От стар локомотив
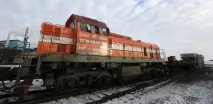
Видях весел оранжев дизелов локомотив на Innoprom-2015, на съвместния щанд на компаниите UMMC. Вярно, не беше огромен колос, а красиво изпълнен модел 1:30. „Преобразуваме дизелови локомотиви, чийто експлоатационен живот е към края си, в такива модерни машини“, казаха представители на компанията. Със собствените си очи да видя как старите трудолюбиви хора получават нов живот, се оказа едва след шест месеца.
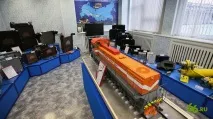
Сега моделът на дизеловия локомотив TEM2, който е сглобен специално за Innoprom, стои в изложбената зала на SHAAZ.
И не просто да видиш, а дори да караш нов локомотив. Но на първо място.
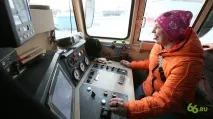
Емоциите от карането на дизелов локомотив са неописуеми! Чиста наслада и прилив на адреналин! 100 тона с едно движение на китката! Не е за вас да карате "реношка"!
Производството за модернизация на дизелови локомотиви се намира на 250 км от централата на UMMC във Верхняя Пишма - в Курганска област. Два модела се преобразуват в завода за автоагрегати в Шадринск: голям шестосен TEM2 и четириосен TGM4B. Има много от тези и други в предприятията на UMMC и те са постоянно на работа. По-малки машини, TGM4B, маневрират вътре в комбайните и фабриките. Големите ТЕМ също работят извън определена територия, например доставят стоки от завод до жп гара.
Александър Папировски, заместник-технически директор по модернизацията на дизеловите локомотиви SHAAZ:
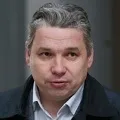
— Дизеловите локомотиви за модернизация идват при нас от различни места, където холдингът има свои подразделения: Урал, Кузбас, Оренбургска област и др. Това са машини, които са използвани 28-30 години - експлоатационният им живот. След нашата работа минаватпоне още 20 години.
За първи път информация, че модерните автомобили не могат да се купуват, а се правят от стари, се чу на UMMC през 2011 г. Започнаха да търсят партньори - тези, които могат да проектират такава продукция и всъщност самия сайт за нейното поставяне.
Александър Папировски:
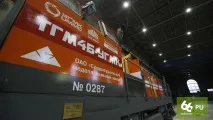
Корпусът на всеки модернизиран дизелов локомотив е нещо подобно на кучешко родословие: от логото, поставено върху него, можете да разберете цялата информация за колата. В допълнение към модела и серийния номер, всеки модернизиран дизелов локомотив има своите „родители“ - UMMC, SHAAZ и Woodward Mega, както и предприятието, където ще се използва машината.
Ново производство възникна, може да се каже, от нулата. Някога на мястото на днешния цех е имало леярна - в ШААЗ правели отливки от чугун и цветни метали за собствени нужди. С прехода към пазарна икономика броят на поръчките рязко намаля и необходимостта от леярна отпадна. Сградата стои празна от няколко години. Организирането на ново производствено съоръжение направи възможно реанимирането на магазина и вдъхването на нов живот в него.
„От тази бивша работилница са останали само стените и покривът“, казва Александър Папировски. „Променихме напълно оформлението, технологичните пътища, подовете, отворите за портали, колоните за мостови кранове и др.“
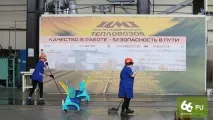
Това, което прави впечатление на влизане в магазина е чистотата. Подовете тук се мият, изглежда, постоянно. Тук е много топло, чисто и удобно. Дори не може да се каже, че някога тук е имало леярна.
В новия цех са монтирани два мостови крана. „Крановете са с дистанционно управление“, казва с гордост Александър. „Без кабели, без кабини на голяма надморска височина. Човек, който има разрешително, просто закача специално дистанционно на врата си и от него управлява количките. Синхронно можете да вдигнете всеки максимумдопустимо натоварване. В същото време, като е на земята, той вижда всички препятствия, разбира как най-добре да извърши тази или онази технологична операция. Много е удобно".
Разбира се, работилницата беше оборудвана и с железопътни релси - все пак дизеловите локомотиви се движат по релси.
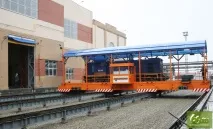
В цеха има девет технологични звена. Всеки е оборудван със собствени порти (като в добър автосервиз) и пътища за достъп. Ако локомотивът трябва да бъде преместен на друго място, той се извежда от работилницата, закарва се на специална платформа, оборудвана с релси, и се премества до желаната врата.
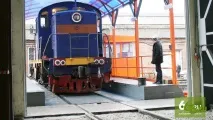
Релсите в цеха и релсите на платформата се комбинират, дизеловият локомотив отново влиза в цеха.
Първата технологична област е приемането.
Александър Папировски:
Всички компоненти са внимателно проверени.
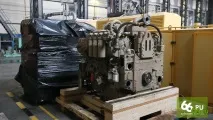
Двигателите Cummins се доставят в Шадринск от САЩ. Сервизното обслужване на агрегатите се извършва от специалисти на КАМСС ООД, дилър на Cummins за България. Сервизният клон, който е най-близо до SHAAZ, се намира в Екатеринбург, така че ако е необходимо, специалистите могат бързо да отидат до предприятието.
Тук се използват и самите дизелови локомотиви. Автомобилите пристигат в сервиза "на студено" - източват се всички течности, гориво, дизеловият локомотив не върви, закача се като вагон и се изпраща за модернизация. „Като цяло предприятията, които ни изпращат дизелови локомотиви, могат да демонтират цялото оборудване, от което се нуждаят, ако това не навреди на работата ни. Мнозина просто оставят частите за себе си за резервни части “, обяснява Александър.
В предприятието в Шадринск дизеловият локомотив е буквално разглобен на винт. Остава голата рамка. Всички компоненти, които трябва да се използват в бъдеще, се изпращат в мивката, след това къмотстраняване на неизправности и ремонт. Но има много малко такива устройства. „Ние правим модерна кола, но старите елементи не могат да осигурят нормална ефективност“, обясняват експертите. Според тях отгоре на дизеловия локомотив не остава практически нищо, само ходовата част се използва повторно.
Александър Папировски:
Следващата стъпка е измиването. За малки части е предвидена по-малка камера. И рамката се забива в огромен хангар за миене.
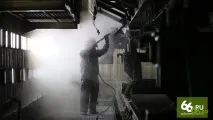
Дизеловите локомотиви се мият с Karcher, както всеки обикновен автомобил.
След измиване и изсушаване старите компоненти на дизеловия локомотив, които ще бъдат използвани при модернизацията, се изпращат за отстраняване на неизправности и ремонт, а след това в камерата за дробеструйна обработка. Рамата на дизеловия локомотив се транспортира до обекта, където ще бъде ремонтирана и модернизирана: ще се монтират надстройка, крепежни елементи на основните възли и възли.
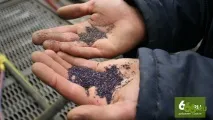
В дробеструйна машина се отстраняват остатъците от боя, различни грундове и китове от частите. Това се прави от такава фракция, излитаща от апарата под налягане от няколко атмосфери.
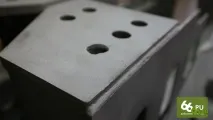
След почистване в дробеструйна камера, металът буквално се полира. Остава да се обезмасли, покрие с грунд и боя.
Следващата стъпка е боядисване. Това става в специална камера. Отделни части се докарват тук на колички. Рамката на дизеловия локомотив също се доставя на специална платформа - в крайна сметка колелата вече са свалени от нея.
Най-после след всички демонтажи, миене и боядисване идва ред на реставрационни процедури.
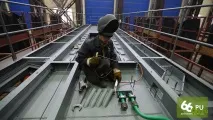
В напълно подготвена рамка се правят нови отвори и надстройки, които по-късно се използват при инсталиране на ново тяло.
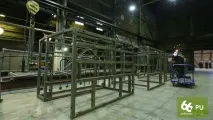
Телата се сглобяват тук - зад стената, в подходящата зона.
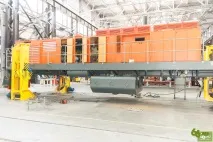
С кранови гредиинсталирайте захранващи блокове, прикрепете различни компоненти. След това - тялото и кабината на радостен оранжев цвят.
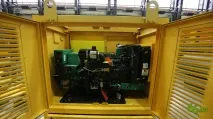
В допълнение към самия двигател, модернизираните дизелови локомотиви са оборудвани с дизел генератор. При дълъг престой (повече от 10 минути) водачите изключват главния двигател и стартират DGU. „В резултат на това всички системи за поддържане на живота на дизеловия локомотив работят, но в същото време, първо, разходът на гориво е значително намален, и второ, експлоатационният живот на главния двигател се запазва“, обяснява Александър.
Готовият връх се комбинира с дъното - рамката се поставя върху колички с колела.
Александър Папировски:
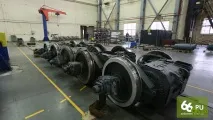
На работниците в Шадринск остава само да извършат входен контрол (за това има специален стенд) и да поставят колесните агрегати на ремонтираните талиги.
Процедурата за възстановяване на талиги е подобна на работата върху целия дизелов локомотив: те се разглобяват напълно, отстраняват се и се сортират с всички приспособления, измиват се, почистват се, дефектират, ремонтират се - и се сглобяват отново.
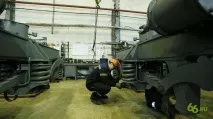
„Ходовата част на дизеловия локомотив, за разлика, да речем, от рамката му, е по-малко податлива на деформация. В същото време в тази област не се появяват особено нови технологии, това ще се случи само при промяна на принципа на работа. Но засега този механизъм е прост и надежден. Няма нужда да го променяте, като захранващи агрегати. Основното е да се грижите за него, а не да го управлявате “, обясняват специалистите.
Последният етап е отстраняването на грешки на електрониката, свързването на всички компоненти и възли към системата за управление. Монтажът на електричество на локомотиви се контролира от унгарски специалисти.
Готовият дизелов локомотив се приема от служители на предприятието, където ще се експлоатира. И те не просто приемат - поне една седмица представителите на клиента живеят в Шадринск и преминават обучение: учат се да управляватмашина, участват в морски изпитания. В края на краищата всъщност те получават напълно нов дизелов локомотив. Външните разлики са само малка част от промените.
Отвътре също е напълно различна кола. В този локомотив има дори два контролни панела - за машиниста и неговия помощник. По отношение на комфорта всичко също е много по-модерно, кабината е оборудвана с микровълнова печка и хладилник.
Във флота на Uralelectromed има само седем дизелови локомотива: три TGM6, три TGM4 и голям TEM2. Един TGM4 вече се върна от Шадринск след модернизация, друг отиде там за преоборудване. Компанията планира да модернизира всички TGM4.
Николай Устинов, заместник-началник на железопътния цех на клон "Производство на полиметали" на АО "Уралелектромед":
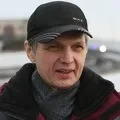
— Модернизираните дизелови локомотиви може да не са толкова евтини: тези пари на теория биха били достатъчни за закупуването на нов TGM4. Но тези машини напускат поточната линия вече остарели. А дизеловите локомотиви SHAAZ са модерни, тяхната експлоатация позволява значителни икономии както на гориво, така и на ресурси: всички системи са дублирани, не се изискват ремонти - само поддръжка. В бъдеще компанията само печели.
SHAAZ е съгласен с това мнение.
Александър Папировски:
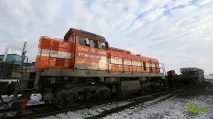
Буквално преди новогодишните празници нов дизелов локомотив дойде в друго предприятие на UMMC - SUMZ. Точно такъв дизелов локомотив видяхме в цеха на завода за автоагрегати в Шадринск.
Серийното производство в SHAAZ работи от 2014 г. За това време в предприятието са модернизирани 18 машини. Средно един дизелов локомотив се модернизира за шест месеца. Пет машини могат да работят едновременно. Производството е предназначено за 30 дизелови локомотива годишно. Но има място за разширяване. Вярно, тогава трябва да увеличитеперсонал - сега в работилницата работят около 100 души.
Според оценките на специалистите от UMMC, паркът от дизелови локомотиви на предприятията на холдинга включва повече от 100 единици оборудване, което изисква модернизация. „За следващите 10 години имаме осигурена работа. И тогава ще излезем на свободния пазар: нашият продукт е търсен както в България, така и в съседните страни - същият Казахстан“, сигурен е Александър Папировски.
Roskomnadzor унищожи бота на Telegram 66.RU. Абонирайте се за резервния канал.