Леене в пясъчно-глинести форми - Студиопедия
Делът на леенето в пясъчно-глинести форми все още представлява 70% от всички отливки. Освен това е лесно да се проследят всички етапи на традиционното леярско производство на неговия пример.
Без да навлизаме в конкретни тънкости, отбелязваме, че формите са направени от пясък и глина с различни видове добавки. По този начин добавянето на някои отпадъци от производството на целулоза и хартия към сместа увеличава повърхностната здравина на формите и ги предпазва от разпадане. Въглищният прах елиминира формовъчния пясък, полепнал по повърхността на чугунените части; по време на изливането на чугуна частиците изгарят и образуват газов слой между отливката и формата, което предотвратява намокрянето на повърхността на формата от метала. Със същата цел към сместа за леене на медни сплави се добавя мазут.
Приготвянето на формовъчни пясъци е цялостно производство, освен това е високо механизирано. Пясъкът и глината първо се изсушават в пещи, след което глината се смила в ротационни или топкови мелници. След това се смесват пясък, глина и други добавки, сместа се оставя да узрее, след това се разхлабва и се подава към формата.
Между другото, сега избраната смес предимно не се изхвърля. Използваните форми се раздробяват, стоманените и чугунените частици се отделят с магнит, останалите частици се пресяват на сита и отново се пускат в действие, като към получената маса се добавят 20-30% от прясната смес.
За да започнете формоването, трябва освен сместа да имате още модели и пръти. Какво е модел, е ясно без специални обяснения, той е като копие на външните очертания на отлятата част. Размерите му са по-големи - трябва да добавите за свиване и неточности, както и надбавки за обработка. Необходими са и наклони за отливане - конус, който улеснява изваждането на модела от формата. На фиг. 2.1 показва отливката, модела и форматаколекция.
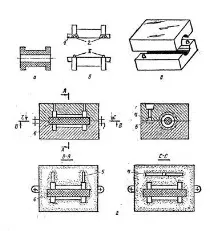
Фигура 2.1 - Отливка (a), модел (b), сърцевинна кутия (c) и възел на формата (d);
1 - моделни знаци; 2 - гнезда; 3 - шипове; 4 - шлакоуловител; 5 - захранващо устройство; 6 - прът.
Използвайки един модел, можете да получите от 5 до 500 отливки. Ако се изискват повече отливки, а те трябва да са по-прецизни, то моделите се изработват и от метал - чугун, месинг и алуминий.
За разлика от модела, пръчките остават по време на изливането на метала вътре във формата. Следователно те не са направени от дърво, а по същия начин като самите форми: от пясъчно-глинести смеси или дори от метал: те са подсилени с рамки и пробити с вентилационни канали, където газовете, отделени от стопилката, могат да излязат.
След като моделът и пръчките са готови, можете да започнете формоването, т.е. до изработката на самата форма - отпечатъци на модели, кухини, където ще се излее стопилката. Ако трябва да се отлее много голям продукт, тогава формоването се извършва директно в почвата. Формите се изработват в колби - метални кутии от стомана или алуминиева сплав без дъно и без капак. Колбите (обикновено има две от тях) държат формата за пясъчно леене, не позволяват да се разпадне по време на транспортиране и изливане на метал. В стените на колбата се пробиват дупки, през които излизат изпаренията и газовете, образувани при сушенето и изливането, а по вътрешната повърхност се правят ребра, за да се предотврати изсипването на пръстта.
Процесът започва с факта, че моделът се монтира с гладка повърхност върху щита под модела. След това поставят долната колба там, след което моделът се напудря с талк или графит, така че да не се придържа към формата, и се засява с малък слой облицовъчна смес.
За разлика от останалата част от формовъчния пясък, облицовъчният пясък е в пряк контакт с течния метал и поради тази причина се приготвя отсвежи материали, докато за пълнеж се използва предимно смес.
След това облицовъчната смес се притиска около модела и се покрива с няколко слоя пълнежна смес, като всеки слой се уплътнява внимателно. По стените на колбата те се опитват да увеличат максимално плътността на пълнене на сместа, в противен случай сместа може да изпадне от колбата при обръщане и сглобяване на формата.
След завършване на пълненето излишната смес се изгребва с линийка и се пробиват с игли (или, както се наричат още, вентилационни отвори), вентилационните канали, чиято цел, както вече беше споменато, е да повишат газопропускливостта на формата. За да не проникне течен метал в тях и за да не се развали повърхността на бъдещата отливка, каналите не се довеждат до модела с 15-20 mm.
Следващата операция е да завъртите колбата на 180°. Поставя се с конектора нагоре и се поръсва с разделителен пясък, а самият модел се пудри. Горната се поставя върху долната. Сега монтират модела на щранга и го запълват първо с облицовка, а след това с пълнежна смес. Последният отново се уплътнява внимателно и вентилационните канали се пробиват отново.
Моделът на щранга (вертикален канал за подаване на стопилката към формата) се изважда и горната му част леко се разширява. Образува се вдлъбнатина - затворена купа, където се излива течен метал. Основната му цел е да улесни навлизането на струя метал от разливна черпачка в щранга, както и да улесни отделянето на метала от шлаката, която плува по повърхността му; в горната част на купата на затвора понякога се поставят прегради, които го забавят.
След това горната колба се отстранява, а в долната колба се изрязват хоризонтални канали - лейки. Краищата на формата около модела се намокрят леко с вода, за да не се ронят при изваждане на модела. В модела отгоре се завинтва винт, който колелцата наричат "повдигач", лекс удари на дървено чукче моделът се “накълцва” и внимателно се изважда от формата. Остава внимателно да се провери формата и да се коригират възможните повреди, да се издуха кухината й със силна струя сгъстен въздух, за да се отстранят остатъците от земята, да се боядиса с формовъчна боя и да се изсуши.
Всичко е завършено с монтажа: горната колба е точно закачена по дължината на направляващите щифтове с долната, а върху тях се поставя тежък товар или се завинтва заедно. Ако не е направено нито едното, нито другото, тогава при изливане металът може да проникне в съединителя и да изтече.
Земни или глинесто-пясъчни форми за всяка отливка трябва да се правят наново. За да се намали сложността на формоването, понякога се използват полупостоянни форми, които се изработват от огнеупорни маси, предварително изпечени при температура 800-900 K. Такива форми могат да издържат на няколко десетки или дори стотици пълнежи и се нуждаят само от периодично подновяване на слоя защитна боя в контакт с течен метал.
Това е най-лесният начин - формоване в две колби върху плътен модел. Леярите познават много такива методи: формоване според разглобяеми модели и в няколко колби, и формоване на купчина, и формоване без колби, и според шаблони, и в пръти и др. Като цяло има много начини, но принципът е един и същ - получаване на кухина, съответстваща на формата на бъдещата отливка.
Сега относно пълненето. Това също е цяла наука. По този начин методът за подаване на стопилката към формата зависи не само от размерите, конфигурацията и дебелината на стената на отливката, но и от метала. Ако леете сив чугун, направете метала на тънки профили. Ако частта е изработена от стомана, стопилката се пренася в дебели части: стоманата има голямо свиване и е невъзможно да се постигне добро хранене на леене през тънки места. За бързо запълване на формите се използват клиновидни лейки, които захранват стопилката с тънък слойи широка струя; ако имате нужда от гладко и безударно захранване, използвайте сифон и леяци от рожкови. Дъждовниците от своя страна раздробяват метала на малки потоци и са добри в случаите, когато има страх, че голям непрекъснат поток ще измие матрицата.
След като формата е залята със стопилката, е необходимо да се изчака, докато отливката се втвърди и охлади до около 700-800 К. Едва тогава може да се избие, т.е. освобождаване от формата. Когато бъдат избити, горещите отливки пламват от топлина, а формованата пръст виси във въздуха с разяждащ прах. Това е много неприятна работа и вече почти навсякъде е механизирана. Колбата се окачва на кран и се разклаща с мощни вибратори (задействани от въздух). Под кобилицата в пода има люк, затворен с дебела решетка. Когато половината форма с отливката изпадне в резултат на вибрациите на колбата, тя се разпада на парчета, изгореният пясък пада през решетката и се отнася в цеха за подготовка на почвата, където се използва отново, а отливката остава отгоре.
На първо място, отливката трябва да бъде почистена от пръчките, които запушват всички нейни дупки и кухини. Преди това прътите бяха избити с пневматични длета и чукове, сега най-често се използва хидротретиране; пръчките се разрушават и разяждат от силна водна струя, а смесеният с нея кварцов пясък бомбардира повърхността на отливката и отлепва мръсотията и натрупванията от нея. Тъй като хидроочистителят се извършва в затворена камера и работникът, работещ със струята, е през цялото време навън, той не трябва да се мокри или да вдишва праха.
Друг метод за почистване е почистването с пескоструйни и пясъкоструйни машини.
Още по-усъвършенстван метод за почистване е електрохимичното почистване и почистването с електрохидравличен удар. И накрая, излишният метал - леяците - се отстраняваот крехки чугунени отливки с чук, а от отливки от други материали се отрязва с триони или газови горелки. Насечките и неравностите се отстраняват с абразивни колела.
Сега отливката е почти готова. След повърхностен преглед, рутинни измервания, проверка на химическия състав чрез химични или спектрографски методи и изследване на микроструктурата, той се изпраща за рентгеново предаване за установяване на скрити дефекти. Напоследък широко се използват гама лъчи и ултразвук за трансилюминация. Отливките от магнитни материали също се подлагат на така наречените магнитни тестове. Идеята им е, че потокът от силови линии, преминаващ през отливката, срещайки препятствие (в случая с вътрешен дефект), променя посоката си или се разсейва. Това се фиксира от индукционни устройства - магнитни дефектоскопи.
След като откриете дори сериозни дефекти, не е необходимо да изхвърляте отливката. През повечето време може да се поправи. Например, дефектна зона се изрязва до чист метал и получената кухина се запълва със стопилка със същия химически състав като отливката или дори с по-добро качество. Вместо пробиване, можете да разтопите дефектното място с електрическа дъга или газов нож.
Този метод на "ремонт" на отливки е метализация. Малки капки метал, разтопени от електрическа дъга, се издухват със сгъстен въздух и се изпращат директно до дефектното място.
Леенето в пясъчно-глинести форми за еднократна употреба се използва при индивидуално и дребномащабно производство на големи детайли от черни и цветни сплави.
При индивидуалното производство леенето в пясъчно-глинести форми е най-икономичният метод поради ниската цена на формовъчните материали и моделното оборудване. Но получените отливки имат грапава повърхност, ниска точност на размерите и порадиедрозърнеста структура и значителна порьозност на метала в отливките - ниски механични свойства. Отливките, получени по този метод, трябва да имат резерв за последваща обработка (3-10 mm).
1.2 Леене на черупки
Пясъчно-глинената форма, която е описана подробно по-горе, се състои от две части: тънък вътрешен слой, който е непосредствено до отливката и образува нейната повърхност, и външен слой, който е десет пъти по-дебел и е необходим само за придаване на здравина на формата. Именно заради него леярите изгребват цяла планина (до 12 тона) пясък и глина за всеки тон отливки. Ако вътрешният слой беше достатъчно здрав, външният слой изобщо нямаше да е необходим.
Това е идеята за отливане в черупкови форми. Благодарение на напредъка в химията на полимерите от кварцов пясък с малка добавка на специална смола, като пулверизиран бакелит, леярските работници се научиха как да правят тънки черупки и черупки с помощта на специални машини. Те са 15-20 пъти по-здрави от пясъчно-глинестите форми и затова не се нуждаят от дебел външен слой. В резултат на това потреблението на формовъчен пясък на тон отливка намалява 8-10 пъти. Отливките са много точни, с чиста повърхност, припуските за обработка са наполовина, няма нужда от избиване и почистване и се отваря пътят към пълна автоматизация на производството. Черупковите форми са силно газопропускливи, поради което газовете се отстраняват по време на изливането на метал, което значително подобрява качеството на отливките.
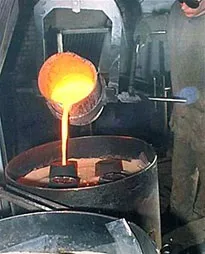
Корпусните форми се използват в серийно и масово производство на отливки с малки и средни размери от 0,5 до 50 кг от черни и цветни метали и техните сплави, части от автомобили, трактори, мотоциклети, дизелови локомотиви, кораби и други продукти.
1.3 Леене в метални форми (кокилни форми)
Охлаждащата форма е древно изобретение. Дори скитите са отливали върховете на своите бронзови стрели в метални форми. Предимството им пред пясъчните е преди всичко издръжливостта. По този начин в една чугунена форма могат да бъдат направени стотици хиляди малки отливки от алуминиеви, цинкови или магнезиеви сплави. За най-големите стоманени отливки със своята химическа агресивност и относително висока температура тази цифра пада до 10-15 броя, което определя границата на икономическата приложимост на метода.
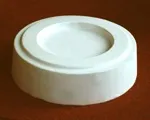
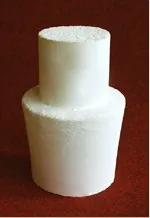
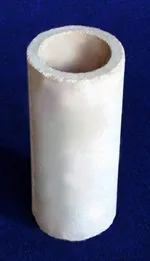
Не намерихте това, което търсихте? Използвайте търсачката: