Поддръжка на корабни двигатели
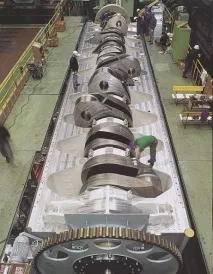
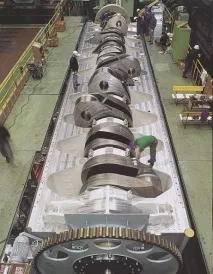
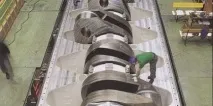
Ако рамката на основата е изместена или неправилно закрепена към основата на кораба, тя и коляновият вал могат да се деформират, което може да причини пукнатини в рамката на основата, счупване на коляновия вал, повреда на съединителите, счупване на прикрепените валове.
По правило отстрани на фундаментната рамка има ориентири, чиято повърхност лежи в една равнина, успоредна на оста на коляновия вал. Чрез прилагане на контролна линийка върху повърхността на реперите можете да откриете деформацията на рамката.
Ако дизеловият двигател е монтиран на гумено-метални амортисьори, проверете дали върху тях е попаднало масло (гориво). Невъзможно е да боядисате гумата на амортисьора с маслена боя; за да увеличите експлоатационния живот на гумата, можете да я покриете с разтвор на креда веднъж на всеки 2-3 месеца.
Ако двигателят се монтира отново, след 100 часа работа фундаментните болтове, закрепващи рамката, се проверяват за затягане и, ако е необходимо, се затягат. Следващата проверка се извършва след 500 часа и след това на всеки 1000 часа работа. При високооборотни и ударно монтирани двигатели закрепването на рамката се проверява след 250-500 часа.
Не забравяйте да проверите закрепването на рамката след авария (сблъсък, заземяване), след силна и продължителна буря.
Ако болтовете не са затегнати равномерно в рамката на основата, възникват локални пренапрежения и могат да се появят пукнатини. След проверка на затягането на болтовете е задължително да проверите липсата на деформация на рамката, като приложите контролна линийка къмреферентни повърхности или измерете разстоянието между коляновия вал.
Когато двигателят работи, на работната повърхност на цилиндровата обвивка се появяват надрасквания, триене и рискове. Причината за тези дефекти е леко задръстване на буталото, когато двигателят работи с претоварване, силно образуване на нагар в цилиндъра, недостатъчно смазване на цилиндъра, неправилно сглобяване на коляновия механизъм, счупване на буталния пръстен. Тези дефекти се отстраняват чрез шлайфане с фин корборундов камък или намаслена шкурка в напречна посока.
Ако износването на втулките на цилиндъра се различава значително едно от друго, тогава е необходимо да се установи причината за това и, ако е възможно, да се отстрани. Нормално може да се счита износване в диаметър от 0,01-0,07 mm (в зависимост от диаметъра на цилиндъра, скоростта, цикъла и вида на продухването) за всеки 1000 часа работа на двигателя.
Степента на износване на работната повърхност на обвивката на цилиндъра зависи от твърдостта и антифрикционните свойства на метала на обвивката, чистотата на обработката му, качеството на сработване на буталните пръстени, качеството на маслото и разпределението му върху работната повърхност на обшивката, качеството на горивото и естеството на изгарянето му в цилиндъра, от натоварването и температурните условия на двигателя, наличието на устойчиви на износване покрития върху повърхността. на втулката и буталните пръстени. Твърдостта на буталните пръстени трябва да надвишава твърдостта на втулката с 10-20 HB.
Втулките на цилиндъра се износват неравномерно по височина. Най-голямо износване се наблюдава в горната му част.
Това се дължи на следните причини:
по време на работния ход налягането на газовете в цилиндъра намалява и следователно най-голямото специфично налягане на буталните пръстени върху стените на втулката възниква в горната позиция на буталото;
влошаване на условията на смазване;
най-голямото топлинно натоварване;
корозивно действиепродукти от горенето върху металните втулки.
Правилното смазване на работната повърхност на цилиндровата втулка е един от основните фактори, предотвратяващи нейното износване.
Работата на двигателя с претоварване е придружена от повишена температура на стените на цилиндъра и частите на буталната група, влошава условията за тяхното смазване, увеличава образуването на въглерод и в крайна сметка причинява интензивно износване на цилиндровата обвивка и буталните пръстени.
Повредата на повърхността на ръкава от страната на водата се дължи на кавитация и електрохимична корозия. За да се предотвратят тези явления, се използват специални добавки за охлаждаща вода и се монтират цинкови протектори в охладителната кухина.
Техническата поддръжка на капаците на работните цилиндри се състои в периодична проверка на техните охладителни кухини, почистване на отлагания, подмяна на цинкови протектори, проверка за пукнатини.
За да се провери липсата на пукнатини в буталото, капака и цилиндровата обвивка, те се почистват от мащаб и въглеродни отлагания, след това внимателно се изследват с лупа и, ако има съмнение за пукнатини, се извършва хидравличен тест от страната на охлаждащата кухина при налягане от 6 kgf / cm 2. Най-често пукнатините се появяват в мостовете между леглото на инжектора и леглото на изпускателния и всмукателния клапан към капака на цилиндъра.
Когато проверявате буталата, обърнете внимание на пукнатини, надрасквания, изгаряне на главата, следи от газ, преминаващ през буталните пръстени, тяхната подвижност в жлебовете. При значително коксуване на пръстените буталото се държи в горещ алкален разтвор за един час и след това се измива с керосин.
Изгарянето и износването на буталните пръстени са по-чести при двутактови двигатели, работещи при по-високи температури на буталото, и причиняват влошаване на стартирането на двигателя, проникване на изгорели газове в картера, повишаваненепрозрачност на отработените газове, увеличаване на специфичния разход на гориво и намаляване на мощността на двигателя. Износването и неправилното монтиране на маслени скреперни пръстени са придружени от повишена консумация на масло, повишена непрозрачност на отработените газове, които имат синкав цвят, изгаряне на компресионни пръстени поради обилен поток на масло към тях. При значително износване на пръстените и загуба на еластичност, пръстените се сменят с нови.
Чистият бутален болт се проверява с лупа и се заменя, ако се открият пукнатини.
Основният вид повреда на буталните щифтове и втулката на горната глава на свързващия прът е нарязване; причините могат да бъдат следните:
липса или недостатъчно смазване на лагера на главата;
неадекватно качество на маслото; недостатъчни хлабини в основния лагер или незадоволително прилягане на пръста;
изкривено движение поради лошо сглобяване;
подгряване на подглавния лагер;
стартиране на двигателя без изпомпване на масло;
високо налягане на газа в цилиндъра на двигателя;
бързо зареждане на незагрят двигател; значително и продължително претоварване на двигателя.
Наблюдението на биелните по време на работа на двигателя се свежда до наблюдение на лагерите в горната и долната глава и болтовете на биелата.
Когато проверявате болтовете на свързващия прът, проверете състоянието на резбата, липсата на пукнатини, прорези, триене. Болтовете трябва лесно и плътно да влизат в дупките. Тяхното остатъчно удължение не трябва да надвишава нормите, установени от завода. Дефектните болтове се заменят с резервни, като последните трябва да имат паспорт с посочване на химическия състав и механичните качества, както и печат OTK.
Показател за нормалната работа на лагерите на биелата и рамката е тяхната температура (посочена в инструкцията за експлоатациядвигател), който се контролира приблизително чрез докосване на местата, които са най-близо до основния лагер и капаците на люка на картера.
При проверка на втулките на горната глава на свързващия прът, надраскванията по тях се почистват със скрепер и пролуката между втулката и буталния щифт се проверява с щуп. Ако празнината се доближи до границата, втулките се сменят.
Най-честите повреди на лагерите на главата, рамката и коляновия вал са пукнатини в бабита и отлепване на последния.
Причините за тези щети могат да бъдат следните:
лош бабит или некачествено пълнене от него;
големи луфтове, причиняващи удари по време на работа на лагерите;
неправилно монтиране на лагера по време на монтажа;
непаралелност на оста на шийката на мотовилката спрямо оста на шийката на рамката на коляновия вал;
високо налягане на газа в цилиндъра на двигателя;
неадекватно качество на маслото;
липса или недостатъчна интензивност на смазване; претоварване на двигателя.
Нормалното износване на лагерните черупки за 1000 часа работа за повечето корабни двигатели е 0,010-0,015 mm. Повредените лагери се сменят, шийката на коляновия вал се проверява и почиства внимателно и се отстраняват причините за повредата.
Коляновият вал работи в много трудни условия и е най-критичната, сложна и скъпа част от двигателя, което налага внимателно да се следи работата му.
Ако по време на работа на двигателя правилното положение на коляновия вал в лагерите е нарушено (проверете чрез измерване на факелите) и валът започне да работи с недопустимо отклонение, тогава се появява умора на метала, в него се появяват пукнатини и след това валът се счупва.
Положението на коляновия вал се проверява чрез измерване на изтеглянето и разширението. Тегленето се проверява по специаленскоба. Raskeps се измерват с циферблатен индикатор, монтиран между бузите с кръвните червеи в хоризонтално и вертикално положение. Стойността на допустимите течения се определя от дизеловия завод.
Когато проверявате коляновия вал, проверете за драскотини, драскотини и неравности. Повърхностните повреди по шийките се почистват внимателно с лична пила и се полират до огледално покритие на ръка с шкурка, намазана с масло или керосин, като се използват устройства от два дървени блока. След това се проверяват елиптичността и конусността на заземяващата шийка, чиито стойности не трябва да надвишават граничните стойности, посочени в инструкцията за експлоатация на този двигател.
За много видове двигатели животът на коляновия вал определя цялостния живот на двигателя, тъй като поради високата цена и трудоемкостта на производството на коляновия вал, повторното производство на двигателя често е непрактично.
В практиката на работа на двигатели повредите на коляновите валове не са необичайни. В повечето случаи те възникват поради недостатъчно внимателно наблюдение на коляновия вал по време на работа на двигателя, поради което персоналът по поддръжката на двигателя трябва внимателно да следи състоянието му и да вземе мерки за предотвратяване на повреда на последния.