Статии RCIT - Как да подобрим надеждността на буксата
Промени, уточнения, практически обмен на опит
По време на експлоатацията на товарни вагони през 2008 г. по пътната мрежа на Руските железници са допуснати 841 случая на дефектни товарни вагони, които са в експлоатация след извършване на планирани видове ремонти в предприятията на Централната дирекция за ремонт на товарни вагони. Проведените проучвания установиха, че случаите на бракове с вагони са разпределени в процентно отношение, както следва:
- отопление на буксата | 94,200% |
- сблъсък при маневри | 0,02 0% |
- закъснения на влаковете на етапа повече от един час | 0,02 0% |
- неизправности на оборудването за автоматично прикачване | 0,017% |
- откачване на вагони поради технологични неизправности | 0,008% |
- дерайлиране на вагон от товарен влак | 0,008% |
Прост анализ на допуснатите случаи на брак при ремонт на товарни вагони показва, че най-голям брой бракове при влакова работа са направени при отоплението на буксата (94,2%). При разработването на стратегия за подобряване на надеждността на буксите с ролкови лагери, специалистите от Централната дирекция идентифицират основните групи причини за нагряване на букси. Те включват: - неизправности на крайния монтаж; - дефекти в смазването на буксата; - повреди на лагери; - други причини за повреда на буксата.
Анализирайки по-подробно браковете поради повреда на буксовите възли за 2008 г., бяха разгледани всички причини, обединени в групи. Данните от анализа са представени в таблицата.
Анализ на бракове поради повреда на букси по причини за 2008 г.Не. | Причини за разкачване на вагони (неизправности) | Количество, % |
1 | Неизправностилагерни пръстени | 23,74% |
2 | Проблеми с ролки | 15,28% |
3 | О отслабване на крайния монтаж | 11,87% |
4 | Относно поливането на лубриканта | 11,24% |
5 | Неправилен избор на лагери (несъответствие между радиални и аксиални хлабини) | 7,20% |
6 | Дефектни лабиринтни уплътнения | 6,19% |
7 | Различните размери на ролките по диаметър и дължина са над допустимите | 4,55% |
8 | Пукнатини, счупвания на упорни пръстени | 3,66% |
9 | Дефектни корпуси на букси | 3,16% |
10 | Неизправности на сепаратора | 2,90% |
единадесет | Замърсяване с мазнини | 2,65% |
12 | Неизправности на количката | 2,53% |
13 | Унищожаване на крайния монтаж | 2,15% |
14 | Липса (излишък) на смазка | 2,02% |
15 | Пълно разрушаване на лагерите | 0,76% |
16 | Наличието на повече от приемливи дефекти по повърхността на протектора на колелото | 0,13% |
Графично представеният анализ на причините за брака (фиг. 1) ви позволява визуално да определите тези, за които е възникнал максимален брой бракове поради повреда на кутията на осите.
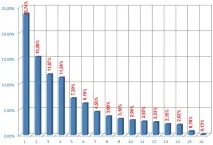
Ориз. 1. Анализ на причините за дефекти поради повреда на букси през 2008 г.: 1 — повреда на лагерни пръстени; 2 - неизправности на ролките; 3 - отслабване на крайния монтаж; 4 - поливане на смазката; 5 - неправилен избор на лагери (несъответствие между радиални и аксиални хлабини); 6 - неизправности на лабиринтни уплътнения; 7 - различните размери на ролките по диаметър и дължина са по-високи от допустимите; 8 -пукнатини, счупвания на упорни пръстени; 9 - неизправности на букси; 10 - неизправности на сепараторите; 11 - замърсяване с мазнини; 12 - неизправности на колички; 13 - разрушаване на крайния монтаж; 14 - липса (излишък) на смазване; 15 - пълно унищожаване на лагери; 16 - наличието на повече от допустимите дефекти по повърхността на колелата
Въз основа на анализа на случаите на брак, дължащи се на повреда на блоковете на буксата през последната година, могат да се идентифицират няколко области в работата, свързана с подобряване на надеждността на този блок.
Първата посока се отнася до съществуващия дизайн на буксовия възел. Това предполага разработването на организационни и технически мерки за подобряване на качеството на планираните видове ремонти, надеждността на подвижния състав, намаляване на броя на отказите на техническото оборудване и случаите на брак. Тези дейности включват: - създаване на работна група за разглеждане на проблеми, възникващи при ремонт на колооси на товарни вагони; - внедряване на разработената STO на руските железници OJSC „Колесни комплекти. Формиране, ремонт, проучване и експлоатация”; - изготвяне на техническо задание за разработване на техническо задание за ремонтиран цилиндричен лагер на букса на товарен вагон, както и внедряване на разработената спецификация и проектна документация за ремонтиран цилиндричен лагер на букса на товарен вагон; - въвеждането в предприятията на Руските железници на "Класификатора на неизправностите на колелата на вагоните и техните елементи" 1.20.001-2007; - въвеждането в предприятията на Руските железници на "Класификатор на дефекти и повреди на търкалящи лагери" TsVT-22 и "Методи за определяне на причините за счупване на шийката на оста и разрушаване на буксовата кутия"; - завършване на разработването и внедряването на ремонтната карта на колоосите; - завършванесертифициране на колесни двойки от нова формация във вагоно-колесни работилници; - създаване на регионални центрове за техническо обучение на персонала на колесно-ролковите цехове; - техническо обучение на майстори и майстори на колело-валцови цехове в областните центрове; - 100% проверка на ремонтирани букси на колооси на виброакустични стендове; - допълнителен контрол на радиалните хлабини на лагерния блок директно върху шийката на оста на колоосите при избор на лагерни блокове; - смазване на повърхността на търкаляне на вътрешните пръстени с тънък слой нанесена смазка преди монтиране на корпуса на буксата с комплект лагери на шийката на оста; - изменение на инструкции № 3-ЦВРК за изпитване с щуп 0,04 mm на плътността на свързващата повърхност на гайката M110 и шайбата Belleville към плоския упорен пръстен след монтиране на крайния монтаж; - изчисляване на технико-икономическата ефективност на настилка на опорните и направляващите повърхности на буксите. Разглеждане на въпроса за осъществимостта на ремонт на корпуси на букси чрез наваряване; - изпращане на заявка до заводите доставчици за монтиране на защитни капаци на лабиринтните пръстени на нови букси; - разработване и внедряване на устройство за редактиране и контрол на геометричните параметри на ревизионни капаци. 100% контрол на съединителната повърхност на ревизионните капаци; - разработване на технология за наблюдение на състоянието на лабиринтни пръстени и лабиринтни канали на корпуси на букси, методи и устройства за наблюдение на аксиалното биене на лагерите; - при извършване на междинна ревизия на буксата не използвайте отстранената от предната част на буксата смазка, а я заменете с необходимото количество прясна; - осигурете по време на планирани видове ремонти прехвърлянето на парка на кабинковия вагон на АО "Руски железници" към колооси с оси тип RU1-Sh; - използвайте болтове M20X60.4.8 и M20X60.5.8 крайно закрепване с максимален срок на експлоатация 10 години; - при наличие на механични повреди по повърхността на лабиринтните пръстени, извършете механична обработка на тези повърхности; - определя реда за входящ контрол на гумени изделия за буксата; - да разпространи най-добрите практики на VKM Gorky-Sortirovochny при извършване на входяща проверка на нови кутии на букси с въвеждането на допълнения и промени в технологичните процеси за ремонт на сглобката на буксите.
Едно от условията за надеждна работа на буксата е предотвратяването на дефекти в смазването, като поливане и наличие на примеси. Чужди примеси попадат в буксата поради хлабавото прилягане на плоското гумено уплътнение между ревизионния и монтажния капак. Възможно е да се намали вероятността от попадане на влага и чужди примеси в смазката по време на целия период на работа на блока на буксата по време на периода на основен ремонт чрез запечатване на комплекта на буксата. В този случай печатите на предприятията, които са извършили ремонта или проверката на осовата кутия на колоосите, и датите на тези видове работа са монтирани върху пломбите.
Поставянето на уплътнения трябва да бъде задължително както за ремонтните, така и за работещите предприятия. Отговорността за състоянието на буксовия възел трябва да се възложи на фирмата, извършила последната работа с този буксов възел и уплътнение.
Няма да е разкритие, че инспекторите-ремонтници в пунктовете за техническа поддръжка на вагони, когато проверяват външното състояние на буксите, отварят ревизионните капаци. В същото време инструкциите не предвиждат отговорност за качеството на извършената работа. Тази мярка, поставянето на пломби върху ревизионните капаци, е наложителна необходимост. Основната йцелта е да се защитят ремонтните предприятия на Руските железници от премахване на инспекционните капаци от служители, които не са преминали тестове за правото да извършват междинен одит по предписания начин.
Самото смазване също оказва значително влияние върху безпроблемната работа на буксовите лагери. Най-широко за полуоси на автомобили с ролкови лагери се използва железопътна грес LZ-TsNII съгласно GOST 19791-74 или LZ-TsNII (y) съгласно TU 0254-307-00148820-95 (с промени 1 и 2). Представлява хомогенен мехлем от светло жълто до тъмно жълто.
От 2001 г. смазката Buxol се използва комерсиално във фрикционни възли с търкалящи лагери. В момента на Северния път се тества влак (50 вагона), чиито букси на колоосите са запълнени със смазка Metalplaks-P. В момента тези тестове все още не са дали категорични положителни резултати. Няма еднозначни препоръки и от изследователски институти. В бъдеще е необходимо да се разработят и въведат нови греси за букси с цилиндрични лагери.
Друг фактор за идентифициране на неизправностите на буксите е качественото изследване на причините за нагряване на блока на буксите. За да направите това, е необходимо въз основа на параграф 5, Приложение 5, Инструкция № 3-ЦВРК да допълните плана за изследване със снимки на откритите дефекти на лагера. Въз основа на плановете на проведените изследвания, срязвания в 17% от случаите, причините за нагряване на буксата не са идентифицирани (фиг. 2). Този факт показва, че по време на експлоатацията на колоосите, след всякакъв вид ревизия на блока на буксата, обикновеното разработване на лагерите се извършва в рамките на един месец. Но параграф 3.3 (а) от насоки № 3-ЦВРК ясно гласи: „ако инсталациятае произведен месец или по-малко преди откриването на нагряване, тогава колоосът може да бъде разрешен за работа. Въз основа на гореизложеното експертите предлагат да се зададе температурното ниво на нагряване на буксата, при което колоосът може да работи след всякакъв вид проверка в рамките на един месец.
Втората, по-модерна посока за подобряване на надеждността на буксата е използването на букси с касетъчни лагери. Структурно, касетъчните лагери възприемат както радиалните, така и 14% от аксиалните натоварвания, действащи върху лагерите. В момента на полигона Воркута-Череповец се провеждат експлоатационни изпитания на 51 гондолни вагона, произведени от Федералното държавно унитарно предприятие PO Uralvagonzavod модел 12-132-03 с лагери тип касета Compact TBU 130x250x160, произведени от SKF.
В момента на полигона Воркута-Череповец се провеждат оперативни изпитания на 51 гондолни вагона, произведени от FSUE PO Uralvagonzavod модел 12-132-03 с лагери тип касета Compact TBU 130x250x160, произведени от SKF. В бъдеще използването на лагери от този тип ще позволи да се изостави трудоемката работа по техния ремонт. Не е необходимо да се закупува необходимото количество смазка за изпълнение на производствената програма за освобождаване на автомобили от ремонт, съхранение, лабораторни изследвания. В допълнение, с прехвърлянето на колесни комплекти към оси с касетъчни лагери, ремонтните предприятия решават проблема с изхвърлянето на греста, която е била в експлоатация.
При получаване в ремонтните съоръжения, касетъчните лагери подлежат на входяща проверка. Когато се проверява: - наличие на придружителни документи; - целостта на опаковката; - пълен комплект и външен вид на лагера.
Как да подобрим надеждносттабукса? А.В. Саперов, технолог на Централната дирекция за ремонт на товарни вагони - клон на Руските железници