за температурата на газа - показващи и самосигнални. При хидравлично разбиване на шкафа не се допускаинсталирайте записващи устройства, а в GRP (GRU), в които не се отчита газовият поток, записващо устройство за измерване на температурата;
7) Импулсни тръби за свързване на регулатор, PZK, PSU и измервателни уреди с тези точки на газопроводи, където се контролира налягането на газа;
8) Изпускателни и продухващи тръбопроводи за изхвърляне на газ в атмосферата от PSU и продухване на газопроводи и оборудване. Тръбопроводите за продухване се поставят на входния газопровод зад първото спирателно устройство, на байпаса между две спирателни устройства, в зони с оборудване, което е изключено за рутинна проверка и ремонт;
9) Заключващи устройства. Броят и местоположението на заключващите устройства трябва да осигуряват възможност за изключване на хидравличното разбиване (GRU), както и оборудване и измервателни уреди за тяхната ревизия и ремонт без спиране на подаването на газ.
При хидравличното разбиване (GRU) на котелна централа със схема за подаване на газ в задънена улица основното технологично оборудване се настройва въз основа на следните условия.
Регулаторът трябва да поддържа налягане pn=pr+∆p в контролираната точка, където pr е налягането на газа пред горелките на котела, ∆p е загубата на налягане на газа в участъка на газопровода от точката на свързване на манометъра пред горелката, най-отдалечена от хидравличното разбиване (GRU) до контролираната точка при максималния изчислен дебит на газ.
Устройството за затваряне е настроено да се задейства, когато налягането в контролираната точка се увеличи до pv = 1,25pp. В същото време pv не трябва да надвишава максимално допустимото налягане пред горелките, което осигурява тяхната стабилна (без отделяне на пламъка) работа.
Затварящият клапан е настроен да се задейства, когато налягането в контролираната точка спадне до pc, което осигурява (като се вземат предвид загубите ∆p) налягането пред горелката с 20-30 kgf / m 2 (ниско налягане) или 200-300 kgf / m 2 (средноналягане) е по-голямо от това, което е посочено като минимално допустимо в паспорта на горелката или, при липса на такива индикации, при което, според данните на организацията за въвеждане в експлоатация, горелките могат да изгаснат или да възникне обратен удар.
PSU е настроен за пълна работа, когато налягането в контролираната точка се повиши до pp = 1.15pn
Схема GRP-B с две редукционни линии, с отоплителна система без газомер.
1 - Регулатор на налягането на газа 2 - Предпазен спирателен вентил (ПЗК) 3 - Газов филтър 4 - Предпазен клапан 5 - Регулатор на налягането на газа за захранване на отоплителния котел 6 - ПЗК 7 - Манометри 8 - Манометър 9 - Кранове за налягане 10 - Газомер за отоплителен котел 11 - Газов електромагнитен вентил 12 - Котел 13 - Отоплителни радиатори 14 - Газ детектор
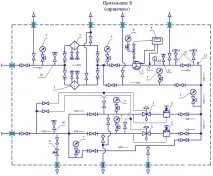