Рационален избор на гориво за общинска котелна централа или при какви условия могат да станат въглища
S.M. Назаров, Е.В. Калинин, Министерство на промишлеността, енергетиката и природните ресурси на Ростовска област; Р. L. Isyemin, Тамбовски регионален център за обучение и информация за биоенергетика; S.N. Кузмин, В. В. Коняхин, А. В. Михалев, Тамбовски държавен технически институт
Университет; M.E. Ковалерчик, ЗАО СМНУ Воскресенское, Воскресенск, Московска област
Известен е проблемът с нарастващите тарифи на жилищно-комуналните услуги, включително тези за комунални енергийни услуги, както и проблемът с високата степен на износване на оборудването и комуникациите в системата на жилищно-комуналните услуги в България, както и трудностите при финансирането на модернизацията на комуналната енергетика. Опитът на комуналните предприятия в много региони на България показва, че модернизацията по правило е по пътя на преминаване на котли на въглища и мазут към изгаряне на природен газ (с подмяна на старото котелно оборудване). В същото време се предполага, че преминаването на котелната централа към изгаряне на природен газ драстично намалява цената на генерираната топлинна енергия, подобрява екологичните характеристики на котелната централа и условията на работа на персонала по поддръжката. Заключението за икономическата ефективност на използването на газ като енергиен носител обаче се прави, както беше отбелязано по-рано [1], без да се взема предвид възможността за използване
котли, които могат да горят нискокачествени и по-евтини въглища. В последния случай, както ще бъде показано по-долу, заключението за ефективността на използването на природния газ като енергиен носител не е толкова очевидно.
Нека разгледаме резултатите от проучване за осъществимост за преобразуване на котел, работещ с въглища, за изгаряне на природен газ.
Да приемем, че някаква котелна централа с прикрепенс товар от 1 MW е оборудван с котли Universal-6, които, както е известно [2], са предназначени за изгаряне на пресят антрацит (при изгаряне на обикновен антрацит или дори на твърди въглища, топлинната мощност на котлите от този тип пада наполовина). Когато котелната централа се преобразува на изгаряне на природен газ, в нея ще трябва да се монтират два котела KVA-0,63 Hn (произведени от OJSC Borisoglebsk Boiler-Mechanical Plant). В същото време разходите за реконструкция на такава котелна централа, включително изпълнението на проектните работи, закупуването на оборудване, демонтирането на старото, инсталирането и пускането в експлоатация на ново оборудване в цените на 3-то тримесечие на 2005 г., трябва да възлизат на 3199 хиляди рубли. (според 000 "Газтехпроект", Тамбов, който завърши проекта за газификация на такава котелна централа).
Основните показатели за такова изчисление са обобщени в таблицата.
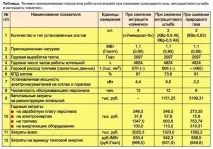
Междувременно опитът с използването на водогрейни котли, разработени от Асоциацията KARTEK, Тамбовския държавен технически университет (TSTU) и произведени от CJSC SMNU Voskresenskoye за изгаряне на нискокачествени въглища, показва, че цената на 1 Gcal топлина, генерирана от котелна централа, може да бъде допълнително намалена без допълнителни капиталови разходи, които са неизбежни при газификация на котелна централа. За да направите това, е необходимо да използвате нискокачествени въглища, като антрацитни фини частици или въглищни суспензии. Например антрацитната утайка има калоричност от 4700 kcal/kg (19,7 MJ/kg), съдържанието на пепел може да достигне до 33%, но цената (включително транспортния компонент) е само 996 рубли/тон.
Въпреки това, не е възможно да се изгори утайка в обикновени водогрейни котли, оборудвани с чугунени решетки за изгаряне на едри въглища във фиксиран слой, т.к. повече от 90% от утайката се състои от частици с размер до 6 mm. Толкова плиткочастиците ще паднат през процепите на решетката. Използването на така наречените ъглови решетки с водно охлаждане, както показва нашият опит, при изгаряне на антрацит също е проблематично - поради опасността от бързо изгаряне на решетката при много висока (над 1900 ° C) температура на горивния горивен слой.
При жаротръбни димоотводни котли, проектирани от КАРТЕК-ТГТУ, се използва стъпаловидна водоохлаждаема въздухоразпределителна решетка, която се монтира в долната част на пламъчната тръба. Конструкцията на котел с такава решетка е защитена с евразийски патент № 006130 и е описана подробно в предишни публикации [4, 5, 6].
Връщайки се към въпроса за избора на рационален източник на енергия за случая на модернизация на котелна централа с прикачен товар от 1 MW, анализиран по-горе, трябва да се отбележи, че в такава котелна централа могат да се монтират два котела KVR-0,8 AK и KVR-0,5 AK. В същото време капиталовите разходи за реконструкцията на котелната централа ще възлизат на 1 милион 115 хиляди рубли. (2,7 пъти по-малко, отколкото когато котелната централа е преобразувана на природен газ), а цената на 1 Gcal генерирана топлина ще бъде 631 рубли. Основните технически и икономически показатели за работата на котелната централа при изгаряне на антрацитни утайки също са дадени в таблицата.
Трябва също да се отбележи, че в котлите KVR-AK е възможно да се изгарят не само антрацитни глоби, но и глоби от каменни въглища, отсевки, въглищни утайки.
Съвместно изгаряне на въглища и биомаса
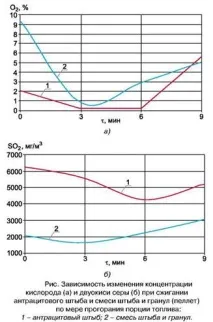
Освен това, при съвместно изгаряне на пелети и утайка в горното съотношение, емисиите на серен диоксид в атмосферата се намаляват около два пъти в сравнение с изгарянето на единична утайка (фиг. б). Когато част от въглищата се заменят с биогориво, емисиите на въглероден двуокис в атмосферата съответно намаляват (биомасата се счита за CO2 неутрално гориво), което е важно във връзка с навлизането вдействие на Протокола от Киото.
Като биогориво е възможно да се използват не само пелети от слънчогледови люспи, но и пелети от дървесни отпадъци, както и пелети от зърнени отпадъци и люспи от просо (производството на такива пелети се установява например в Комбината за хлебни продукти Романовски).
Обемното тегло на гранулите е 630-750 kg/m 3 , доставят се насипно или в чували с голяма вместимост ("биг бегове") и транспортирането им не създава големи проблеми. Като се има предвид ниската производителност на котлите, приготвянето на смес от гранули и въглища може да се извърши ръчно или с помощта на прости механизми.
1. При извършване на сравнителен икономически анализ за избор на оптимален енергиен източник за котелна централа е необходимо да се вземе предвид възможността за използване на котли, чиято конструкция позволява изгаряне на нискокачествени въглища (фини, утайки, отсевки), както и обикновени въглища.
2. При преобразуване на котелна централа за изгаряне на нискокачествени въглища и оборудване на котелна централа с котли с пещи с кипящ слой, в които може да се изгаря такова гориво, цената на генерираната топлинна енергия е по-ниска, отколкото при преобразуване на котелна централа за изгаряне на природен газ и инсталиране на газови котли в котелна централа.
3. За намаляване на емисиите на серни оксиди в атмосферата при изгарянето на нискокачествени въглища се препоръчва съвместното изгаряне на въглища и биомаса, включително под формата на биогранули.
1. Осипов A.D., Isyemin R.L., Akolzin A.P. Методология за избор на рационална схема за енергоснабдяване на селскостопански производствени съоръжения // Индустриална енергетика. 1991. № 5. стр. 42-45.
2. Roddatis K.F., Poltaretsky A.N. Наръчник за котелни инсталации с ниска производителност. - М.: Енергоатомиздат. 1989. 488 стр.
3. Исемин Р.Л., Кузмин С.Н., Коняхин В.В., МихалевА.В., Будкова Е.В. Екологични и икономически предимства от използването на жаротръбни димни водогрейни котли, оборудвани с пещи с полукипящ слой // Въглища. 2002. № 10. С. 57-61.
4. Исемин Р.Л., Коняхин В.В., Кузмин С.Н., Будкова Е.В., Кондуков Н.Б. Трипътен водогреен жаротръбен котел с димоотвод с пещ с полукипящ слой за изгаряне на нискокачествени въглища. Резултати от четири години работа // Новини за топлоснабдяване. 2002. № 11. С. 21-25.
5. Кузмин С.Н., Будкова Е.В., Исемин Р.Л., Кондуков Н.Б. Разработване на котел за изгаряне на нискокачествено твърдо гориво // Екотехнологии и спестяване на ресурси. 2004. № 5. С. 73-78.