ОБЕМНО КОВАНЕ
РАЗВИТИЕ НА ТЕХНОЛОГИЧНИЯ ПРОЦЕС ГОРЕЩО ОБЕМНО КОВАНЕ
Да се консолидират знанията, получени в теоретичните часове по обработка на метали чрез налягане. Да се разработи технологичен процес за получаване на изковка чрез горещо коване на манивела за горещо коване в отворена матрица.
1. В съответствие с опцията за задание (Приложение 1) начертайте скици на даден готов детайл, коване и отворена матрица.
2. Изберете температурния диапазон за обработка.
3. Определете времето за нагряване на детайла.
4. Изчислете параметрите на горещо коване (Таблица 1).
1. Основни положения
Процесът на формоване на метал (MPD) се състои в придаване на необходимата форма, размери и физични и механични свойства на материала, без да се нарушава неговата непрекъснатост чрез пластична деформация. В зависимост от пълнотата на възстановяване на първоначалната форма и размери на тялото след прекратяване на действието на външните сили се разграничават еластична и пластична деформация, които се придружават взаимно в процеса на OMD.
Промяната във формата и размерите на твърдото тяло в резултат на действието на външни сили се оценява по степента на деформация. Максимално допустимата степен на деформация зависи от пластичността на обработвания материал и неговата устойчивост на деформация. От своя страна те се определят от химичния състав на сплавта, температурата на обработка, скоростта на деформация и схемата на натоварване.
Така пластичността се увеличава и устойчивостта на деформация намалява в следните случаи:
1. С намаляване на съдържанието на въглерод и легиращи елементи в стоманата.
2. С повишаване на температурата на обработка.
3. С намаляване на скоростта на деформация (промяна в степента на деформация за единица време). Въпреки това, при много високи скорости (напр.електромагнитно и експлозивно коване) за много метали е допустима изключително голяма степен на деформация, при която не настъпва разрушаване.
4. При прилагане на схема на натоварване, която създава цялостна неравномерна компресия. Следователно, например при пресоване, коване, металът проявява по-голяма способност за пластична деформация, отколкото при изтегляне.
Следователно пластичността и технологичните възможности на MMD трябва да се разглеждат не като неизменно свойство на всеки материал, а като неговото състояние, в зависимост от конкретните условия на обработка. Възможно е да се създаде набор от условия (дребнозърнеста структура на метала, съответна температура и скорост на деформация), при които редица метали преминават в състояние на свръхпластичност.
Пластичната деформация причинява фундаментална промяна в структурата и свойствата на метала; в този случай зърната се смачкват и разтягат по посока на пластичния поток на метала, създавайки влакнеста структура. В резултат на студена пластична деформация, твърдостта и якостта се увеличават 1,5-2 пъти с едновременно намаляване на пластичността, електрическата проводимост и промяна на магнитната проницаемост. Втвърдяването на метала в резултат на студена пластична деформация се наричаработно закаляванеилиработно закаляване.
Втвърдяването привежда метала в нестабилно структурно състояние, което е свързано с изкривяване на кристалната решетка. При нагряване на студено формован метал и деформиране на предварително нагрятия метал в него протичат процеси на размекване, нареченивръщанеирекристализация.
Връщането за чисти метали се появява при температури над 0,3 Tmelt, където Tmelt е точката на топене, ° K. Увеличаването на амплитудата на топлинните вибрации на атомите на изкривена кристална решетка им позволява давръщане в положение на стабилно равновесие. В същото време пластичността се увеличава донякъде и влакнестата структура не се променя.
Рекристализацията настъпва при повишаване на температурата до 0,4 Tm за чисти метали. В този случай подвижността на атомите е достатъчна за тяхното пренареждане, водещо до образуване и растеж на нови равноосни зърна с ненарушена кристална структура вместо деформирани. Втвърдяването е напълно отстранено и влакнестата структура става равноосна. OMD, проведено над температурата на прекристализация, се наричагорещо, по-долу -студено.
Влакнестата структура на деформирания метал води до анизотропия на неговите свойства (якостта и якостта на удар по протежение на влакната му са по-високи, отколкото напречно). Следователно потокът от метал по време на обработката под налягане трябва да бъде насочен така, че влакната да съвпадат с посоката на най-големите напрежения в частта по време на нейната работа.
OMD значително влияе върху свойствата на материалите. Тя ви позволява да подобрите качеството на отлятия метал, т.к. излятата дендритна структура се превръща в относително фино зърно. По време на гореща деформация кухините и микропукнатините вътре в блока се елиминират, неговата сегрегация (хетерогенност на химичния състав) намалява поради значителни движения на металните слоеве.
2. Нагряване на метала по време на обработка под налягане
При гореща деформация пластичността на метала е по-висока, а устойчивостта на деформация е по-ниска, отколкото при студена деформация, следователно е придружена от по-ниски разходи за енергия. В резултат на това студената деформация се използва само ако горещата деформация е неприемлива.
Нагряването на метала по време на OMD влияе върху качеството и цената на продуктите. Основни изисквания за нагряване: необходимо е равномерно нагряване на детайла по напречното сечение и дължинатемпература за най-кратко време с най-малка загуба на метал в мащаба и икономичен разход на гориво. Неправилното нагряване причинява различни дефекти: пукнатини, обезвъглеродяване, повишено окисление, прегряване и изгаряне.
При бавно нагряване производителността намалява, окисляването и обезвъглеродяването на повърхността на детайла се увеличават. При прегряване (нагряване над оптималния интервал OMD) се получава растеж на зърна, което намалява механичните свойства. Коригира се чрез нормално отгряване чрез нагряване до оптимална температура, задържане и след това бавно охлаждане с пещта. При изгаряне, т.е. при нагряване до температура, близка до температурата на топене, границите на зърната се стопяват и се появяват пукнатини, което е непоправим дефект.
Всеки метал и сплав има свой специфичен температурен диапазон за горещо формоване, който се избира според таблиците в зависимост от марката на сплавта. Така например за въглеродни стомани температурата на началото на горещата деформация се избира съгласно диаграмата на състоянието желязо-циментит 100–200 ° C по-ниска от температурата на топене на стомана с даден химичен състав, а температурата на края на деформацията се приема с 50–100 ° C по-висока от температурата на прекристализация.
Заготовките и блоковете се нагряват в ковачници или пещи преди обработка под налягане. Пещите се различават от отоплителните пещи по малкия си размер, те се нагряват с въглища, кокс или мазут, металът се нагрява в тях чрез директен контакт с горивото. Използват се за нагряване на малки детайли при ръчно коване.
Пещите за нагряване на заготовки се разделят на пламъчни и електрически, а според разпределението на температурата - на камерни и методични. В камерни пещи - пещи с периодично нагряване - температурата е една и съща през цялата работапространство. Методичните пещи с постоянно нарастваща температура на работното пространство от мястото на зареждане на заготовките до мястото на тяхното разтоварване са непрекъснати пещи.
3. Практическа част от работата
Дизайнът на технологичния процес на горещо коване се състои в разработването на чертеж (скица) на изковка, изпълнен въз основа на чертеж (скица) на готовия детайл (фиг. 1, 2) и изчисляване на основните параметри на коване, които са въведени в (Таблица 1).
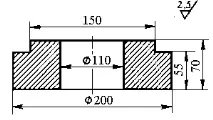
Ориз. 1. Детайлна скица
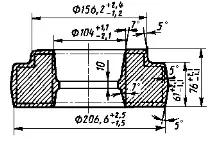
Ориз. 2. Скица на изковката
Преди да се разработи скица на изковка, масата на дадена част се определя предварително по формулата:
където G D е масата на частта, kg g е плътността на метала (за стомана g \u003d 7,8 g / cm 3). V – обем на частта, cm3.
Име на параметъра
стойност
При изготвяне на скица на изковка общият контур на готовия детайл се изобразява с тънки линии. Контурът на изковката е изчертан с плътни линии. Цифрите над линията на размерите показват номиналните размери на изковката и допустимите гранични отклонения.
Разработването на скица на коване се извършва в следната последователност:
1. Равнината на разделяне на матрицата е избрана. Тя трябва да осигурява възможност за свободно извличане на изковката от матрицата, да предотвратява евентуалното изместване на едначаст от матрицата спрямо друга, разделителната равнина трябва да пресича вертикалните повърхности на изковката.
2. На повърхността на изковката, която ще се обработва (обозначена със знака), се определят надбавки. Те се избират съгласно таблици от GOSTs, в зависимост от общите размери и тегло на изковките и от изискванията за изковки (Таблица 2).
3. Съгласно същите таблици се определят допустими отклонения - допустими отклонения в размерите на изковките поради възможното им недостигане на височина, изместване на матриците и тяхното износване.
4. Не винаги е възможно да се получи сложна конфигурация на коване чрез щамповане. Следователно, за да се опрости формата, се предписват припокривания, които са част от обема на изковката, добавени за улесняване на нейното производство. Припокриванията включват също наклони за щамповане, вътрешни радиуси на кривина, прегради на отвори.
5. В матрици с една разделителна равнина е невъзможно да се получи проходен отвор в изковките. Следователно в тях се прави дупка отгоре и отдолу и между тях остава джъмпер, чиято дебелина е S = 0,1 d отвори за коване. Отвори с диаметър по-малък от 30 mm не се правят в изковки, те се получават чрез пробиване.
6. На страничните повърхности на изковката (перпендикулярно на равнината на разделяне на матрицата), за да се улесни отстраняването й от матрицата, се задават наклони за щамповане. Има външни a и вътрешни b наклони. Вътрешните наклони са с 2 o - 3 o повече от външните, т.к когато изковката се охлади, нейните вътрешни повърхности се притискат към матрицата, а външните повърхности се отдалечават от стените на матрицата, намалявайки вероятността изковката да се забие в матрицата (Таблица 3, Фиг. 3).
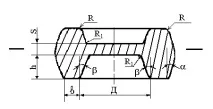
Ориз. 3. Външен R и вътрешен R1 радиуси на кривина на изковки, плосък мост за пробиване, външни a и вътрешни b наклони на изковки