Овърклок, платформа за съдържание
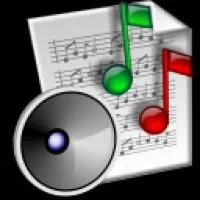
Ориз. 108. Схема на операцията на разпръскване по ширина:
1 - горен и 2 - долен нападатели
Овърклок(вижте Таблица 18). Тази операция е предназначена за локално разширяване на детайла без увеличаване на дължината му. Най-често на разпръскване се подлага част от детайла, който е предварително компресиран с обикновен плосък ударник и след това, когато
с помощта на специален опорен инструмент металът се ускорява по ширина (фиг. 108). На фиг. 108, а отгоре показва началния, а отдолу - крайния етап на овърклок. На фиг. 108b показва междинен етап в друга проекция. Обикновено сравнително ниски детайли са подложени на разпръскване, така че инструментът за разпръскване се използва за намаляване само на едната страна на детайла, докато другата страна е върху голяма повърхност на плоска матрица. След ускорение, деформираната зона се обработва с плоски нападатели, за да се изгладят ръбовете-издатини между съседни намаления.
Инструментът за облицоване, използван за разпръскване, може да бъде кръгъл, полукръгъл, овален и дори правоъгълен. На фиг. 108 показва полукръгъл разпръсквач. Между дължината и напречния размер на инструмента съотношението се поддържа в границите 5-10, което осигурява преференциално протичане на метала перпендикулярно на дължината на инструмента. При съотношения, равни на 3-4, удълженията са незначителни. Стойностите на специфичните сили от страната на инструмента за разпръскване и долния ударник върху метала са обратно пропорционални на площите на проекцията на съответните контактни повърхности, следователно компресията по време на разпръскването се дължи главно на деформацията на метала от страната на инструмента за разпръскване. Ако дебелината на детайла е значителна (вижте горната позиция на фиг. 108, а), тогава намаляването на височината и разширяването. не нанасяйте върху цялата му дебелина. Ако детайлът е толкова тънък (илипредварително компресиран), че по време на ускорение в едно преминаване инструментът е потопен в детайла с най-малко 50% от височината му, тогава деформацията се простира до цялата дебелина на детайла. В този случай металът първоначално се деформира само от страната на инструмента за разпръскване под действието на големи специфични сили. Обемът на зоната на физическа деформация през този период е много по-малък от обема на зоната на геометрична деформация.
На този етап се създават условия за деформация в останалата част от зоната на геометрична деформация, която възниква под въздействието на два процеса; 1) поради известно огъване на детайла, неговите странични части се издигат и контактната площ намалява, което води до намаляване на разликата в специфичните сили от ударника и търкалянето;
2) напречните деформации, които създават напрежения на опън във все още недеформирания метален слой, улесняват неговата деформация.
При разпръскване по ширина общото разширение е сумата от частичните разширения при всяко компресиране на даден проход. Това се случва в резултат на насочване на подавания през детайла. Деформациите по време на изправяне могат да се изчислят по същия начин, както при протягане без струговане. Протягане без разширение и разпръскване са крайни случаи на общия процес на високо издигане с многопосочни напречни деформации.
Ускорението на правоъгълен детайл е описано по-горе. Коването обаче се използва широко и за кръгли заготовки, например за намаляване на дебелината и увеличаване на диаметъра на дискови изковки, които обикновено имат главина с или без отвор, който не участва в ускорението. Ускоряването се извършва в кръг, обикновено близо до главината на изковката, и се използва плосък инструмент с кръгло и овално сечение (в зависимост от диаметрите на главината и самия диск), който трябвабъдете специализирани. При коване на чукове ускорението става с кръгови подавания. На пресите са разположени ротационни механизми за въртене на горния ударник, което позволява ускорение без преместване на детайла.
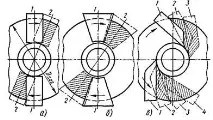
Ориз. 109. Ускоряване чрез съседни компресии с плосък ударник (а), ускорение на вентилатора (c) и ускорение от ударници, разположени тангенциално към главината на диска (c)
I, 2 и т.н. - числа на компресия
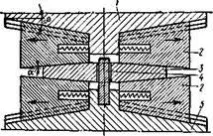
Ориз. 110. Схема на дизайна на "плаващи нападатели" за разпръскване:
I—горна плоча; 2—ударници; 3—кован диск; 4—центриращ прът; 5 - долна плоча
Ускоряване на дисковото поле на Пресата по схемата, показана на фиг. 109, а, възниква с припокриването на част от зоната на деформация на предишното компресиране.
Само при първото компресиране центърът на деформация съответства на правоъгълната форма на ударника, който има вдлъбнатина за поставяне на дисковата главина в него. Формата на зоната на деформация при последващи редукции след завъртане на ударниците под определен ъгъл може да се съди по защрихованите зони. Чрез промяна на ширината на ударника и съответно ъгъла на неговото въртене по време на ускорение е възможно да се получат различни съотношения на размера на зоната на деформация и интензивността на процеса на ускорение. Много широк нападател е непрактичен поради голямото затягане на главината (намаляващо височината му). Прекалено тясната глава води до нежелано огъване на лентата на острието и не осигурява приемлива производителност. Режимът на ускорение "кръст-кръст" (вместо последователно съседни съкращения) се характеризира с голямо допълнително време за увеличени завъртания на ударника.
В специализираното производство ветрилообразното разпръскване на дискове е много технологично напреднало с нападатели, контурирани от прави линии, минаващи през оста на диска (фиг. 109, б). Не по-малко обещаващ е инструментът за ускоряване,предназначен'-невим. Разположението на ударника (фиг. 109, в) по тангенциалната линия към главината осигурява ускорение без затягане по главината и без огъване на мрежата. Когато подаванията са насочени обратно на часовниковата стрелка, центровете на деформация (виж пунктираната линия) имат ветрилообразна форма, образувана от допирателни към контура на главината. Обратната посока на захранването е придружена от образуването на огнища с по-сложна форма. Чрез промяна на формата на ударниците в план и посоката на подаване е възможно да се контролира потока на метала по време на ускорение с преобладаване на срязване или нормална деформация в желаната посока.
Добре известен дизайн на ускоряващ инструмент под формата на плаващи нападатели (фиг. ON). Както при нормалното ускорение, ударниците са разположени диаметрално, но всеки от тях (горен и долен) се състои от две части, които се движат радиално от оста на диска и разтягат пружините (посоките са посочени със стрелки). Ъгълът а се определя по чертежа на изковката, а ъгълът ветта се определя конструктивно. При голям ъгъл на намокряне скоростта на радиалното движение на ударниците в процеса на компресиране на диска ще надвиши скоростта на металния поток.
la в същата посока и ускорението ще се извършва при условия на активно триене. В този случай изковката и ударникът не трябва да се смазват. Ако мокрият ъгъл е малък (по-малък от ъгъла на триене), тогава ускорението се извършва с резистивно триене и е необходимо смазване. Улеснява се деформацията по време на ускорение от плаващи нападатели (силите се намаляват 2 пъти), намаляват се припокриванията. Нежеланото разширяване на отвора на диска може да бъде предотвратено чрез водно охлаждане на центриращия прът.
Образуването на первази, первази, вдлъбнатини. За точно разпределяне на метала между отделните части на изковката детайлът се маркира (с измервателен уред или по шаблони). На маркираните места се правят вдлъбнатини, наречени серифи или бастинг.Инструментът за лепене има формата на кръгли или ъглови пръти. Маркираните вдлъбнатини се увеличават до височината на перваза, перваза или вдлъбнатината. Съответният инструмент се нарича скоби (фиг. 111). Профилът на прищипване се избира в съответствие с необходимия контур на первазите или вдлъбнатините на изковката. За да получите едностранна перваза (фиг. 112, а), продължете, както е посочено по-горе, и след това компресирайте метала до нивото на вдлъбнатината (със стойността на делта Н). Голямата контактна площ от страната на долния нападател осигурява ниски специфични усилия, а компресията се осъществява само от действието на горния нападател. По същия начин се получава двустранен перваз (фиг. 112, b). В този случай е важно деформацията да е еднаква от страната на работната повърхност. За да се получи вдлъбнатина (фиг. 112, c), тя се маркира, освен това се маркират вдлъбнатини на съответните места, между които след това металът се нагъва. Освен това изисква външна сила да бъде концентрирана в горната част на детайла. За целта под горния ударник се поставя плосък валяк и така се постига преференциална деформация на метала в горната част на детайла. Производството на две резки от двете страни на изковката е показано на фиг. 112, гр
Ако е необходимо да се получи издатина върху изковка, тогава тя се получава от две первази, изпълнени от двете страни на издатината
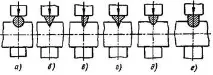
Ориз. 111. Затягане на детайла и използван инструмент:
а - кръгло валцуване; b - триъгълно равностранно стесняване; в - правоъгълно притискане; g - оформена щипка; d - стеснение с изпъкнали лица; д - полуовално стеснение
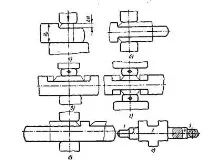
Фиг., 112. Схеми на операции за образуване на первази, вдлъбнатини, первази и техните комбинации
pa (фиг. 112, д). По същия начин се получава двустранна издатина. На фиг. 112e показва сравнително сложно коване,изковани в резултат на образуването на комбинация от первази, первази и вдлъбнатини, а краищата на изковката са получили кръгло напречно сечение по време на валцуване - секции 1 и 5; секции 2 и 4, съседни на тях, са квадратна секция с издърпване; средната секция 5, върху която има прорез отгоре и издатина отдолу, има правоъгълно сечение. По същия начин е възможно да се получат изковки с две, три первази, двойни вдлъбнатини и первази със сложна форма.
Размерите и техните съотношения за первази и вдлъбнатини се регулират от стандарти. За чукови изковки (GOST 7829-70), первази в краищата на изковки с дължина над 15 mm и междинни первази с дължина над 10 mm се изковават без опростяване на формата на изковките (без припокривания), ако съответният размер на перваза в съседство с въпросния перваз е най-малко 40 mm. За пресови изковки, съгласно GOST 7062-67, не се предвижда получаването на первази и вдлъбнатини по-малки от 13 mm, ако размерът на издатината в близост до този перваз е 200 mm или повече. Первази и яки с дължина съответно над 45 и 30 мм се изковават без припокривания, което опростява чертежа на изковката. Изчисленията за образуване на первази, вдлъбнатини, первази, рамена, фланци и подобни елементи за коване се основават на предположението, че обемът на метала остава непроменен по време на деформация.
Трансфер на метал (виж таблица 18). Тази операция се състои в изместване на една част от детайла спрямо другата, като металът се деформира само в пролуката между тях (фиг. 113). В резултат на прехвърлянето оста на детайла става стъпаловидна. Разграничете прехвърлянето на метал в една и две успоредни равнини. При прехвърляне в една равнина (фиг. 113, а), след лепене и затягане, детайлът се измества от дясната му страна спрямо лявата, фиксиран в равнината /. Ако прехвърлянето се извършва на преса с подвижна маса, тогава долният нападател се измества спрямоГорна част. При работа с чук върху долния ударник под детайла се поставя плоска ролка или специална облицовка. Тук отсъства зоната на геометрична деформация като обем от метал между контактните повърхности на инструмента. Зоната на физическа деформация е много слабо развита и представлява малък обем метал в зоната на срязване на влакната по време на подаване на метал.
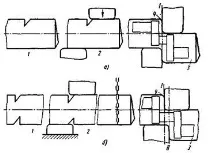
Ориз. 113. Схема на операцията по прехвърляне на метал:
1 - детайл след лепене и затягане; 2 - детайл върху изместен долен нападател; 3 - детайл след прехвърляне
Прехвърлянето в две равнини (фиг. 113, b) се извършва подобно на прехвърлянето в една равнина, но между скобите в равнините / и // се поставя определено количество метал, което основно представлява зоната на физическа деформация. Получената шийка обикновено е бъдещ щифт (например при производството на колянови валове). По време на преместването дългият преместващ се край на детайла трябва да бъде окачен на вериги с помощта на кран и спуснат по протежение на преместването. При липса на кран се използва набор от подложки, които се отстраняват последователно при спускане на края на детайла. За да избегнете вредно действие
рязане на влакна, лепене и защипване се извършват с инструмент с голям радиус на скосяване. При предаване в две или повече равнини, срязването на влакната е малко вероятно.
В процеса на прехвърляне на метала той се затяга на местата, посочени на фиг. ОТ буквата у - За да се компенсира затягането, височината на детайла трябва да се увеличи спрямо размера на изковката с 15-25%. В края на операцията излишният метал се ускорява, което прави възможно получаването на ребра за коване с малки радиуси на заобляне.
Огъване и други операции (виж таблица 18). Операцията на огъване при коване на чукове и преси се извършва междуподложни опори. Тази операция не изисква много усилия и обикновено се извършва при ниска температура (850-950°C). В зоната на разтягане по време на огъване се образува мивка, за компенсиране на която се прави съответно удебеляване на детайла пред завоя. Ако това не може да се направи, тогава след огъване изковката трябва да бъде допълнително коригирана. В зоната на компресия могат да се образуват гънки, които могат да бъдат избегнати с голям радиус на ъгъла на огъване. Ако този радиус => 0,5 H0, тогава дължината на детайла L0 по време на огъване се изчислява от централната линия на изковката. При по-малка дебелина на детайла дължината му се определя като сумата от правите участъци на изковката, докато за всеки ъгъл на огъване се добавя 0,25 H0. За рязане на краищата на изковката се добавя до 3 H0 към дължината на детайла, в зависимост от радиуса на огъване. Процесът на огъване е разгледан по-подробно в гл. VII.
В допълнение към описаните в коването се използват и други операции: например усукване (при производството на колянови валове), вендузи (при производството на резервоари), заваряване и някои други. Значителен брой операции се извършват в опорни матрици. Повечето от тях са разгледани в описанието на примери за процеса на коване.