Пълнене на форми с метал
Пълнене на форми с метал
Изливането на големи стоманени блокове се извършва по два начина: отгоре (фиг.5.4) и според схемата на сифон (фиг.5.5). Широко известно е, че всеки от тези методи има някои характеристики, които при определени условия могат да предоставят някакви технологични предимства или да се считат за недостатъци.
Стоманеното леене отгоре е много интересно от гледна точка на създаване на оптимални условия за формиране на слитък, тъй като естеството на пълнене на формата в този случай позволява запълването на печалбата последно. Тоест, горещи порции метал от кофата попадат в печалбата, която след това захранва тялото на слитъка. В същото време, когато стоманата се излива в големи блокове, поради голямата им височина, металът се пръска в долната част на формата поради удара на струята върху палета. В този случай на повърхността на слитъците се появяват голям брой дефекти под формата на пръски, плен, пукнатини, инверсии, подкоркови мехурчета, вълнообразност, заливи и др.
За подобряване на качеството на повърхността, както беше отбелязано по-горе, се използва смазване на формата. Трябва да се има предвид, че нарушаването на технологията на смазване води до образуване на подкоркови мехурчета върху блокове и повърхностни дефекти върху изковки.
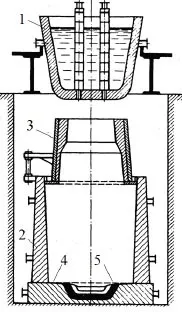
Фигура 5.4– Схема на разпределителен съд и леярска форма отгоре: 1 - разливно устройство; 2 - мухъл; 3- изгодно разширение; 4-палет; 5- втулка
За да се стабилизира скоростта на изтичане на стомана и по този начин скоростта на издигане на метала във формата, при изливане на стомана в големи слитъци се използва така нареченият резервоар отгоре, което позволява да се поддържа металното огледало на почти същата височина и по този начин да се осигури постояннаскорост на изтичане. Кошът се състои от стоманен корпус с облицовка от шамотни тухли или високоалуминиев бетон отвътре. При изливане на блокове за коване, чиято маса надвишава капацитета на една топлина, резервоарът служи и като резервоар за течна стомана по време на смяната на кофите за разливане на стомана.
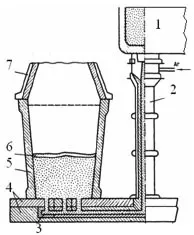
Фигура 5.5- Схема на отливане на сифонна стомана: 1 - черпак, 2 - централно окабеляване, 3 - сифонно окабеляване, 4 - палет, 5 - форма, 6 - топлоизолационна смес, 7 - изгодно разширение
Съответно, задължително условие за изливане отгоре е наличието на кумпел тава, която допринася за бързото образуване на "възглавница" от течен метал и за намаляване на нежеланото пръскане на струята. В същото време стоманена вложка с дебелина 100-200 mm обикновено се поставя в центъра на палета и по този начин предотвратява разтопяването на палета и заваряването на блока към палета. Независимо от това, в началния момент на изливане, повърхностните слоеве на облицовката много бързо се нагряват от падащата стоманена струя до висока температура и материалът на обвивката губи своята здравина и стоманената струя лесно я отмива.
Понякога преди леене кюмпелът се напълва 2/3 със стомана и се оставя да се втвърди. Този метод обаче донякъде усложнява и забавя процеса на леене като цяло.
Сифонното изливане (фиг. 5.5) се основава на принципа на комуникиращите съдове. При изливане по сифонен метод металната струя навлиза във формата отдолу през система от вертикални и хоризонтални канали.
Леенето по сифонния метод се придружава от по-спокойно издигане на стоманата във формата (0,15–0,35 m / min), което влияе благоприятно върху качеството на слитъка.
Времето за пълнене на формата може да се изчисли по следната формула:
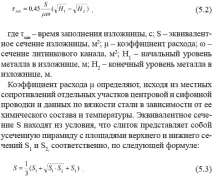
Известно е, чесифонното леене осигурява по-високо качество на повърхността на блоковете и съответно намалява разходите за почистване на метала. Въпреки това, при този метод на изливане, подготовката на канавката изисква повече време и пари, отколкото при изливане отгоре; освен това се увеличават загубите на метал (лечници, авариен скрап).
За да се оцени методът на изливане на стомана, е необходимо да се вземат предвид техническите и икономическите показатели на цялото производство като цяло. От тази гледна точка резултатите от експерименталните нагрявания, проведени в една инсталация, не са показателни.
За да се сравнят техническите и икономическите показатели на процеса на леене на стомана по горните два метода, е необходимо да се вземат предвид загубите на метал по време на леене и оголване, разходите за труд за подготовка на форми, удължители и палети, огнеупорен материал, почистване на заготовки, леене на стомана, разходите за леене и оголване, капиталови разходи, производителност на разливни участъци и др.
Значително предимство на метода за леене на сифон е възможността за запълване на формата под слой топлоизолационна смес, което не само предотвратява окисляването на повърхността на металното огледало, но също така позволява значително да се подобри качеството на повърхността на слитъка. Използваните в практиката смеси са леки, фино диспергирани, ниско топлопроводими прахове със сравнително висока точка на топене и ниска течливост при високи температури. Тези прахове се подават върху металната повърхност преди отливането или на ранен етап от пълненето на формата.
Механизмът на действие на топлоизолационните смеси е сложен, тъй като в процеса на пълнене на формата е трислойна система, състояща се от течна шлака, синтерован слой и слой от остатъчен топлоизолационен прах. защотодолният слой на топлоизолационната смес, разположен директно върху металното огледало, се топи, след което изпълнява функциите за защита на металната повърхност от окисляване, абсорбиране на неметални включвания, плаващи на повърхността, и също се влива в пролуката между менискуса и стената на формата, образувайки слой от шлака между слитъка и стените на формата. Слоят от шлака между вътрешната повърхност на формата и слитъка намалява скоростта на охлаждане в кората по време на началния период на образуване на слитъка и по този начин намалява възможността за прекъсване на повърхността на слитъка. Слоят от шлака на границата на матрицата и блока също така предотвратява изтичането на метала в неравностите на стените на формата и допринася за развитието на свободно свиване на стоманата по време на втвърдяването. Спеченият слой е, така да се каже, преграда, която потиска кипенето на метала във формата, като по този начин гарантира безопасността на остатъчния горен слой. Най-горният слой, който има прахообразна структура, има висока подвижност и е равномерно разпределен върху металната повърхност, осигурявайки добра топлоизолация на огледалото.
Анализът на условията за взаимодействие на топлоизолационни смеси с потоци от течен метал, влизащи във формата по време на сифонно леене, показа, че за да се намали замърсяването на долната част на слитъка с частици от сместа, е желателно да се изключи директният контакт на сместа с долната част на формата. За тази цел опаковките със сместа се окачват или укрепват с дървени рамки на известно разстояние от дъното на формата.
Най-голямо практическо приложение са получили топлоизолационните смеси на базата на въглищна пепел от ТЕЦ, вермикулит, перлит и някои други материали. Разработените в момента специализирани смеси на основата на нисковъглеродна пепел от топлоелектрически централи са предназначени за леене на слитъци от различни видове по сифонен метод.видове от почти цялата гама произвеждана стомана. По правило смесите съдържат аморфен графит или въглерод-съдържащи добавки (до 30%), които предотвратяват синтероването и топенето на праховете. Разходът на такива смеси е 1,5-2,5 kg/t. Основните изисквания към топлоизолационните смеси могат да бъдат формулирани, както следва:
- точката на топене трябва да бъде в диапазона 1100 - 1350 ° C;
- вискозитетът на течната смес трябва да бъде 0,2–0,6 Pa*s при оптимална температура на излятия метал във формата;
- течната шлака не трябва да променя значително своя вискозитет в рамките на възможните температурни колебания, които възникват по време на процеса на изливане, тоест трябва да бъде „дълъг“;
- течният слой шлака трябва да намокри добре оксидите върху металната повърхност и да намали повърхностното напрежение на стоманата.
В практиката на изливане на големи стоманени блокове се използват широко така наречените екзотермични смеси, т.е. смеси, в процеса на които топлината се отделя директно в метала на печалбата. Към екзотермичните смеси се налагат следните изисквания: висока калоричност, която осигурява топенето на компонентите и компенсиране на топлинните загуби, висока скорост на горене, безопасност при експлозия, минимално отделяне на вредни газове и висока степен на асимилация на неметални включвания. Съставът на екзотермичните смеси включва горими, кислородсъдържащи и шлакообразуващи компоненти. Като горими материали се използват алуминий или силикокалций. Натриев нитрат, манганова руда, котлен камък, концентрати от желязна руда служат като окислители в шлакообразуващите смеси. Функциите на шлакообразуващите компоненти в смесите се изпълняват от шлака от доменни пещи, силикатен блок, флуор шпат и др.
Екзотермичната смес обикновено се поставя на дъното на формата преди отливането. Наличието на магнезий или силикокалций в състава на такава смес предизвиква силен пироефект по време на изгарянето и е придружено от отделяне на голямо количество дим. Съдържанието на селитра и флуорипат в екзотермичната смес причинява замърсяване на въздуха на работната площадка, което силно възпрепятства масовото използване на такива смеси. Освен това тези смеси са относително скъпи, трудни за производство и съхранение поради големия брой компоненти и експлозивността.
Понастоящем високоефективно топлоизолационно покритие на основата на пепел от оризови люспи се използва широко в чуждестранната и вътрешната практика. Има много високи топлоизолационни свойства. Съществуват различни версии на състава на тези смеси, които се различават по незначителни добавки на други растителни отпадъци (например пепел от слънчогледова люспа и др.). Въпреки това, чистата пепел от оризови люспи показва най-добри резултати. Когато е в контакт с течна стомана, тя бързо образува течен филм, който драстично намалява абсорбцията на кислород и азот от течната стомана. В същото време това покритие абсорбира неметални включвания (алуминиеви оксиди), открити в течната стомана, предотвратявайки образуването на отлагания в резервоара.
Свойствата на пепелта от оризови люспи в областта на точката на топене на материала са оптимални за работа. Над тънък разтопен слой покритието остава в стабилно твърдо състояние и запазва високите си изолационни свойства. Ниската му обемна плътност гарантира максимална топлоизолация при нисък разход на материал. На практика е установено, че при използване на пепел от оризови люспи добивът може да се увеличи с 2-4% в сравнение сизползване на синтетични топлоизолационни смеси.
Като цяло топлоизолационните смеси, използвани за изливане на големи блокове, трябва да имат висока мобилност, лекота, ниска топлопроводимост и висока точка на топене, тоест свойства, които определят качеството на изолацията на метално огледало по време на леене и втвърдяване на блокове. Изборът на конкретна смес за леене на големи блокове трябва да се извършва въз основа на тестове при производствени условия. В този случай е важен не само съставът на сместа, но и начинът, по който се подава във формата.