Lean, 6-sigma и TOC подобряват организационната ефективност
Правилната комбинация от тези практики в минната и металургичната промишленост на Бразилия дава забележими резултати. Уебсайтът //www.industryweek.com говори за успешното прилагане на методологията iTLS в предприятията от групата Votorantim
Автор: Реза Р. Пирасте Превод: Денис Стариков
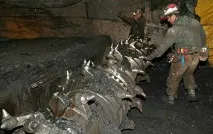
Очевидно е, че производствените организации, ориентирани към печалба, концентрират усилията си върху постигането на планираните нива на доходи от производствената си дейност, разчитайки на собствения си капацитет и ресурси. Ако целите не бъдат постигнати, това води до ниски приходи и високи нива на запасите, което увеличава оперативните разходи. В резултат на това размерът на печалбата и нормата на възвръщаемост на инвестициите са значително отрицателно засегнати. Тази ситуация също оставя организацията в състояние на стрес и известна празнота поради привидно парадоксална ситуация, при която ключовите организационни ресурси се превръщат в потенциална заплаха за бъдещите приходи на компанията.
За подобряване на производителността и увеличаване на рентабилността на организациите е обичайно да се прилагат различни техники като част от процеса на непрекъснато подобрение, катоLean Manufacturing (Lean), 6-Sigma и Теорията на ограниченията на системите (TOC). Дълго време обаче нямаше научни изследвания, които да измерват ефективността и приноса на използването на такива техники за подобряване на ефективността на организациите. По тази причина в периода от 2003 до 2005г. по този въпрос са проведени мащабни проучвания, в които ефективността на споделянето натри от тези техники в логическа последователност и също сравнява получените резултати с резултатите от използването само на една от тези техники.
Интегрираният модел на метода беше подложен на серия от специфични тестове, известни като iTLS, като част от процес на непрекъснато подобряване. Този iTLS модел включваше Теорията на ограниченията на системите от Елияху Голдрат, методологията наСтегнатото производство, по-известна като производствената система на Toyota, и 6-Sigma, методология, създадена от Motorola. Този модел предполага използването на споменатите методи в определена последователност, което допринася за фокусирането върху ключовите силни страни на всеки от тези методи.
След 2,5 години, през които 211 специалисти по процеси на непрекъснато усъвършенстване внедриха предпочитаните от тях методологии в 21 производствени предприятия, бяха завършени 105 проекта.
Проучването даде възможност да се измери финансовата ефективност, получена чрез прилагането на всеки от тези методи. Статистическият анализ показа, че методитеLean и 6-Sigma са допринесли за получаване на значителни финансови резултати в организациите, в които са били приложени. Резултатите от прилагането на тези методи поотделно са приблизително еднакви (получената стойност на значимата вероятност (P-стойност), равна на 0,622, не показва значителна разлика между тези два метода при анализ на фактора за финансова ефективност).
Една организация, която възприе интегриран подход, беше групата компании Votorantim, четвъртата по големина частна организация в Бразилия, работеща в няколко страни и в различни пазарни сегменти като минно дело, стомана, цимент, целулоза ихартия, стомана и плодови сокове. Пет завода са внедрили интегрирана система от TOC, Lean и 6-Sigma, така наречената iTLS методология за непрекъснато подобрение, разработена и публикувана подробно през 2006 г. от д-р Реза Пиратеш (Piratesh и Farah, 2006). Две от тези фабрики, които ще бъдат разгледани по-долу, са минна фабрика и топилна фабрика.
В казуса по-долу iTLS успешно синхронизира производството и използва съществуващия производствен капацитет, за да осигури стабилност на процеса. Тази методология се прилага безпрепятствено поради ангажираността на персонала на организациите и силния им фокус върху успеха. TOC, Lean Manufacturing и 6-Sigma (iTLS) интегриран системен модел (iTLS) iTLS съчетава три от най-мощните компоненти -Lean, 6-Sigma и TOC - като ги съчетава оптимално и ги синхронизира:
- фокусиране само върху няколко критични елемента, които ограничават дейността на компанията като цяло, чрез използването на TOC;
- отстраняване на дефекти в производството чрез откриване на така наречените "скрити фабрики" в рамките на методаLin ;
- намаляване на възможността за нежелана променливост, за да се гарантира стабилност на процеса чрез 6-Sigma.
Използването на тази интегрирана система за непрекъснато подобряване на производството направи възможно да се гарантира, че капацитетът и ресурсите, включени в производствения процес, се превръщат в стабилно производство, което генерира доход с висок дял от печалбата.
Резултати
Казусът по-долу е обобщение на опита с iTLS методологията в няколко бразилскиконгломерати, включващи минни фабрики, рудообогатителни фабрики, както и металургични. Във всички случаи, в които се прилага методологията iTLS, пропускателната способност за производство се увеличава значително за 3-4 месеца. Продължаващото използване на тази техника през следващите 3-4 месеца позволи да се стабилизират производствените процеси, заедно с постигането на стратегически важни целеви обеми на производство, което преди това се смяташе за почти невъзможно.
Новите производствени показатели значително надвишават предишните, а инвестиции в допълнителни мощности не са наливани. Резултатът е постигането на по-високи показатели за приходи, печалба и възвращаемост на инвестициите.
Практически пример
Предположения: Нито една от фабриките не можа да достигне целевите производствени обеми, доброто производствено представяне беше само едно събитие, което доведе до загуба на приходи поради закъснели доставки. Мениджърите на завода бяха подложени на постоянен натиск за непостигане на стратегически цели за ефективност и в резултат на това влошаване на цялата организация.
Наблюдавани са и други нежелани явления:
- Поставените цели не бяха постигнати.
- Броят на предприетите действия беше голям и продължи да нараства, което затрудняваше управлението на тези действия.
- Нарастващ натиск за придобиване на все повече и повече ресурси.
- Служителите отчаяни; имаше мнение: "колкото повече се опитваме, толкова по-малко постигаме".
- Издирването на извършителите от една страна и постоянните им оправдания от друга страна, заедно с ненамесата на част от служителите създадоха негативна атмосфера, в която нямашеположително сътрудничество между персонала.
- Производителността на ресурсите беше много ниска.
- Липса на необходимите превантивни мерки.
- Апатия на служителите.
Приложение
Моделът iTLS беше приложен едновременно към всички растения. Неговите цели бяха да стабилизира и подобри производствените процеси, за да осигури оптимално взаимодействие с пазара. Бяха разграничени 4 основни елемента: 1) Приложение на инструмента Drum-Buffer-Rope TOC за идентифициране на ограниченията на производствения процес и планиране на граничната зона:
- „Барабанен“ ресурс, който задава скоростта на изтегляне за производство и задава TACT за доставяне (т.е. производството започва да работи по такъв начин, че да отговаря директно на изискванията на клиентите) на произведени продукти на пазара.
- Създаване на буфери, свързани с ресурса на "барабана" и осигуряващи защита срещу възникващи отклонения в производствения процес и при транспортиране.
- Издърпващо освобождаване на материали („въже“), което осигурява синхронизирането на производствения процес с ресурса „барабан“.
2) Използването на Lean инструменти за идентифициране на етапите, отговорни за възникването на производствени дефекти и изключването им от производствения процес с цел повишаване на неговата ефективност. 3) Прилагане на инструменти 6-Sigma за осигуряване на устойчивост на направените промени чрез въвеждане на статистически контрол върху производствените процеси. 4) Прилагане на добре установени модели и методологии за решаване на възникващи проблеми, достъпни за работниците и управленския персонал, за да се гарантира, че всяка от тези групи служители може самостоятелно да осигури непрекъснати подобрения в своите процеси.
Има пряка връзка междуотговор на работата на ресурса-"барабан" в комбинация с поддържане на стабилността на производството и показатели за финансова ефективност. Веднага след като „барабанът“ беше открит на базата на определянето на оптималния капацитет на ограничението, работата му се превърна в ключов момент за освобождаване на материали и изпълнение на превози.
Ограничението на ресурсите трябваше да бъде защитено от възможни отклонения, възникнали на етапите на производствения процес, които го предхождат в резултат на взаимозависими операции. Целта на това беше да се гарантира, че необходимият капацитет на този ресурс се използва в пълно производство. В организации с непрекъснат производствен процес, защитата на ресурса на ограничението, който е отправната точка за организацията на "барабана" и отдела за доставка, се осъществява чрез създаване на буфери с определен размер, които захранват този ресурс по време на производствени повреди, за да се осигури непрекъснато производство и непрекъснато снабдяване.
Веднага след като бяха въведени буфери с необходимия размер, те започнаха да абсорбират всички отрицателни отклонения, които потенциално засягат ограничението на ресурсите и процеса на доставка. Важно е да се разбере, че когато такива отклонения засягат буфера, последният намалява обема си и трябва да бъде възстановен. Неговото попълване стана възможно благодарение на използването на излишния капацитет, предхождащ ограничението на ресурсите („барабан“) и отдела за корабоплаване (
10%). По същество те бяха защитни сили. Тяхното използване при възникване на подходящи нужди и направи възможно попълването на буферите.
По този начин всяка производствена стъпка, която е по-малка от 110% от барабана, се счита за ограничение, тъй като може да има потенциал даглобален отрицателен ефект върху размера на пасажа. Може да изглежда, че дейността в този случай е била временно небалансирана. Въпреки това работните екипи след това се захващат за работа, за да увеличат максимално стойността на производствения процес чрез намаляване и стабилизиране на нивата на скрап. За тази цел бяха използвани 6-сигма инструменти за намаляване на променливостта. Този модел включва управление на буфери, за да се оптимизира процеса на вземане на решения въз основа на интерпретацията на състоянието на буферите в определени моменти от време. Буферите се превърнаха в основен източник на информация за ръководството, позволявайки им да проследяват какво се случва в производствения процес, да предотвратяват потенциални заплахи, да определят причините за тяхното възникване и да вземат решения, които допринасят за процеса на непрекъснато подобряване. За целта бяха използвани средствата за статистически контрол на процеса.
Сходството на резултатите, получени с помощта на модела iTLS, беше в съответствие с очакванията. По-долу са някои от резултатите, които всяко растение е успяло да постигне:
- Производството се увеличи с 10%, което позволи да се задоволят изискванията на потребителите на 100%, без да е необходимо да се привличат допълнителни капиталови инвестиции.
- Печалбите са се увеличили с 5%.
- Периодът на изплащане на всяка компания беше намален до няколко месеца, а в един завод беше само 28 дни - най-ниско ниво за всички времена.
- Производствените процеси се стабилизираха, което направи възможно постигането на прогнозираните по-рано стратегически важни целеви обеми на производство.
Eugenio Germont, главен изпълнителен директор на Votorantim Metais Unidade Tres Marias, коментира, че „...успяхмев това мащабно начинание ... и затова постигнахме всички наши цели ... "
Синергиите в приложениятаTOC, Lean и 6-Sigma, изразени в модела iTLS, се превърнаха в средство за постигане на бързи и ефективни подобрения на производителността в минните и стоманодобивните заводи. Това от своя страна направи възможно изпълнението на задълженията към клиентите на 100%. Този модел използва инструментите на теорията на ограниченията, за да се съсредоточи върху области, изискващи промяна, методологията Lean за елиминиране на производствени дефекти и системата 6-Sigma за контрол на производствения процес и произтичащите от него отклонения.