Количествено определяне на технологичността
Технологичността на конструкцията може да бъде обективно оценена чрез изчисляване на количествените показатели за технологичност съгласно GOST 14.201-73 и GOST 14.204-73.
Съгласно GOST 14.201-73 е осигурен значителен диапазон (22) от количествени показатели. Количествените показатели за технологичност се делят на основни и допълнителни.
A.Основните индикатори са:
1. Абсолютната стойност на трудоемкостта на продукта Tu. Опитът показва, че трудоемкостта на механичната обработка по отношение на общата трудоемкост (по отношение на специфичното тегло в%) е стабилна за един и същ вид продукти. Следователно за сравнителна оценка е достатъчно да се определи трудоемкостта на механичната обработка.
2. Абсолютната стойност на технологичните разходи за производство на продукт Ct.u.. Най-добре е технологичността да се оцени по себестойност. Но в същото време трябва да се помни, че изчисляването му не в производствени условия, а по време на проектирането е много трудоемко.
3. Индикатор за степента на технологичност по отношение на сложността на изработката
където Tu и Tu.B. - очакваната трудоемкост на производството на нов продукт и трудоемкостта на базовия показател.
4. Показател за нивото на технологичност по техническа цена
където св.и. и св.и.б. - очакваната техническа цена на проектирания продукт и цената на базовия продукт.
Б.Допълнителните показателиза технологичност включват редица частни и сложни, абсолютни и относителни показатели, които оценяват дизайна както от икономическа, така и от техническа страна.
1. Коефициент на използване на материала
..
къдетоmu е масата на продукта; Smз - сумата от масите на заготовките,q- масата на детайла;Q.– тегло на детайла.
2. Специфична трудоемкост на изработка на продукт
,
където P е параметърът на продукта (мощност, тяга, маса на конструкцията и т.н.). Тогаваtи ще изрази разходите за труд за единица мощност и т.н.
3. Единична цена
,
където C е общата цена на производството на продукта.
4. Специфична технологична себестойност
,
където Sti е общата технологична цена за производство на продукта.
5. Коефициент на унификация и стандартизация на частите:
където Kud е коефициентът на обединение на части; Kue - коефициент на обединение на структурните елементи; Кп.ст - коефициент на приложимост на стандартизирани обработени повърхности;Nud,Nsd – брой унифицирани и стандартни части;Nue,Ne - съответно броят на унифицираните конструктивни елементи на детайла и общия брой, бр.; Dos, Dmo - съответно броят на повърхностите на частта, обработени със стандартен инструмент, и всички повърхности, подложени на механична обработка, бр;Nd - общият брой части.
6. Коефициентът на повторяемост на структурните елементи
,
къдетоNn - броят на наименованията на съставните части на структурата;Nk - общият брой компоненти на структурата.
7. Коефициент на повърхностна обработка
,
където Dmo е броят на повърхностите, подложени на механична обработка; Te е общият брой на повърхностите.
8. Тегло на детайлаq, kg.
9. Максималната стойност на качеството на ИТ обработката.
10. Максималната стойност на параметъра за грапавост на обработени повърхностиRa.
11. Коефициентът на прилагане на типичните технологични процеси при производството на тази част (получаване на детайл от механична, термична и друга обработка)
където Qtp, Qe- съответно броят на типичните технологичнипроцеси за производство на части и общи, бр.
Нивото на технологичност на конструкцията на частта Ku се определя като съотношението на постигнатия показател за технологичност към основния, посочен в заданието
където K е постигнатият (прогнозиран) показател за технологичност; KB е основен показател за технологичност, който обикновено се определя от данните на основната част.
Осигуряването на технологичност на дизайна на частите при обработката им на машини с ЦПУ има характеристики, които се дължат на възможностите на машините с ЦПУ.
С машините с ЦПУ дизайнерът може да създава форми на части, които се описват от сложни извити повърхности, които точно съответстват на изчисленията. В този случай не е необходимо тези форми да се опростяват с елементарни прави участъци. По този начин е възможно да се увеличи здравината на машините, да се намали теглото им, което е от съществено значение за различни самолети. Като цяло, тестването за технологичност подобрява точността и производителността на обработката, намалява разходите за изчисляване и изготвяне на програми. Последното обстоятелство е важно за подготовката на производството в рамките на ASTPP.
Анализът на производствения опит ни позволява да формулираме основните изисквания за технологичност на частите:
1. За струговане на части - комбиниране на няколко прости части в една сложна:
- приближаване на формата на заготовката до изчислената;
- обединяване на жлебове, жлебове, преходни радиуси;
- местоположението на същия тип ключови жлебове от едната страна на частта;
2.За части за фрезоване:
избор на съотношението на радиуса на свързване на стенитеRкъм височината на стенатаHв рамките на:
- за леки сплави ;
- за стомани;
- за трудни за рязане материали;
- обединяване на радиуситеконюгиране на елементите на частта;
- избор на радиусиR, свързващи взаимно перпендикулярни равнини, осигуряващи най-голямата крайна повърхност на инструмента (особено при наличие на големи хоризонтални сечения);
- използването на симетрични дизайни на части.
Примери за технологични и нетехнологични конструкции на елементите на частите са представени в таблица. единадесет
Таблица 11 Примери за технологични и нетехнологични конструкции на детайлни елементи
Конструкции | Предимства на технологичния дизайн | |
нискотехнологичен | технологичен | |
Намаляване на дължината на обработката | ||
Възможност за обработка с едно минаване | ||
Подобряване условията на работа на чешмата | ||
Възможност за използване на протягане вместо дълбане | ||
Подобрени условия на обработка | ||
Възможност за обработка на множество дупки в една настройка и опростяване на дизайна на приспособлението | ||
Намален риск от отклоняване и счупване на свредлото | ||
Един и същ | ||
Един и същ | ||
Възможност за използване на нормален инструмент с по-къса дължина | ||
Изключване на рязане със скорост близка до нула в областта близо до оста на въртене |
За да се намалят разходите за програмиране, е желателно да се опростят геометричните изображения на елементите в детайла и да се типизират повтарящи се елементи, да се използва симетрия и огледало. Често при закрепване на части върху машинни маси за технитеясна ориентация по координатните оси с помощта на отвори за фиксиране на координати. Разстоянието от център до център между тези отвори трябва да бъде кратно на 100 mm (за малки части - 50 mm).
3. За CNC машинни части:
- инструментална достъпност на дизайна, осигуряваща свободен достъп на инструмента до максималния възможен брой повърхности при обработка от една инсталация;
- използването на конзолна обработка, тъй като скучните пръти не могат да се използват поради неудобството да ги променяте и съхранявате в магазина;
- ограничение на максималния диаметър на отвора - той не трябва да надвишава диаметъра на плъзгащия шпиндел повече от 2,5 пъти.
Дизайнерите, разработващи чертежи на детайли, обработени на машини с ЦПУ, трябва да отговарят на следните изисквания:
- размерите в чертежите трябва да бъдат посочени в правоъгълна координатна система, която по-късно се прикрепя към координатната система на машината;
- основните повърхности на частта, особено монтажните, трябва да бъдат подравнени с координатните равнини;
- отворите, разположени на диаметъра и обикновено определени от централния ъгъл между техните оси и диаметър D, трябва да бъдат зададени от координатите на осите на всеки отвор (фиг. 1.);
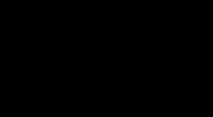
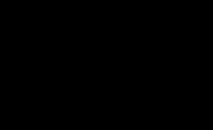
Ориз. 1. Пример за задаване на размери на чертеж на детайл за обработка на детайл на CNC машина (дясно отляво, грешно отдясно)
- размерите на отворите могат да бъдат свързани с произхода (фиг. 1.);
- при наличие на голям брой дупки се използва табличен метод за посочване на размери, който също е удобен за програмиране;
- възможно е линейно подравняване на размерите по дължината на обработката;
- когато чертаете размери на чертежи, трябва да се стремите да се отървете от необходимосттаизлишно преизчисляване. Размерите трябва да се нанасят по верижния метод, като се посочи толеранс, съответстващ на получаване на желания резултат;
- формата за уточняване на контура на частта е по-удобна с аналитично описание, особено за CAM системи.